Introduction
Have you ever had a crisis of confidence? Have you ever met a trustworthy company only to lose your confidence in them for some reason?
In this Internet age, trust is very important. Both large and small businesses can be at risk of consumer boycott actions due to some mistakes.
So, is Castimoo a trustworthy supplier?
When you try to search this question, congratulations, you approve of Castimoo’s services and ability to provide you with value. There is just a little bit of concern for you, which we totally understand.
Especially in this information-explosive age, which is filled with all kinds of rumors. However, after you read this article, I’m sure you’ll have a better understanding of Castimoo.
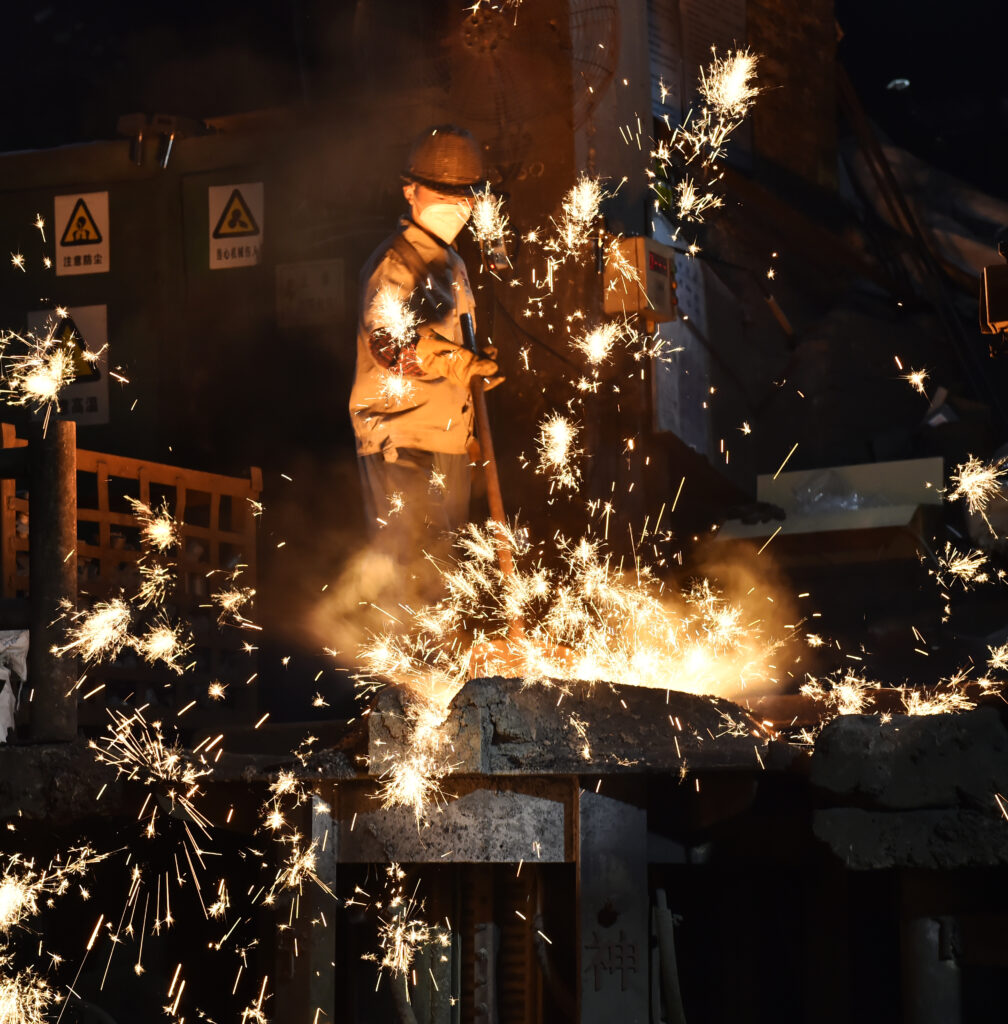
1. Professional
Castimoo is a manufacturer specializing in iron castings and has been in this field for nearly 30 years since it was founded in 1993.
The founding team is led by a university professor specializing in casting, providing professional design and production services for domestic and overseas customers.
With a standardized production process and perfect product testing equipment, the company is able to undertake a variety of ductile iron, alloy cast iron and high-grade gray cast iron according to customers’ needs.
Our company has obtained ISO9001 quality management system certification and our products have been exported to Europe, America, Japan and Southeast Asia for many years.
We have provided professional and effective solutions for over 300 domestic and international customers and have been highly evaluated by them.
