When choosing a casting material for a project, it’s important to understand the key differences between cast iron (which is also called gray iron) and ductile iron castings. Both materials have their own advantages and disadvantages that should be taken into account.
In general, cast iron is best suited for applications where strength and hardness are more important than ductile properties, while ductile iron is best suited for applications where ductility is more important than strength and hardness.
Cast Iron vs. Ductile Iron: The Main Differences
Cast iron are made with carbon and silicon as the main alloying elements. The carbon creates flakes within the structure of the metal which gives it its unique gray color.
Cast iron is known for its good damping capacity, meaning it can absorb shock without deforming. It also has good resistance to abrasion, making it ideal for applications where there is a lot of friction.
For these reasons, cast iron is often used in the automotive industry for engine blocks and cylinder heads. Another advantage of cast iron is that it is easier to machine than other types of iron, making it a cost-effective choice for many applications.
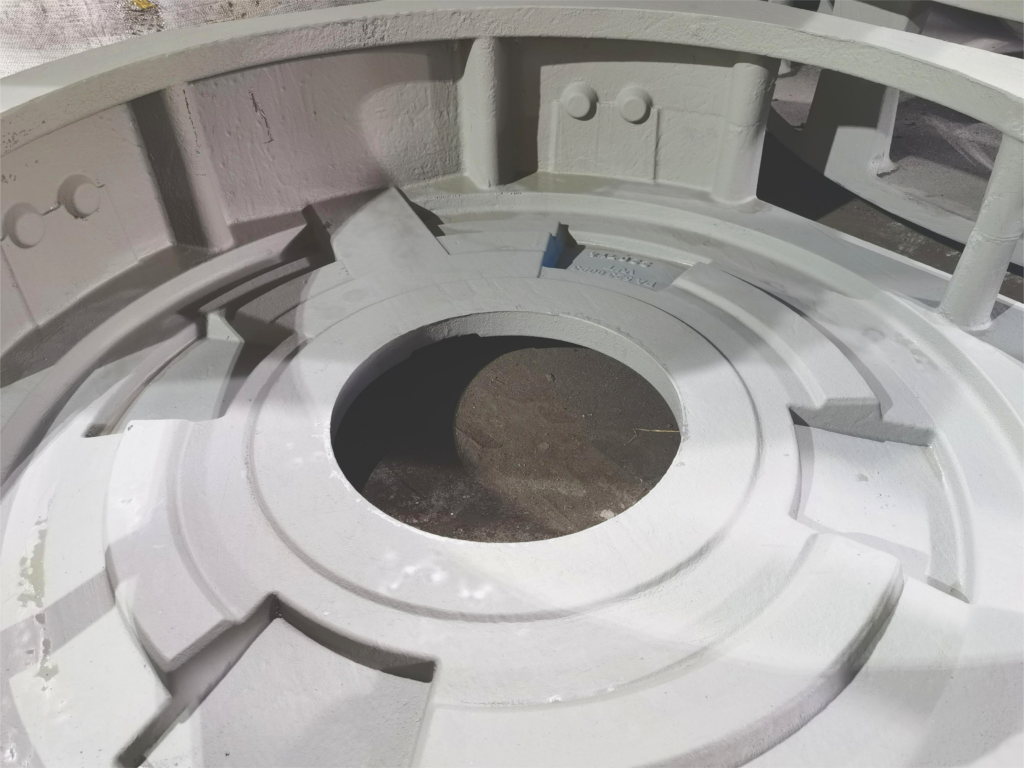
Ductile iron is made with carbon, silicon, manganese, and molybdenum as the main alloying elements. The addition of manganese and molybdenum makes ductile iron more resistant to wear and tear than cast iron. It also has higher tensile strength and ductility, which means it can withstand greater stress without breaking.
For these reasons, ductile iron is often used in construction applications such as pipes and valves. It is also used in the Automotive industry for suspension components such as tie rods and control arms.
Ductile iron can be more expensive than cast iron due to the addition of manganese and molybdenum, but its increased strength and durability make it worth the investment for many applications.
