Introduction
Cast iron is a process that has been around for centuries. It is a method of making metal objects by pouring molten iron into a mold. The process of making iron castings can be difficult because it is important to control the temperature of the iron to get the desired result. In this blog post, we will discuss how to control the temperature of the iron water to make high quality iron castings.
Why is it important to control the temperature of the molten iron?
When making iron castings, the temperature of the molten iron is generally controlled at approximately 1,520°C (2,749°F). This temperature is ideal because it allows the iron to maintain its malleability.
If the molten iron is too cold, the molten iron will not flow through the mold and will result in an uneven shape. On the other hand, if the molten iron is too hot, it can lead to cracks or other defects in the casting. By properly controlling the temperature of the molten iron, you can produce high quality iron castings.
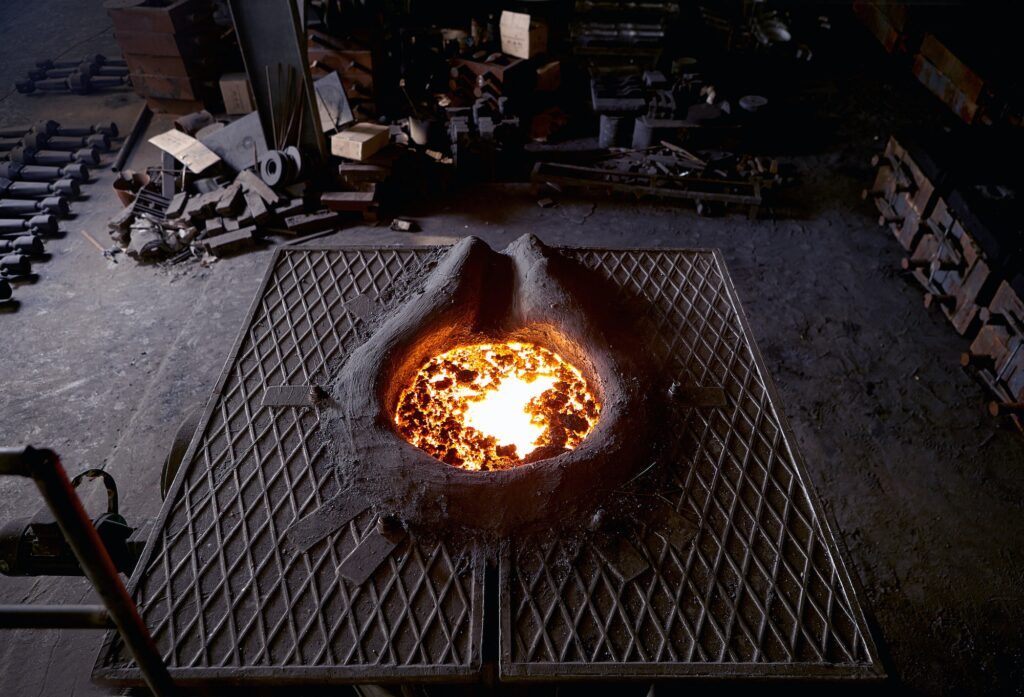
7 Ways to Control the Temperature of Molten Iron
1. Heat evenly
One way to control the temperature of the molten iron is to ensure that the molten iron is heated evenly throughout the casting process. The furnace should be equipped with temperature control devices and heat shields to prevent the molten iron from getting too hot.
In addition, controlling the temperature of the molten iron can be achieved by using slag and fluxes, which help insulate the molten iron and create a more uniform heat distribution.
The addition of carbon-based materials such as graphite provides a protective layer for the molten iron while also heating it more evenly.
Another technique is to add a thermocouple to the outside of the mold, which will allow for more precise temperature control.
Finally, less stirring can help maintain uniform heat throughout the pouring process.
2. Use a cold mold or core
A second way to control the temperature of the molten iron is to use a cold mold or core. This method involves placing a metal mold or pre-prepared shape into the molten iron, which will absorb some of its heat and cool it down.