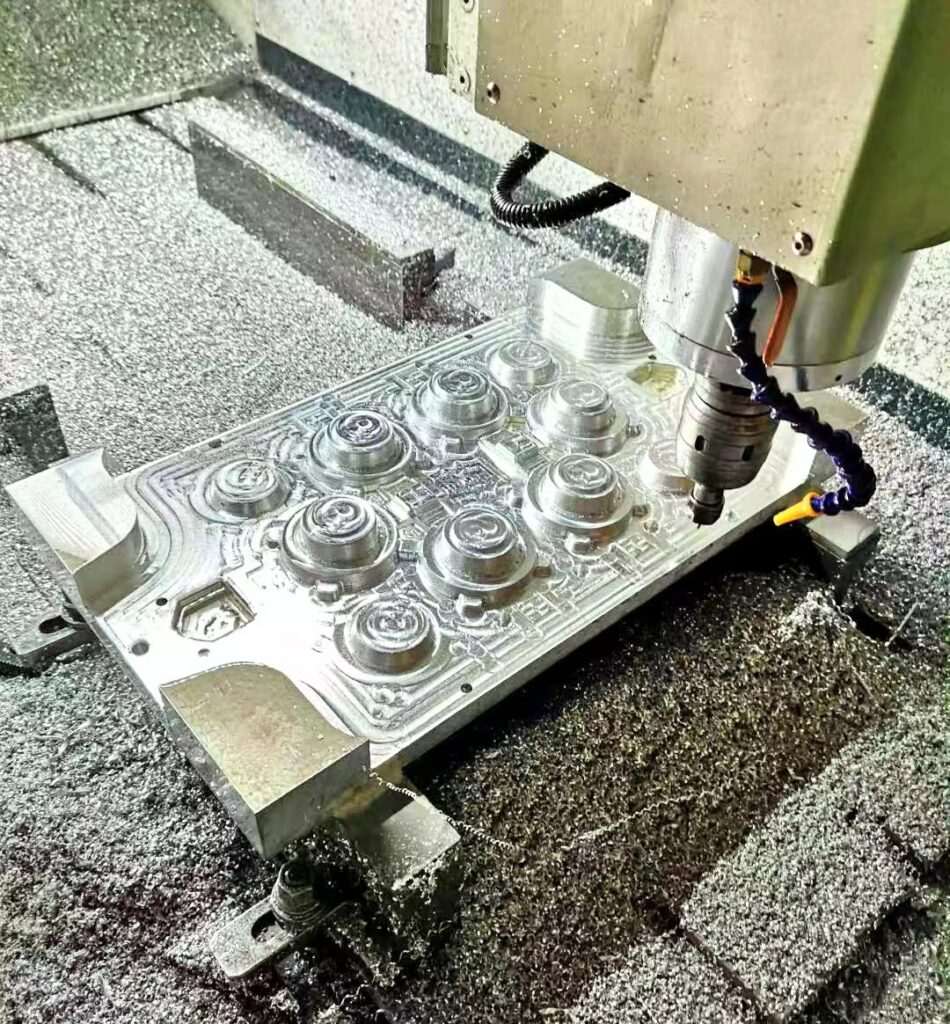
Design team
With 3D drawing and guidance from university professors in casting, is able to design a reasonable pouring system for ductile iron products, so customers don’t have to worry about shrinkage anymore.
Mold production
From design drawing to making sample in 10 days at the shortest, ensure you get the sample for evaluation in the shortest time and develop local market quickly.
Casting production
Two automatic molding lines, three sets of medium frequency electric furnace, more than 50 professional workers in two shifts for you to ensure that you can get the best service experience.
