Iron castings are a valuable and versatile resource with many amazing properties. They can be used for a wide variety of applications, from machine parts to architectural details.
In this blog post, we will discuss the various properties of iron castings and how they can benefit your business. Stay tuned!
What Is Iron Casting?
When it comes to ferrous metals, iron is the most widely used element in the world. In its pure form, iron is relatively soft and does not have many applications.
However, when iron is combined with other elements, it can be quite strong and durable. This makes it ideal for a wide range of applications, including iron castings.
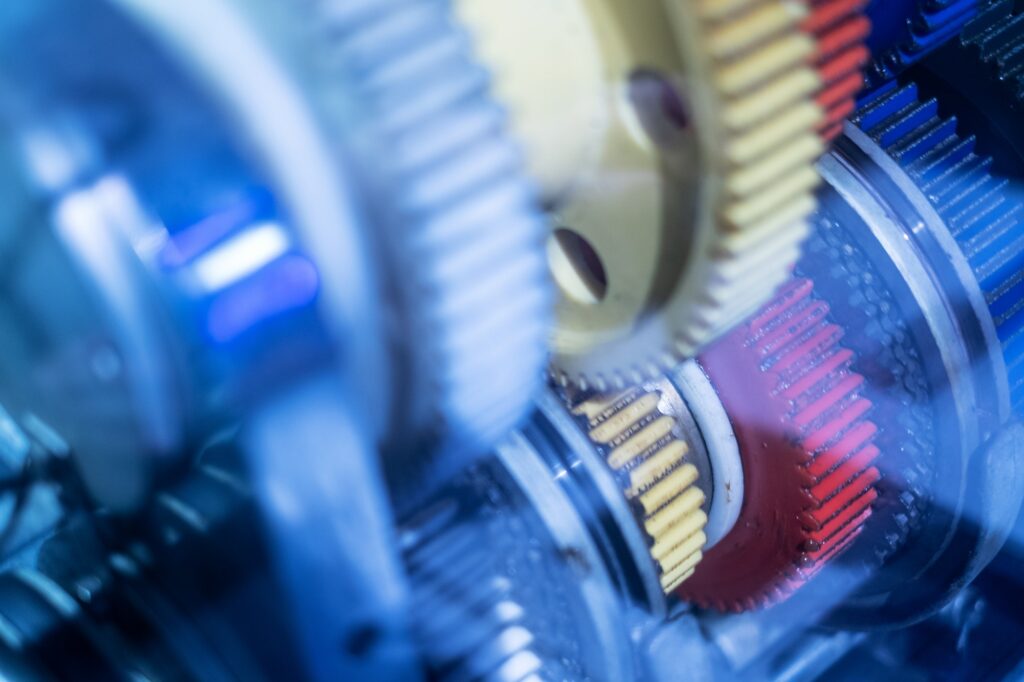
Iron casting is one of the oldest metals and has been used in various forms for over 3000 years. Cast iron is mainly composed of carbon and silicon. The carbon content in cast iron can be as high as 4%.
Iron castings are made by pouring molten iron into a mold. The iron is then allowed to cool and harden into the desired shape.
Iron castings are used in a variety of industries, including automotive, construction, and mining. They are also used in a variety of consumer products, such as cookware and door hardware.
The Applications for Iron Castings
Construction
Iron castings are commonly used in construction. They are often used to create structural components such as columns, beams, and trusses.
Iron castings can also be used to create decorative elements such as wrought iron fences and gates.
Engineering
Iron castings are used in a variety of engineering applications. They are often used to create engine blocks, cylinder heads, and gearboxes.
Iron castings can also be used to create structural components for bridges and buildings.
