Can Cast Iron Be Welded?
The answer is yes! Cast iron can be welded.
Welding is a process of joining two materials, usually metals, by melting them together and using a filler material to form a strong bond.
The filler material is molten when it is applied and cools to form a joint between the two pieces that are being welded.
Welding is used in a variety of applications, from construction to automotive manufacturing.
Welding can be done with different types of materials, including cast iron.
Cast iron is made by melting pig iron (an ingredient in steel making) in a furnace and adding carbon.
The molten pig iron is poured into molds called casts.
As the pig iron cools, it solidifies into the desired shape.
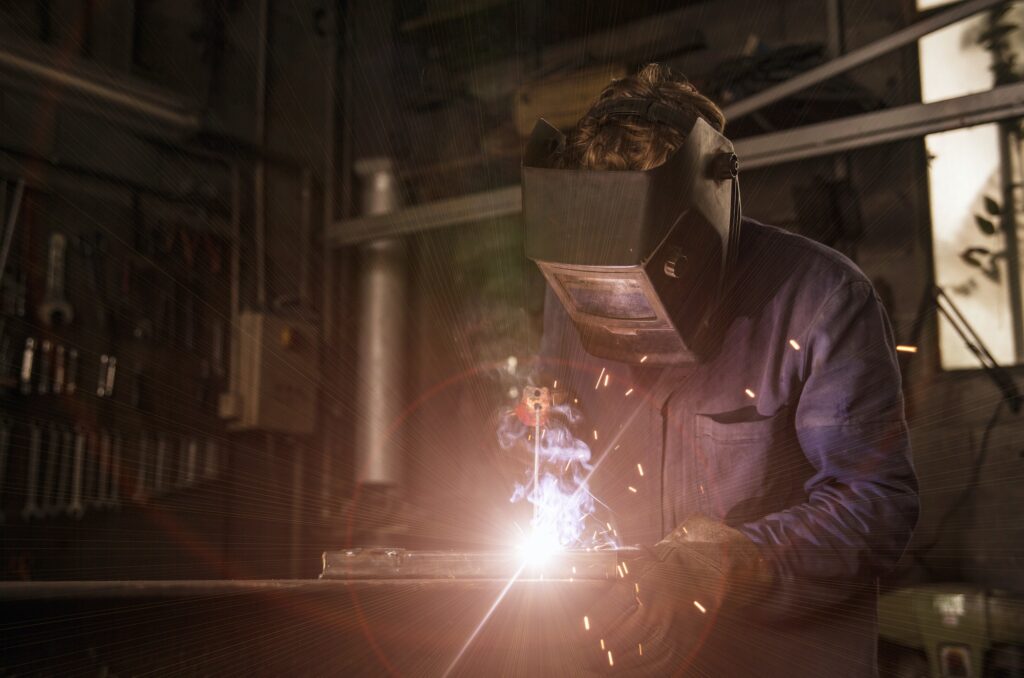
The main obstacle to welding cast iron is its high carbon content.
When welding carbon-rich materials like cast iron, there’s a risk that the weld will not fuse properly with the base metal.
This is because carbon has a lower melting point than iron, when welding, the heat from the welding arc can cause the carbon to vaporize and create voids in the weld bead.
These voids weaken the joint and make it more likely to break under stress.
Benefits and Risks of Welding Cast Iron Parts
Welding offers a number of benefits over other methods of joining cast iron parts together.
For starters, it’s fast and efficient.
Welding can also be used to repair damaged or worn-out parts.
Additionally, welding produces strong joints that are resistant to fatigue and vibration.
