Introduction
Iron castings have been used in industrial applications for centuries. They are an important part of many different types of machinery. In this blog post, we will discuss about iron castings and their role in industry. We will cover a variety of topics, including how they are made, what different types are available, the reason of machinery industry use iron castings and how they are used in various industries.
The Process of Making Iron Castings
Iron castings are made by pouring molten metal into a mold or shape, then allowing it to cool and solidify. This process is known as casting and the finished product is an iron casting. The molten metal can be poured into a variety of shapes, allowing for the creation of a wide variety of designs.
This process can be done manually or using specialized machines. Manual casting is accomplished by slowly and methodically pouring the molten metal into a mold or shape. This process ensures the quality and dimensional consistency of the casting.
Machine casting relies on more sophisticated machines to pour the molten metal into the desired shape. These machines measure temperature and pressure to ensure optimal results, resulting in castings with more accurate dimensions and stronger, more durable surfaces.
The final step of the process is to allow the casting to cool completely before it is processed or finished. This allows any shrinkage that may have occurred during the cooling process to be addressed and prevents damage from occurring. Once cooled, the casting can be machined and finished as needed.
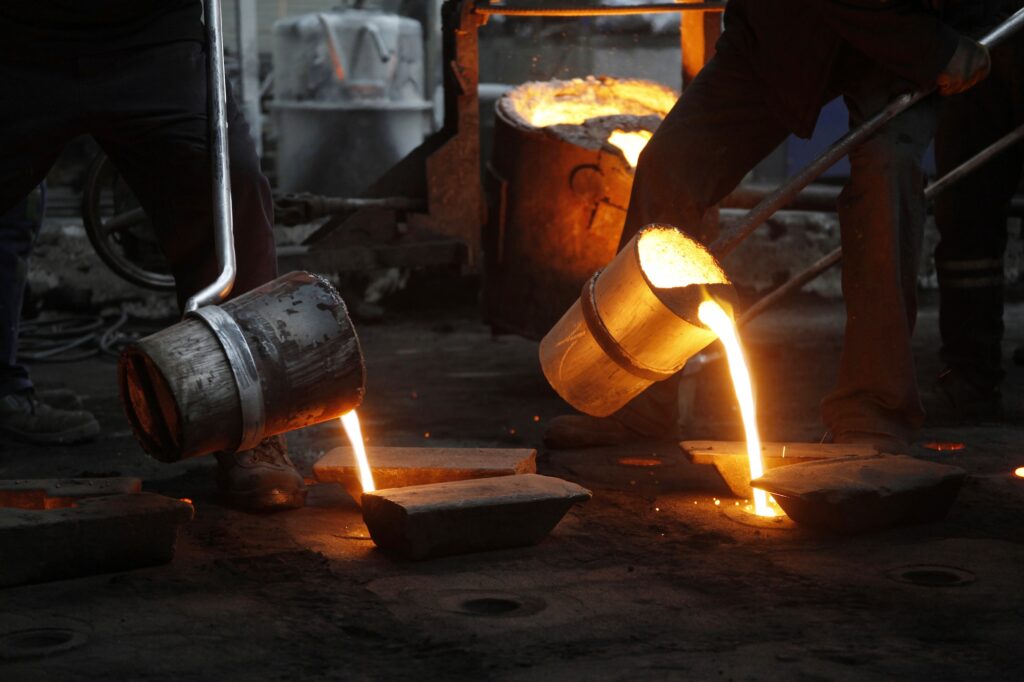
Iron castings are used in many industries, from automotive parts to pipe fittings, and they offer strength and durability unmatched by other materials. The process of manufacturing iron castings is complex and precise, ensuring that the finished product will meet or exceed industry standards. Using the right tools, knowledge and skills, high quality iron castings can be produced.
Types of Iron Castings Available
There are many different types of iron castings available, from simple shapes to complex designs. Common examples include gears, valves, fittings and other mechanical parts. Different methods can be used to customize the final product, making it possible to create unique shapes and sizes.
