Introduction
When machining iron castings, it is important to maintain accuracy throughout the process. If the casting is not machined correctly, it can lead to defects and problems in the final product.
In this blog post, we will discuss 10 ways to improve the accuracy of your machining operations when machining iron castings. By following these tips, you can ensure that your castings are machined correctly and meet your high standards for quality.
1. Use High Quality Cutting Tools
When machining iron castings, using the right cutting tools is critical to achieving accuracy. Choose a high-quality cutting tool, such as a carbide or diamond tip, for the best results.
A well-made cutting tool will help maintain the accuracy of your machining project and provide a longer life for the tool itself. In the long run, this will save you time and money.
High quality cutting tools also have a better surface finish. Because of their sharpness, they can provide a smooth surface with fewer rough spots than lower quality tools. This is especially important when machining complex parts or thin walls of castings.
Using high quality cutting tools can also help prevent machine downtime. Poor quality tools can easily break or be damaged, leading to expensive repairs and lost production time. With a reliable cutting tool, you can reduce the chances of this happening.
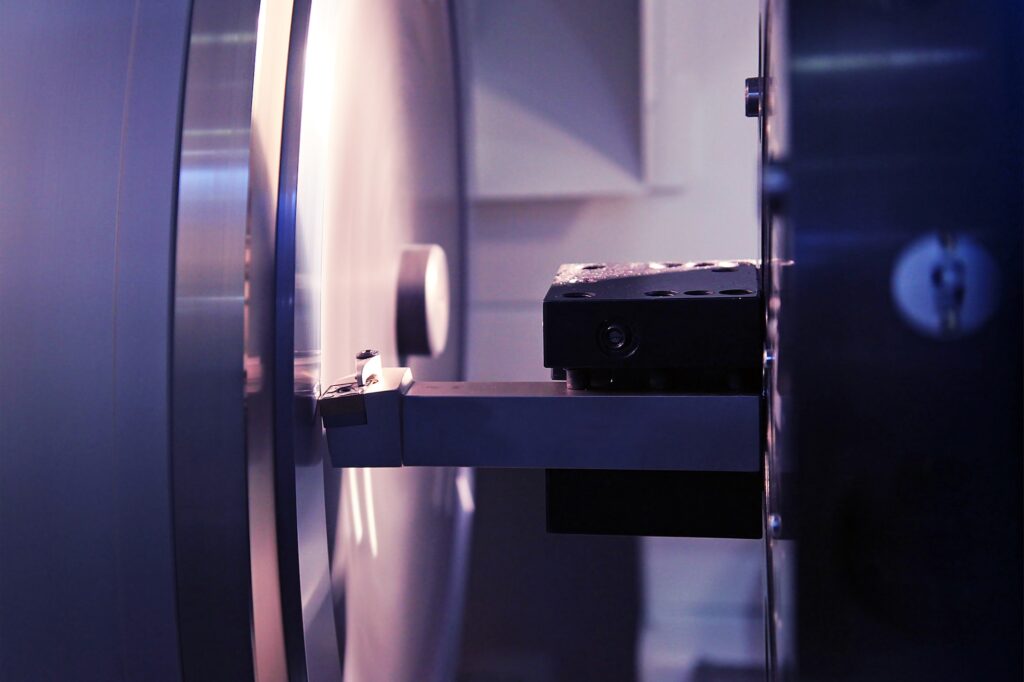
Finally, high-quality cutting tools will also provide better performance when working with iron castings. The best tools are specifically designed to cut quickly, while also reducing the amount of wear and tear. They are designed to get the job done in less time, allowing you to produce higher quality parts with greater precision.
When machining iron castings, investing in quality cutting tools is critical to accuracy and efficiency. With reliable tools, you can be sure that your finished product will meet the highest standards.
2. Check All Equipment Before You Start
Before you start working on your castings, make sure you check all the equipment you will be using. This includes your cutting tools, machines, and any other relevant tools or materials.
Taking the time to thoroughly inspect all of your equipment can go a long way in helping to improve the accuracy of the machining of your castings.
First, make sure you have all the necessary cutting tools and that they are sharp and in good condition. Dull blades or worn cutting tools can cause problems when machining, so make sure they are all in top condition.
Next, check the machine itself to make sure it is properly adjusted and working properly. Make sure it’s all set up correctly and that everything is running smoothly. This will help ensure that you get accurate and precise cuts every time.