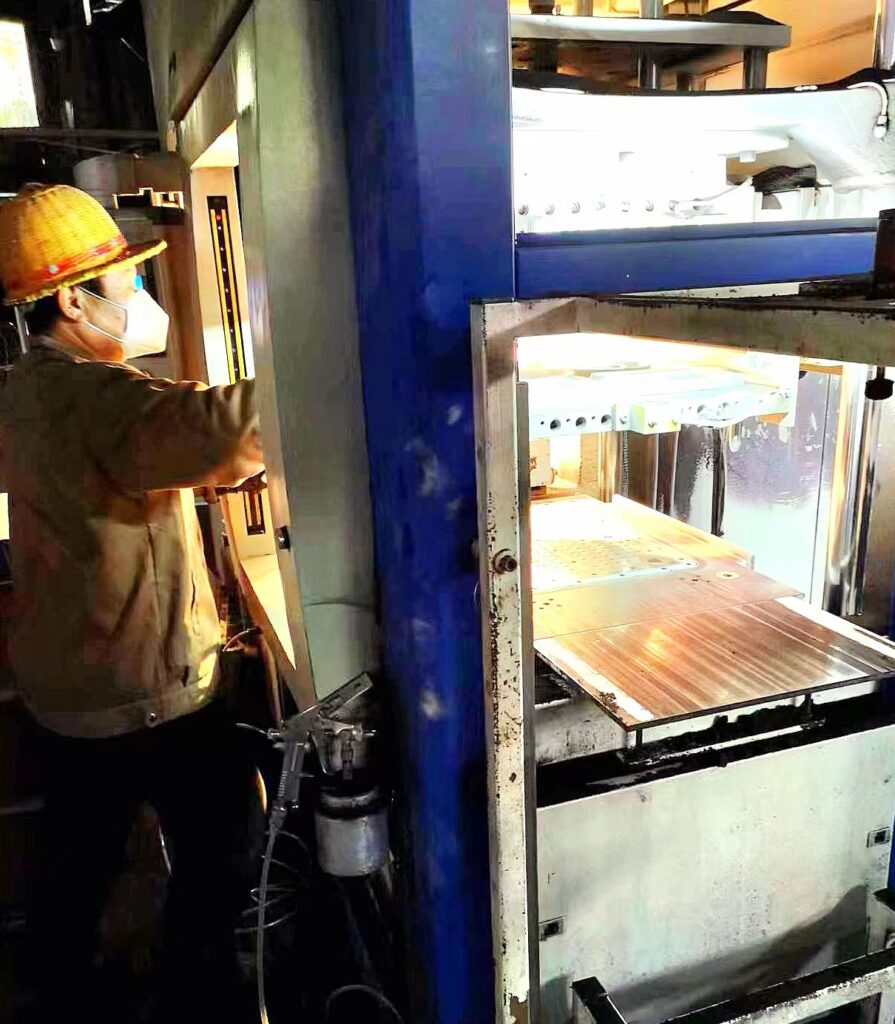
Machining
With a professional machining team with over 20 years of experience. With more than 10 sets of NC and CNC machines to ensure on-time delivery. Quality inspection management system, strictly control the processing accuracy.
Quality inspection
We use metallograph to observe the graphite form; hardness tester to measure the hardness of the castings; spectrometer to detect the composition of the castings, the composition of each furnace must be recorded; quality inspection management system to strictly control the accuracy of machining.
Packing
Before packing, we will do a good job of anti-rust treatment, there are two anti-rust methods of water-based and oil-based for you to choose. The wooden box for export is also in accordance with the export regulations.
Transportation