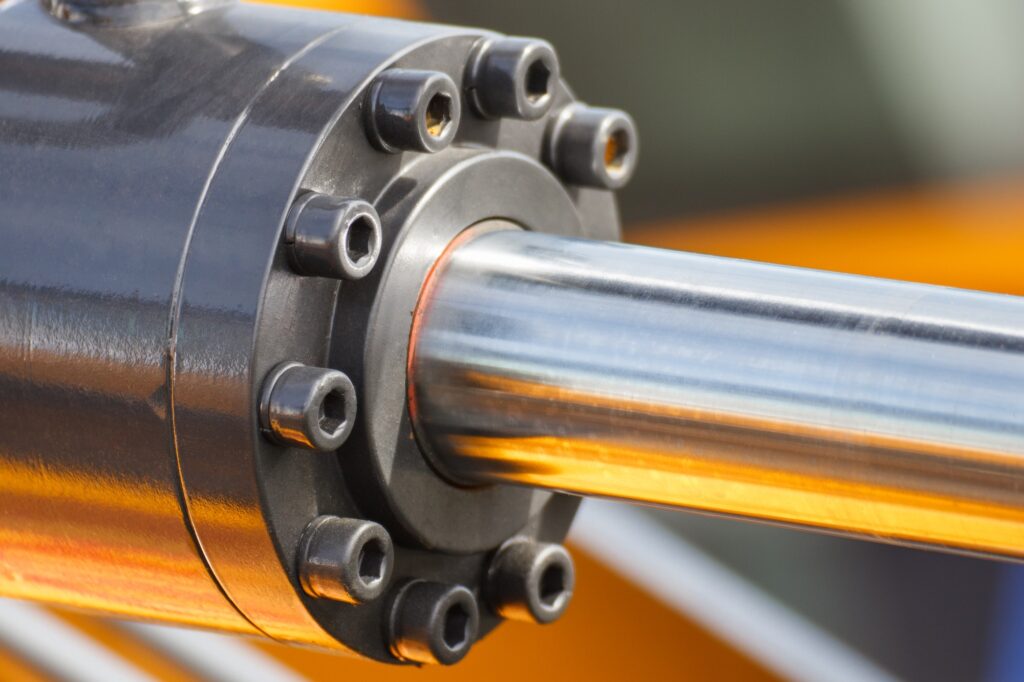
Manufacturing
Iron castings are used extensively in manufacturing. They are often used to create machine parts such as gears, pulleys, and shafts.
Iron castings can also be used to create molds for plastic injection molding and metal die casting.
Mining
Iron castings are commonly used in mining applications. They are often used to create wear-resistant parts for crushing and grinding equipment.
Iron castings can also be used in DRAG line buckets and shovels.
Transportation
Iron castings are essential components of many transportation applications. They are commonly used to create engine blocks and cylinder heads for trucks and buses.
Iron castings can also be used in the construction of railway tracks and railway cars.
The Different Properties of Iron Castings
Iron castings are one of the most versatile materials used in manufacturing. They are strong, durable, and resistant to many different types of wear and tear.
They can also be made in a variety of shapes and sizes to suit the needs of any project. We’ll take a closer look at some of the most common properties of iron castings and how they can benefit your next manufacturing project.
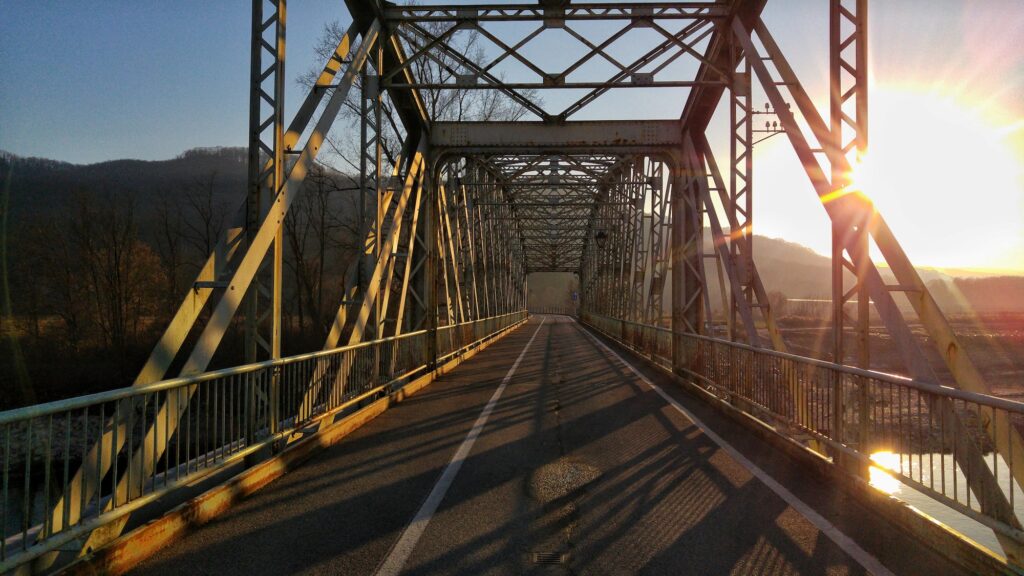
Strength and Durability
One of the most important properties of iron castings is their strength.
They are much stronger than other types of casting materials, such as aluminum or bronze. This makes them ideal for projects that require a high degree of strength and durability.
Additionally, iron castings are resistant to many different types of wear and tear, including corrosion, abrasion, and impact damage. This makes them an excellent choice for applications where other materials would not be able to withstand the same level of wear and tear.
