Introduction
The production of iron castings has been an important part of the industrial revolution.
It is molded using a mixture of iron and coarse abrasives that are pressurized on a workbench. The advent of molding machines has made a huge difference in this industry.
This article will explain in detail what are the machines used for molding when producing iron castings, and what are the characteristics of each.
Hand molding
Before the molding machine was produced, people are used to mold iron castings by hand. The process of casting iron castings by hand consists of several steps.
First, the raw materials must be mixed together in the correct proportions. This is usually done by combining the metal ore with other substances such as sand, ash or other compounds that help bind the metal together.
Once the mixture is created, it must be heated until it becomes a molten liquid. Depending on the type of metal used, this can take anywhere from a few minutes to several hours.
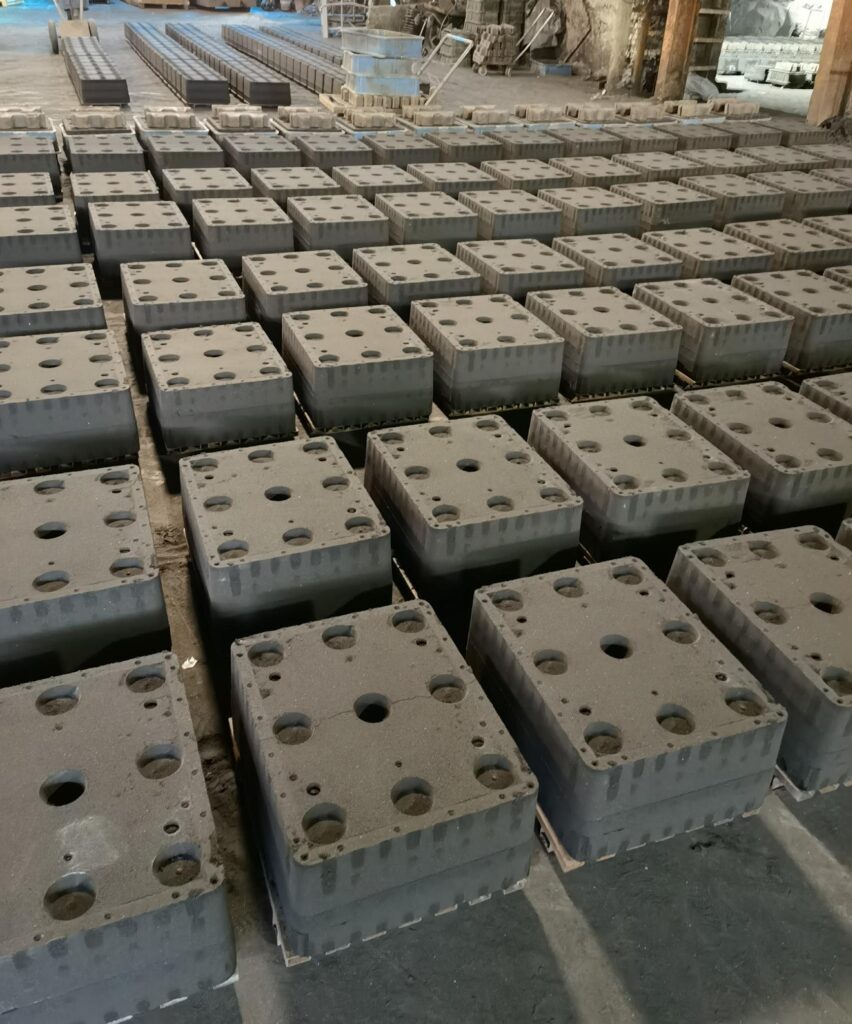
Once the metal has melted and become a liquid, it must be poured into a mold before it hardens again.
This is where the manual mold maker comes into play, as they must carefully control the temperature and timing of the poured metal to ensure that it fills all the cavities in the mold correctly.
The mold itself can be made of sand or graphite and will determine how thick or thin the walls of each casting will be.
Finally, after the mold has been poured and allowed to cool, any excess material is removed with a hammer or other tool so that only the finished part remains.
Hand molding offers many advantages over mechanized processes, such as lower costs because expensive machines and tools do not have to be purchased; greater flexibility in making parts because there are no fixed rules or specific parameters; better control of parts because each part is touched directly during production; and because there is no waiting for machines to set up or reset between runs. Therefore turnaround times are faster.
In addition, hand molding typically produces more consistent quality results because it is easier to detect small defects and inconsistencies in parts by hand than with automated systems.
Of course hand molding has its drawbacks. The biggest issue is the labor cost associated with hand molding, as multiple workers are required to participate in the process and it usually takes more time than an automated process.
It is not suitable for small, high volume orders. In addition, there is an increased risk of injury due to the nature of handling molten metal and heavy objects by hand.
