Introduction
In the world of iron casting, sand casting remains a widely utilized and cost-effective method for producing intricate and robust components. However, like any manufacturing process, it comes with its fair share of challenges. At Castimoo, your trusted Chinese iron casting supplier, we understand the importance of addressing these challenges to deliver exceptional products.
In this comprehensive guide, we will delve into the common challenges encountered in sand casting and provide valuable insights on how to overcome them. Whether you’re in China, the USA, Japan, Europe, or any other part of the world, these tips will help you achieve top-quality iron castings.
1. Sand Quality Matters
Challenge: Inconsistent sand quality can lead to defects in castings, such as surface roughness and porosity.
Solution: Source high-quality molding sand, regularly test its properties, and implement strict quality control measures to ensure consistency.
When it comes to sand casting, the quality of the molding sand is of paramount importance. The sand serves as both the mold material and the parting agent, making it a critical factor in the final quality of your iron castings. Common challenges related to sand quality include inconsistencies in grain size, moisture content, and contaminants.
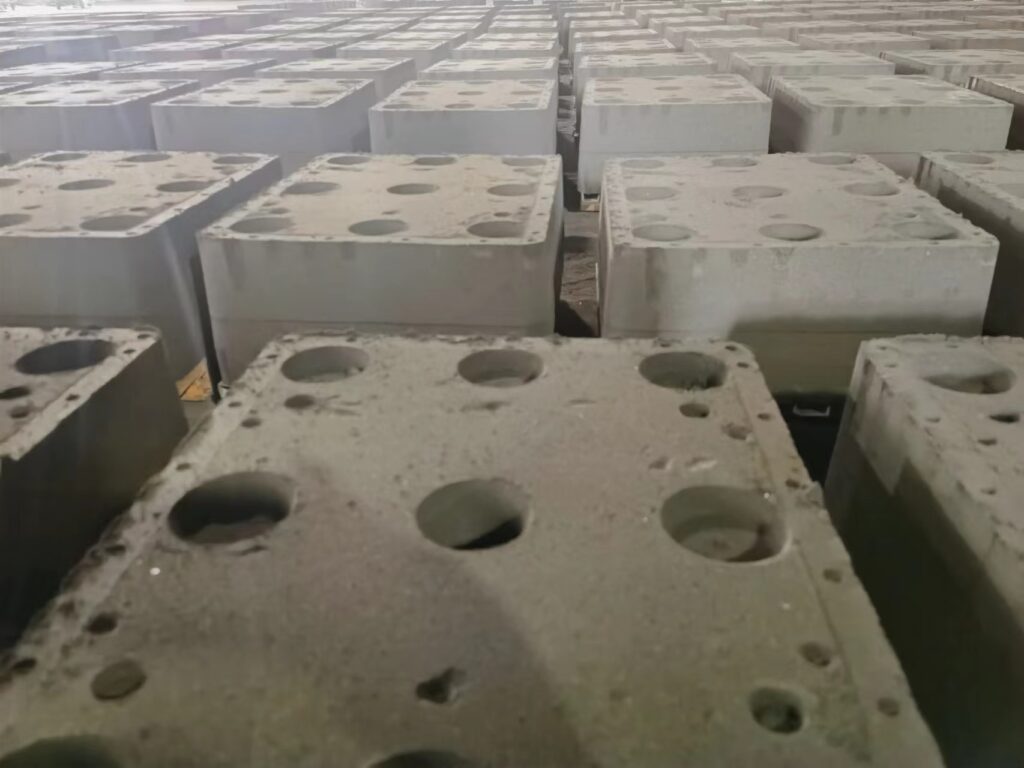
Sourcing High-Quality Molding Sand
To overcome these challenges, it’s crucial to start with high-quality molding sand. Your choice of molding sand can significantly impact the casting process’s success. Look for sand suppliers who specialize in foundry-grade molding sand, which is specifically processed and graded for casting applications. Foundry sand should have the following characteristics:
Consistent Grain Size: Inconsistent grain size can lead to surface roughness and defects in your castings. Ensure that the sand has a uniform grain size distribution.
Low Moisture Content: Excess moisture can cause steam to form during pouring, leading to defects like pinholes and porosity. Ensure that the sand has a low and controlled moisture content.
Low Contaminants: Contaminants like clay, silt, and organic matter can adversely affect mold quality. Choose sand with minimal impurities.
Regular Sand Testing
Once you’ve sourced high-quality molding sand, it’s essential to monitor and maintain its properties consistently. Regular sand testing is a critical part of this process. Key tests for molding sand include:
Green Sand Properties: Assess properties like green compression strength, green shear strength, and compactibility to ensure the sand can hold its shape and support the casting.
Moisture Content: Maintain the desired moisture content to prevent issues during casting.
Permeability: Adequate permeability is necessary for proper venting and gas evacuation in the mold.
Clay Content: Keep an eye on clay content to prevent mold cracking and improve mold hardness.
Implementing Quality Control Measures
To maintain consistent sand quality, it’s essential to implement stringent quality control measures within your foundry. This includes:
Storage and Handling: Properly store and handle molding sand to prevent contamination and moisture absorption.
Sand Reclamation: Invest in sand reclamation systems to recycle and reuse molding sand efficiently, reducing waste and costs.