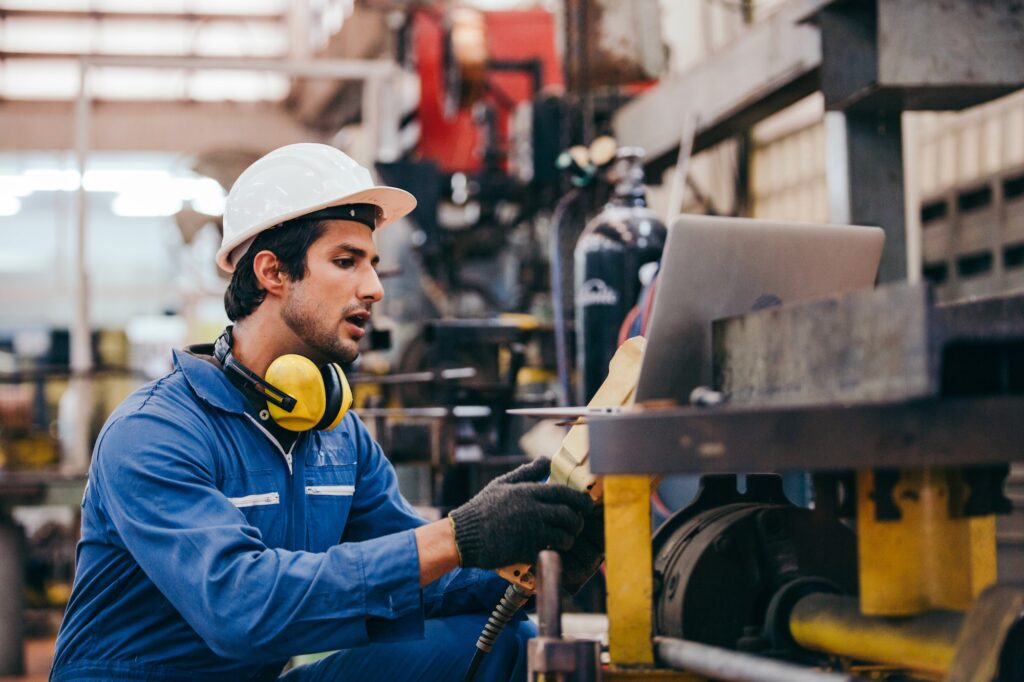
Finally, check any other materials or tools that you may need. Make sure everything is in order and that there are no problems.
Taking the time to check all of your equipment before you start machining will help ensure that you have better accuracy in your castings, resulting in a higher quality finished product. In addition, this will save you time in the long run by reducing the need for rework.
3. Choosing The Right Material for Your Castings
The type of material used to make a casting can have an impact on its accuracy after machining. For many machining projects, iron castings are a durable and cost-effective option – but they must be made from the right material to ensure the best results.
When selecting the right material for iron castings, mechanical properties such as ductility, strength, hardness and corrosion resistance must be considered. The material should also have a low coefficient of thermal expansion and good machinability.
In general, the most commonly used iron castings are made of gray iron or ductile iron, which is stronger and more resistant to corrosion than other types of iron. Gray iron contains graphite flakes that help absorb vibrations and give it strength. Ductile iron has relatively good ductility and strength.