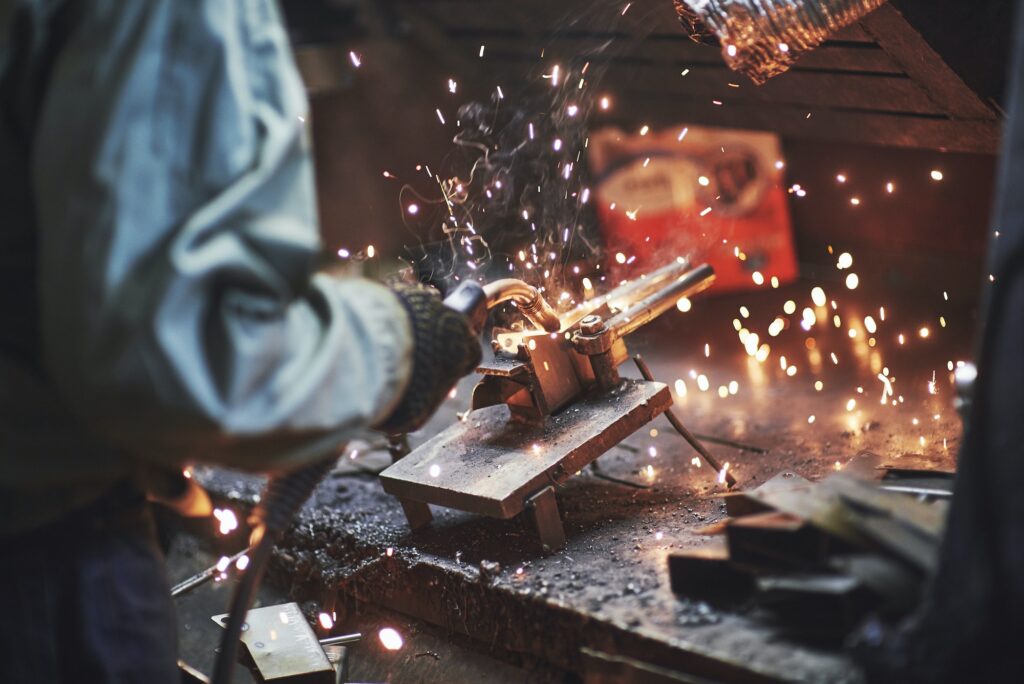
Like any other type of manufacturing process, there are a few risks associated with welding.
First and foremost, it’s important to make sure that all safety precautions are followed to avoid accidents.
Secondly, poor welds can lead to joint failure or other structural problems.
Finally, improper ventilation can cause dangerous fumes to build up in the workspace.
6 Factors to Consider Before Welding
1. The Type of Cast Iron
There are three types of cast iron: white cast iron, gray cast iron, and ductile cast iron.
Gray cast and white cast iron are the most common types of cast iron used in construction.
Gray cast iron contains more carbon than white cast iron and is more brittle as a result.
White cast iron contains less carbon and is more malleable.
2. The Age of the Cast Iron
Older cast irons are more likely to have higher carbon content, which makes them more difficult to weld.
Newer cast irons have lower carbon content and are easier to weld as a result.
3. The Condition of the Cast Iron
If the cast iron you’re working with is in good condition, it will be easier to weld than if it is in poor condition.
If the cast iron is rusty or has flaking paint, it will be more difficult to weld because those factors can affect the quality of the weld.
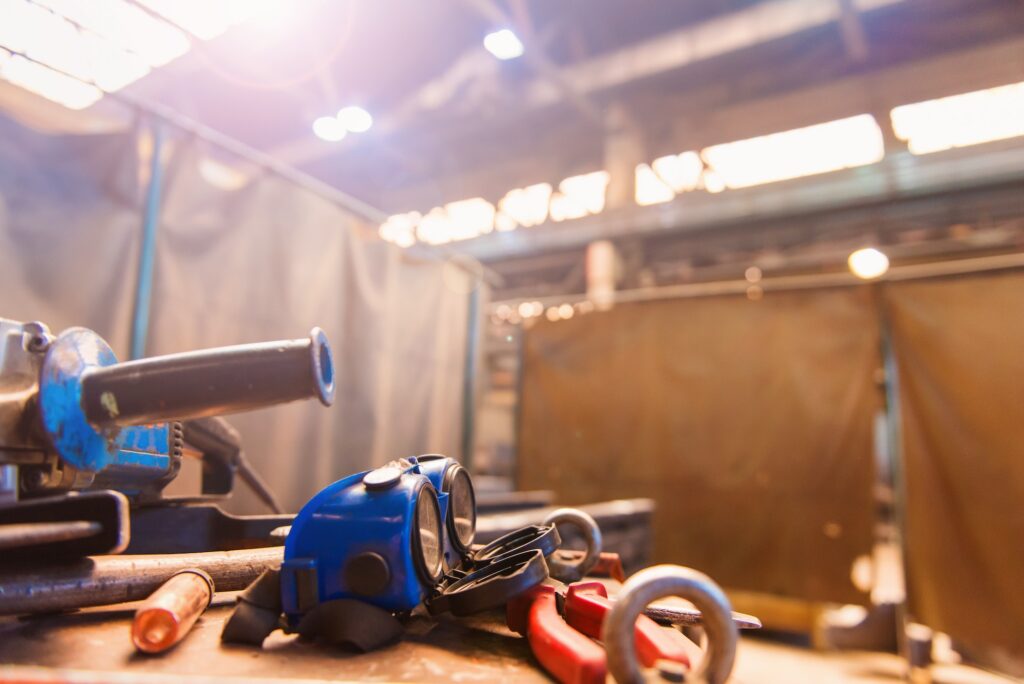
4. The Material Thickness of the Cast Iron
This is because the thicker the material, the more heat is required to weld it.
