Introduction
The automotive industry relies on iron castings to make strong and durable parts. Iron castings are used in a wide range of applications, from engine blocks and cylinder heads to suspension components and brake systems.
Iron castings offer many advantages over other materials, such as strength, wear resistance, and thermal conductivity. In this blog post, we will discuss the properties of iron castings used in the automotive industry and how they can benefit your vehicle.
The automotive industry is no stranger to strength. The properties of iron castings used in this industry demonstrate a level of durability and tenacity that keeps them functioning under immense pressures and great temperatures. The combination of high elasticity, tensile strength, and ductility allows these castings to resist wear and tear, protecting vital parts from chemical corrosion or high-impact force.
The properties also create a furnace-like environment for operating the components at peak performance during even the hottest days. The use of high-grade iron castings in the automotive industry lends itself to long-lasting performance and overall quality that cannot be matched.
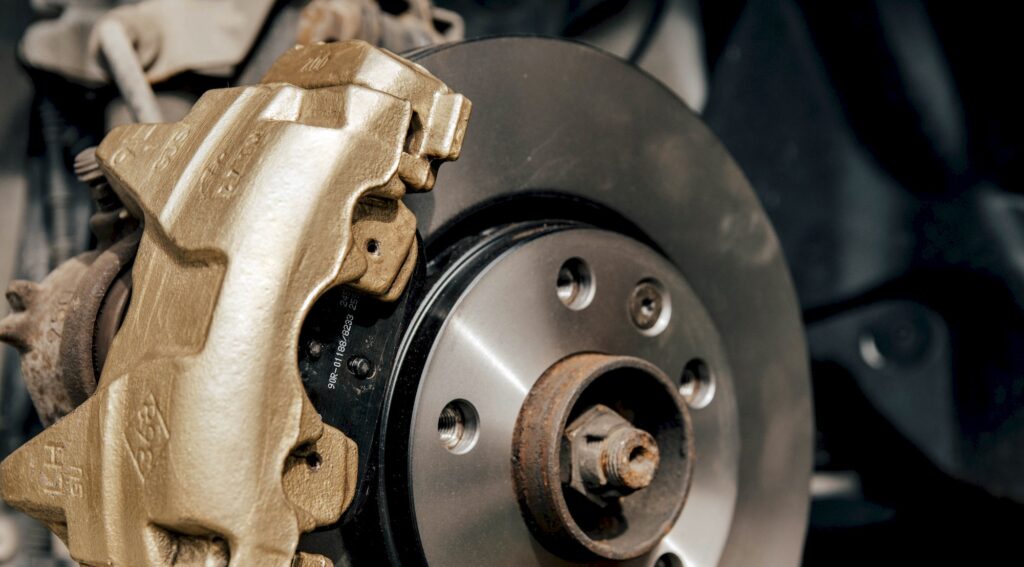
Strength
One of the most important properties of iron castings is their strength. Iron is one of the strongest metals available for casting, making it ideal for use in automotive applications. It is able to withstand high temperatures and pressure without breaking down or becoming brittle. This makes it an excellent choice for engine components like cylinder heads and blocks and suspension components like control arms and tie rods.
Iron is one of the strongest metals available, making it ideal for use in components that must withstand high levels of stress and strain. It is also highly resistant to corrosion and wear, which makes it a great choice for parts that must be exposed to harsh environments or subjected to frequent use.
The strength of iron castings used in the automotive industry is remarkable. The ability of these materials to bear loads and withstand the harshest driving environments makes them highly desirable for many leading manufacturers. The process behind making these strong parts includes extreme heat and pressure that bond the material together, transforming it into an incredibly sturdy product capable of withstanding harsh conditions.
To ensure that each casting meets industry standards, rigorous testing and quality control are put in place every step of the way. The result is a material capable of doing its job without fail, a dependability that can be seen throughout cars on roads around the world today. The property of strength provided by iron castings continues to be an invaluable resource to the automotive industry, providing unimpeachable reliability in the face of its toughest challenges.
