Introduction
In the field of machinery and equipment, iron castings play a crucial role in ensuring optimal performance and durability. However, the quality and efficiency of iron castings largely depend on the design and manufacture of their molds.
This is where 3D modeling comes in as an essential tool for optimizing the design and production of iron castings molds. In this article, we will explore the reasons why 3D modeling is a must-have in the design of iron castings molds.
Iron Castings in Machinery and Equipment
Iron castings are widely used in the manufacturing of machinery and equipment due to their excellent mechanical properties, versatility, and cost-effectiveness. They are used in a variety of applications, such as engine blocks, transmission housings, pump housings, and many more. The quality and precision of these castings are essential in ensuring optimal performance, safety, and durability of the equipment.
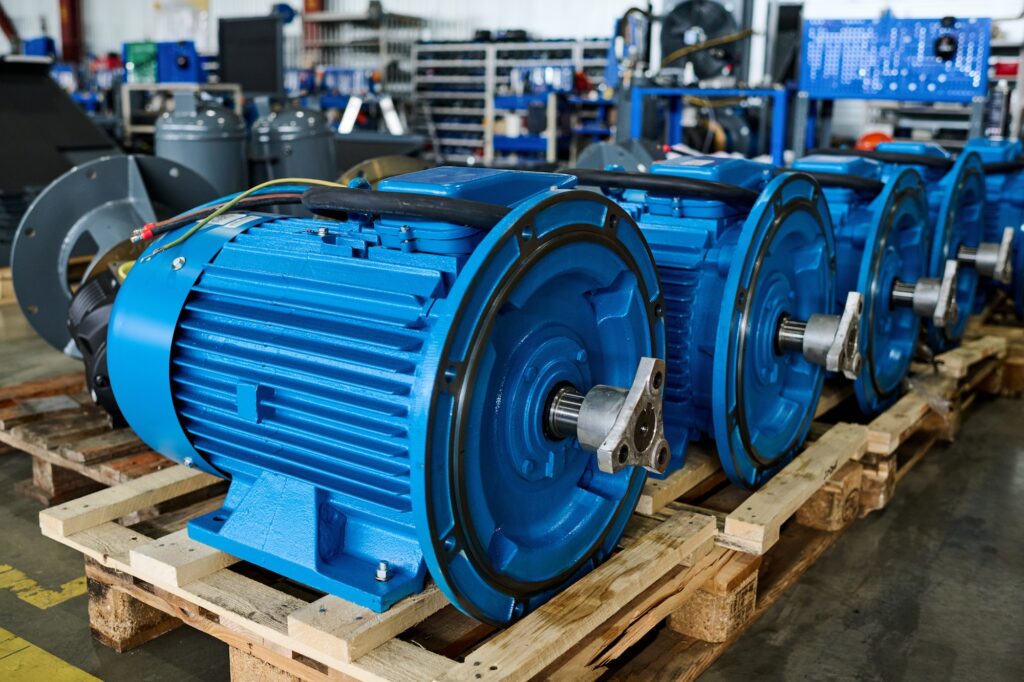
The Importance of Iron Castings Mold Design
The design of iron castings molds is a critical step in the production process that affects the quality, efficiency, and cost-effectiveness of the final product. Poor mold design can result in casting defects, reduced mechanical properties, and increased production costs.
Therefore, it is essential to ensure that the mold design is accurate, efficient, and optimized for the intended application.
Why 3D Modeling is Essential in Iron Castings Mold Design
3D modeling is a powerful tool for optimizing the design and production of iron castings molds. It allows for more accurate and efficient mold designs, reduces the risk of casting defects, and improves the overall quality and performance of the castings. Some of the key benefits of 3D modeling in iron castings mold design include:
Improved Precision: 3D modeling allows for more precise and accurate mold designs, resulting in higher quality and more efficient production.
Faster Turnaround Times: 3D modeling enables faster and more efficient mold design iterations, reducing the time and cost of production.
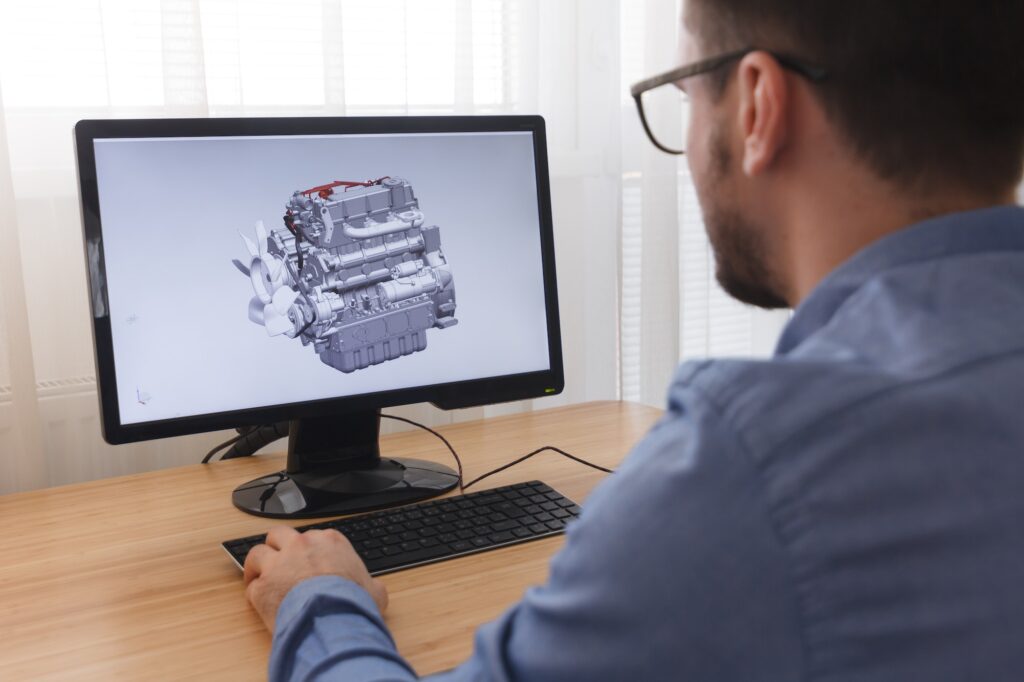
Reduced Costs: 3D modeling helps to identify and eliminate design flaws early on, reducing the need for costly rework and improving the overall cost-effectiveness of the production process.