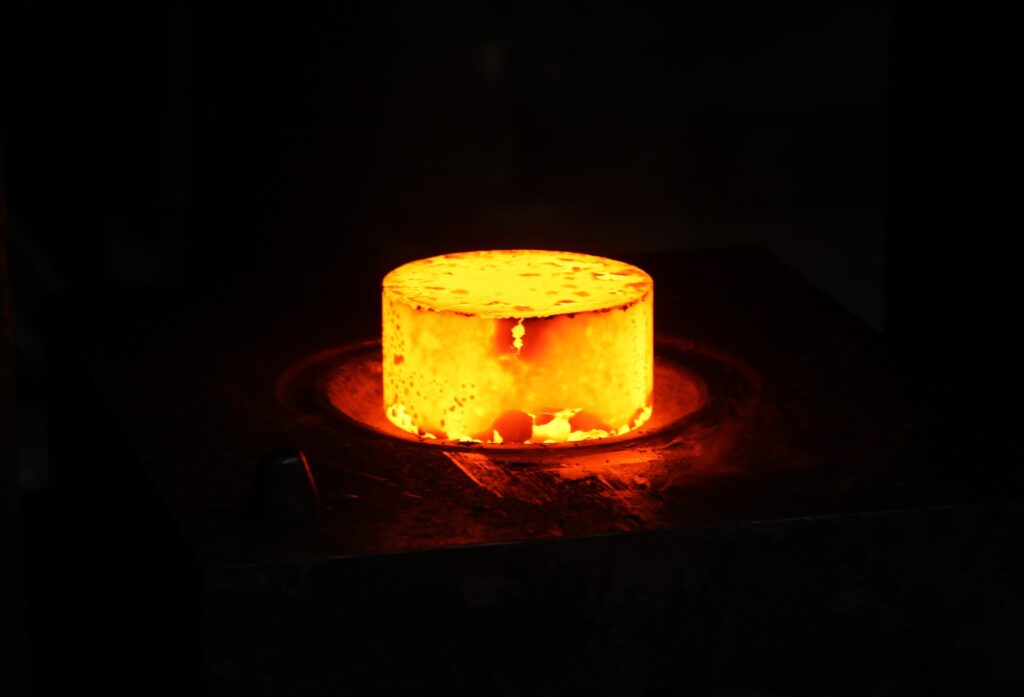
Once the right material has been selected, careful consideration of other factors, such as mold design, pouring temperature, cooling rate and casting surface finish, can help ensure that the machined part has the best possible accuracy. For example, ensuring that there are no sharp corners or edges on the casting can reduce wear on the casting.
Finally, it is important to remember that the choice of material will have a direct impact on the cost and performance of the machined part. Choosing the right material for the casting can help you achieve the best possible accuracy.
4. Plan Your Machining Operation Ahead of Time
Good planning is the key to a successful machining job. Plan out your cutting operation step by step before you start so you know exactly what you need to do and how much material will be removed each time.
Planning each step ahead of time will help ensure that the finished part is as accurate as possible. Take the time to study and measure your castings to determine which tools will be needed for each operation, how far apart they should be, and what type of pattern you will use.
Once you have determined the best cutting path, consider how long each cut will take and what type of cutting fluid or coolant you will need. Setting up your machine with the correct parameters can help ensure that your machining operation runs smoothly and accurately.
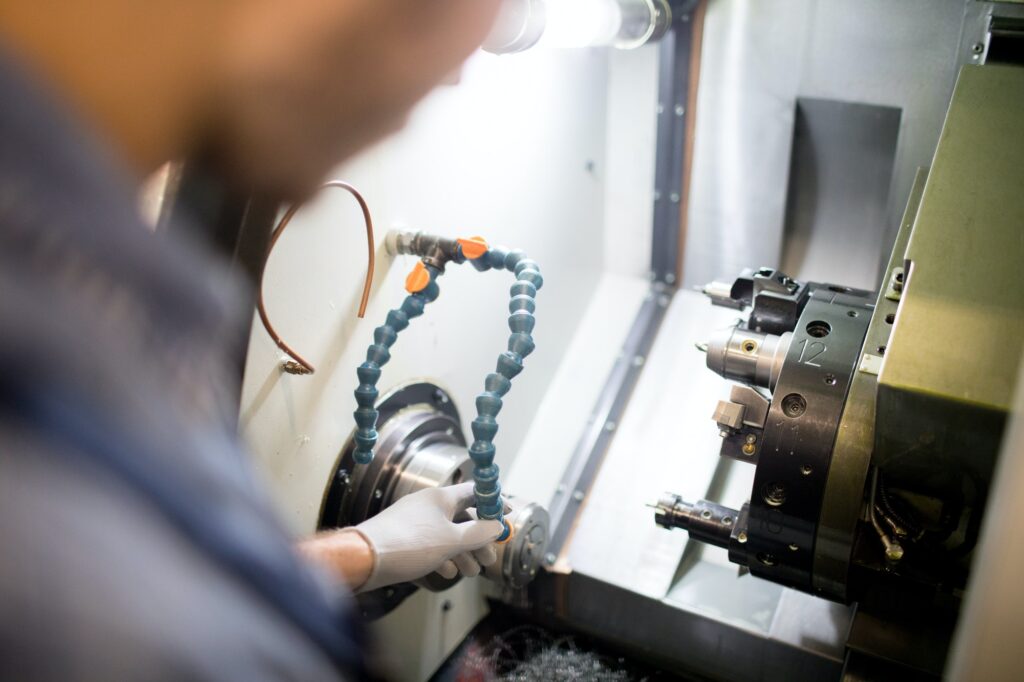
Make sure to check all dimensions before you start machining and throughout the machining process as well. This way, if there are any discrepancies, they can be corrected quickly.