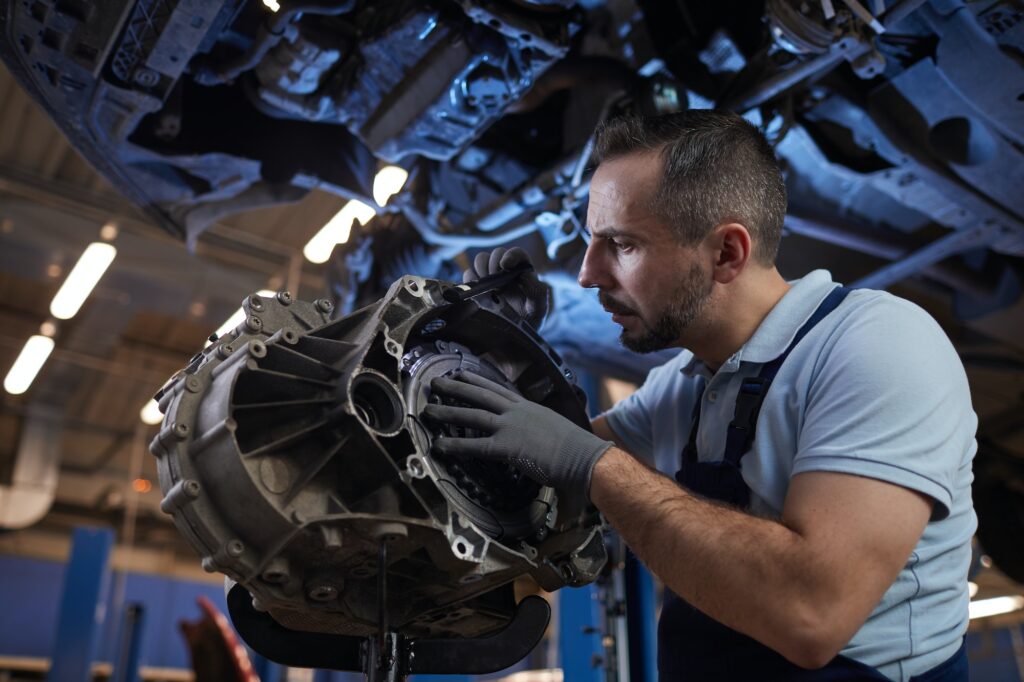
Wear Resistance
Another important property of iron castings is their wear resistance. Iron has a high melting point, making it resistant to abrasion and corrosion. This means that parts made from iron will last longer than those made from other materials, such as aluminum or plastic. This makes them ideal for use in brake systems where friction between the brake pads and rotors can cause wear over time.
So, iron castings are an excellent choice for the automotive industry due to their strength, wear resistance, and thermal conductivity. They provide reliable performance, durability, and a long lifespan, making them perfect for use in a wide range of applications. If you’re looking for strong and durable parts for your vehicle, iron castings are definitely worth considering.
The automotive industry is a hugely competitive sector, requiring versions of components to be swiftly replaced and improved upon on a regular basis. The best materials to create these components often come in the form of iron castings which have been specifically designed to offer wear resistance – the ability to resist erosion caused by movement as material slides and rubs against another surface.
The property of wear resistance that is provided by iron castings used in the automotive industry means that components are made with an incredibly long life span, helping automotive companies remain successful even whilst adapting their models and designs quickly.