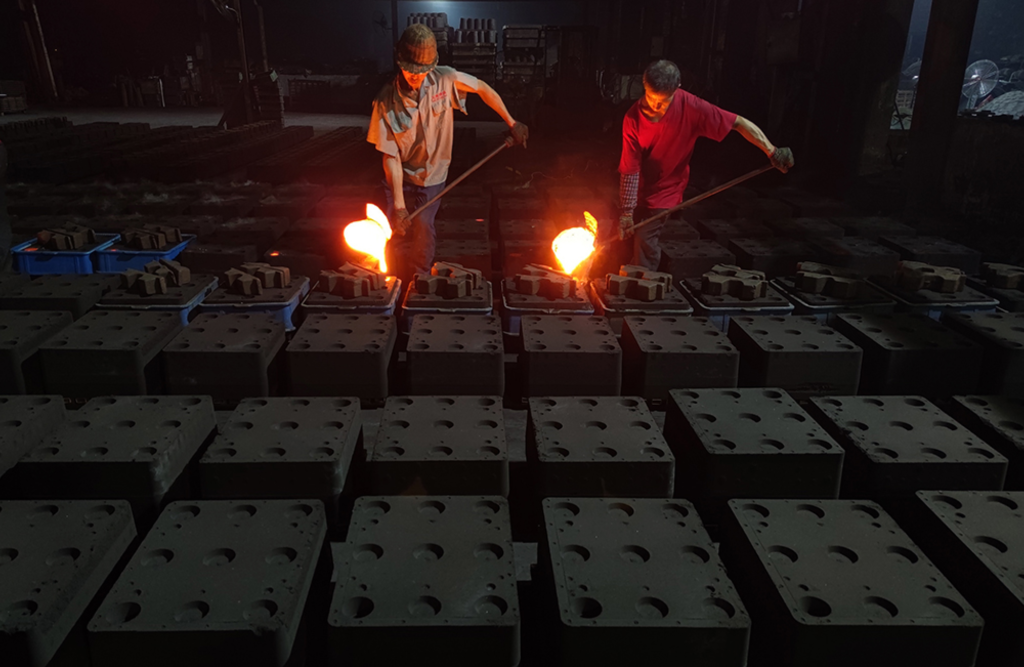
Semi-automatic molding
Commonly used is hydraulic bounce machine molding.
Bounce machine molding is a process used to produce iron castings. It involves the use of a semi-automatic molding machine to form a block of metal into the desired shape and size.
This type of process uses hydraulic pressure to force molten metal into a mold, which is made of sand or ceramic. The molten metal is then cooled and solidified to create the final product.
The process begins by preparing the mold by cleaning it, spraying a mold release agent on its inner surface, and then placing it on the bed of the molding machine.
Once in place, the molten metal is poured into the mold from an elevated pan, often using an automated pouring system to ensure accuracy and precision. At this point, the bounce phase begins as pressure is applied to each mold in order to create a vacuum seal within it.
This allows for greater pressure gain than can be achieved manually and helps ensure that all details within the casting are accurately molded, even allowing for the production of complex textures to customer specifications.
The final step in the process is to cool the castings after they have been removed from the mold. Depending on their size and composition, the cooling time can vary greatly.
Relatively small items may only take a few minutes, while larger items may take hours or even days to solidify for safe handling and shipping.
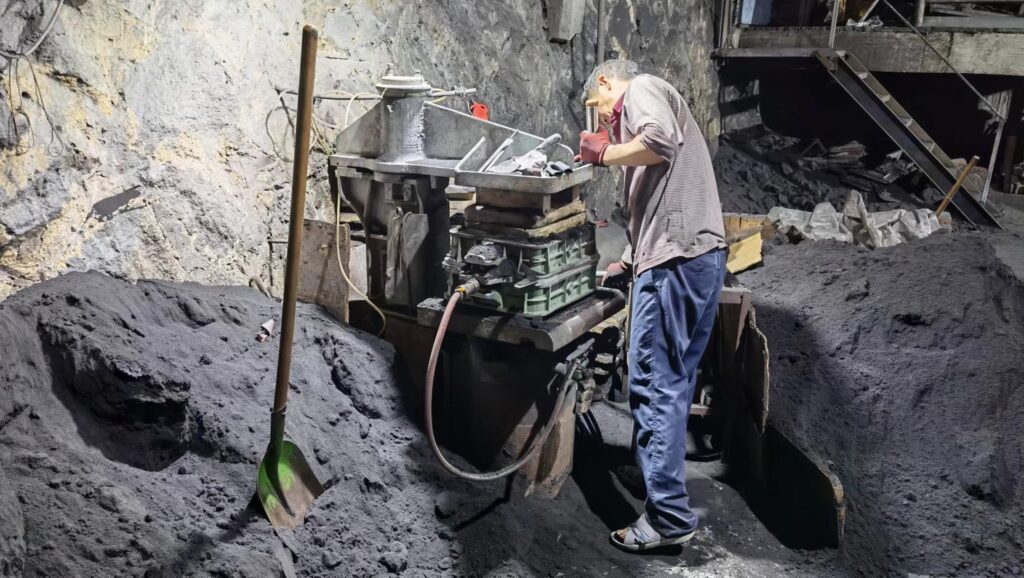
Overall, bounce molding has become an increasingly popular choice among manufacturers because of its ability to produce high-quality castings at a lower cost than traditional methods such as manual pressing. An added benefit of using this process is that it typically requires less labor, making it cost effective when mass production is required.
