Introduction
The ASTM A48 standard is an important document that outlines the requirements for iron castings. It is important to understand the special factors considered in this standard because they can have a big impact on your casting project. In this blog post, we’ll look at the 10 most important issues to consider when using the ASTM A48 standard.
1. Chemical Composition
ASTM A48 specifies the minimum levels of chemical composition that must be met to ensure proper performance of the casting. For example, carbon and sulfur are two elements that must be controlled within specific limits because too much of either element can cause brittleness or corrosion of the casting.
Manganese must also be included in the composition because it has a positive effect on hardness and strength. In addition to these elements, ASTM A48 requires that all castings meet minimum levels of silicon and phosphorus.
The presence of impurities such as sulfur and lead can cause a reduction in the mechanical properties of the casting, so it is important to ensure that these elements are kept to a minimum.
To achieve higher levels of strength, trace elements can be added to the composition. Such as copper and tin to improve the corrosion resistance of the casting, while other elements, such as nickel and cobalt, are sometimes used to control grain size and refine the microstructure.
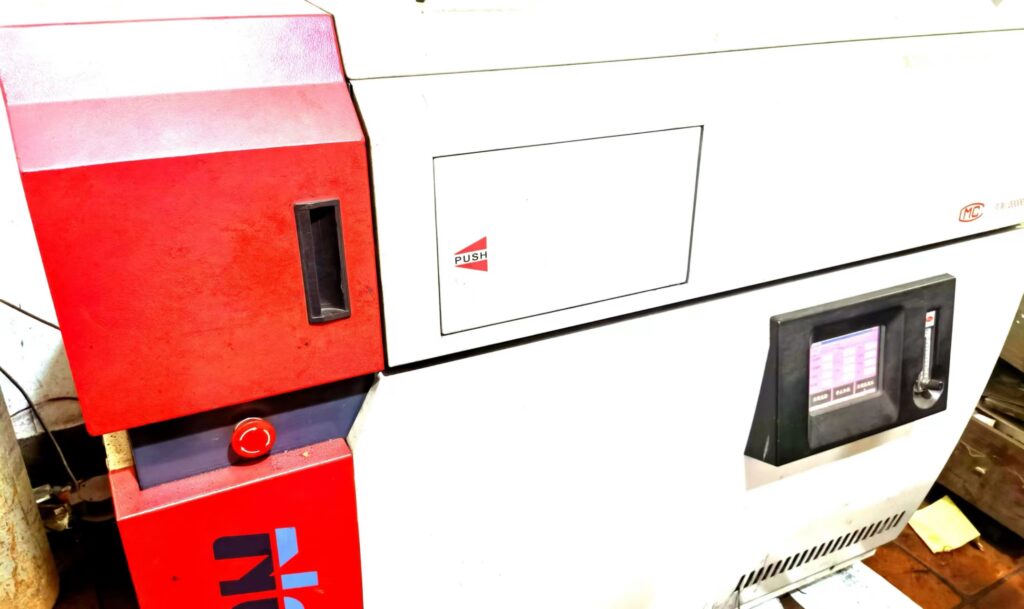
2. Impact Testing
The impact resistance of a casting is an important factor in determining its overall performance. ASTM A48 requires that the casting be tested for impact resistance, such as by dropping it or striking it with a hammer. This helps ensure that the casting is tough enough to withstand a blow without cracking.
When evaluating the impact resistance of a casting, several factors must be considered. The environment in which the test is conducted can have an impact on the results. Temperature and humidity can affect the speed and amount of force applied to the casting during the test. Other variables, such as material type, casting shape, size, thickness and composition.
It is also important to determine the amount of energy required for impact testing. Depending on the material and the thickness of the casting, different forces may be required to break or deform it, so it is important to use the appropriate level of energy in the test.
Finally, the direction of the impact force must be taken into account. Castings that are impacted from one side require a different amount of energy than castings that are impacted from both sides at the same time. By understanding how these factors affect the results of impact testing, engineers can ensure that their castings meet standard requirements.
3. Tensile Strength
Tensile strength is a measure of a casting’s ability to resist being pulled apart. ASTM A48 requires that all castings must meet a minimum level of tensile strength to be accepted for use in an application.