Cast Iron vs. Ductile Iron: Different Grades
Grades of Cast (Gray) Iron
Country | Specification | 150 | 200 | 250 | 300 | 350 |
China | GB/T 5612-1985 | HT150 | HT200 | HT250 | HT300 | HT350 |
France | NFA 32-101-1987 | FGL150 | FGL200 | FGL250 | FGL300 | FGL350 |
Germany | DIN 1691-1985 | GG15 | GG20 | GG25 | GG30 | GG35 |
International | ISO 185-1988 | 150 | 200 | 250 | 300 | 350 |
Italy | UNI 5007-1969 | G15 | G20 | G25 | G30 | G35 |
Japan | JIS G5501-1981 | FC150 | FC200 | FC250 | FC300 | FC350 |
United Kingdom | BS 1452-1990 | 150 | 200 | 250 | 300 | 350 |
USA | ASTM A48-83 | 20A | 30A | 35A | 45A | 50A |
The higher the grade number, the higher the carbon content.
Grades of Ductile (Nodular) Iron
Country | Specification | 400-18 | 400-15 | 500 | 600 | 700 | 800 |
China | GB/T 1348-1988 | QT400-18 | QT400-15 | QT500-7 | QT600-3 | QT700-2 | QT800-2 |
France | NFA 32-201-1976 | FGS370/17 | FGS400/12 | FGS500/7 | FGS600/3 | FGS700/2 | FGS800/2 |
German | DIN 1693-1973 | GGG400/18 | GGG400/15 | GGG500/7 | GGG600/3 | GGG700/2 | GGG800/2 |
International | ISO 1083-1976 | 370/17 | 400/12 | 500/7 | 600/3 | 700/2 | 800/2 |
Italy | UNI 4544-1979 | GS370/17 | GS400/12 | GS500/7 | GS600/3 | GS700/2 | GS800/2 |
Japan | JIS G5502-1982 | FCD (37)363/17 | FCD (40)392/12 | FCD (50)490/7 | FCD (60)588/3 | FCD (70)686/2 | FCD (80)758/2 |
Unite Kingdom | BS2789-1985 | 400/18 | 420/12 | 500/7 | 600/3 | 700/2 | 800/2 |
USA | ASTM A536-84-1976 | 60-40-18 | 65-45-12 | 80-55-06 | 80-60-03 | 100-70-03 | 120-90-02 |
These numbers represent percentages by weight of carbon (C), silicon (Si), and manganese (Mn). Just like with cast iron, the higher grades have more carbon and are therefore stronger and harder but more brittle as well.
It should be noted that there are many other alloys that can be added to both cast iron and ductile iron to alter their properties. These alloys include chromium, molybdenum, nickel, vanadium, etc. Adding these alloys can increase strength, hardness, abrasion resistance, corrosion resistance. But will also increase cost.
Cast Iron vs. Ductile Iron: Application Areas
Cast iron is commonly used in applications where high strength is not required but wear resistance and low cost are important considerations such as: machine tool beds, gears, rollers, crankshafts, pump housings, valves, valve seats and wedges, pressure vessels, manifolds, pistons, piston rings and cylinders, brake drums and discs, differential cases and covers.