Iron castings can be made from ductile iron, gray cast iron, and alloy cast iron. Depending on the part you need, different types of casting processes may be best suited to produce the desired result.
Sand casting, for example, is a popular choice for producing parts with intricate details and complex shapes. It involves creating a mold from sand and filling it with molten iron. Once the metal has cooled and solidified, it is removed from the mold in its finished form. This process is commonly used to make large parts for industrial applications, such as turbines or pumps.
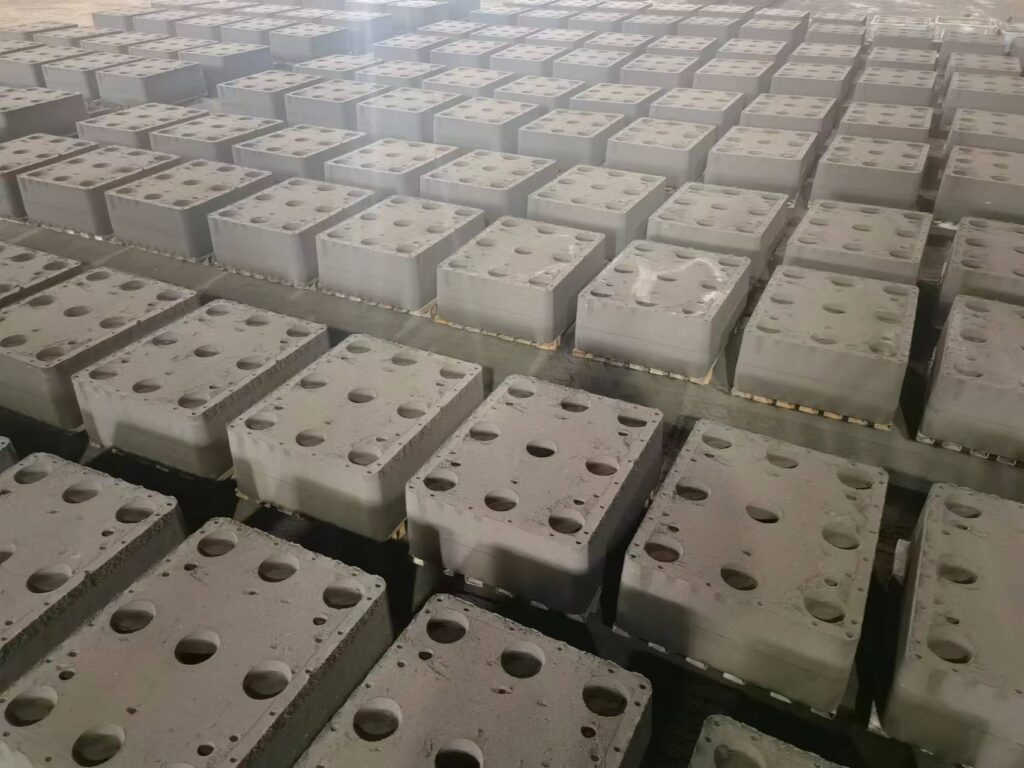
Investment casting is another popular option for producing precision parts and components. It involves creating a wax model of the desired part and then covering it with multiple layers of ceramic slurry. When the slurry is heated, the wax melts and leaves a cavity for the molten metal to be poured into. After cooling, the ceramic mold is broken to reveal the finished part. Investment casting is often used for fine parts, which require a high degree of accuracy and detail.
Centrifugal casting is used to make cylindrical parts that are usually hollow. Molten iron is poured into a rotating mold, and as the mold rotates, a uniform layer of metal is formed around its inner walls. The result is a seamless part that is uniform in thickness throughout. Centrifugal casting is often used to produce pipes, tubes and other structural parts.
No matter what type of iron casting you need, each process has distinct advantages that can help you get the best results for your application. The key is to find the right method for the job. With careful consideration, you can make a casting that meets your exact specifications.
Why Does the Machinery Industry Use Iron Castings?
It is due to the unique properties of iron that make it very suitable for many manufacturing applications. Iron castings are strong but lightweight, highly durable and easy to machine.