we have cooperated with local logistics and freight companies for many years to ensure that you will receive the goods in the shortest time. And we will provide the best service and the most suitable price.
Our professionalism is the basis of your trust.
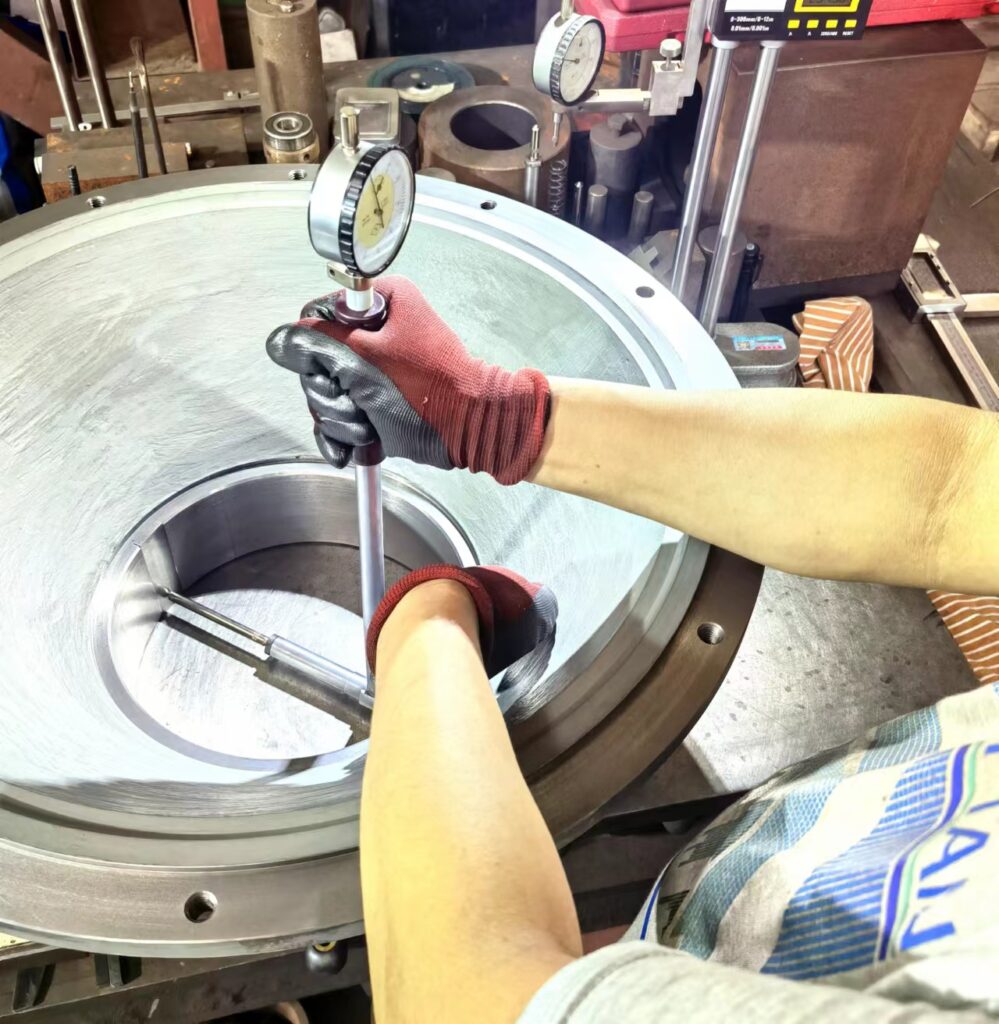
2. Reliable
When your product encounters problems and it is difficult to solve, Castimoo is very willing to provide you with help in any way we can.
Some customers often encounter difficult problems when they buy iron castings produced by other foundries. Here are two cases in which we have helped our customers to solve their problems after many trials.
Case 1
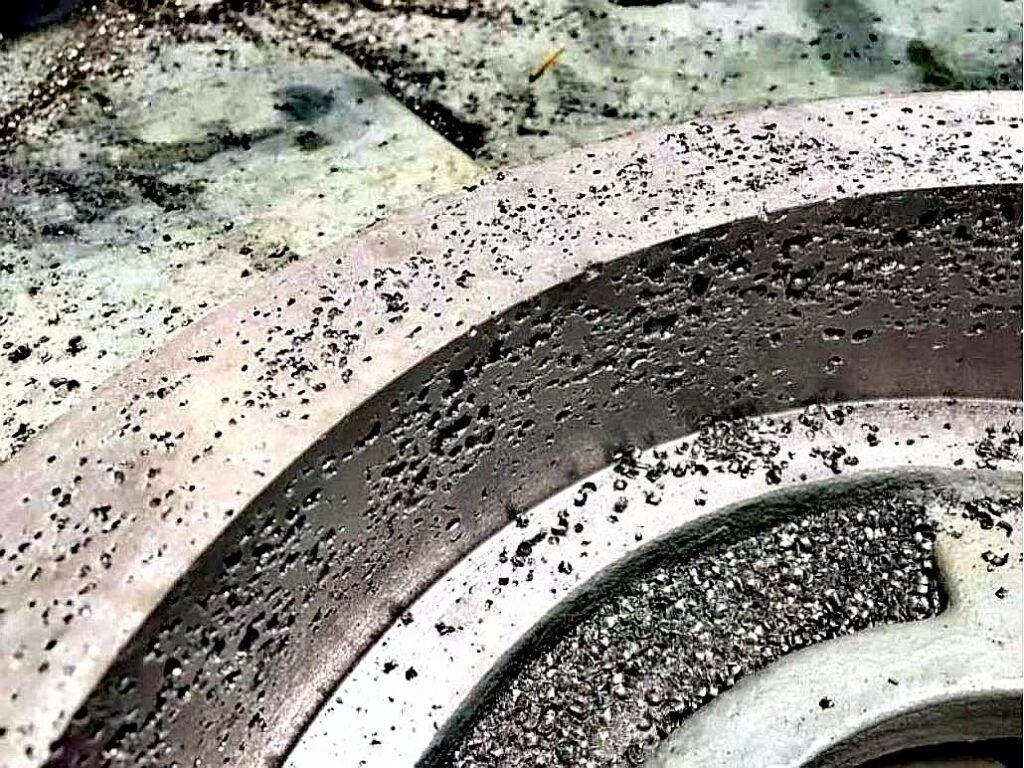
Defects as shown
200 grade gray iron, diameter 1.1m, weight 500kg, wall thickness 40mm at the center, the casting has a large number of internal blow holes.