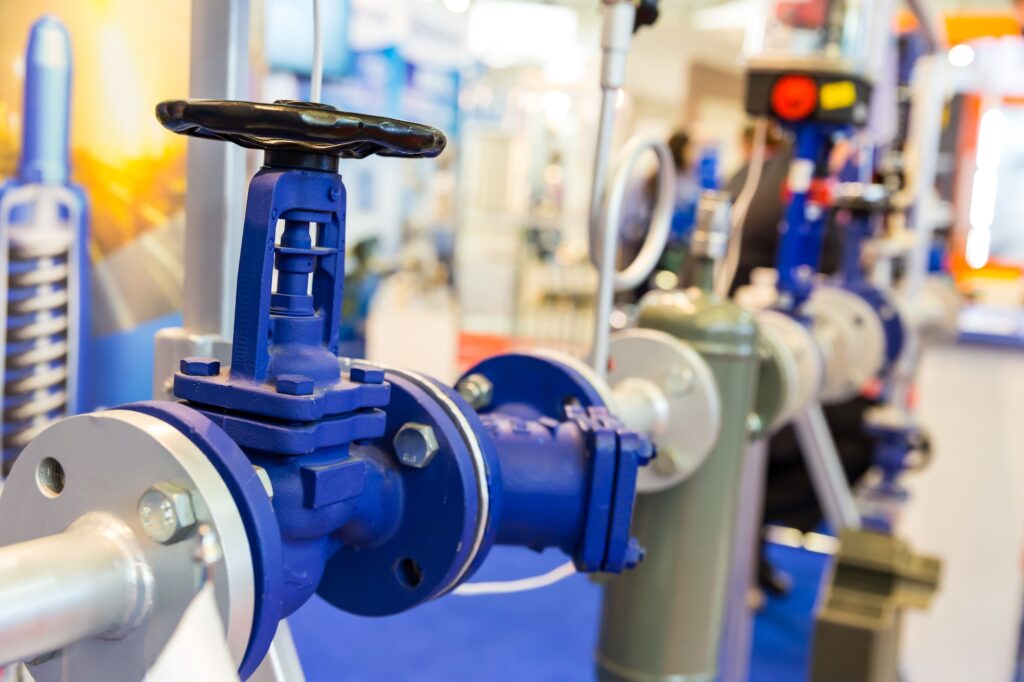
Ductile iron is commonly used in many of the same applications as cast iron but is typically used when higher strength or improved ductility is required such as: automotive suspension components, hydraulic cylinder barrels, crankshafts, connecting rods, gears transmission shafts and axles.
Cast Iron vs. Ductile Iron: Production Process
Cast iron are made by pouring molten pig iron into sand molds. Once the pig iron has cooled and hardened, it’s ready to be used in whatever application it was intended for. The main benefit of cast iron is that it’s very strong and durable.
Cast iron also has good vibration dampening qualities, which makes it ideal for use in applications where there will be a lot of movement or vibrations.
Ductile iron castings are made using the same basic method as cast iron. The difference is in the composition of the pig iron.
In order to create ductile iron, manufacturers add spheroidizer containing magnesium or cerium to the pig iron before pouring it into the mold.
This addition gives ductile iron its increased ductility over cast iron. The increased ductility of ductile iron makes it an ideal choice for applications that require flexibility or elongation.
Cast Iron vs. Ductile Iron: Machinability
One of the biggest difference between cast iron and ductile iron is machinability—or how easy or difficult it is to machine a particular type of iron.
In general, cast iron is easier to machine than ductile iron.
The reason for this is that cast iron has a lower carbon content than ductile iron, which means that there are fewer carbon particles in the metal that can cause obstacles during the machining process.
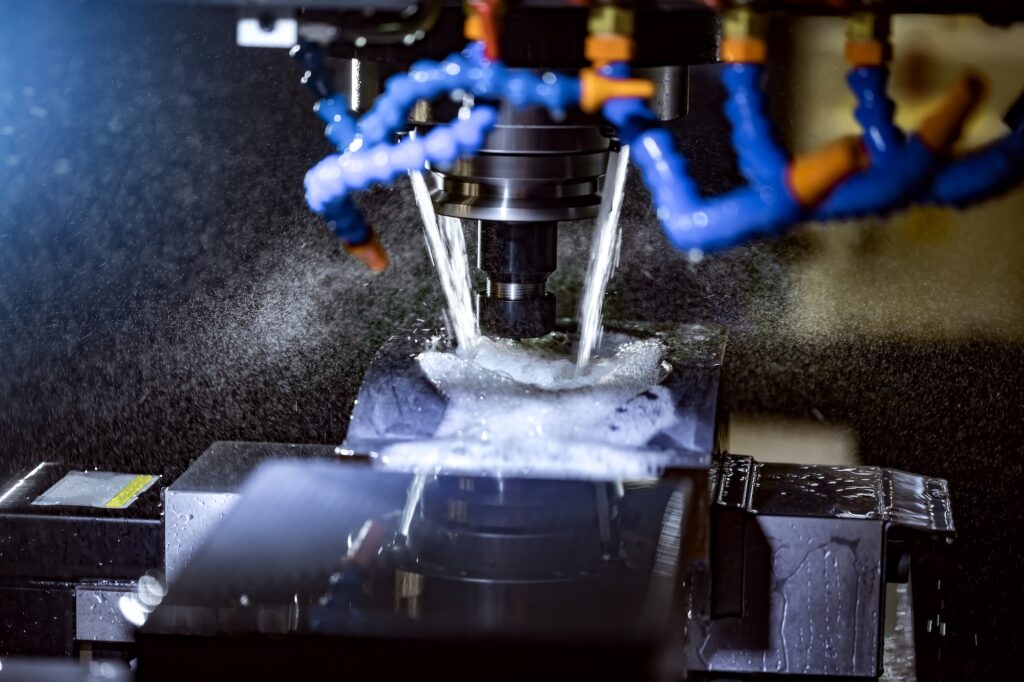
However, even though cast iron is generally easier to machine than ductile iron, there are still some challenges that need to be taken into account. For example, cast iron tends to be more brittle than ductile iron, which means that it can break more easily during the machining process.