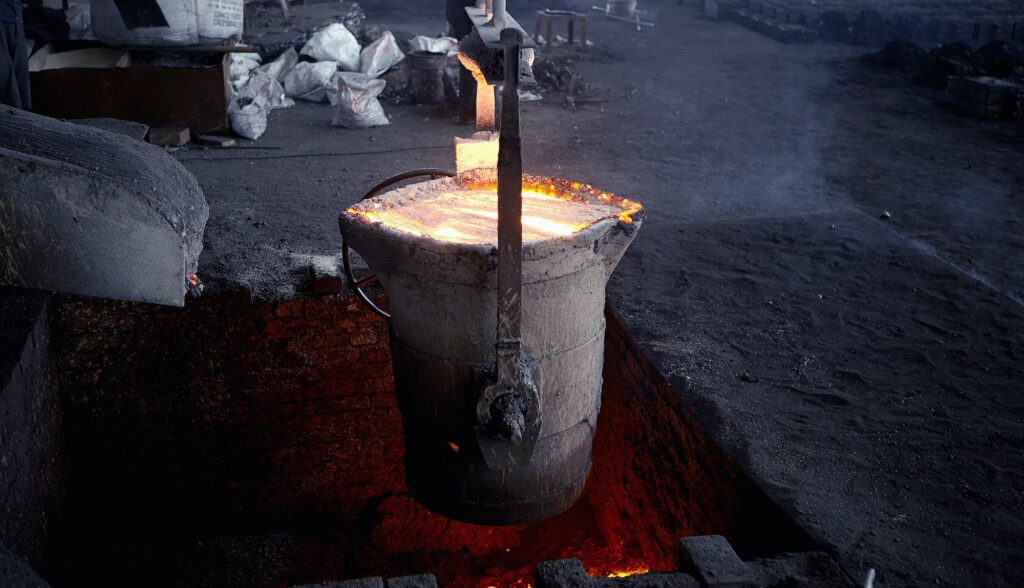
The mold or core can be made of a variety of metals, including aluminum, copper and cast iron. The key to the success of this method is to ensure that the molten iron does not exceed the melting point of the metal in the cold mold or core.
In addition, the temperature of the molten iron can be controlled by a process called “cold forging”. In this process, cold steel bars are used to form shapes and objects in the molten iron. The cold steel bar absorbs some heat from the molten iron to cool it down.
3. Add a heat sink
A third way to control the temperature of the molten iron is to add a heat sink, such as graphite or clay. This material absorbs some of the excess heat from the molten iron and helps maintain a stable temperature. Heat sinks are typically used in electric furnaces, but can also be used to cool molten iron.
Adding a radiator is a cost-effective measure that not only helps maintain a stable temperature of the molten iron, but also reduces energy costs and increases productivity.
Radiators provide an efficient way to transfer heat away from the furnace without the additional expense of cooling fans. Installing a radiator in the furnace also helps to reduce emissions and save energy because it prevents the iron from overheating.
4. Use an inert gas environment
A fourth way to control the temperature of the iron is to use an inert gas environment in the casting process. A furnace filled with an inert gas (such as nitrogen or argon) can help keep the temperature of the molten iron from rising too quickly.

This is achieved by reducing the amount of oxygen in contact with the molten iron, as it reduces the rate at which oxidation (combination with oxygen) occurs.
The use of an inert gas environment has other benefits for controlling the temperature of cast iron. For example, it helps to reduce heat loss and maintain a more uniform temperature. This is especially important for larger castings, as conventional methods have difficulty maintaining uniform temperatures over such large volumes.
An inert gas environment not only helps to control the temperature of the iron, but also helps to improve the quality of the casting. When oxygen reacts with iron and other metals during the oxidation process, it produces products of oxides.
These oxides can negatively affect the mechanical properties of the casting, such as strength and ductility. By reducing the amount of oxygen in contact with the iron, the inert gas environment helps to reduce the formation of oxides, thereby improving the quality of the casting.
In addition, the use of an inert gas environment in the casting process helps to reduce the risk of burns and improves safety. Molten iron is extremely hot and can burn if exposed to air. An inert gas environment helps isolate the molten iron from oxygen, thereby reducing the risk of burns and other hazards.