In addition, they have excellent corrosion resistance, can withstand a great deal of wear and tear, and can also withstand the stresses of continuous use, which makes them an important component for use in industrial machinery.
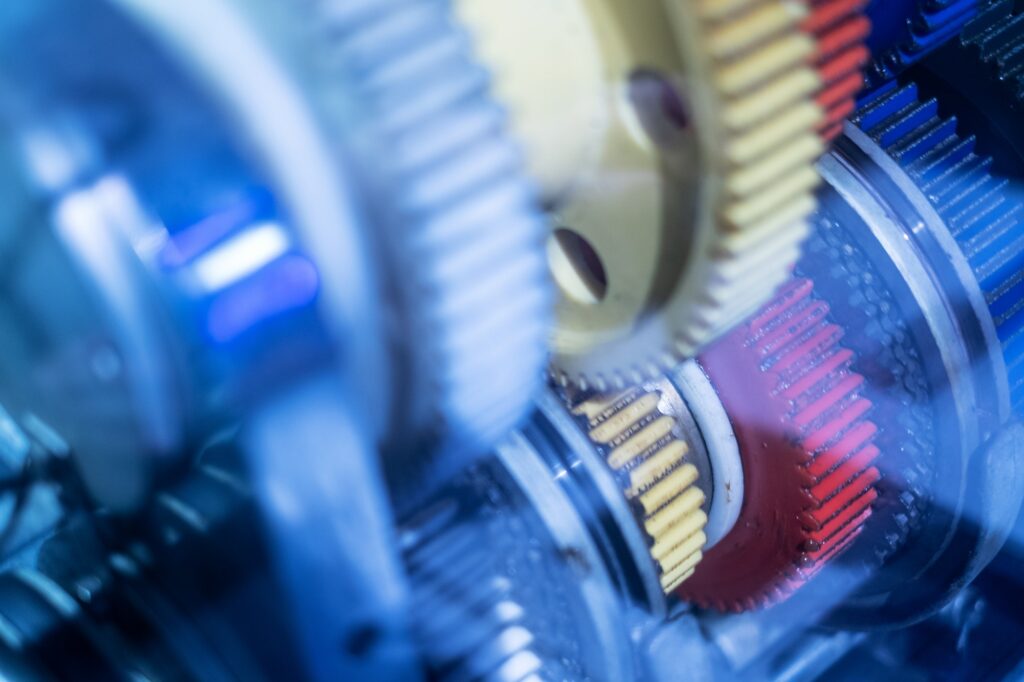
Iron castings also provide a cost-effective solution for many machines and equipment because they can be produced quickly, easily and in large quantities. This makes them ideal for projects with tight deadlines or budgets.
They are relatively easy to maintain and require very little maintenance compared to other materials. Iron castings are the best choice for many types of industrial machinery and equipment because of their versatility, strength, durability and economy. Their use can help companies save money and reduce the need for costly repairs or replacement parts due to wear and tear.
Iron castings are also an environmentally friendly option because they can be recycled and reused. This means that less waste is generated when manufacturing with iron castings, reducing the amount of energy and resources used in production. In addition, iron castings are non-toxic, making them a safer option for use in industrial environments.
Combined with all of these benefits, it is easy to see why iron castings are a popular choice for use in many mechanical industries. They offer a durable, cost-effective solution that can withstand the rigors of constant use without sacrificing performance or reliability. From small components to large projects, iron castings provide the ideal solution for any industrial machine or equipment need.