In addition, cast iron also has a higher graphite content than ductile iron, which can cause issues with clogging and build-up during the machining process.
Cast Iron vs. Ductile Iron: Surface Finish Quality
Another important consideration when choosing between cast iron and ductile iron is surface finish quality—or how smooth and polished the final product will be. When it comes to surface finish quality, ductile iron definitely has the upper hand over cast iron.
The reason for this is that, because of its higher carbon content, ductile iron can be heat-treated in such a way that its surface becomes harder and smoother. This results in a much higher-quality surface finish when compared to cast iron.
Cast Iron vs. Ductile Iron: Heat Treatments
Cast iron castings are best suited for applications where high temperatures are not a concern. In general, cast iron can withstand temperatures up to 1200°F (650°C). When cast iron is heated above this range, the graphite flake structure begins to deteriorate, which can lead to premature failure. For this reason, gray iron is not typically used in high-temperature applications.
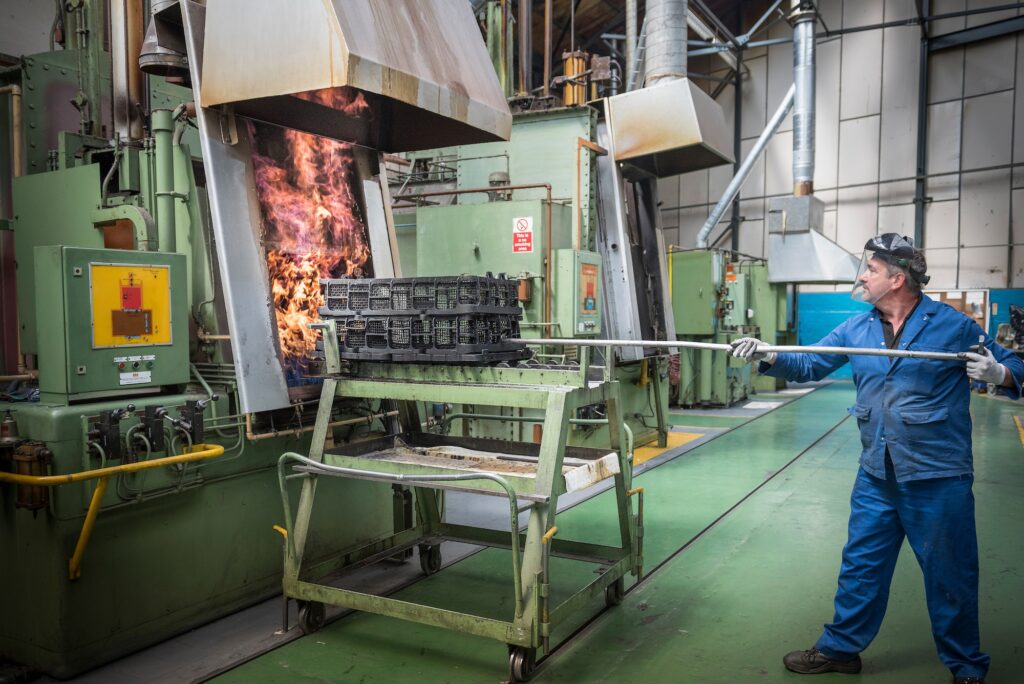
Ductile iron, on the other hand, is best suited for applications that require high temperatures. The microstructure of ductile iron is more resistant to degradation at high temperatures than gray iron. As a result, ductile iron can withstand temperatures up to 1800°F (980°C).