Tensile Strength
Tensile strength is a measure of how much force a material can withstand before breaking. This is an important property for iron castings because it determines how strong the final product will be.
Yield Strength
Yield strength is a measure of how much force a material can withstand before it begins to deform permanently. It determines how tough the final product will be.
Hardness
Hardness is a measure of how resistant a material is to indentation and scratching. It determines how durable the final product will be.

Versatility
Iron castings are also very versatile. They can be made in a wide variety of shapes and sizes to suit the needs of any project.
Additionally, they can be designed to meet a variety of mechanical and physical properties. This means that they can be used in a wide range of applications, from small parts to large structures.
Cost-Effectiveness
Another advantage of iron castings is their cost-effectiveness. They are typically less expensive than other materials, such as steel or titanium. This makes them an excellent choice for projects where cost is a major concern.
Additionally, they are often readily available from supplier inventory, which can help save time and money on your next project.
No matter what your needs may be, iron castings are an excellent choice for your next manufacturing project. Thanks to their strength, tensile strength, yield strength, durability, hardness, versatility, and cost-effectiveness, they offer a number of advantages over other materials.
If you’re looking for a material that can provide all of these benefits for your next project, look no further than iron castings!
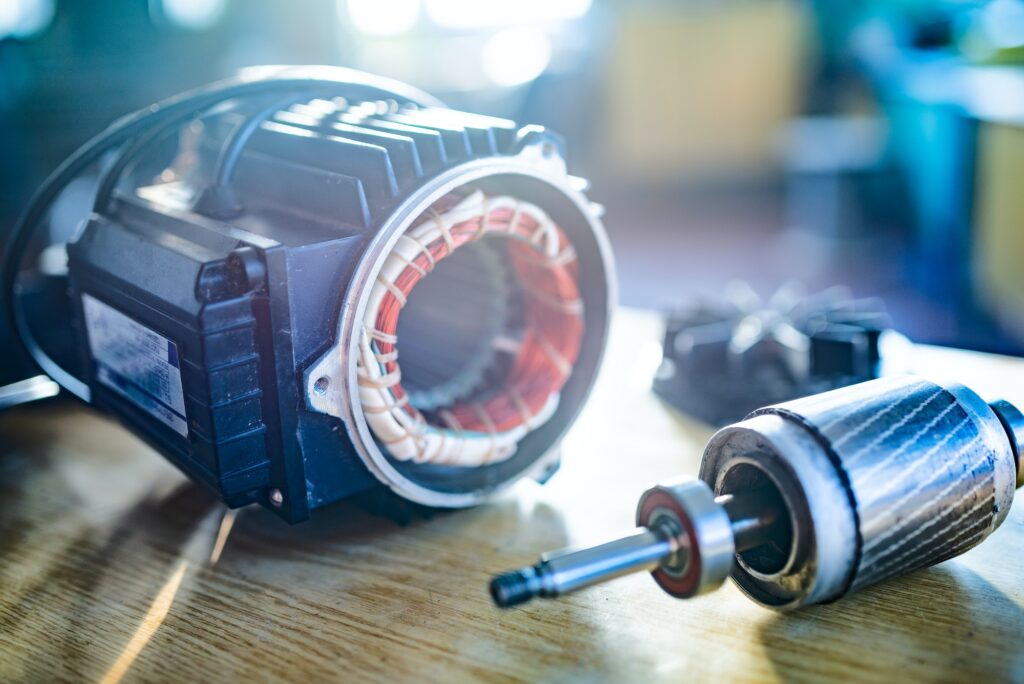
The Drawbacks of Iron Castings
There are some drawbacks to using iron castings as well.
First, they are very heavy. This can make them difficult to transport and can add to the overall weight of a product.
Second, iron castings can be quite brittle. This means that they may break if they are subject to too much force or if they are dropped from a height.
Third, iron castings can rust if they are exposed to water or other chemicals over time. This can cause them to become less durable and less aesthetically pleasing over time.
Fourth, depending on the application, cast irons may require machining prior to use which could require additional cost .
The Process of Iron Castings
Iron castings are an essential component in a variety of industries. The process of creating iron castings is intricate and involves a high degree of precision.