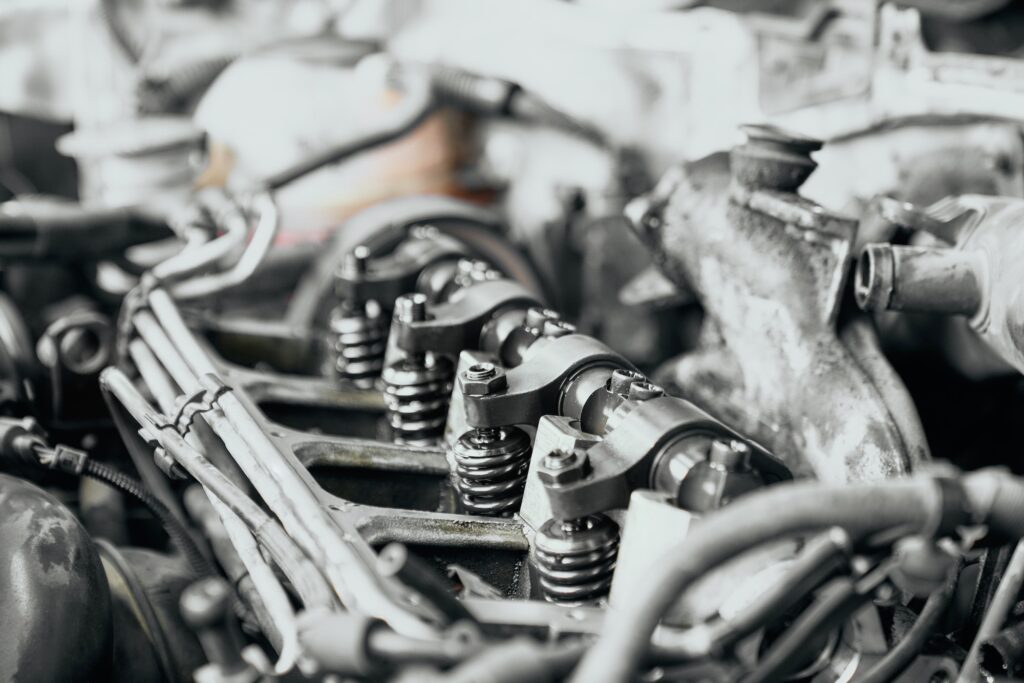
Thermal Conductivity
Iron also has high thermal conductivity, making it ideal for engine components like cylinder heads and blocks. This allows heat to be transferred quickly away from these parts which help keep the engine running at its optimal temperature range. It also helps reduce wear on these components by reducing the amount of heat buildup that can occur during operation.
So, iron has excellent thermal conductivity properties, making it well suited for use in components that need to dissipate heat quickly and efficiently. This helps ensure that engines run cooler and more efficiently while also reducing wear on internal components due to excessive heat buildup.
The thermal conductivity property is essential when selecting materials for use in the automotive industry. The ability to conduct heat defines the capabilities of various materials, including iron castings. The thermal conductivity of the materials used to produce iron castings is directly related to their success in the automotive industry, with higher grades offering better strength and durability plus improved temperature regulation.
The versatility of iron castings for automotive applications means that manufacturers can quickly and easily build components that can handle even some of the most extreme conditions thrown at them from day-to-day or occasional use. The advantage of not having to switch out components regularly contributes heavily towards increased profits across the entire industry.
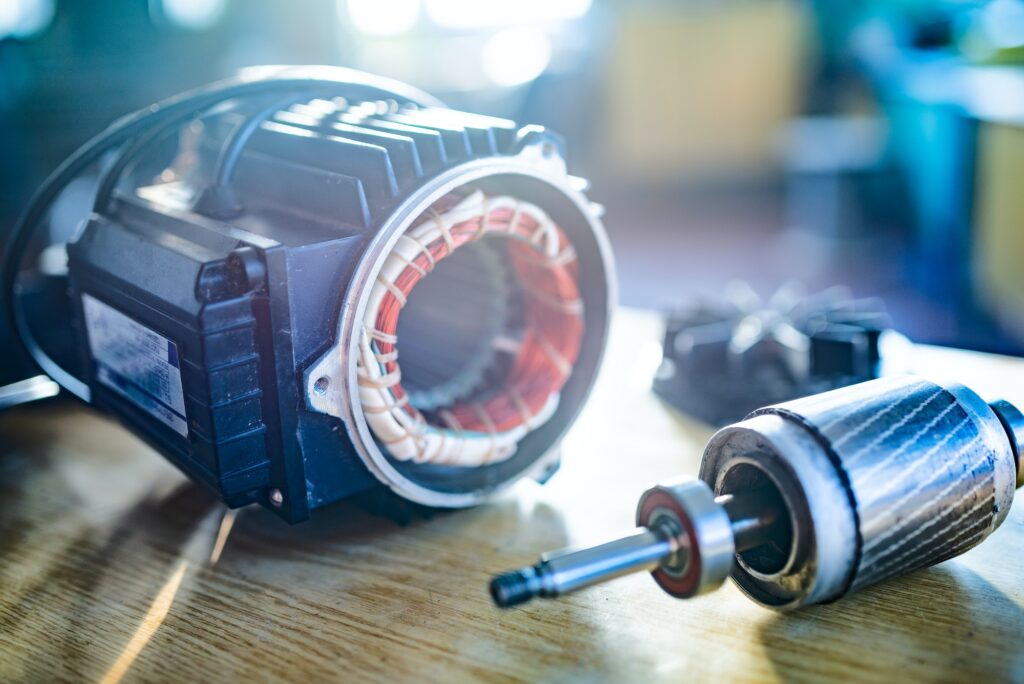
Cost-Effective
Iron castings are cost-effective compared to other materials, such as aluminum or plastic, due to their lower production costs. This makes them an attractive option for automakers who need to quickly produce large quantities of parts without breaking their budget.