Routine Inspections: Regularly inspect the sand for any signs of contamination or degradation, and take corrective actions as needed.
By addressing the challenge of sand quality head-on through sourcing, testing, and quality control measures, you can significantly enhance the success and consistency of your sand casting process.
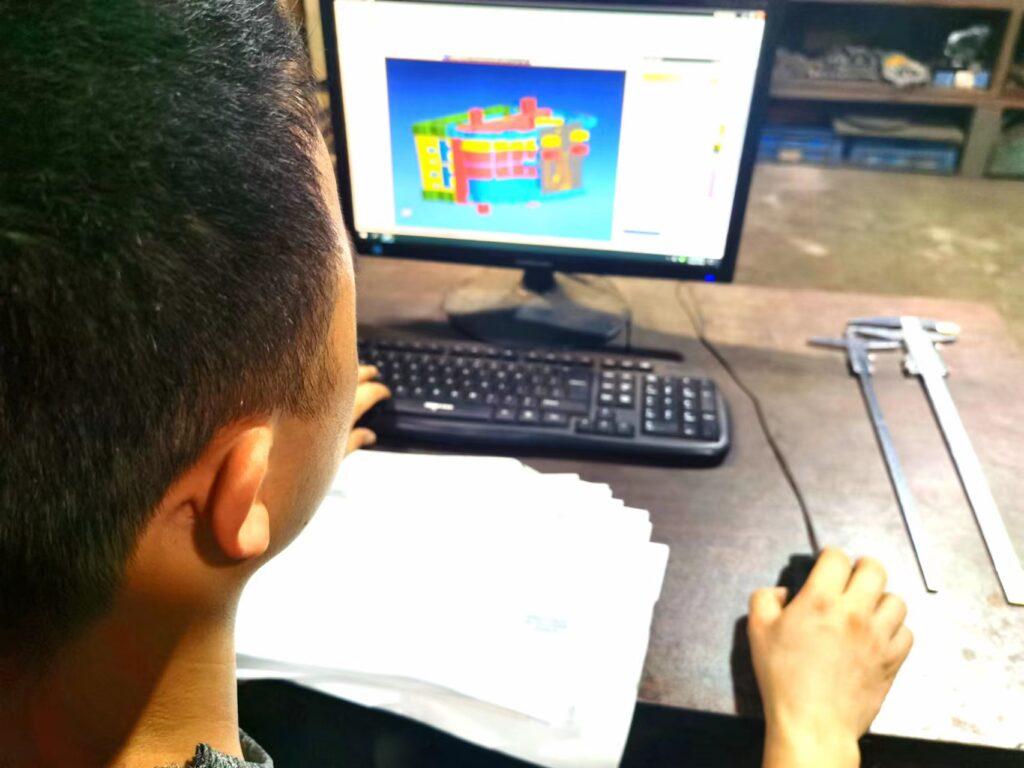
2. Proper Pattern Design
Challenge: Inadequate pattern design can result in casting defects, such as warping, shrinkage, and mismatched parts.
Solution: Invest time in meticulous pattern design, accounting for factors like draft angles, fillets, and parting lines.
Pattern design is a crucial step in the sand casting process, as it directly influences the quality and accuracy of the final iron casting. Common challenges associated with pattern design include warping, shrinkage, and the misalignment of parts.
Meticulous Pattern Design
To overcome these challenges, it’s essential to invest time and expertise in the pattern design phase. Here are key considerations for achieving success in pattern design:
Draft Angles: Incorporate draft angles on vertical surfaces of the pattern. Draft angles allow for easy removal of the pattern from the mold and prevent damage to the mold cavity. Typically, a draft angle of 1-3 degrees is sufficient.
Fillets and Radii: Incorporate fillets and radii on sharp corners and edges of the pattern. This helps reduce stress concentrations and the risk of cracking during casting.
Parting Lines: Ensure that parting lines (the lines where the mold separates into cope and drag) are strategically placed to minimize casting defects. Properly aligned parting lines contribute to even metal flow and consistent casting thickness.
Core Prints: Design and place core prints effectively to support the cores used in the mold. Adequate core print design prevents core shift and misalignment during molding.
Shrinkage Allowance: Account for shrinkage in your pattern design. Patterns should be slightly larger than the final desired dimensions to compensate for the shrinkage of molten metal as it cools and solidifies.
Pattern Material: Choose pattern materials that can withstand the rigors of the casting process. Common materials include wood, plastic, and metal, depending on the casting volume and complexity.
Pattern Inspection: Regularly inspect and maintain your patterns to ensure they are free from damage or wear that could affect casting quality.