Finally, take the time to calculate the feed rate and depth of cut for each operation. This will help you determine how much material needs to be removed and ensure you don’t overcut or damage your castings.
By planning each machining operation well in advance, you can ensure that the finished product is as accurate and precise as possible. With a little preparation, your castings will turn out just right every time.
5. Maintain A Steady Speed While Machining
The machining process for iron castings is greatly influenced by the speed at which the workpiece is cut. It is important to maintain a consistent speed, as changing speeds can lead to inconsistent finishes and even cause additional problems with the casting itself. If you are machining large parts, it is especially important to maintain the speed of the machine.
The speed of the machine should remain constant throughout the machining process. This helps ensure that all cutting edges are at a uniform angle and also prevents any potential damage or defects caused by vibration. For larger parts, a slow, steady feed rate is recommended, as this will help reduce the possibility of burrs.
By maintaining a steady speed during machining, it is possible to achieve a consistent finish, improve accuracy and extend tool life. In addition, it is important to note that maintaining a steady speed can also help reduce the risk of accidents and injuries.
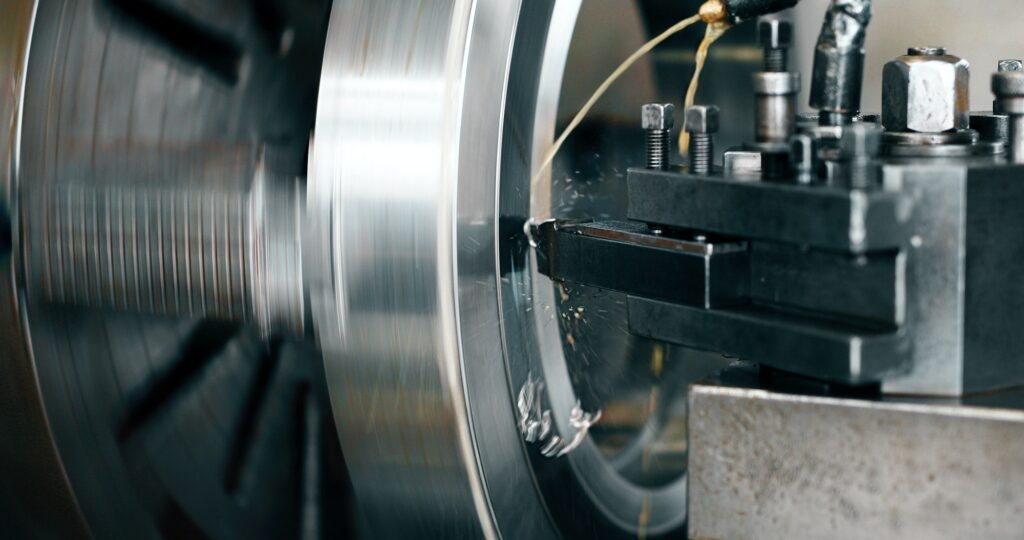
6. Check Your Tools Regularly
Dull and damaged tools are more likely to cause inaccuracies during machining, so be sure to check the condition of your cutting tools frequently throughout the process. Check them before, during and after machining to make sure they are still sharp and intact. If you find any wear or damage, replace your tools immediately.
It’s also important to check the overall accuracy of your tools. Check them regularly for signs of wear and any other indicators that may affect their cutting performance. Make sure that all dimensions are accurate and that there are no defects or flaws that have resulted over time. If the tools are not up to par, your machining accuracy will suffer, so check them often to ensure optimal performance.
Finally, use high-quality tools that meet the specifications of the work you are doing. This can make a huge difference in the overall accuracy and quality of your machining process. Investing in great tools, along with proper setup and maintenance, can have a major impact on the accuracy of your parts.
7. Properly Lubricate Your Machining Equipment
Lubricating your machining equipment will help keep it running smoothly and reduce friction, which can lead to inaccuracies in the final product. By reducing friction, the cutting tools used to machine iron castings will stay sharper for longer, resulting in more accurate and consistent parts.
The type of lubricant used is also important. It should be specifically designed for the type of machining equipment and the material being machined. For example, metalworking oils will be best suited for machining iron castings, while water-based lubricants are best suited for non-ferrous metals.