When it comes to heat treatment, both cast iron and ductile iron can be annealed, normalized, quenched, and tempered. However, because of its higher carbon content, cast iron is more difficult to weld than ductile iron. Ductile iron can also be alloyed with chromium, molybdenum, and nickel to improve its weldability.
Cast Iron vs. Ductile Iron: The Cost
Cast iron castings are less expensive than ductile iron castings. That’s because they’re easier to produce and don’t require as much material. Cast iron is also more resistant to wear and tear than ductile iron, which means it will last longer before it needs to be replaced or repaired. However, cast iron is more brittle than ductile iron, which means it’s more likely to break or crack under stress.
Ductile iron is more expensive than gray iron because it’s more difficult to produce and requires more material. However, its increased strength and durability means it will last longer before it needs to be replaced or repaired. Ductile iron is also less likely to break or crack under stress than cast iron, making it the ideal choice for applications where safety is a concern.
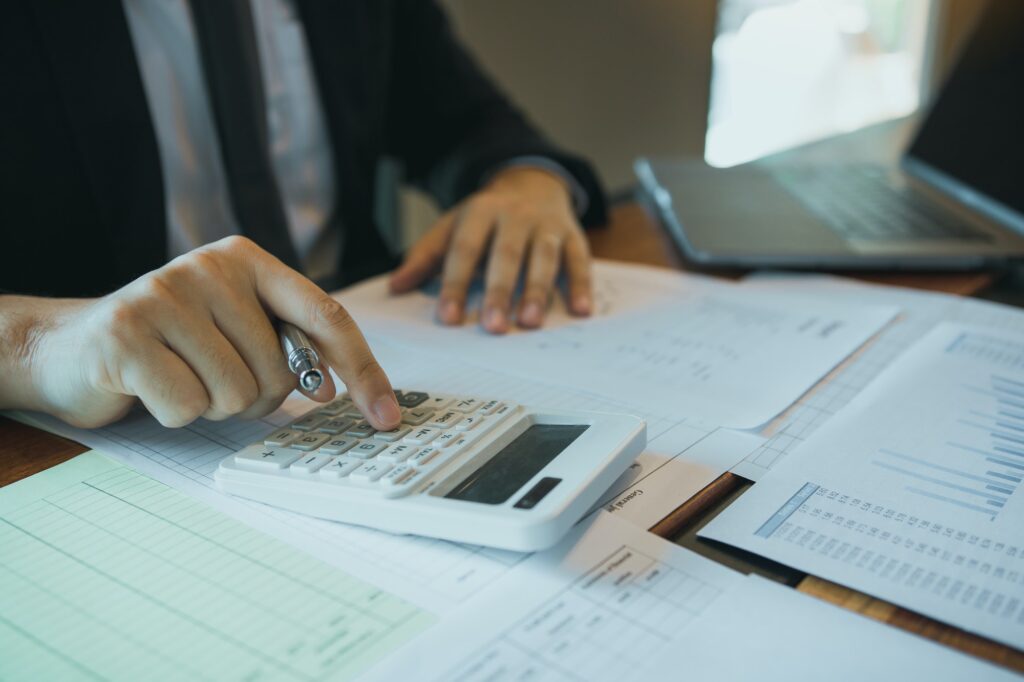
For cast iron, the average price per pound is USD$0.60 (USD$1.32/kg). For ductile iron, the average price per pound is USD$0.85 (USD$1.87/kg). This means that, on average, ductile iron costs 40% more than cast iron.
It should be noted that I have visited no less than 50 foundries in China. The quality of the castings produced also varies. Some manufacturers produce ductile iron for less than $1/kg, which is less than $0.45 per pound. Such prices look very attractive, but for the quality of the product to put a question mark.
If you’re looking for the most economical option, then cast iron castings are the way to go. But if you need a casting that’s stronger and more durable, then you’ll need to pay more for ductile iron.