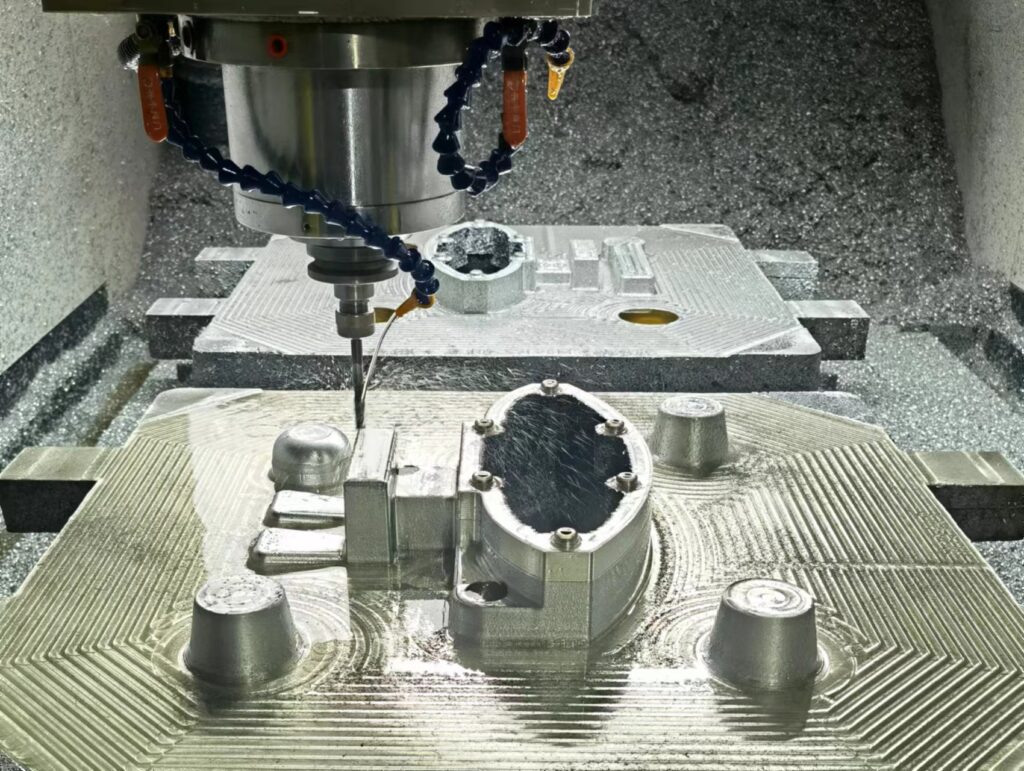
Pattern-Making Techniques
Pattern-making is both an art and a science. Experienced pattern makers use a combination of traditional craftsmanship and modern technologies like CNC machining to create precise and repeatable patterns. The choice of pattern-making technique depends on the complexity of the casting and the required production volume.
For intricate and low-volume castings, handcrafted wooden patterns or 3D-printed patterns may be suitable. These methods offer flexibility in design but may be time-consuming for larger production runs. In contrast, CNC-machined patterns are ideal for high-precision, high-volume castings, offering unparalleled accuracy and consistency.
By investing in meticulous pattern design and employing appropriate pattern-making techniques, you can address common challenges related to pattern design and pave the way for high-quality iron castings.
3. Venting and Gating
Challenge: Poor venting and gating can cause trapped gases and metal to not flow evenly, leading to defects like porosity and inclusions.
Solution: Design effective venting and gating systems, ensuring smooth metal flow and proper gas evacuation.
Effective venting and gating systems are critical components of a successful sand casting process. Venting and gating play pivotal roles in ensuring proper metal flow, preventing defects, and achieving consistent casting quality.
Venting for Gas Evacuation
One of the primary purposes of venting in sand casting is to facilitate the escape of gases generated during the casting process. Trapped gases, such as air and volatile compounds, can lead to defects like porosity and inclusions in the final casting. To overcome this challenge:
Strategically Place Vents: Design and position vents strategically throughout the mold to allow gas to escape. Vents are typically narrow channels that connect the mold cavity to the outside. They should be placed at locations where gas is likely to be trapped, such as near complex geometry or deep pockets.
Vent Size and Placement: The size and placement of vents depend on factors like mold size, casting material, and mold hardness. Consult with experienced foundry personnel or use simulation software to determine optimal vent design.
Vent Material: Choose vent materials that can withstand the heat and abrasion of the casting process. Common materials include ceramic or metal vent inserts.
Vent Maintenance: Regularly inspect and maintain vents to prevent blockages and ensure their effectiveness.
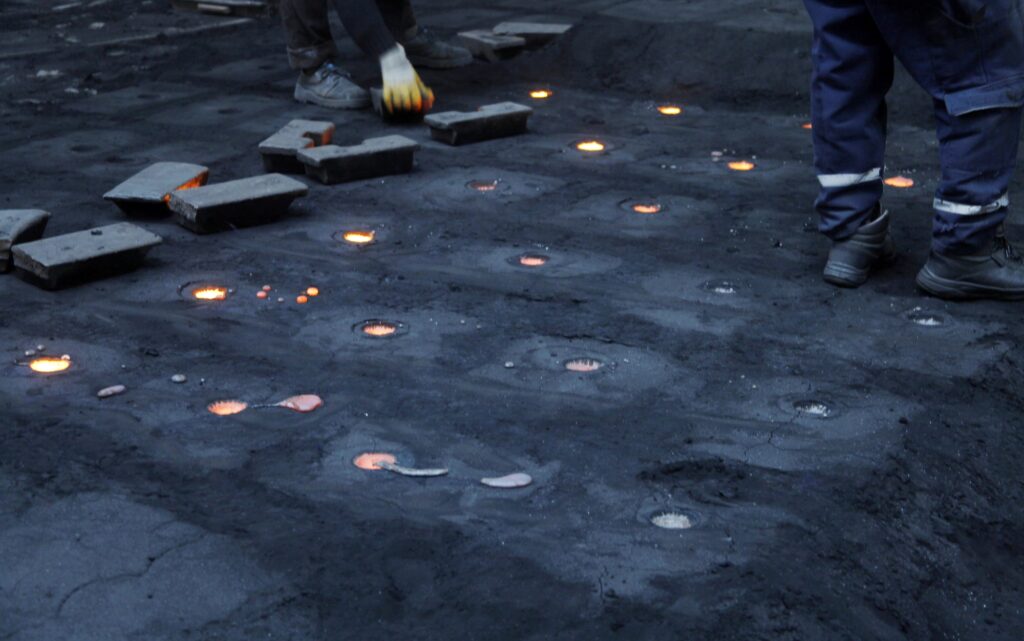
Gating for Smooth Metal Flow
Gating refers to the system of channels and gates that guide molten metal into the mold cavity. Proper gating design is essential for achieving uniform metal flow, preventing turbulence, and minimizing the risk of defects such as misruns and cold shuts. Here are key considerations for effective gating:
Sprues and Runners: Design sprues and runners to ensure a smooth and controlled flow of molten metal. The geometry and size of these components should match the casting’s requirements.