In addition, its superior detail molding capabilities make it ideal for those looking for complex castings with precisely measured and textured designs for their projects.
Automatic Molding
The process of using an automatic molding machine to make iron castings involves several steps that bring the casting closer to completion.
First, a pattern is designed and made, usually out of wood or plastic.
The pattern is then placed in a flask filled with enough sand to leave a cavity in the shape of the desired casting when the model is withdrawn. The pattern is then removed from the flask and molten iron is poured into the cavity left by its absence. As it cools, it becomes solidified and the shape of the casting is formed.
The next step in this process is core making.
This involves the creation of secondary cavities and channels inside the casting for cooling or other functions. The core is usually made of a sand or ceramic mixture and must be carefully positioned in the flask before casting to conform to the desired shape and function after cooling.
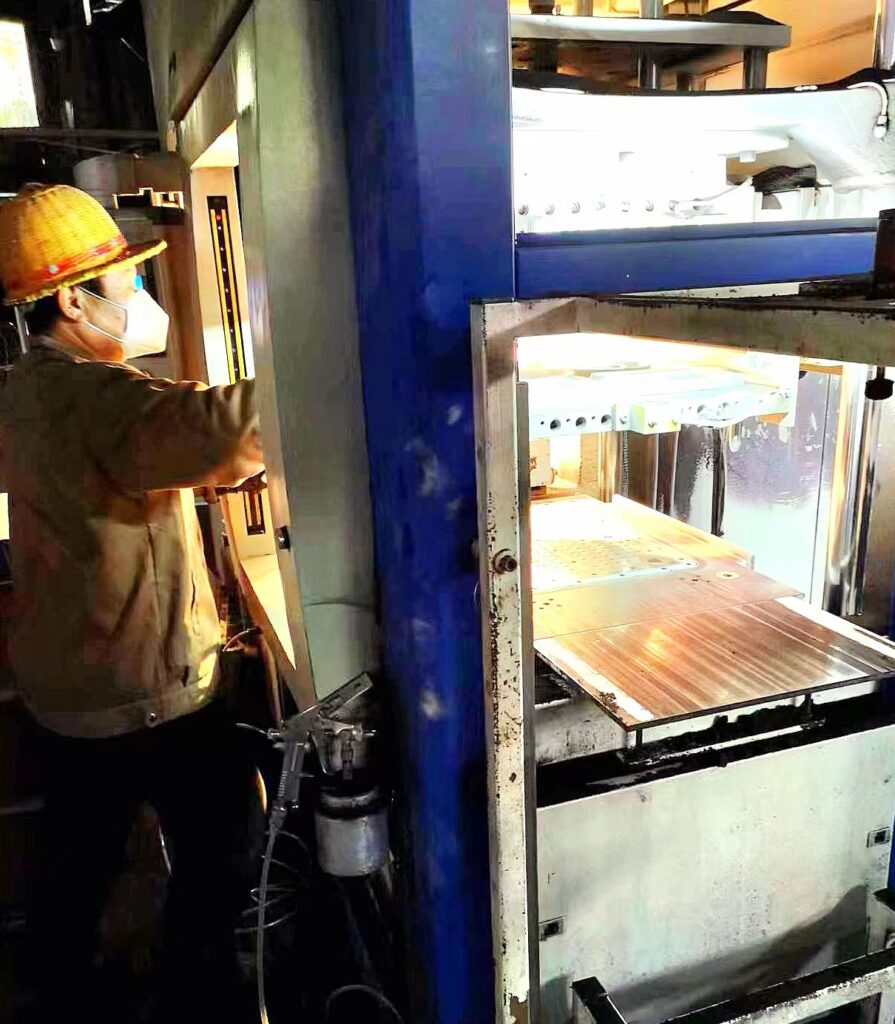
Once these processes are complete, a pouring system is attached to introduce air into the mold cavity during pouring to help prevent entrapment of air while filling the metal fluid, while allowing excess gas pressure to escape, as well as minimizing turbulence when introducing the metal fluid into the complex geometry of the casting cavity.