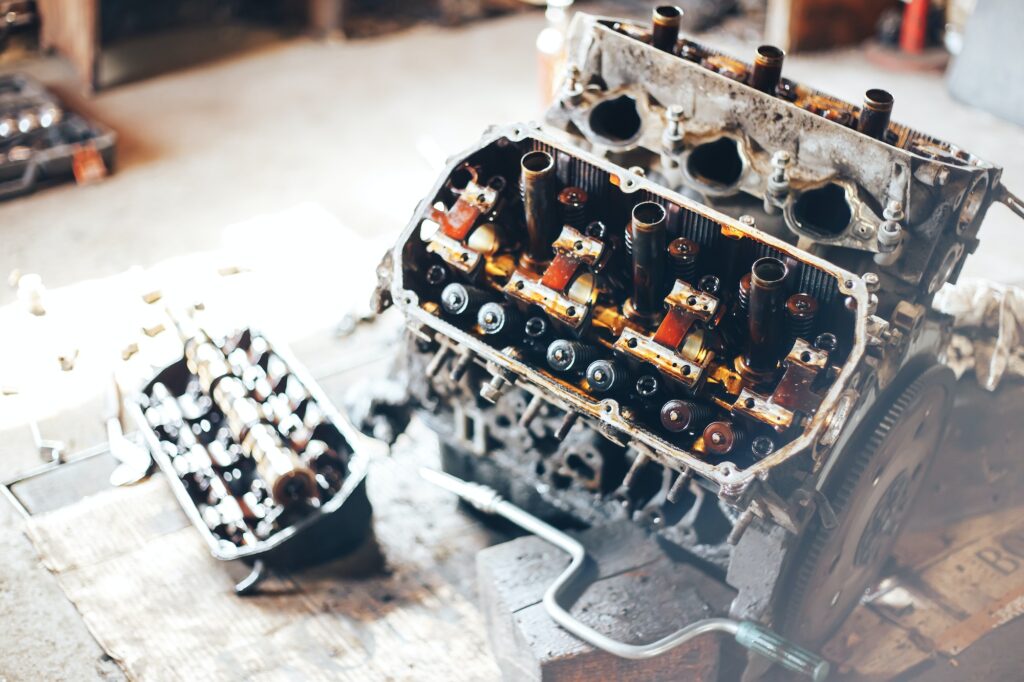
Role in the Automotive Industry
Iron castings are widely used in the automotive industry as components for engines and other mechanical systems. Their strength, durability and corrosion resistance make them ideal for use in cars, trucks and other vehicles.
Iron castings are also used to make structural components such as frames and bumpers that can withstand the rigors of everyday driving. They are even used to produce wheels with intricate designs that have aesthetic appeal and functional value.
The strength and durability of iron castings make them an ideal material for engines, transmissions, steering components and other critical mechanical systems. Their ability to withstand extreme temperatures and stresses allows them to be used in engine and transmission blocks, as well as other high-performance components.
Iron castings are also very resistant to corrosion, making them suitable for use in exposed areas such as exhaust systems. This makes them ideal for vehicles that may be exposed to road salt and other harsh environments.
Overall, iron castings are an important part of the automotive industry. They are often preferred due to their strength and durability, which helps ensure a longer life and better performance of the part.
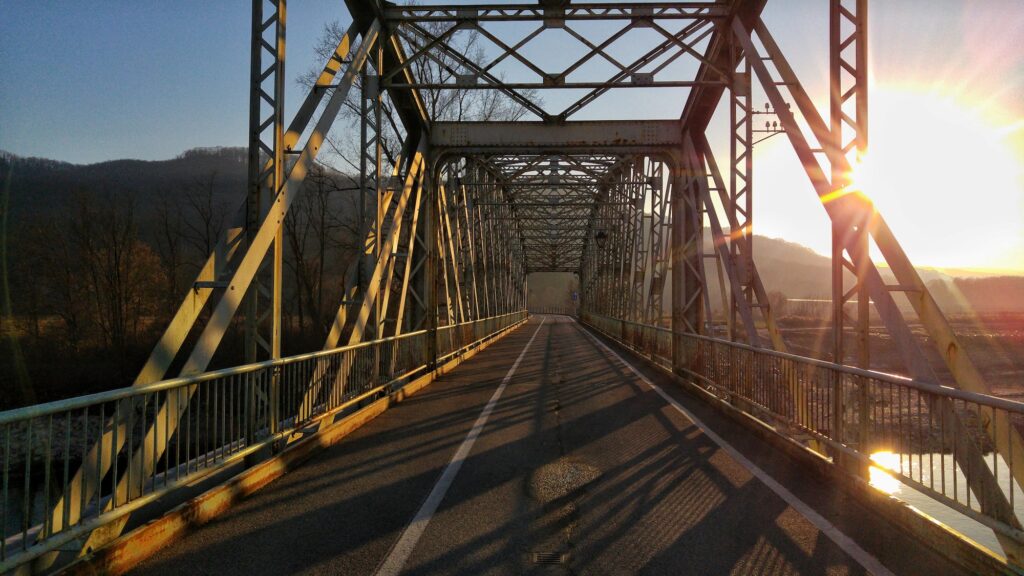
Role in the Construction Industry
Iron castings are used in a variety of ways throughout the construction industry. Common applications include steel reinforcement for strengthening concrete, pipes for plumbing and drainage systems, and even decorative items such as statues, fountains and sculptures.