Ingate Design: Properly position ingates (the entry points from the runner into the mold cavity) to allow for even metal distribution. Avoid sharp changes in direction that can cause turbulence.
Risers: Include risers (also known as feeders) to provide a reservoir of molten metal that can compensate for shrinkage as the casting solidifies. Risers should be designed to feed the casting without introducing defects.
Gating System Optimization: Utilize gating system simulation software to optimize gating design for specific casting geometries and materials.
Exothermic Feeder Sleeves: Consider using exothermic feeder sleeves to enhance feeding capacity and reduce the risk of shrinkage-related defects.
Simulation and Prototyping
To ensure the effectiveness of your venting and gating systems, consider using casting simulation software. These tools can model the casting process, allowing you to visualize and optimize the flow of molten metal and the escape of gases. Simulation helps in making informed decisions about vent and gate design before actual casting, reducing the likelihood of defects and the need for costly trial-and-error adjustments.
4. Controlling Pouring Temperature
Challenge: Incorrect pouring temperatures can result in issues like cold shuts, hot tears, or excessive shrinkage.
Solution: Monitor and control pouring temperature rigorously, considering the type of metal being cast and the mold material.
The temperature at which molten metal is poured into the mold is a critical factor that directly impacts the quality and integrity of the casting. Controlling pouring temperature is essential to avoid defects such as cold shuts, hot tears, and excessive shrinkage.
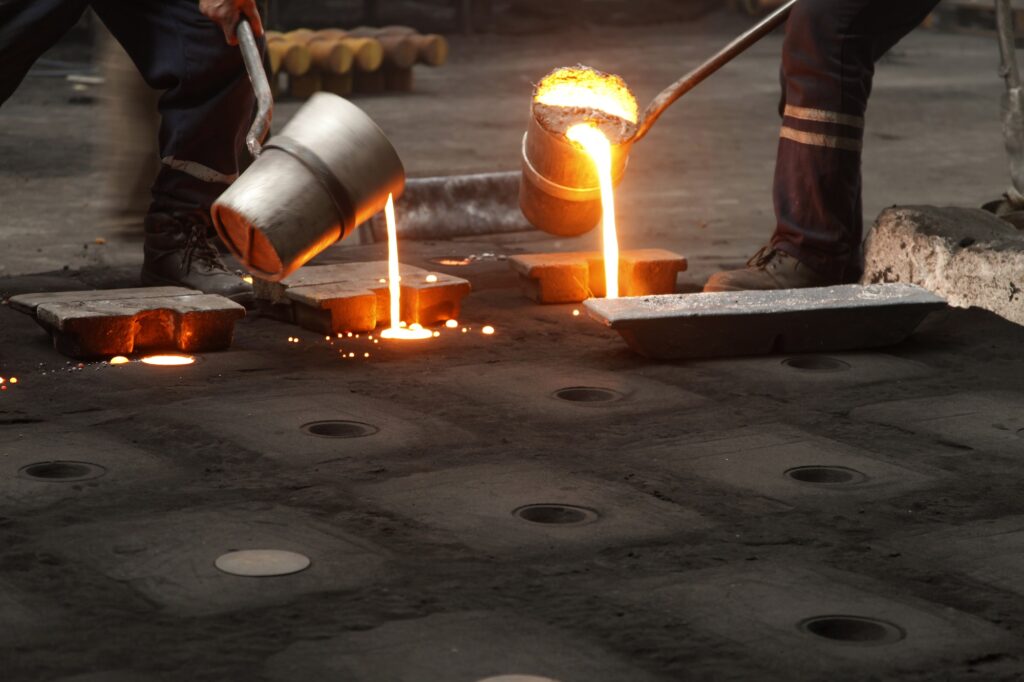
Pouring Temperature Considerations
When addressing the challenge of controlling pouring temperature, several key considerations come into play:
Metal Type: Different metals have different pouring temperature ranges. It’s crucial to understand the specific requirements of the metal you’re casting. For example, cast iron typically requires higher pouring temperatures than aluminum.
Mold Material: The type of mold material also influences pouring temperature. Insulating molds, such as those made of sand, may require slightly higher pouring temperatures to compensate for heat loss during pouring.