Analysis of its causes
1. High resin water content; 2. High composition of old sand; 3. Too much resin added; 4. Low pouring temperature; 5. Many impurities in raw materials.
Experimental research
1. Replace high quality resin; 2. Increase the addition of new sand; 3. Reduce the addition of resin; 4. Increase the pouring temperature after the furnace temperature; 5. Choose clean and oxidation-free scrap steel.
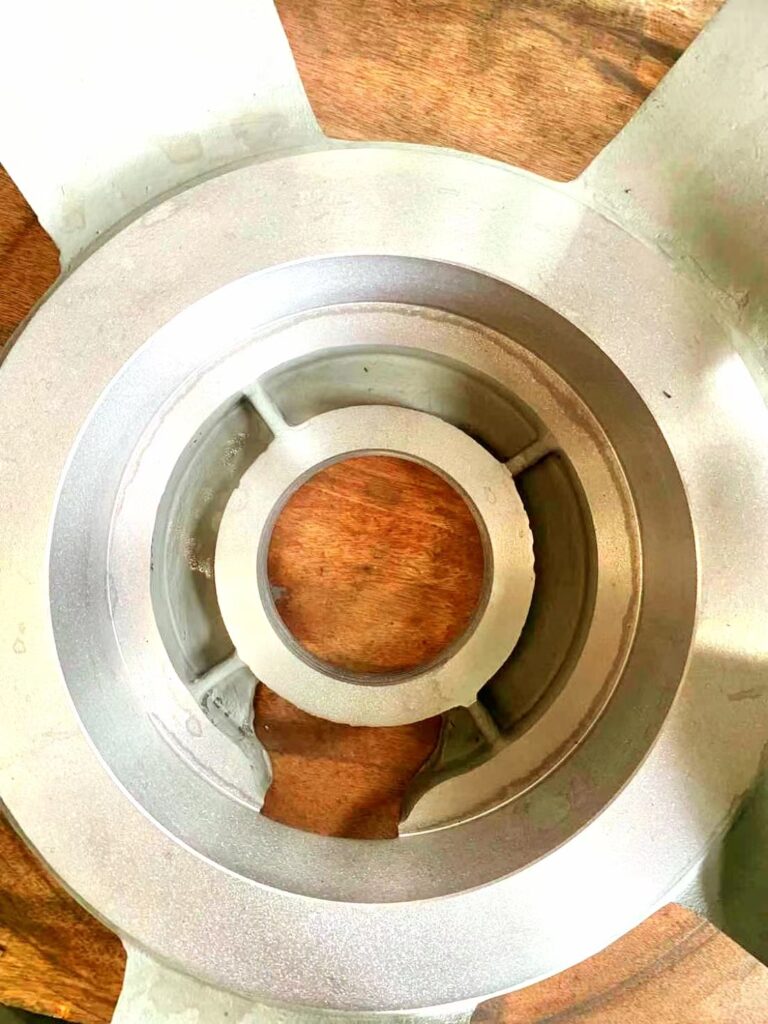
Overcome the problem
Through tests, it was found that none of the above countermeasures for the suspected cause was effective.
After checking a lot of information, including the research of Japanese scholars, it is easy to produce porosity when the N content in iron is ≥140PPM.
Finally, it was decided to change the calcination process from a carbon additive with N content of 5000PPM to a carbon additive of 1000PPM, and the porosity of the casting disappeared completely.