The ASTM A48 standard specifies the maximum allowable tensile strength for a particular casting based on its type and size. For example, gray cast iron has a higher minimum allowable tensile strength than ductile iron or steel alloys of the same size. It is important to note that while this standard provides a baseline of acceptable tensile strengths, the actual values obtained during testing may vary considerably from casting to casting.
To determine the tensile strength of a casting, engineers utilize a device called a tensiometer. This instrument applies a force to the material until it reaches the breaking point or yielding. The force applied is measured in pounds per square inch (PSI).
4. Density
Density is the amount of material packed into a given volume and it affects the quality of the material. ASTM A48 requires that any iron casting must have a density of at least 7.2g/cm³ to ensure proper performance.
This requirement is based on the fact that less dense materials are more likely to crack during casting and machining due to thermal stress. In addition, less dense objects may also be weaker and less durable than objects made from denser materials.
The ASTM A48 standard also outlines the maximum allowable limits for density. The maximum allowable density is 8.4g/cm³, as this ensures that the casting is not too dense and may be prone to warping or other defects after casting, resulting in structural instability of the finished casting and reducing its overall strength.
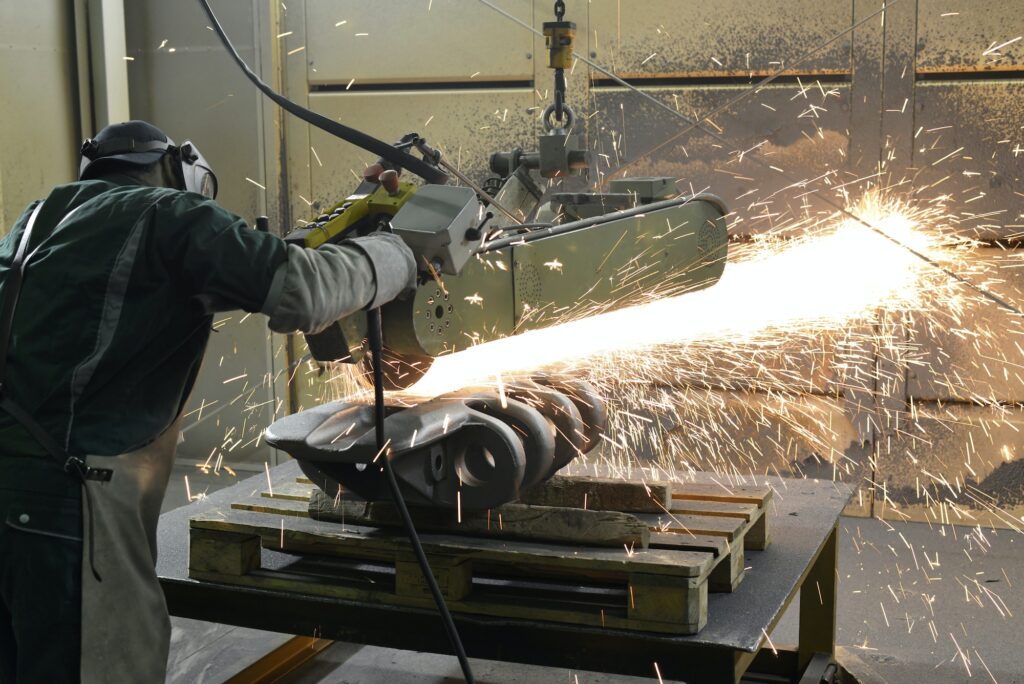
5. Abrasion and Corrosion Resistance
Abrasion and corrosion resistance are important factors in determining how long a casting will last. ASTM A48 specifies the test procedures that must be performed to determine the wear and corrosion resistance of a casting.
ASTM A48 test procedures include the use of calibrated abrasives to measure the wear resistance of a casting. The castings are subjected to abrasion for a specified period of time, and then inspected and measured for signs of wear. This is done using a microscope and measuring equipment such as calipers or depth gauges.
Corrosion resistance is also evaluated using ASTM A48 standards. Castings are subjected to a salt spray test and then inspected for signs of corrosion. This is done by measuring the depth of penetration of the salt solution into the casting, which indicates how well the casting resists corrosion.
6. Porosity
ASTM A48 requires castings to have a minimum level of porosity and no visible voids or cracks. Porosity affects the strength and durability of the casting, so it is important to ensure that it is at the required level.