Iron castings have many benefits in automotive applications due to their strength, wear resistance, thermal conductivity, and cost-effectiveness compared to other materials such as aluminum or plastic. They are an essential part of any vehicle’s construction process, helping ensure that each part is built with quality materials that will last for years.
The automotive industry is highly dependent on the property of iron castings due to their cost-effectiveness and range of applications. These properties include high wear resistance, enhanced impact strength, ease in fabrication, superior machinability for intricate structures, appreciable resistance to corrosion, and absorbing vibrations.
The cost-effectiveness of iron castings makes them suitable for a wide variety of applications in cars and other related industries, including connecting rods, bearing caps and brackets, transmission shafts, and flanges. Seven out of ten components used in automobiles are manufactured from iron castings because they are more economical than those made from other materials.
The automotive industry has witnessed an increasing demand for property of iron castings that can effectively reduce costs while maintaining performance levels.
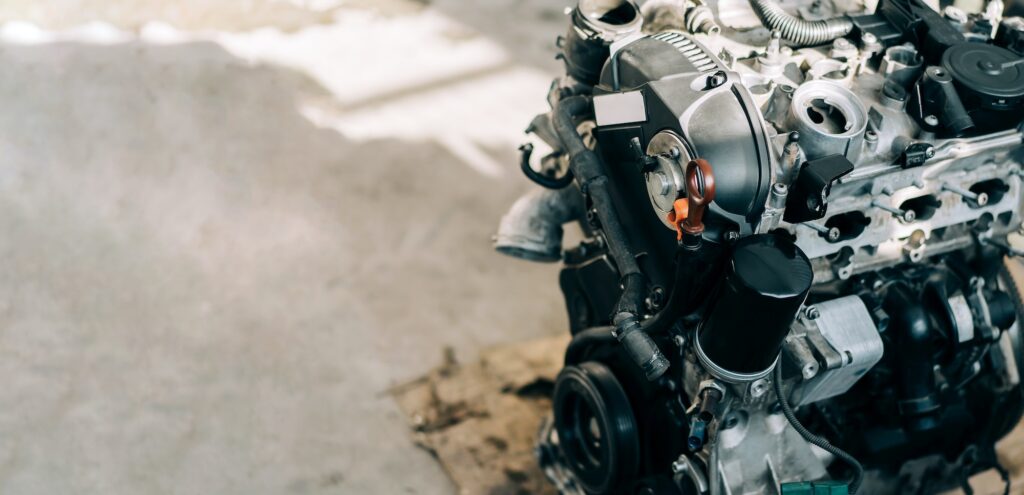
Malleability and Machinability
Iron castings are also known for their malleability and machinability. This means they can be easily shaped into complex shapes without sacrificing any strength or integrity. This makes them ideal for parts that require intricate designs or precise tolerances. Additionally, iron can be machined quickly and accurately with minimal waste material produced during production.