Case 2
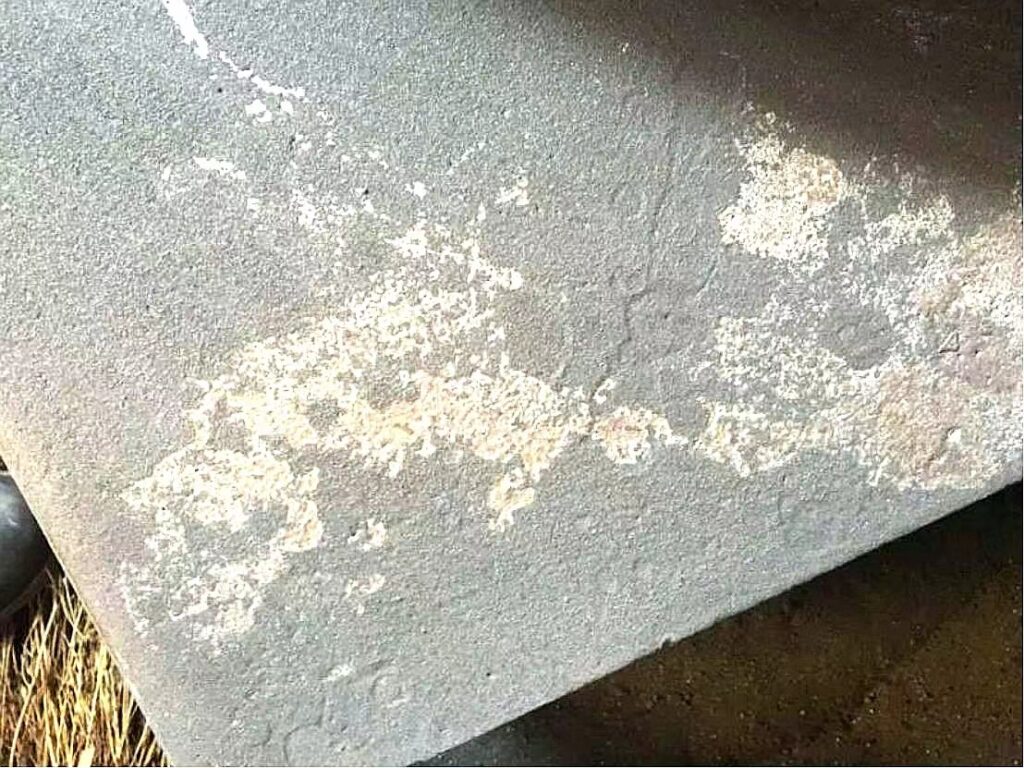
Defects as shown
200 grade gray iron, weight 450kg, main wall thickness 40mm, resin sand molding process, the surface of the casting appears mottled.
Analysis of its causes
1. resin oil and curing agent mix unevenly; 2. impurities in the iron water; 3. iron ladle wall is not fire-resistant, molten iron into the cavity; 4. covering agent quality is not good, molten iron into; 5. filter quality is not good, no slag blocking effect.
Experimental research
1. use small sand mixer to mix the new sand evenly, then modeling, but the mottling did not disappear; 2. use ceramic filter; 3. filler of the iron ladle with high temperature resistant material; 4. use good quality covering agent.
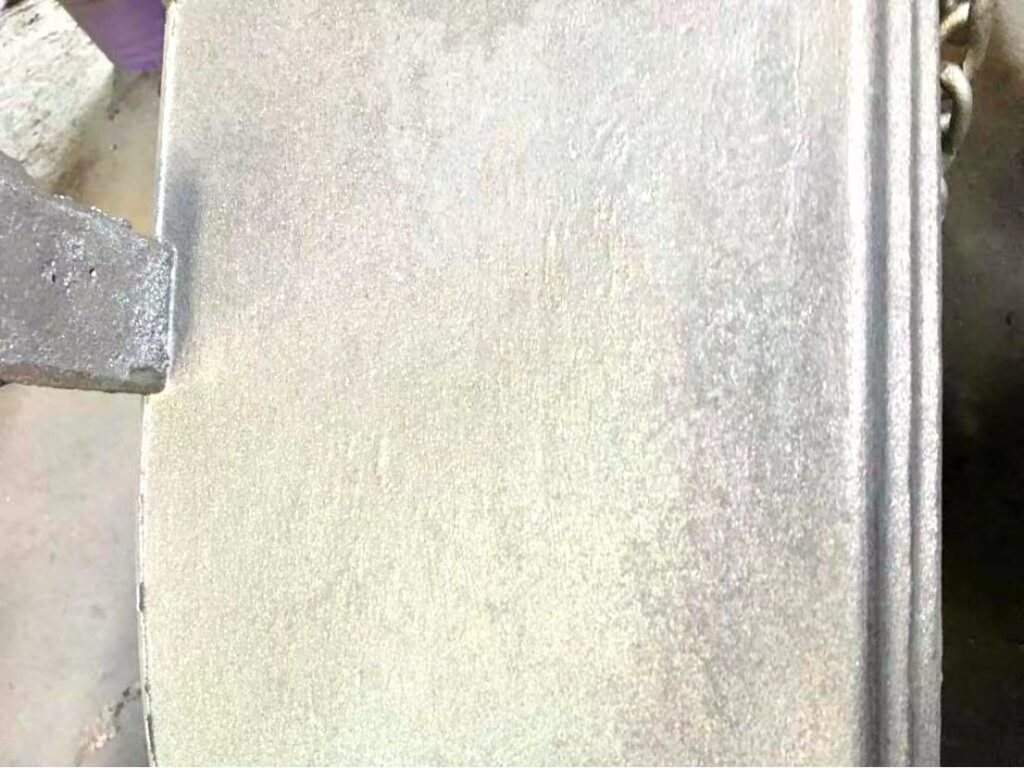
Overcome the problem
The above measures did not improve the effect. Finally, by replacing the paint with a higher refractive index, the spots disappeared completely.