The amount of air or other gases contained in the material is a key factor in porosity. If there is too much air or gas trapped in the material, then it will create voids in the casting, which will reduce its strength and durability.
The rate of cooling is another factor to consider. If the material is cooled too quickly, it can lead to voids in the casting as well as other defects. Slower cooling rates can allow gases to escape more easily, and these problems are to be avoided.
Finally, the grain size of the metal should also be taken into account. If the grain size is too small, then shrinkage and other porosity problems can result. the ASTM A48 standard requires a coarse grain size to achieve optimum casting performance.
7. Surface finish
ASTM A48 requires castings to have a specific surface finish because it has an effect on both the appearance and performance of the part. For example, surface roughness can affect fatigue life and wear resistance.
Factors that determine surface finish include porosity, core marks, surface roughness, oil/water spots, and discoloration.
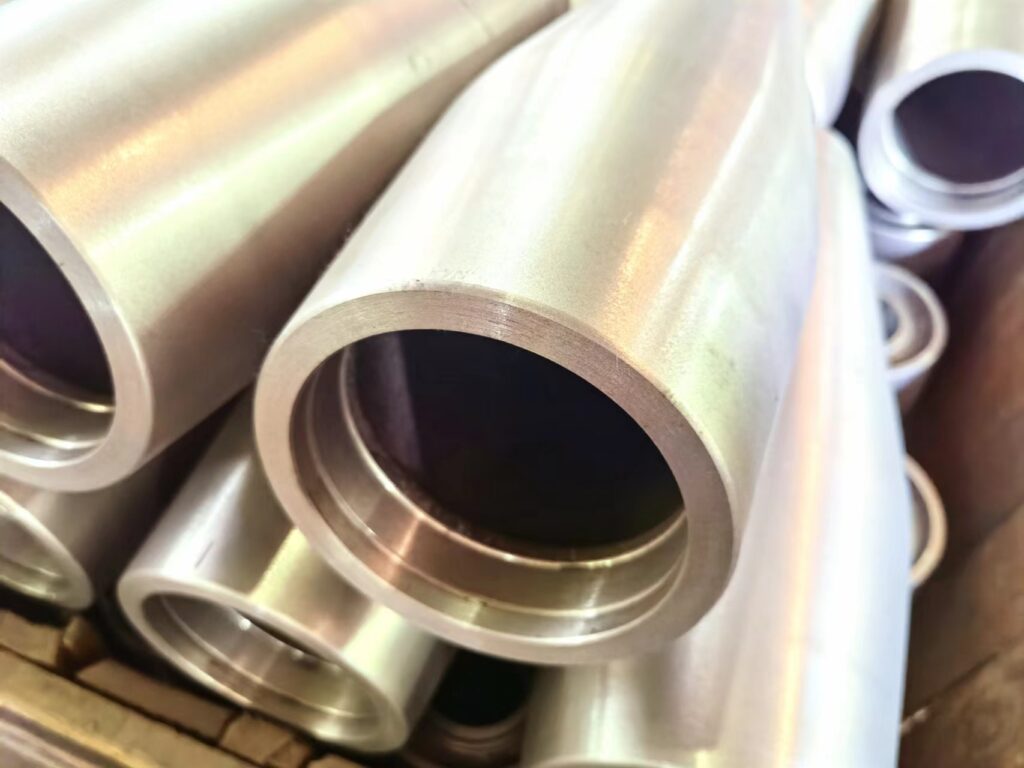
Porosity refers to the presence of small air pockets under the surface of a casting, which can be caused by improper molding or cooling techniques. Porosity is difficult to detect with the naked eye because it is usually too small to be easily detected.
Core marks are small indentations on the surface of the casting, caused by the core material used in the molding process. Core marks are usually visible to the naked eye and can be difficult to remove.
Surface roughness is measured in micro inches or microns and refers to the unevenness of the casting. The smoother the surface finish, the better the casting will look and perform.
Oil/water spots are caused by moisture or oil left on the metal during the machining process. These spots can cause discoloration and affect the reflection of light on the metal.
Finally, discoloration is a change in color due to exposure to certain substances or exposure to certain environments.