If the material is too thick, then it will be extremely difficult to weld and you may not be able to achieve a quality weld.
On the other hand, if the material is too thin, then it may not be strong enough to hold up under its own weight or the weight of whatever it is you are welding it to.
You will need to take into account the thickness of both the base metal and any filler metals you are using.
The base metal is the metal that you are actually welding, while filler metals are used to add strength or other properties to the weld.
There are many different types of filler metals available, so be sure to consult with a professional before choosing one for your project.
5. Joint Design of the Cast Iron
The joint is where two pieces of metal come together and will be welded together.
There are many different types of joints available, but not all of them are suitable for every project.
For example, lap joints are often used for projects where aesthetics are not a concern, such as in industrial applications.
However, if you are doing a welding project for something that will be on display, such as a piece of art or furniture, then you will want to choose a joint that provides a clean, finished look.
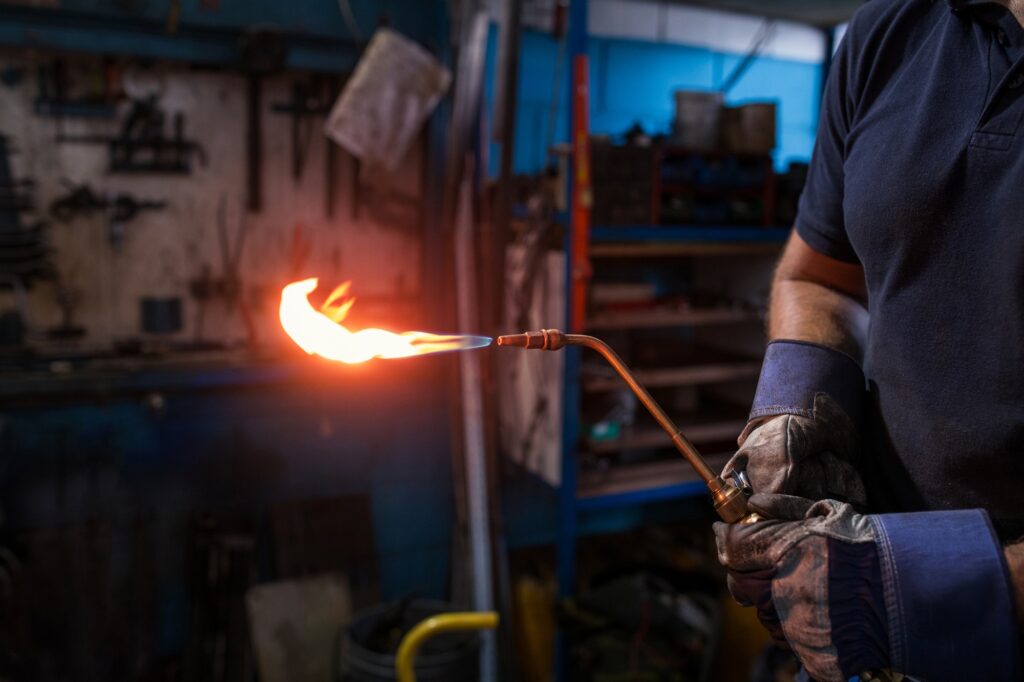
6. Welding Process of the Cast Iron
Finally, you will need to choose a welding process that is appropriate for your project.
There are many different welding processes available, each with its own advantages and disadvantages.
Some of the most popular welding processes include mig welding, tig welding, and arc welding.
Again, it is important to consult with a professional before choosing a welding process so that you can be sure that it is appropriate for your project.
6 Tips for Welding Cast Iron
1. Clean the Surface of the cast iron parts
One of the most important things to do when welding cast iron is to clean the surface of the part.
Any dirt, grease, or debris on the surface of the part will weaken the weld and can cause it to fail.
Be sure to clean the surface of the part thoroughly before beginning any welding.
2. Use the Right Equipment
Another important tip for welding cast iron is to use the right equipment.
You’ll need an AC arc welder that is rated for use with cast iron.
Be sure to read the instruction manual for your welder carefully so that you understand how to set it up and use it properly.
3. Choose the Right Welding Rods
Not all welding rods are created equal.
When welding cast iron, you’ll want to use low-hydrogen welding rods.
These rods produce less hydrogen gas, which can cause Porosity (tiny holes) in the weld.