The automotive industry relies upon The Property of Iron Castings (TPIC) for its most cost-effective production of parts. The TPIC process allows them to create reliable, confidence-inspiring parts that make vehicles safer and lower the overall cost.
The cost-effectiveness achieved through the use of The Property of Iron Castings is unmatched, as it reduces material wastage and improves product quality while cutting assembly costs.
The team at TPIC continually strives to develop new techniques and technologies to cut costs further while providing the highest level of production quality. Therefore, The Property of Iron Castings is an invaluable asset to the automotive industry in terms of time and cost savings.
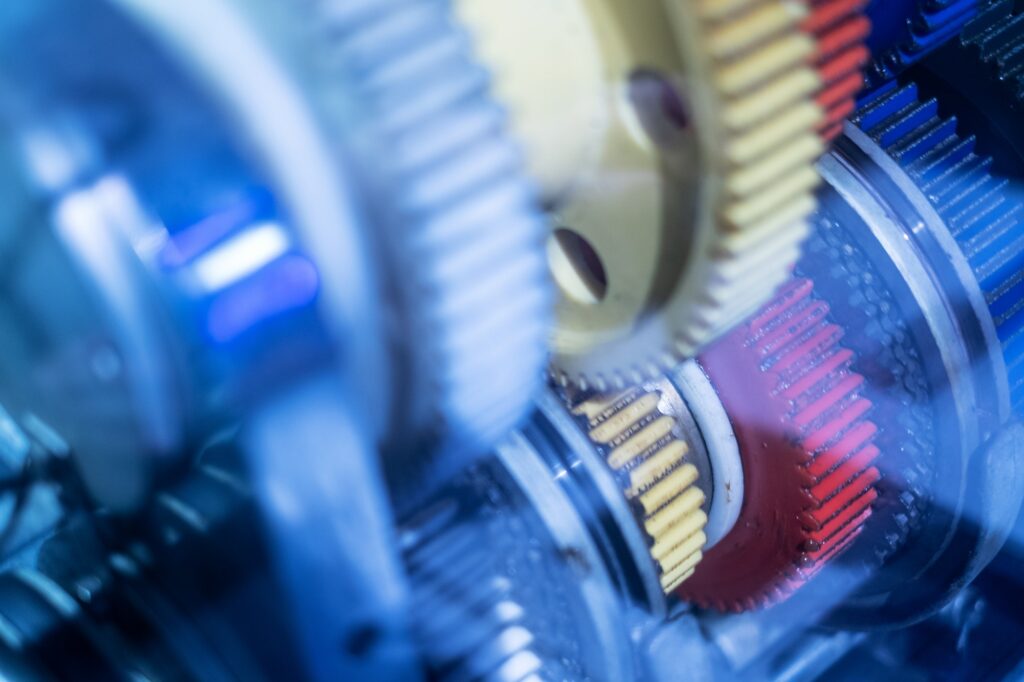
Resistance To Wear And Tear
Because iron castings are strong but still malleable enough to be shaped into intricate shapes using molds or special tools, they can be used in parts that need to bear intense pressure without breaking or becoming deformed over time.
This makes them an excellent choice for parts made from superior materials like aircraft engines or turbochargers that require precise geometry and high levels of resistance to wear and tear from intensive use.
The property of iron castings used in the automotive industry to resist wear and tear is exceptionally impressive. The use of these castings ensures that vehicles experience fewer breakdowns and require less maintenance over their lifespans.
The quality of the iron used in these castings reinforces engine parts, making them more resistant to vibrations, hard braking, and sudden acceleration. The importance of this resistance to wear and tear cannot be overstated as it contributes significantly towards longer lasting functioning of a vehicle’s essential parts.