Finally, after all the necessary preparation steps have been completed, it is time to perform the actual molding on the automatic molding machine.
In order to start the molding, it is necessary to transfer the molten iron from the external container (usually called ladle) to the internal container called runner or gate plate on the machine, which acts as a conduit for the molten metal transfer during the filling operation.
The filling operation starts at low pressure and low temperature to prevent thermal shock to the part being molded and continues until all the internal cavities are filled with liquid metal, balanced on all sides within each cavity, and then firmly hardened after cooling.
In summary, the production of iron castings using an automatic molding machine involves first creating a pattern, positioning the core correctly before pouring the molten iron into the flask, installing the gate system on the machine prior to molding, such as runners/gate plates, etc., conveying the molten iron from the external tank through the internal channels into the casting cavities, while controlling the temperature/pressure throughout the filling process and equalizing before completion to ensure that the entire operation meets high quality production standards, with a high quality end product every time.
Advances in technology have enabled machines to take over most of the processes that were once done manually.
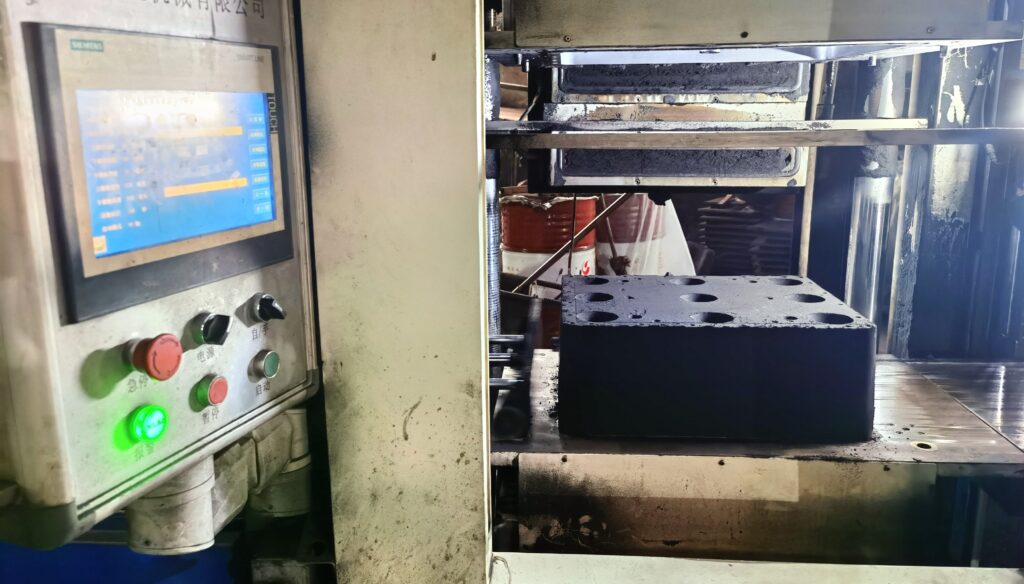
Machines used to cast iron castings include core shooters, plunger machines and centrifugal casting machines, among others. All of these machines use different methods to form the desired shape from molten metal with greater accuracy and consistency than hand forming.
Core shooting machines are the most common automatic molding machines used to produce the precise shapes and sizes inside iron castings.
Plunger machines use a plunger-like tool to force molten metal into various details or cavities in the mold, producing complex shapes with little operator input.
Finally, a centrifugal casting machine rotates the mold around a central axis, flinging molten metal at high speed to the sides of the mold to create castings with smooth surfaces and uniform thickness.
Whichever method you choose, automatic molding machines can help you get the job done quickly and efficiently.
No matter which type of molding machine you use, they all have one thing in common: They offer superior accuracy, consistency and reliability in production operations, while allowing you to create complex shapes or intricate details quickly and efficiently without sacrificing quality or performance standards.
By understanding the characteristics of each molding process, you can choose the right one for your project so you get great results every time.
Conclusion
As the cost of labor rises, mechanized systems offer even more advantages. They require less labor and can produce larger quantities of castings quickly, reducing costs for manufacturers.
In addition, they can closely replicate the complex shapes of computer-aided designs with a high degree of accuracy, making them ideal for customers who need complex parts that meet exact specifications.
Castimoo specializes in the design and production of gray cast iron and ductile iron and has 30 years of experience in the iron casting industry.
Having gone through the stages of manual and semi-automatic moulding, Castimoo is now equipped with two automatic moulding lines to provide you with the most complete and efficient solutions.
If you have a need to purchase iron castings, welcome to contact me.