In addition, iron castings provide a cost-effective solution for producing the large, complex shapes and components often required in the construction process. As an incredibly strong material, they can withstand harsh weather conditions and extreme temperatures, making them perfect for outdoor projects as well.
Iron castings are ideal for the construction industry because of their strength, durability and cost effectiveness. Their applications in commercial and residential environments are diverse and can be used for projects ranging from small repairs to large-scale construction. As a result, iron castings are a valuable resource that helps ensure quality and efficiency.
Role in the Agricultural Machinery
Iron castings can also be found in many different types of agricultural equipment. This includes everything from tractors to harvesters, planters and balers. Using iron castings in agricultural machinery helps ensure that the equipment is strong and durable enough to handle all types of tasks.
Iron castings can also be used to make complex components of precise size and shape, including blades, gears, plows and other agricultural components. These components are designed to withstand the wear and tear of rugged agricultural conditions, making them ideal for this type of machinery.
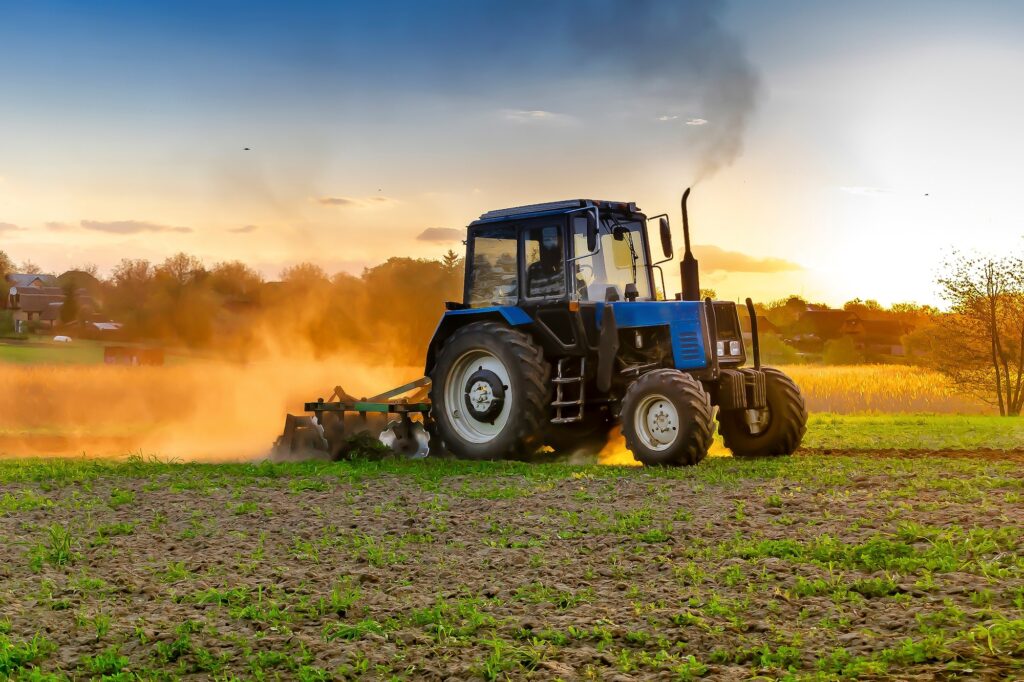
Iron castings can provide just the right amount of strength and durability to keep these complex machines running smoothly without failure. In addition, they are easy to maintain and repair to prevent damage or wear and tear.