5. Use thermocouples
A fifth way to control the temperature of the molten iron is through the use of thermocouples or other temperature sensitive devices. Thermocouples have the advantage of being able to measure temperature extremely accurately and at a very low cost. This makes them a popular choice for many operations that require precise temperature control.
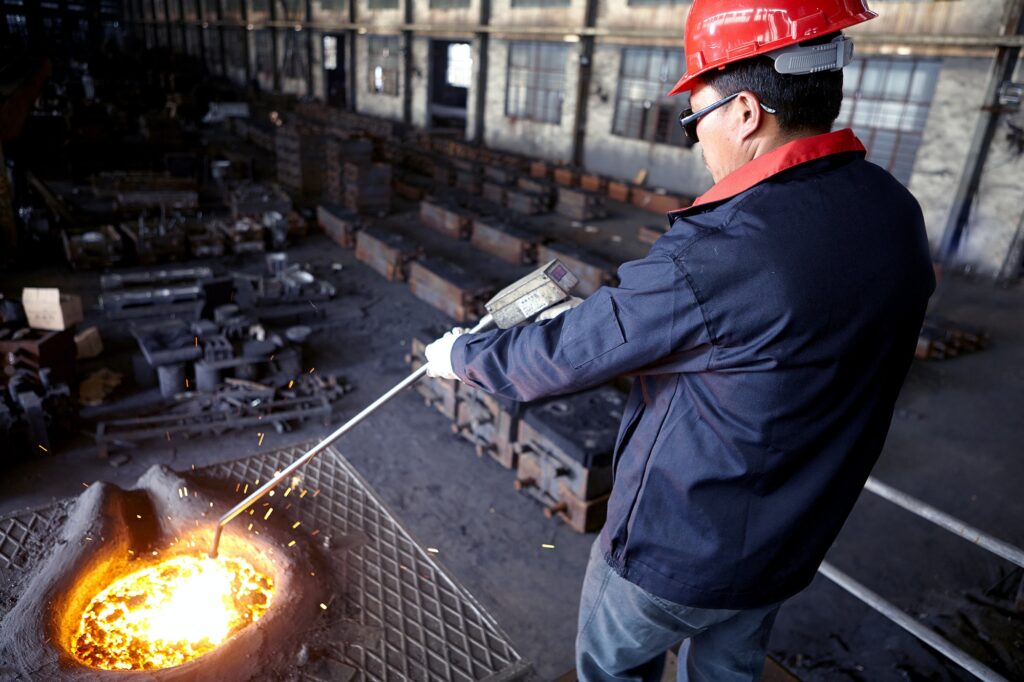
Thermocouples work on the principle of the difference in voltage between two different metals when they are heated or cooled. Thermocouples have two wires connected to a junction that heats or cools with the temperature of the iron. As the temperature of the junction changes, the voltage of each wire changes. This voltage change can be detected and used as an indication of how high or low the temperature of the molten iron is.
Thermocouples are an effective and cost-efficient way to measure and control the temperature of molten iron, allowing operators to maintain a high level of accuracy in their operations. They can be used in a variety of applications, such as controlling the temperature in a furnace or monitoring the temperature in a cast iron production process. With thermocouples, operators have greater control over their process and can ensure that they are producing parts of consistent quality.
6. Add cold water or sand
A sixth method of controlling the temperature of the iron is to add cold water or sand to the iron and cool it down. This method is typically used when the molten iron is too hot and needs to be cooled quickly.
Adding cold water or sand to the hot molten iron will help to lower its temperature immediately. This is because when the heat of the molten iron comes in contact with the cold water or sand, an energy exchange occurs that lowers the temperature of the metal. This can be done by pouring cold water directly over the molten iron or by adding mounds of sand to the molten iron.
The amount of water or sand needed for cooling depends on the temperature of the molten iron and the desired temperature you want to achieve. It is important to make sure that you add it gradually to avoid a rapid drop in temperature, which can lead to cracking and distortion of the metal.