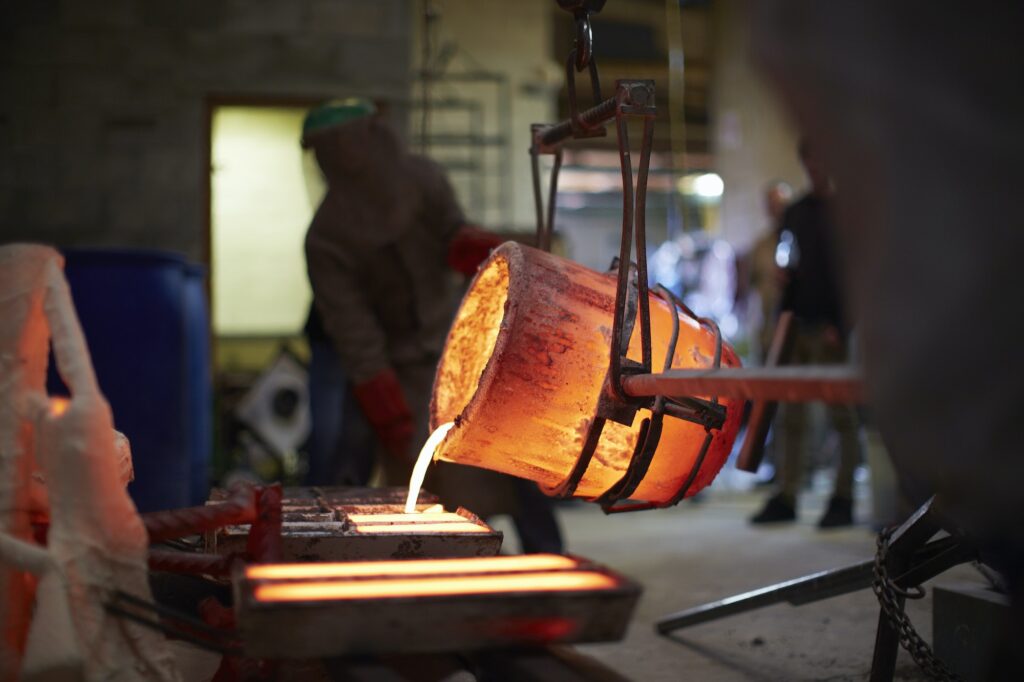
The first step in the process of iron castings is creating the mold. The mold is created by pouring molten iron into a molding sand mixture. Once the iron has cooled, the sand is removed and the molding process can begin.
The furnace needs to be able to reach super high temperatures so that the iron will be melted down. It’s important to monitor the temperature carefully so that the iron doesn’t get too hot or too cold. Once the furnace is up to temperature, it’s time to add the iron. The molten iron is then poured into the mold and left to cool.
The next step is to create the casting. This is done by pouring molten iron into the mold. Once the iron has cooled and set, the casting is removed from the mold and allowed to cool completely.
Once the casting has cooled, it undergoes a series of finishing steps. These steps might include machining, heat treating, surface coating, and more. The goal of these steps is to create a casting that meets the specific specifications required by the customer.
Finally, once all of the finishing touches have been made, the iron casting is ready to be shipped off to its final destination.
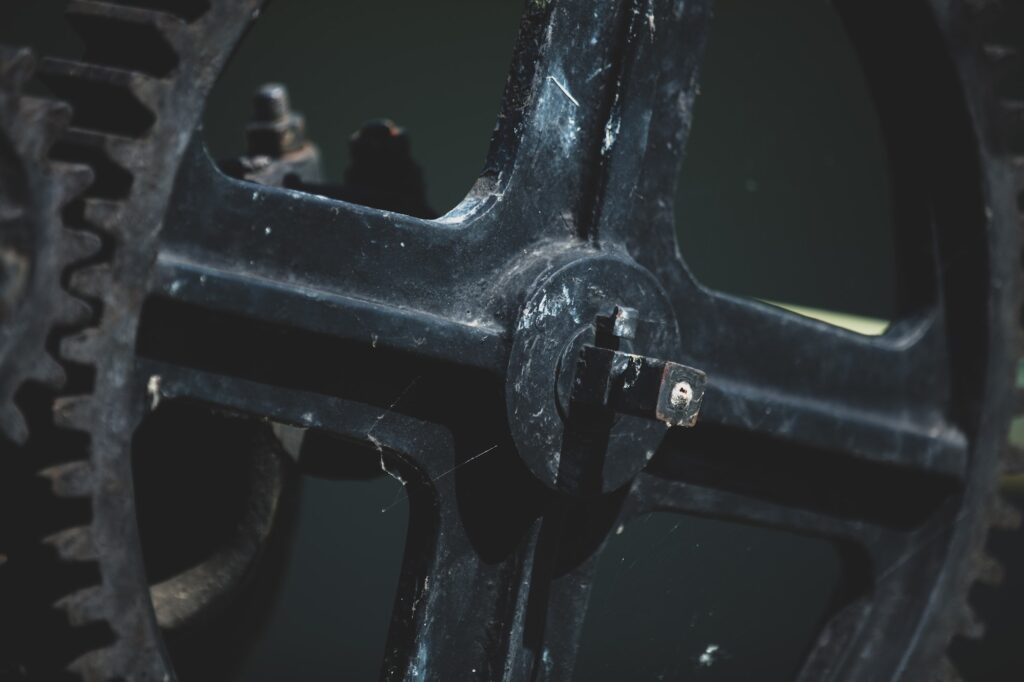
Main Types of Iron Castings
Gray Iron Castings
Gray iron is the most common type of iron casting. It’s made by pouring molten iron into a mold and letting it cool.