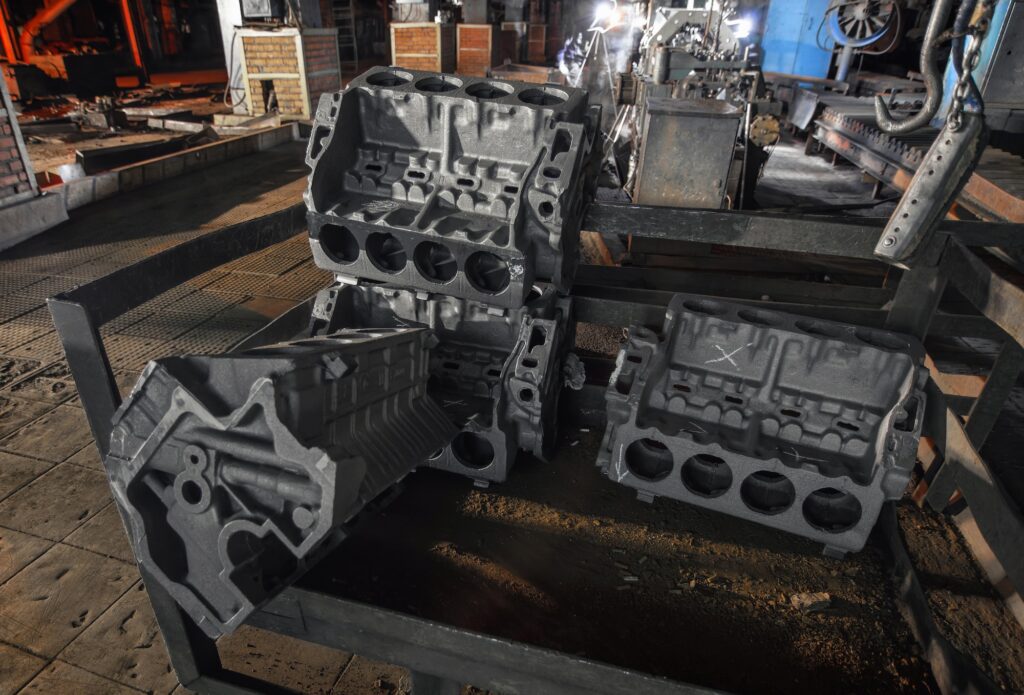
Versatility
Iron castings can be used in many different areas within the automotive industry due to their versatility. They can be found in anything from small components like valves and pumps to larger components such as transmissions, axles, clutches, diffs, manifolds, and exhaust systems.
Furthermore, iron castings have proven extremely effective when used with other metals, such as aluminum alloys or stainless steel, which offer additional strengths while still maintaining high-performance levels.
The property of versatility makes iron castings used in the automotive industry a particularly attractive material for carmakers. The ability for iron castings to be formed and structured into many different shapes allows carmakers to create highly detailed parts with intricate designs that make modern cars visually appealing and efficient.
The strength of iron castings also enables them to withstand wear and tear often encountered by parts used in the automotive industry, allowing car manufacturers to rest assured that their cars remain well-functioning over time. The versatility of iron castings thus provides valuable benefits to the automotive industry, making cars look aesthetically pleasing and work reliably for years.
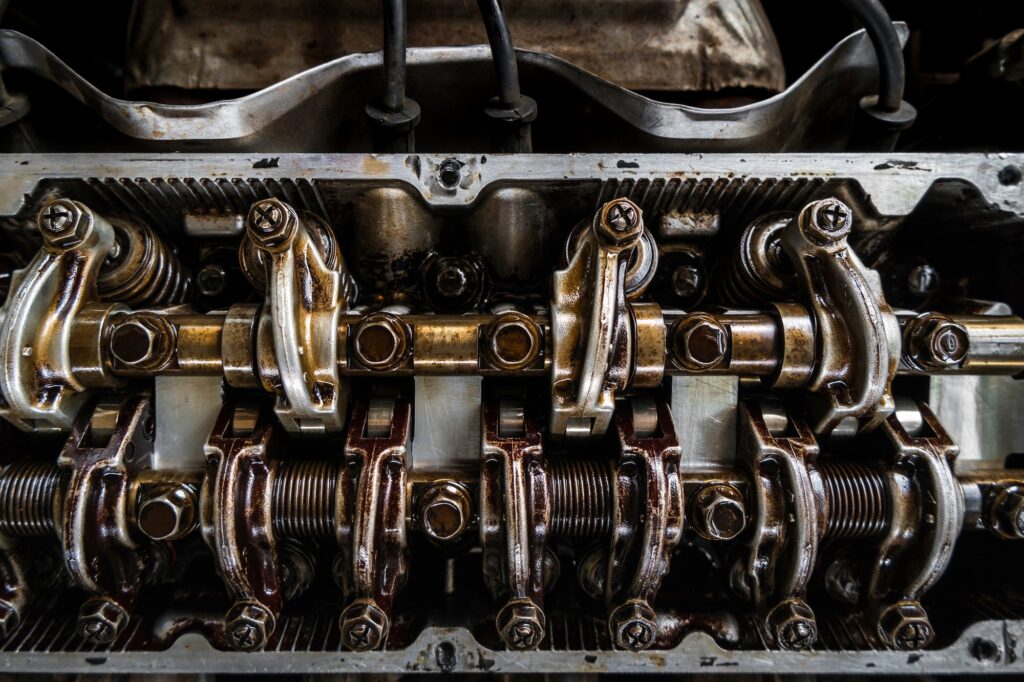
Corrosion Resistance