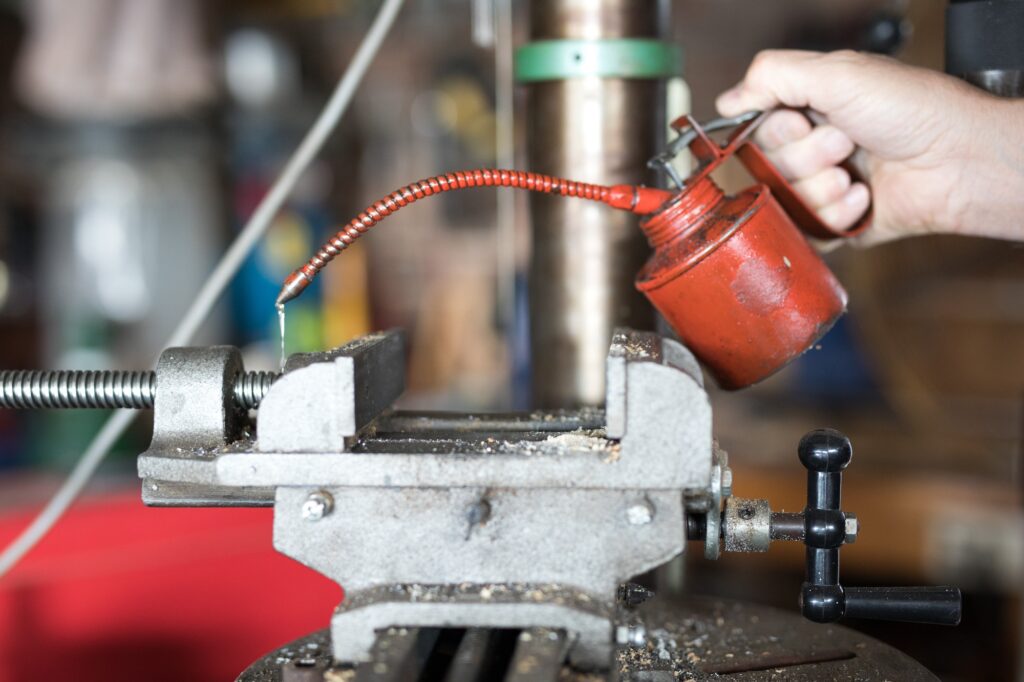
In addition to selecting the correct type of lubricant, it is important to use the correct amount of lubrication. Excessive amounts can cause oil to build up on the surface of the machined part, which can lead to inaccurate readings. On the other hand, not having enough lubrication can cause friction and wear, which in turn can lead to inaccurate end products.
Overall, proper lubrication is critical to ensure accurate machining of iron castings. By choosing the correct type of lubricant and using it correctly, you can greatly reduce friction and extend service life.
8. Maintain A Constant Depth of Cut
If you change your depth of cut too often, it can lead to inconsistencies in the finished product. To maintain accurate iron casting machining, you should maintain a constant depth of cut.
To maintain the same depth of cut, you can use either a fixed tool or an adjustable tool. Fixed tools have a pre-set depth of cut that remains constant during operation. Adjustable cutting tools can be adjusted to different depths of cut, allowing the machinist to make small adjustments as needed.
It is also important to remember that the characteristics of the material being machined and the tool itself will affect the ability to maintain a constant depth of cut. Harder materials require slower speeds and higher pressures. Softer materials require higher speeds and lower pressures. The tool itself must be sharpened or replaced as needed to ensure a consistent depth of cut every time it is processed.
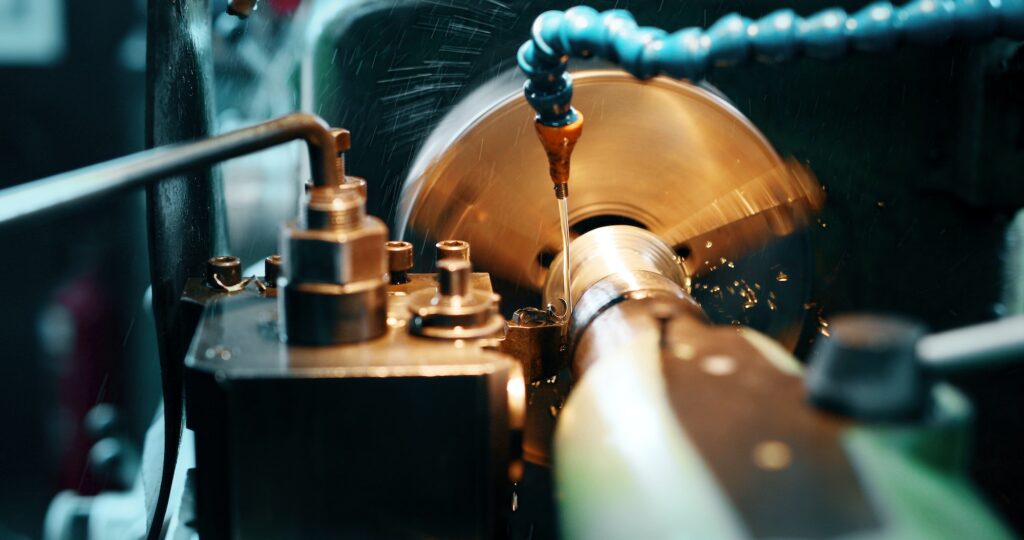
By maintaining the same depth of cut throughout the machining process, you can help ensure the accuracy of your iron castings. This will provide you with better quality parts that will meet your specifications every time.