The resulting casting is gray in color and has a grainy texture. Gray iron is strong and durable, making it ideal for applications where strength and wear resistance are key.
Ductile Iron Castings
Ductile iron is similar to gray iron, but it contains small amounts of magnesium or other elements that give it greater ductility, or flexibility.
This makes ductile iron ideal for applications where impact resistance or dimensional stability is key.
White Iron Castings
White iron is made by adding carbon to molten pig iron. This makes it harder and stronger than gray or ductile iron.
However, white iron is also more brittle, so it’s not well-suited for applications where flexibility or impact resistance is required.
White iron is often used for wear-resistant applications such as crushing or grinding because its hardness helps it withstand abrasion.
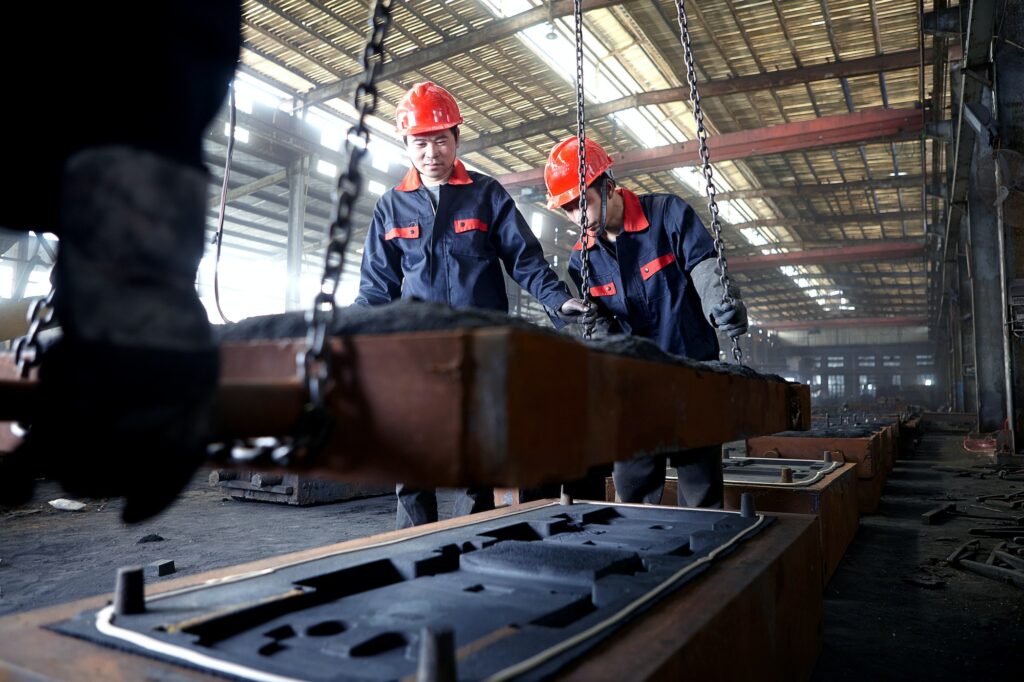
Malleable Iron Castings
Malleable iron is made by annealing white iron castings, which gives them greater ductility and makes them less brittle.
Malleable iron is well-suited for applications that require some flexibility, such as pipe fittings or electrical components.
Conclusion
If you’re looking for a versatile and durable product that can be used in a wide variety of applications, then look no further than iron castings.
Iron castings are strong, resistant to wear and tear, and can be made in any shape or size. In addition, iron castings are also resistant to corrosion.
So if you’re looking for a product that will benefit your business, consider iron castings.
Castimoo is a cast iron manufacturer with 30 years of casting experience. Specializing in the production of gray and ductile iron, we have received high praise from domestic and international customers.
We have encountered a variety of challenges in the casting process, and in the process of continuous experimentation and practice, we have not only solved them one by one, but also provided our customers with high quality iron casting products.
These problems have become our knowledge case base, which is our most valuable knowledge asset. We hope to be of help to you in the future.