In either case, it’s important to consider the total cost of ownership when making your decision so that you can choose the option that’s best for your needs and budget.
Key Considerations for Sourcing in China
As a buyer, you always want to get the best value for your money. When it comes to purchasing cast iron and ductile iron castings from China, there are a few things you should keep in mind in order to ensure you are getting a high quality product.
1.Certification
Check if the company has ISO 9001 certification. This certification means that the company has meets the standards set by the International Organization for Standardization and is committed to providing high quality products and services.
More important than ISO 9001 certification, is discharge permit. A discharge permit is a basic requirement for operating a foundry in China. If your potential foundry supplier is not equipped with this document, there is a risk of stopping production in the middle of the process, so you need to pay more attention.
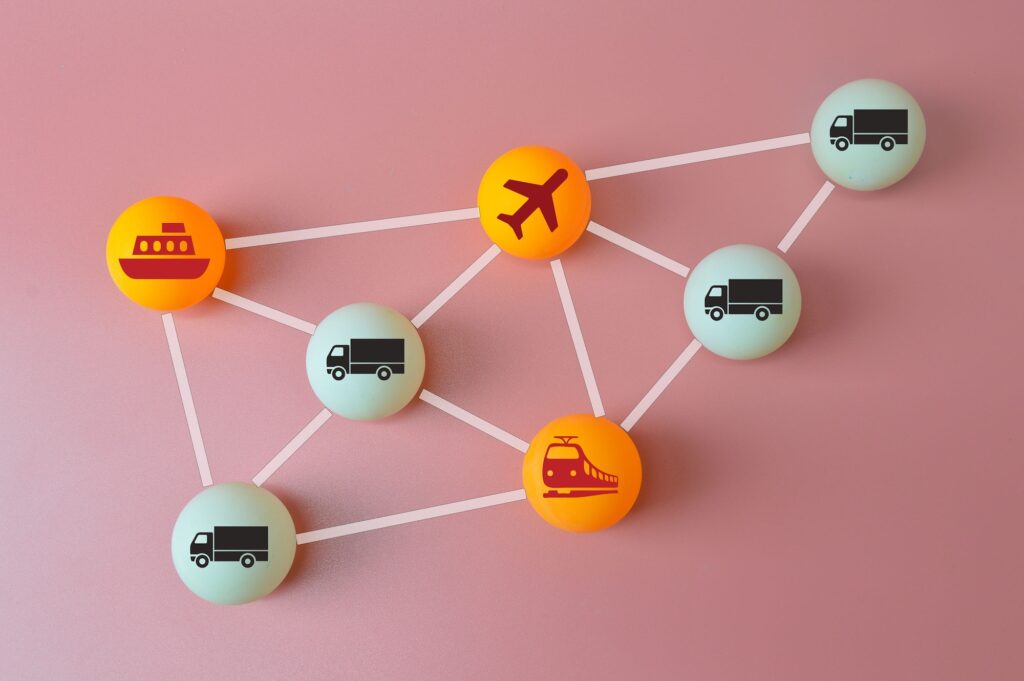
2. Pricing
When it comes to pricing, there is a wide range of prices quoted by suppliers in China. This is because there are a number of factors that can affect the price of iron castings, such as the size and complexity of the casting, the quantities required, and the lead time. As a result, it’s important to get quotes from several different suppliers so that you can compare prices and find the best deal.
3. Quality Control
Quality control is another important consideration when purchasing iron castings from China. There are a number of ways to ensure that you’re getting high-quality products, including working with a reputable supplier, conducting audits at the factory, and requesting samples before placing an order.
Purchasing ductile iron castings from China can be a great way to save money on your procurement costs. However, there are a few things you need to keep in mind in order to ensure that you’re getting high-quality products at a fair price.
Be sure to look for certification, get quotes from multiple suppliers, and conduct quality control checks before making your purchase. With these considerations in mind, you can be confident that you’re getting the best value for your money when sourcing ductile iron castings from China.
Castimoo has 30 years of experience in the cast iron and ductile iron industry, so you can rest assured that we know our stuff. And because we’re a one-stop supplier, we can save you time and hassle in sourcing your casting needs from multiple suppliers. We encourage you to get in touch with us today.