Another important property of iron castings is their corrosion resistance. These metals have very low corrosion rates, which helps ensure that car components will last longer without corroding or rusting over time due to exposure to elements like moisture or saltwater air.
This makes them ideal for use in coastal areas where cars may be exposed to saltwater air regularly, as well as moist environments which could otherwise cause rusting over time if not properly protected with corrosion-resistant materials like iron castings.
The automotive industry has immense demands when selecting materials for components used in their vehicles. Corrosion resistance property is especially important, which is a major advantage of iron castings. The specific alloy and process-related parameters must be considered when choosing the most precise material for a given application.
The chemistry and microstructure of the castings are examined closely to ensure that full corrosive protection is guaranteed for long-lasting results. The optimal choice provided by iron castings provides this essential long-term protection, further enhancing the durability and performance of each component used in the automotive industry.
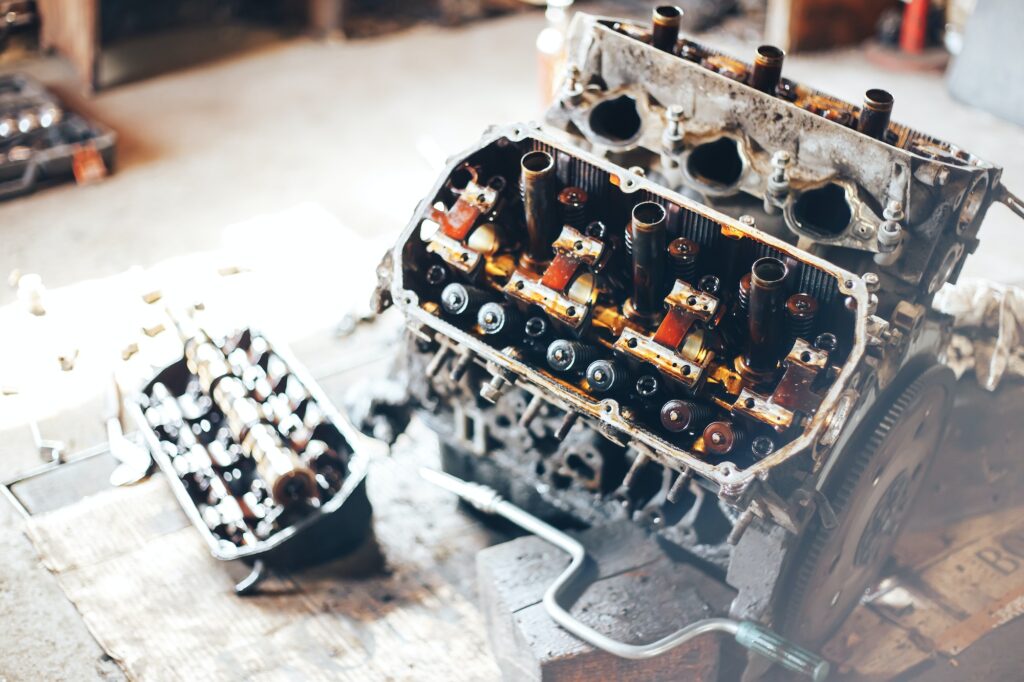
Heat Resistance
Iron castings are also highly heat resistant, making them perfect for engines and other auto parts that must withstand frequent heat cycles due to normal operating conditions within a vehicle’s engine bay or exhaust system.