Thermal Analysis: Consider conducting thermal analysis of the mold to determine the appropriate pouring temperature. This analysis helps account for heat transfer and solidification patterns within the mold.
Pouring Rate: The rate at which molten metal is poured into the mold can affect the temperature distribution and casting quality. A controlled and consistent pouring rate is essential.
Preheating: In some cases, preheating the mold can help maintain the desired pouring temperature. This is particularly relevant for large or thick-walled castings.
Monitoring and Control: Invest in temperature monitoring and control systems to ensure that the pouring temperature remains within the specified range throughout the casting process.
Avoiding Common Pouring Temperature Pitfalls
To overcome the challenges related to pouring temperature, be aware of common pitfalls and mistakes to avoid:
Overheating: Excessive pouring temperature can lead to issues like burn-on, which occurs when the metal reacts with the mold material, leaving a rough surface.
Underheating: Insufficient pouring temperature can result in incomplete filling of the mold, leading to cold shuts and other defects.
Temperature Variation: Inconsistent pouring temperature can cause variations in casting quality, particularly in large molds. Maintain temperature uniformity throughout the pour.
Thermal Stress: Rapid temperature changes or thermal shocks can cause cracking in the casting. Gradual temperature changes are preferred.
Consultation: Consult with metallurgists or experienced foundry personnel to determine the appropriate pouring temperature for your specific casting requirements.
By rigorously monitoring and controlling pouring temperature, you can address one of the critical factors influencing the quality of your iron castings. It’s a precise balance that, when achieved, contributes to defect-free and high-quality results.
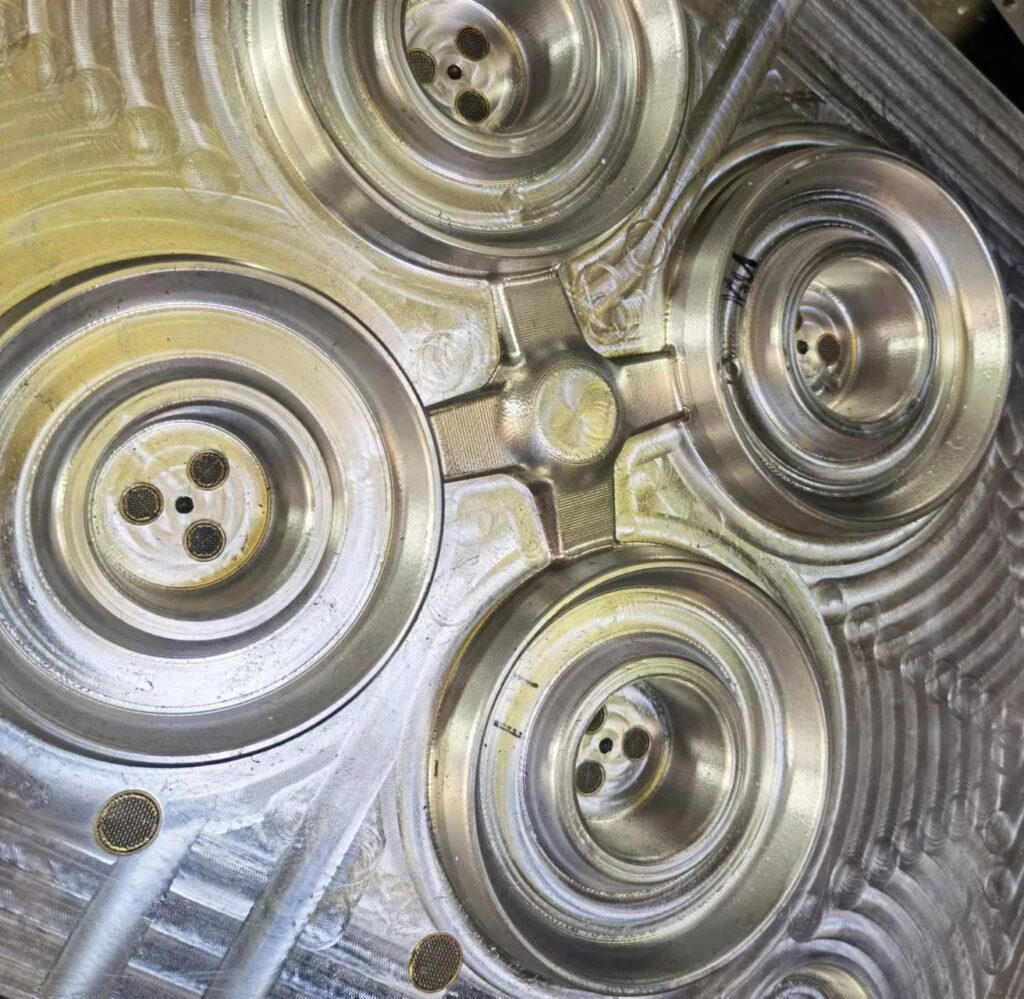
5. Mold Handling and Curing
Challenge: Mishandling molds or inadequate curing can lead to mold breakdown, compromising casting integrity.
Solution: Train staff in proper mold handling and curing techniques, and implement a strict maintenance schedule for molds.
Mold handling and curing are often overlooked aspects of the sand casting process, but they are crucial for maintaining mold integrity and ensuring consistent casting quality. Mishandling molds or neglecting proper curing can lead to mold breakdown and casting defects.