9. Check Your Workpiece Regularly
This is especially important when machining iron castings. This is because the various chemical and physical properties make the machining process unpredictable.
Regular inspections help you to identify any potential problems with your workpieces before they become serious issues that affect the quality of the finished product. If needed, adjustments can be made to the machining process, such as changing cutting tools or altering speeds and feed rates.
By inspecting your workpiece regularly, you will be able to detect any problems with tool wear or chip accumulation that may be affecting accuracy. This can help you avoid costly rework and mistakes down the line.
When machining iron castings, regular inspection of your workpiece is essential to ensure the accuracy and quality of your finished product.
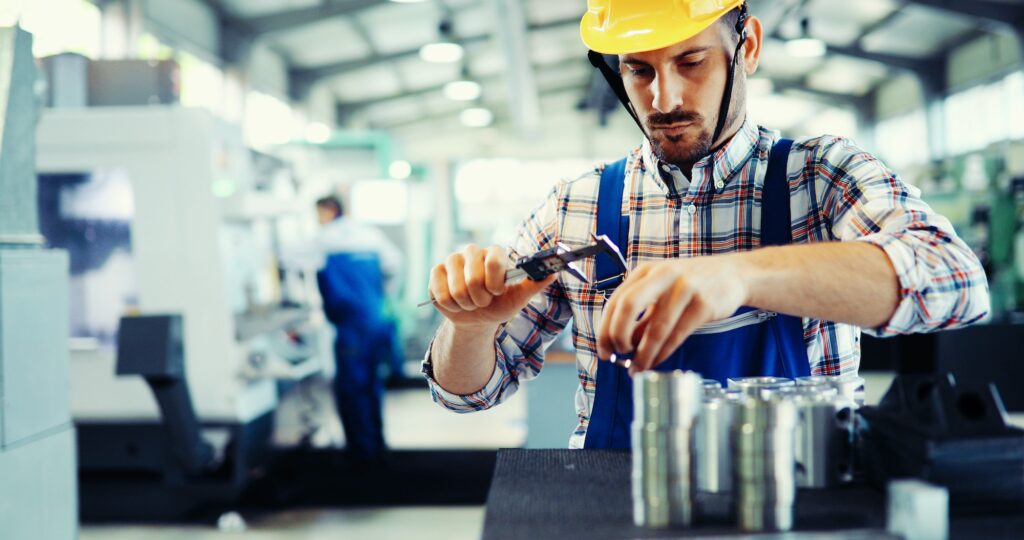
10. Inspect The Finished Product Thoroughly
Once your machining operation is complete, be sure to check the finished casting for accuracy. A thorough inspection can help reduce the risk of machining errors and improve accuracy. This will help you to identify any areas that may need further adjustment or correction before sending it to the next step in production.
It is important that you inspect the finished product from multiple angles and note any signs of porosity, cracks or other defects that may indicate the need for further adjustment or correction. In addition, check for any surface irregularities, such as burrs. And measure the dimensions of the finished product to make sure they are within specifications.
Conclusion
By following these tips, you can be sure that your iron castings will be machined accurately and meet your high standards for quality. With the right tools, materials and plan, you can be sure that your machining operation will be efficient and accurate every time.
We are Castimoo, a supplier dedicated to the production and machining of iron castings. Our products are certified by ISO 9001 and are also well accepted by our customers at home and abroad. If you have plans to purchase iron castings, please feel free to contact us. We are always here for you.