8. Toughness
Toughness is a measure of how much pressure a material can withstand without fracturing or cracking. ASTM A48 requires a minimum level of toughness in castings to ensure proper performance in a variety of applications.
The main factors that affect the toughness of a casting are: the material used, the cooling rate, and the surface finish.
The material used for the casting has a significant impact on its overall strength and corrosion resistance.ASTM A48 requires that the casting be made of cast iron, an alloy consisting of iron, carbon and one or more other elements. This type of material is known for its excellent toughness and strength. It is also resistant to wear and tear from heavy loads and impacts.
The cooling rate is another factor that affects the toughness of the casting. Slow cooling rates can lead to internal stresses that reduce the overall strength and durability of the casting, while rapid cooling rates help maintain its structural integrity. ASTM A48 standards require parts to be cooled at least 40°C per hour to ensure optimum performance.
Finally, the surface finish of the casting can also affect its toughness. A smooth surface reduces the risk of cracking and other microscopic defects that can affect the overall strength and performance of the part. ASTM A48 requires a minimum level of roughness for all castings, which helps ensure that they meet the required level of toughness.
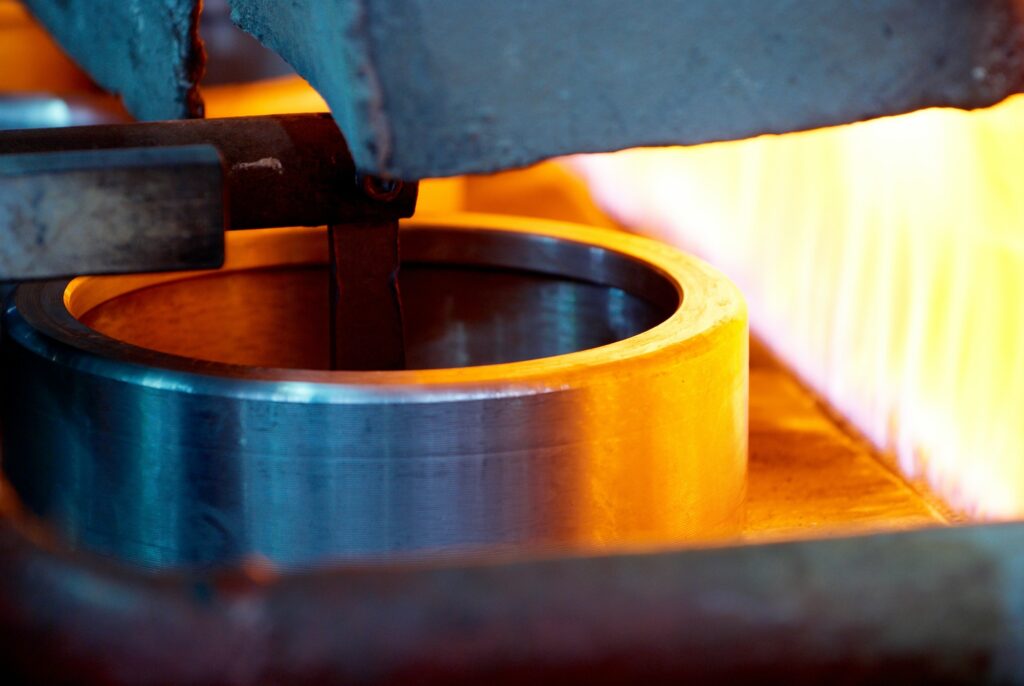
9. Heat Treatments
Heat treating is an important process for improving the performance of castings. ASTM A48 specifies the heat treating procedures that must be followed to ensure proper performance. It is important to understand the factors that must be considered when performing heat treatments.
The first factor to consider is the type of cast iron being used. Different types of cast iron have different heat treatment requirements. For example, ductile iron needs to withstand longer cooling cycles than gray cast iron.
The second factor is the expected result of the heat treatment. Different types of cast iron are often used for different applications and require different heat treatments to achieve the desired results. For example, gray cast iron is often used for engine blocks, which require a different heat treatment than ductile iron used for valves or pipe fittings.
The third factor is the environment in which the heat treatment is performed. Heat treatment must be performed in a controlled environment to ensure proper results. Different environmental conditions have different effects on the results of heat treatment, so it is important to ensure that the temperature, pressure and atmosphere are appropriate for the type of cast iron being used.