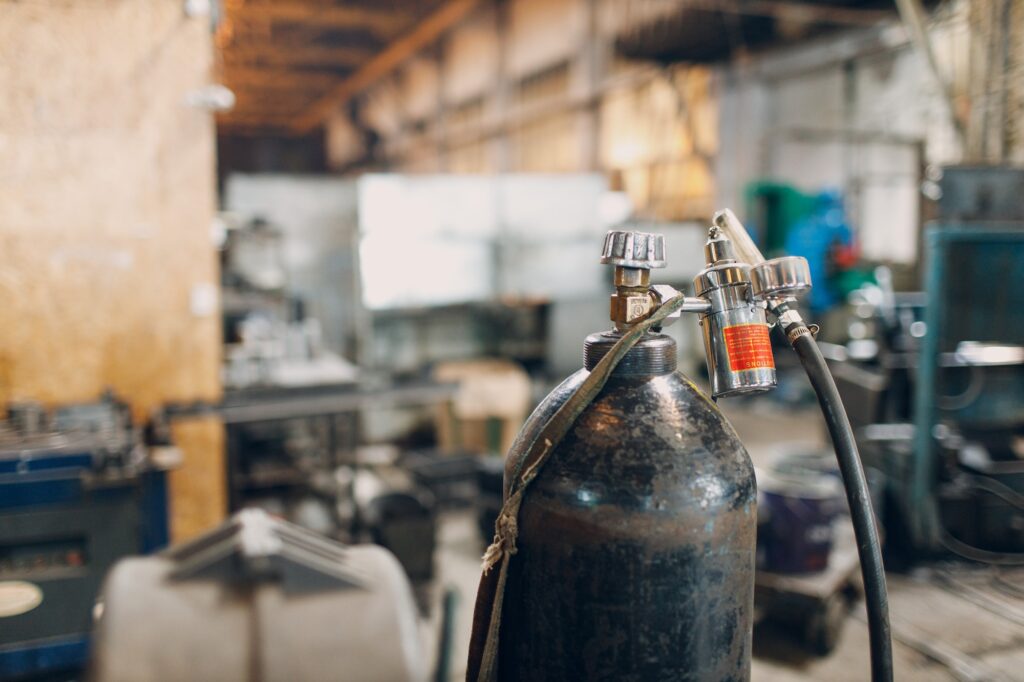
4. Use Low Amperage Settings
When welding cast iron parts, it’s important to use low amperage settings on your welder.
If you use too high of an amperage, you run the risk of burning through the part or causing other damage.
Start at a low amperage and increase as needed until you find a setting that works for you.
5. Use Short Welds
When welding cast iron parts, it’s best to use short welds rather than long ones.
This helps to prevent warping and distortion of the part.
If you must make a long weld, be sure to stop frequently and allow the part to cool so that it doesn’t warp.
6. Preheat the Part Before Welding
Last but not least, be sure to preheat the part before welding.
This helps to prevent cracking and ensures a strong weld overall.
Simply place the part on a heated plate or in an oven set to low heat for about 15 minutes before beginning to weld.
What Else Needs to Be Done After Welding Cast Iron?
1. Inspect the welds
After welding, it is important to inspect the welds to look for any signs of defects.
Identifying and addressing any defects early on will save you time and money in the long run.
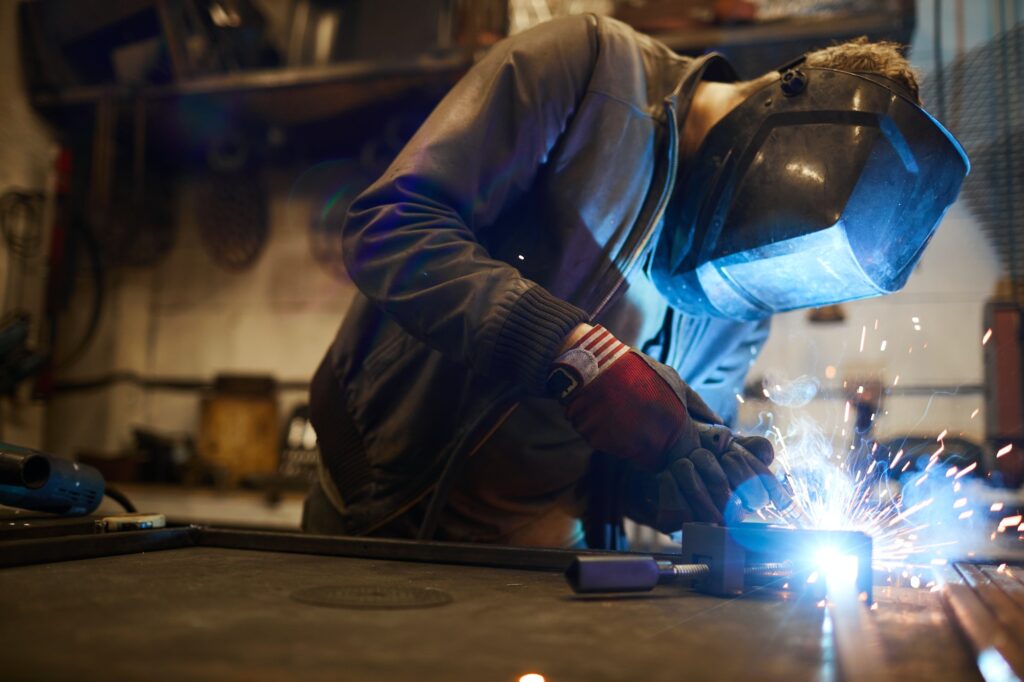
2. Remove any slag
Slag is a byproduct of welding that can weaken the quality of the weld if it is not removed.