Proper Mold Handling
Molds are delicate structures, and mishandling can lead to damage, misalignment, or deformation. To address this challenge, consider the following best practices for mold handling:
Safe Transport: Use appropriate equipment and techniques to safely transport molds within the foundry. This includes the use of cranes, forklifts, or carts.
Avoid Impact: Prevent dropping or impacting molds, as this can lead to cracks or shifts in the mold components.
Secure Storage: Store molds in a clean and organized manner to prevent damage from accidental contact with other objects or environmental factors.
Proper Clamping: Ensure that molds are securely clamped and aligned during casting to prevent any movement that could lead to defects.
Mold Inspection: Regularly inspect molds for signs of wear, damage, or degradation. Address any issues promptly to prevent casting defects.
Effective Mold Curing
Curing is a critical step in the sand casting process that involves allowing the mold to set and dry before pouring molten metal. Inadequate curing can lead to mold breakdown, surface defects, and compromised casting integrity. Here’s how to achieve effective mold curing:
Curing Time: Follow the recommended curing time specified for the molding material being used. This can vary depending on factors such as sand type and environmental conditions.
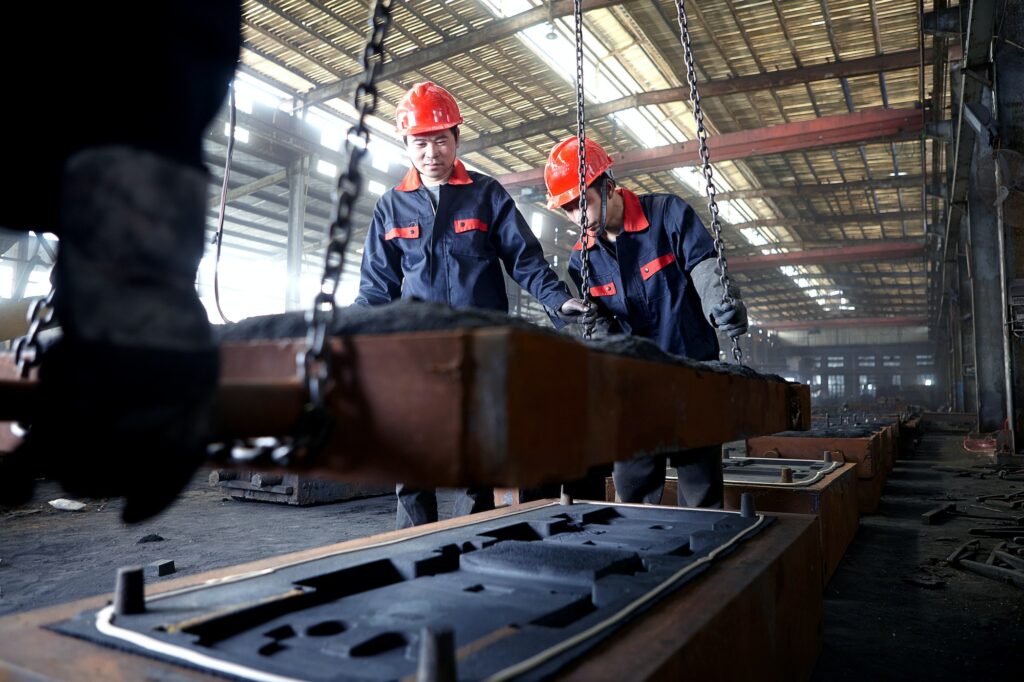
Humidity Control: Maintain the appropriate humidity levels during curing. Excessive moisture or rapid drying can lead to surface defects.
Temperature Control: Ensure that curing takes place within the recommended temperature range. Extreme temperatures can affect curing and mold integrity.
Ventilation: Provide adequate ventilation to allow moisture to escape during curing. Proper airflow can contribute to uniform curing.
Humidity Monitoring: Use humidity sensors or monitoring systems to track the curing environment and make adjustments as needed.
Mold Maintenance
Regular mold maintenance is essential for preserving mold quality and longevity. Implement a strict maintenance schedule that includes:
Cleaning: Periodically clean the mold surfaces to remove residual casting material, coatings, and debris.
Inspecting: Regularly inspect mold components, including cope and drag, for signs of wear, damage, or degradation.
Repair and Replacement: Promptly repair or replace any damaged or worn mold components to prevent defects in future castings.
Storage: Store molds in a clean and dry environment when not in use, protecting them from corrosion and damage.
Training and Education
Proper mold handling and curing techniques should be part of the training for your foundry personnel. Ensure that your team understands the importance of these processes and follows best practices. Training can significantly reduce the risk of mold-related defects and improve casting consistency.
By focusing on proper mold handling, effective curing, and proactive mold maintenance, you can overcome the challenge of mold breakdown and contribute to the overall quality and integrity of your iron castings.
6. Shrinkage and Stress Relief
Challenge: Inadequate consideration of shrinkage and stress relief can result in distortion and cracking of castings.
Solution: Develop a comprehensive plan for post-casting heat treatments and stress relief processes.
Shrinkage and stress relief are critical considerations in the sand casting process, as they directly impact the dimensional accuracy and integrity of the final iron casting. Inadequate attention to these factors can result in distortion, cracking, and other casting defects.