The fourth factor is the time-temperature relationship. Different types of cast iron require different time-temperature relationships, which can be determined by consulting the specific heat treatment requirements given in ASTM A48.
Finally, it is important to consider the cooling rate and quenching method of heat treatment. The cooling rate must be appropriate for the type of cast iron being used to prevent cracking. Quenching is a process of rapidly cooling the metal with water or oil, which can be used to improve the strength of certain cast iron alloys.
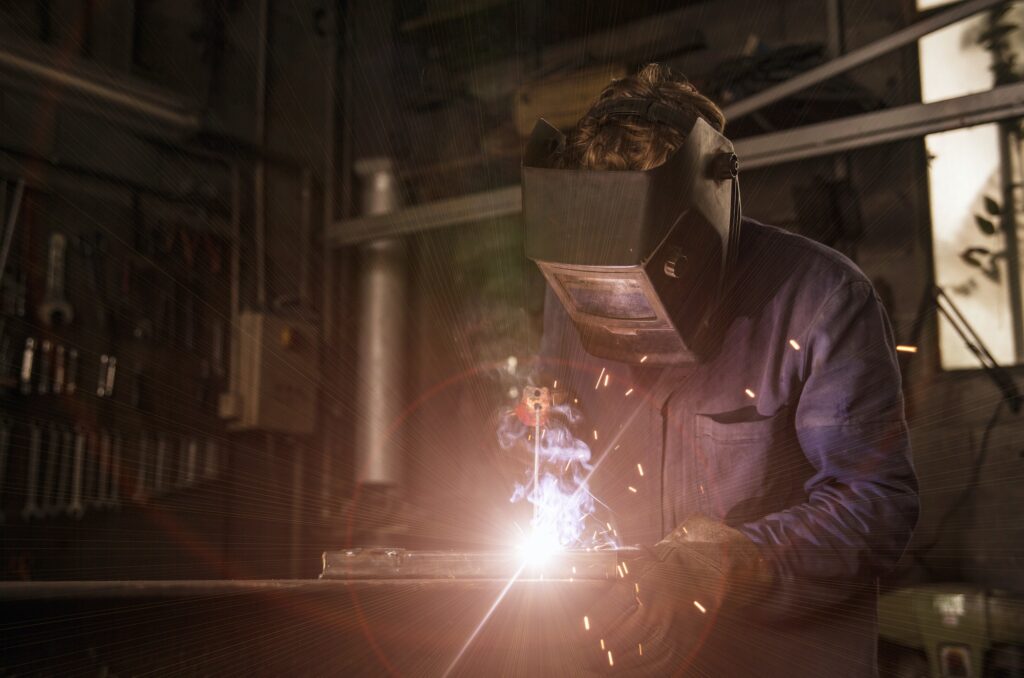
10. Weldability
Weldability is an important factor in determining how easily a casting can be joined to other materials. ASTM A48 requires that castings meet specific weldability requirements so that they can be used in a variety of applications.
The first factor in the solderability requirements is the surface finish of the casting. A smooth surface will allow the solder to adhere better than a rough surface and make for a stronger bond.
The second factor is the composition of the metal used. In castings, different metals have different melting points, so the solder needs to be able to melt at the right temperature and form a strong bond with the metal used.
The third factor is the type of flux used in the soldering process. Fluxes help reduce oxide buildup on the surface of the casting and reduce the surface tension between castings. Flux also helps to keep the solder in a liquid state, thus forming a strong bond.
Finally, the temperature of the soldering process should be carefully monitored. If the temperature is too high, it may cause damage to the metal involved and weaken the bond. On the other hand, if it is too low, it may not be enough to properly melt the solder and form a strong bond.
Conclusion
By understanding these 10 special factors that must be considered when using the ASTM A48 standard, you can ensure that your casting project meets all the necessary requirements. This knowledge will help you create a superior product and reduce costly delays due to non-compliant materials. If you have any questions about this standard, please do not hesitate to contact a qualified professional.
We are Castimoo, a supplier specializing in iron castings. Our gray iron and ductile iron products are exported to countries such as USA, Japan and France, where the quality meets the standards of each country and is unanimously approved by our customers. We are able to advise you on the appropriate products to ensure that your casting project meets all requirements. Feel free to contact us at any time.