The ability to withstand high temperatures helps ensure that car components remain stable even when exposed to extreme conditions inside engines and exhaust systems, thus providing better performance over time with fewer repairs needed due to wear caused by excessive heat exposure.
The automotive industry looks for heat resistance when selecting materials and components for a vehicle, and iron castings are the ideal choice due to their high metallurgical properties.
The heat resistance inherent in iron castings makes them an excellent choice for engine blocks and exhaust manifolds due to the exposure to high temperatures associated with internal combustion engines. Iron castings’ ability to endure extreme temperatures, often up to 1100 degrees Fahrenheit, ensures that cars will continue running at optimal performance.
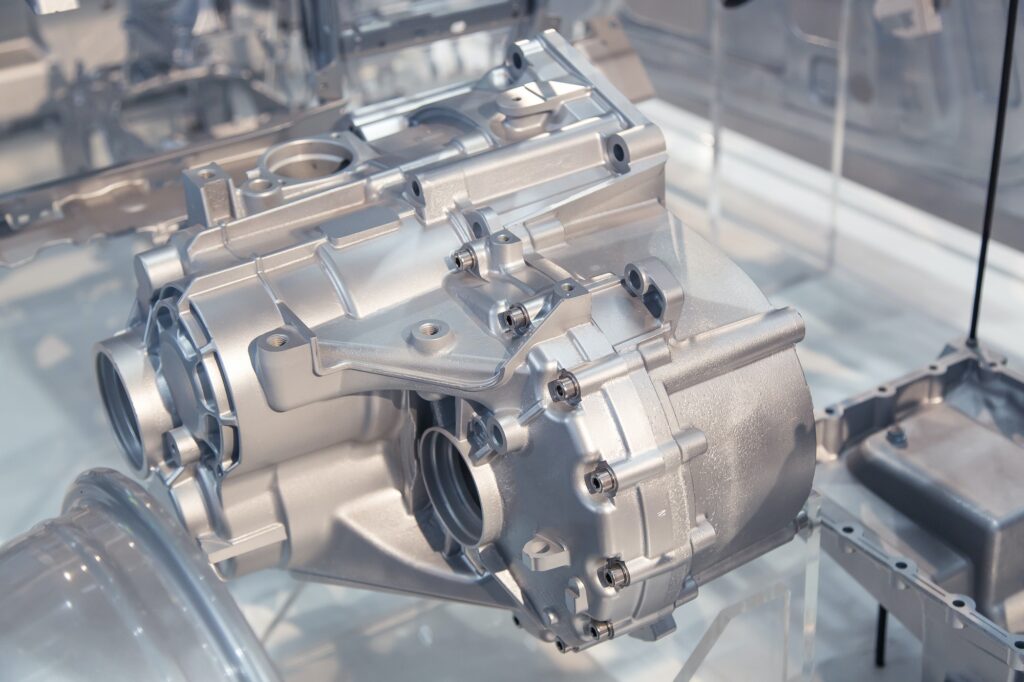
Conclusion
Overall, iron castings offer many advantages over other materials when used in the automotive industry. Their strength and durability make them ideal for use in high-stress applications, while their cost-effectiveness ensures they remain affordable even when used in large quantities.
Additionally, their malleability and machinability make them perfect for complex designs, while their thermal conductivity helps keep engines running cool even under extreme conditions. All these factors combine to make iron an invaluable part of today’s automotive industry.
We are Castimoo, a supplier of iron castings. Specializing in the custom production of gray cast iron and ductile iron products for you. We have a very successful experience in automotive, power generation equipment, machinery and other fields. If you have any need to purchase iron castings, we are always there for you.