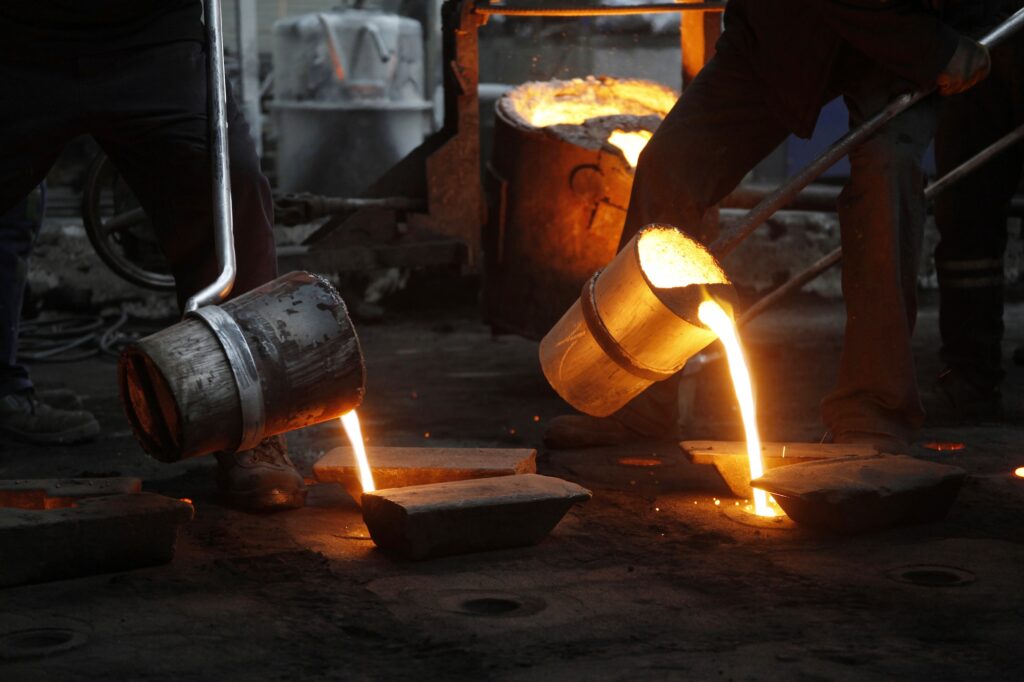
7. Control the pouring rate
The seventh method of controlling the temperature of the molten iron is to control the pouring rate of the molten iron. This method is relatively simple and efficient because it helps to distribute the heat more evenly throughout the molten iron. By controlling the pouring speed, different temperatures can be maintained in different parts of the molten iron.
For example, if the iron is poured too fast, the heat from the molten iron will escape too quickly, resulting in a lower temperature. However, if the pouring is too slow, the heat will build up and increase the temperature of the molten iron.
Therefore, to ensure that the desired temperature of the molten iron is achieved, it is important to pour at a steady rate so that the heat is evenly distributed. This steady rate can be maintained by adjusting the pouring speed using various control devices such as valves, pumps and flow controllers.
By carefully controlling the pouring rate of the molten iron, it is possible to maintain a uniform temperature throughout the casting process. This makes it easier for manufacturers to produce quality products with consistent performance. In addition, controlling the pouring speed helps to reduce energy consumption, as it prevents excessive heat from being wasted.
Controlling the pouring rate of the molten iron is an important part of maintaining a consistent temperature throughout the casting process and producing a high quality product. It is a simple and effective way to help manufacturers save time and achieve desired results while saving money and energy.
Conclusion
Temperature is critical to iron processing because it affects most of the physical properties included in the deformation process, such as impact strength, fatigue strength, plastic deformation characteristics, and weldability. In addition, the normal iron casting process is also very dependent on the correct temperature.
By using these different techniques, it is possible to effectively control the temperature of the molten iron during the casting process and to ensure that the highest possible quality iron castings are produced. With careful planning and attention to detail, anyone can create strong and durable cast iron products with consistent results every time.
Castimoo is an iron casting supplier. Specializing in ductile iron and gray cast iron. Our perfect quality control process has made our products well accepted by domestic and foreign customers. If you need to purchase iron casting products, please contact me. We hope that through cooperation, we can bring you more benefits.