Enhanced Collaboration: 3D modeling enables real-time collaboration between designers, engineers, and manufacturers, ensuring that everyone is on the same page and working towards the same goals.
Design Considerations for Iron Castings
When designing iron castings, there are several key factors to consider, such as material selection, casting geometry, and processing methods. These factors can significantly impact the quality and performance of the final product, and it is crucial to ensure that they are optimized for the intended application. Some important design considerations for iron castings include:
Material Selection: The choice of material for iron castings should be based on the intended application, the required mechanical properties, and the cost-effectiveness of the production process.
Casting Geometry: The geometry of the casting should be optimized to minimize the risk of defects, such as shrinkage and porosity, and to ensure that the casting can be easily removed from the mold.
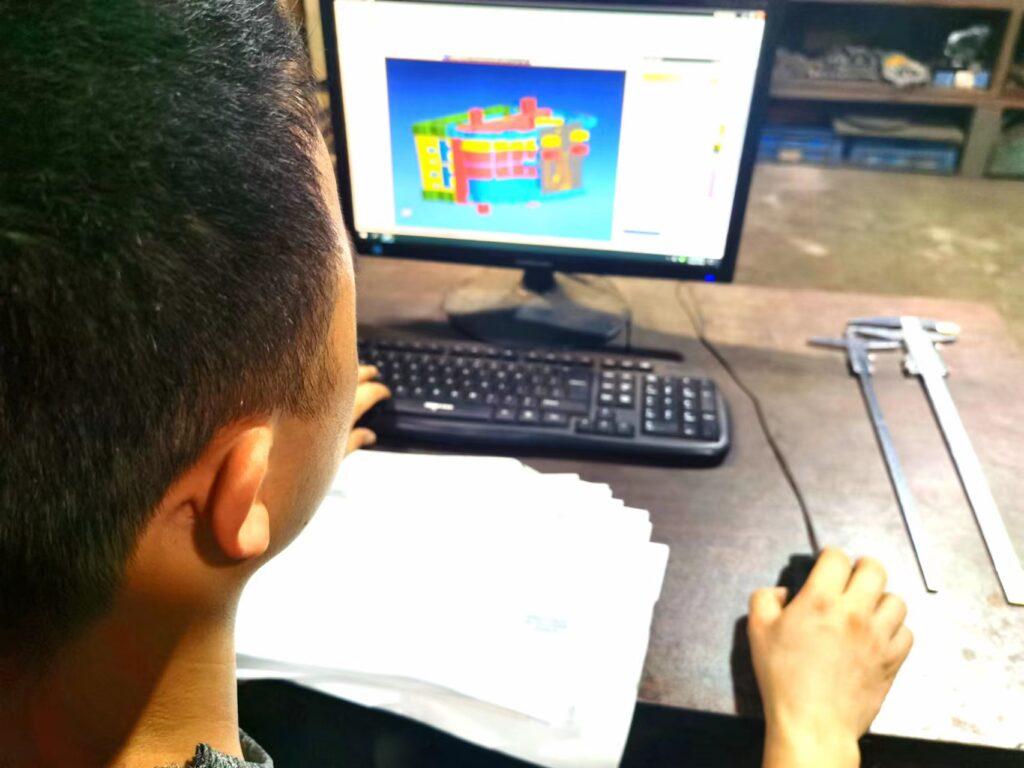
Processing Methods: The processing methods used in the production of iron castings, such as heat treatment and surface finishing, can significantly impact the quality and performance of the final product.
Environmental Considerations: When designing iron castings, it is essential to consider environmental factors, such as the impact of the casting process on air and water quality, and to ensure that the production process is as sustainable as possible.
Conclusion
In conclusion, 3D modeling is an essential tool for optimizing the design and production of iron castings molds. It enables more accurate, efficient, and cost-effective mold designs, resulting in higher quality and more durable castings. When designing iron castings, it is important to consider factors such as material selection, casting geometry, processing methods, and environmental impact to ensure that the final product meets the required specifications and standards.
We are Castimoo, we specialize in the production of high-quality iron castings and are committed to providing our clients with the best possible solutions for their needs. Contact us today to learn more about our products and services.