The quality of the casting surface is directly related to the refractoriness, spreadability and wettability of the coating.
Castimoo would be happy to work with a quality foreign customer like you to help you gain more revenue and profit.
3. Approachable
Castimoo has built strong friendships with many domestic and foreign customers. We cooperate at work, but we are also friends in private.
Our Japanese customers also send their staffs to our foundry regularly every year to learn and exchange casting experience, and we share it with our guests without reservation.
If you have time, you are welcome to visit our foundry at any time.
Not only in casting, but also in other industry fields, such as stamping sheet metal, hardware and auto parts, etc. We also have resources and contacts to share with you.
Even if you are not our customer, we will try our best to help you as long as you need.

Tell two heartwarming stories.
Story 1
In the fall of 2018, our city was hit by the biggest typhoon ever and the factory was damaged.
After learning the news, our foreign guests sent us a condolences the next day.
They said they wanted to make a small contribution to our foundry.
Story 2
At the beginning of 2020, when the epidemic first broke out in China, the price of masks was soaring, and it was even hard to find a mask.
Our foreign customer helped us to get through the difficult time by providing us with two large boxes of masks by air at the first time.
We are very grateful to the foreign customers who have helped us, and will keep them in our hearts.
We also continue to work hard to provide better products and services to repay your trust.
4. Unselfish
I would like to tell you one of the proudest things about Castimoo.
28 years ago, we made iron castings from cast iron scraps, when we were the first in China. This idea really changed the casting industry by reducing the cost of raw materials by $80/ton.
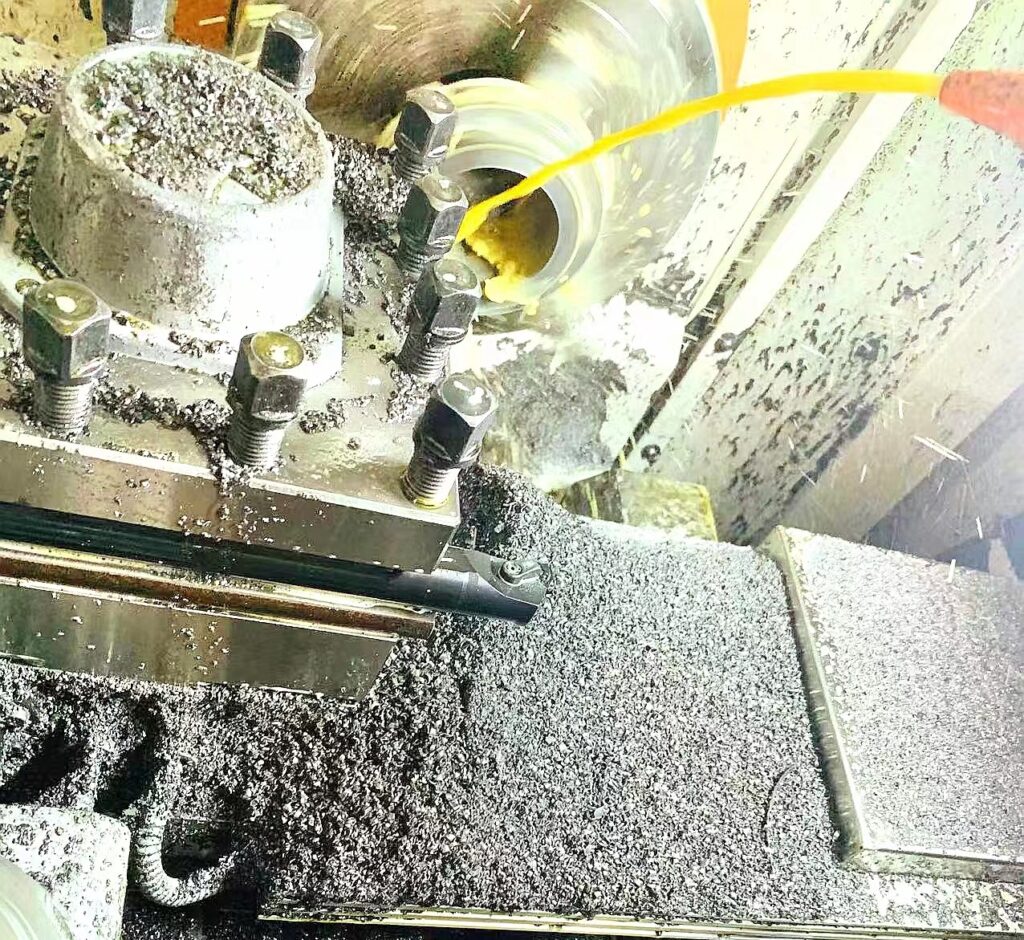
This idea was unprecedented at the time, so we immediately started putting it into practice. Sure enough, all the finished products tested were too hard and failed.