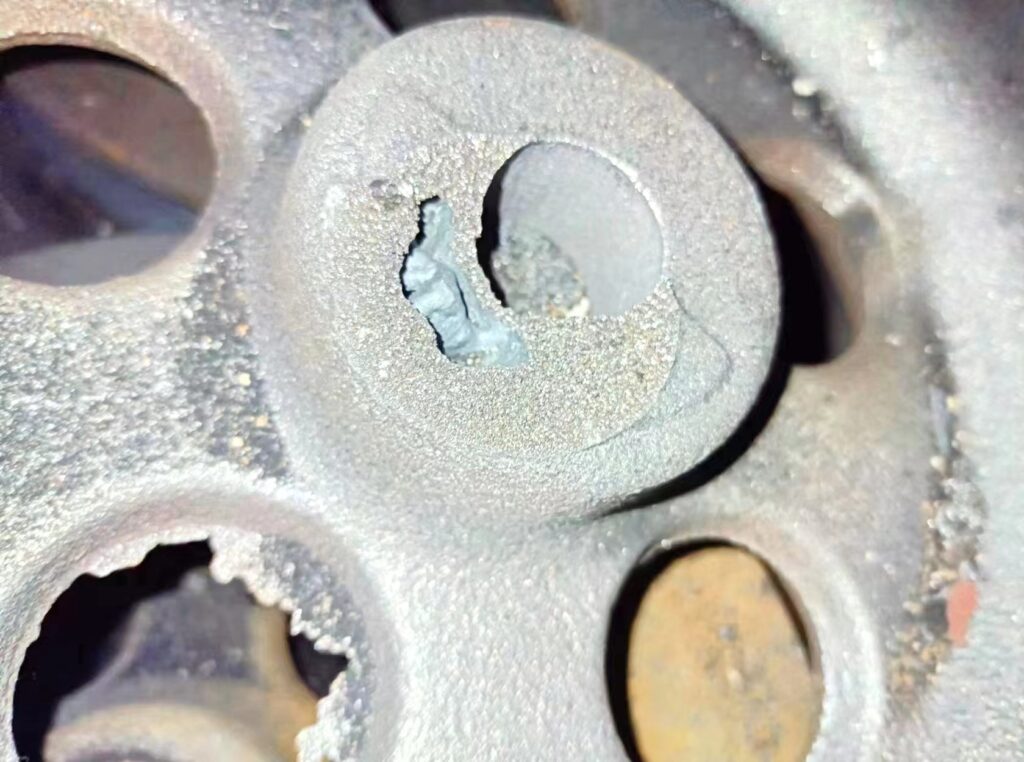
Understanding Shrinkage
Shrinkage occurs when molten metal cools and solidifies. During this process, the metal undergoes a reduction in volume, leading to a decrease in the dimensions of the casting. To address shrinkage-related challenges:
Shrinkage Allowance: In pattern design, incorporate a shrinkage allowance to compensate for the expected reduction in size during solidification. This allowance is typically based on the material being cast and the geometry of the part.
Riser Design: Design risers (also known as feeders) to provide a reservoir of molten metal that can compensate for shrinkage as the casting solidifies. Proper riser design can help prevent shrinkage-related defects.
Stress Relief
Stress can build up in a casting due to temperature gradients and solidification. This internal stress can lead to cracking and distortion if not properly managed. To address stress-related challenges:
Heat Treatment: Develop a comprehensive plan for post-casting heat treatment, which may include processes such as annealing, normalizing, or stress relieving. Heat treatment helps reduce internal stresses and improve casting stability.
Cooling Rate Control: Implement controlled cooling rates to minimize thermal gradients and stress buildup during solidification.
Residual Stress Analysis: Consider using residual stress analysis techniques to identify areas of high stress in the casting and make informed decisions about stress relief processes.
Importance of Cooling Rate Control
One of the critical aspects of preventing stress-related defects is controlling the cooling rate of the casting. Rapid cooling can lead to thermal shock and high levels of internal stress. To address this:
Insulation: Insulate the casting to slow down the cooling rate. Insulating materials or coatings can help maintain a gradual and uniform cooling process.
Post-Casting Heat Treatment: Utilize post-casting heat treatment processes to gradually reduce stress and stabilize the casting’s structure.
Cooling in Sand: Consider burying the casting in sand after pouring to provide a controlled and insulated cooling environment.
Riser Design for Shrinkage Compensation
Proper riser design is instrumental in addressing shrinkage-related challenges. Risers act as reservoirs of molten metal that feed the casting as it solidifies. Key considerations for riser design include:
Size and Placement: Ensure that risers are sufficiently large and strategically placed to compensate for shrinkage in critical areas of the casting.
Riser Efficiency: Evaluate the efficiency of risers in feeding the casting by analyzing their size-to-volume ratios.
Riser Removal: After solidification, remove risers and perform any necessary machining or finishing to achieve the desired casting dimensions.
By developing a comprehensive plan that considers shrinkage allowance, stress relief, and proper riser design, you can effectively address the challenges related to shrinkage and stress in sand casting, resulting in dimensionally accurate and structurally sound castings.