Use a chipping hammer or wire brush to remove any slag from the weld.
3. Dress the welds
Dressing the welds helps to remove any sharp edges and burrs, which can cause injuries.
Use a grinding wheel or file to dress the welds as needed.
4. Apply a protective coating
A protective coating will help to prevent corrosion and extend the life of the welds.
Talk to your supplier about which type of coating is best for your application.
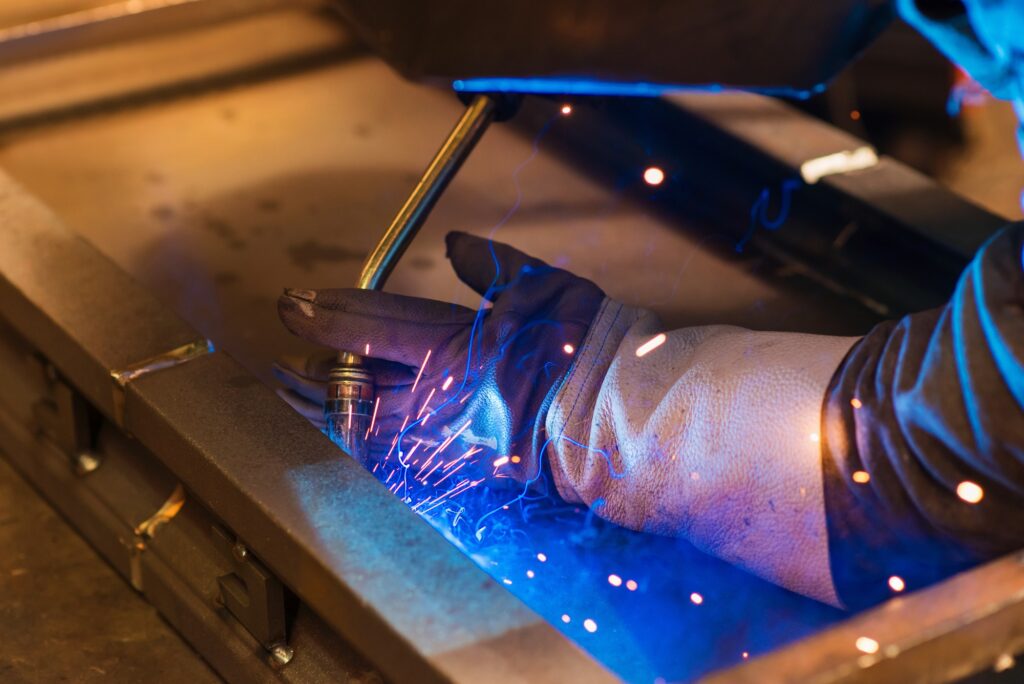
3 Ways to Join Cast Iron Parts Together without Welding
1. Bolting
This is the most common way to join two pieces of cast iron parts together.
Bolts are easy to find and relatively inexpensive, making them a great option for joining cast iron parts.
2. Riveting
Rivets are another popular option for joining cast iron parts.
Rivets are more difficult to install than bolts, but they can create a stronger joint.
3. Tapping
Tapping is a method of threading holes into the cast iron so that screws can be used to join the two pieces together.
Tapping is more difficult than bolting or riveting and is best left to professionals.
Conclusion
Welding is a popular method for joining iron casting parts together due to its speed and efficiency.
However, it’s important to choose the right type of welding process and follow all safety precautions to avoid accidents or structural problems.
When done correctly, welding can produce strong, reliable joints that will last for years to come.