Then we tried to figure out why and test the ingredients.
The cost of the test was $120, which was a lot of money 28 years ago. But the determination to fix the problem and make things right made us unstoppable.
Through lab testing, we found that the graphite and silicon in the cast iron flakes had evaporated during processing, handling and combustion, causing the cast iron product to be too hard.
After finding the cause of the problem, we began experimenting with formulations to increase the carbon and silicon content.
Tested again, the composition was the same as ideal and the hardness was adjusted just right.
And for mass production, we spared no expense and bought an original German carbon and silicon tester. USD5600! My goodness!
From then on, high technology and quality products have been our strengths.
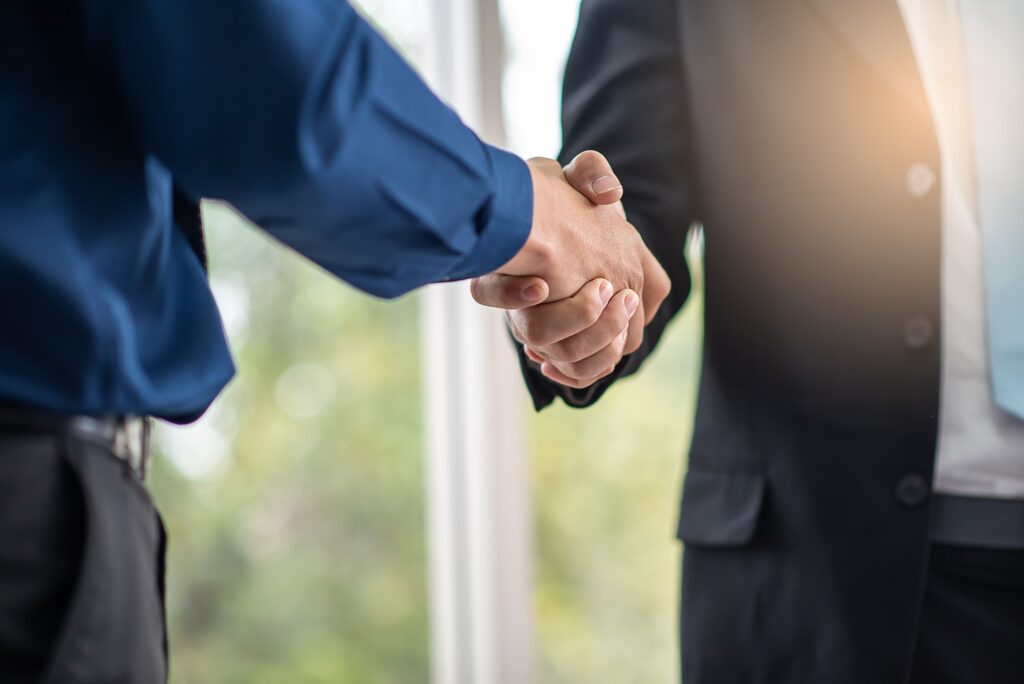
For R&D, we adopt the attitude that we must try when we have the chance. In fact, the cost of trial and error is not high, the cost of missing out is high.
In every business cooperation, our first consideration is the needs and interests of our customers. Only when the other party benefits, there will be a long-lasting cooperation.
Therefore, for cost reduction, we are serious. For each customer’s needs, we will provide the most sincere service.
Conclusion
McKinsey & Company has a trust formula: Trust = (Professionalism * Reliability * Approachability) / Selfishness
This formula can be perfectly applied to supplier evaluation systems.
So, is Castimoo a trustworthy iron casting supplier? I think the answer is already in your mind when you read this far.
Of course, as a supplier of iron castings, we still have a lot to improve in terms of production management. We will do our best every day to provide you with the best products and sincere service.
If you have the need to purchase iron castings, welcome to contact us.
3 Responses