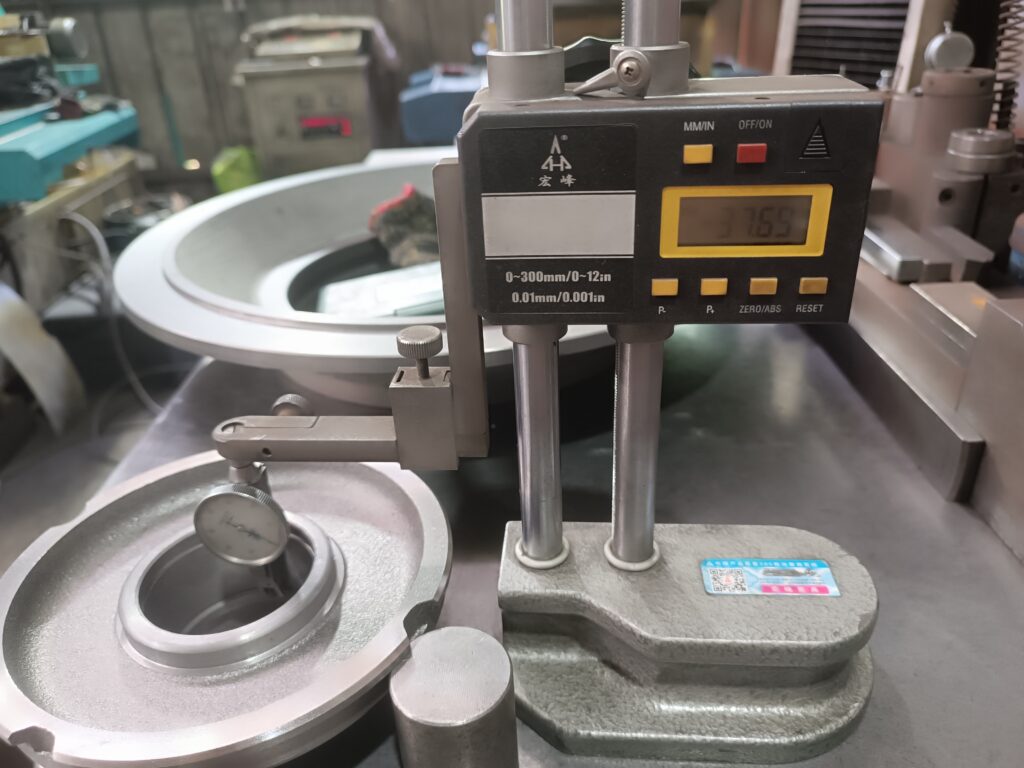
7. Quality Inspection and Testing
Challenge: Neglecting thorough quality inspection and testing can allow defects to go unnoticed.
Solution: Establish a rigorous quality control process that includes visual inspection, non-destructive testing, and dimensional checks.
Quality inspection and testing are the final checkpoints in the sand casting process, ensuring that the castings meet the desired specifications and are free from defects. Neglecting these critical steps can lead to the shipment of subpar products, resulting in customer dissatisfaction and potential rework.
Comprehensive Quality Control Process
To address the challenge of inadequate quality inspection and testing, it’s crucial to establish a comprehensive quality control process that covers all aspects of casting evaluation:
Visual Inspection: Implement a thorough visual inspection of the castings to detect surface defects, such as cracks, inclusions, and porosity. Trained inspectors should examine each casting for signs of irregularities.
Dimensional Checks: Use precision measuring instruments to verify that the castings meet the specified dimensions and tolerances. This includes measuring critical features and comparing them to the casting drawings.
Non-Destructive Testing (NDT): Depending on the application and casting requirements, employ NDT techniques such as radiographic testing, ultrasonic testing, magnetic particle testing, or dye penetrant testing. These methods can detect internal defects without destroying the casting.
Mechanical Testing: Conduct mechanical tests, such as tensile testing and hardness testing, to assess the mechanical properties of the castings. This is especially important for critical components subjected to high loads.
Metallurgical Analysis: Perform metallurgical analysis to examine the microstructure of the casting, ensuring that it meets material specifications and quality standards.
Documentation and Traceability: Maintain comprehensive records of inspection and testing results, including traceability back to specific production batches.

Quality Control Team
Building a skilled and dedicated quality control team is essential to the success of your quality inspection and testing efforts. Ensure that your team members are well-trained in casting inspection techniques and NDT methods. Regular training and certification programs can keep the team up to date with the latest industry standards and best practices.
Continuous Improvement
A commitment to continuous improvement is vital in addressing quality challenges. Regularly review your quality control processes and results to identify areas for enhancement. Collect and analyze data on defects and their root causes, and use this information to implement corrective and preventive actions.
Customer Feedback and Communication
Maintaining open communication with your customers is essential. Solicit feedback on the quality of your castings and actively address any concerns or issues they may have. Building strong relationships with customers can lead to long-term partnerships and repeat business.
Conclusion
Addressing the challenges in sand casting requires a holistic approach that encompasses sand quality, pattern design, venting and gating, pouring temperature control, mold handling and curing, shrinkage and stress relief, and quality inspection and testing. By meticulously addressing each of these challenges, you can consistently deliver high-quality iron castings that meet or exceed customer expectations.
At Castimoo, we understand the importance of overcoming these challenges to provide top-notch iron casting solutions. Whether you’re in China, the USA, Japan, Europe, or any other part of the world, our commitment to quality and expertise in the sand casting process make us your trusted partner in iron casting. Contact Castimoo today to discover how we can meet your iron casting needs and exceed your expectations.