Overall, iron castings are a key component of many agricultural machines and equipment. They provide the strength, durability and precision components needed to operate successfully in both rural and urban environments, making them a valuable asset to the agricultural industry.
Role in the Mining Industry
Iron castings play a key role in mining operations for a variety of mechanical engineering components, including drills, crushers and pumps.
The durability of castings allows for use in harsh mining conditions, such as corrosive chemicals and high temperatures. Iron castings are therefore an important component of mining equipment, helping to ensure productivity and safety.
In addition, precision castings provide precise mating parts for assembly, resulting in efficient production processes and increased operational reliability. The complex geometry of iron castings allows for a high degree of accuracy and repeatability, making them ideal for complex mining components.
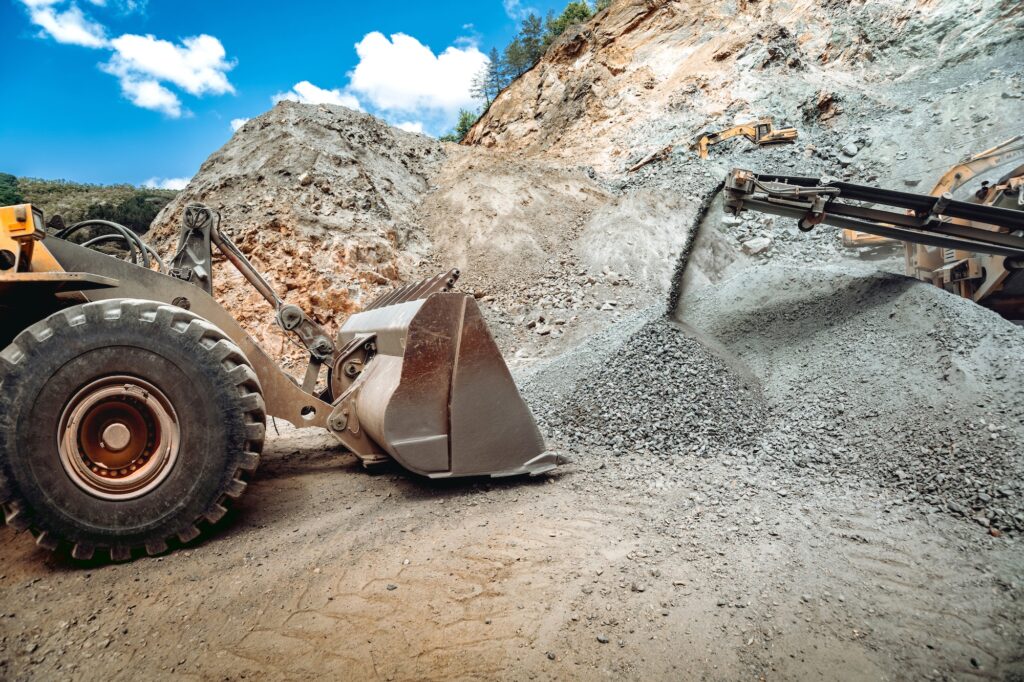
Iron castings are also used to make components for power generation equipment, including turbines and generators. These components require superior strength and reliability in the harsh operating environment of miners.
Iron castings are particularly useful in underground applications where they are used to make lightweight and corrosion resistant components for conveyors, pumps, motors and other equipment. Iron castings are also used in the construction of lifts and skip cars, which are an important part of underground mining operations.
Iron castings are critical to the mining industry and its continued success, providing reliable components that can withstand harsh environments. It ensures reliable performance under challenging conditions. With their high precision and durability, castings contribute to productivity and safety, helping miners achieve their goals safely and efficiently.
Role in the Power Generation and Transmission
Iron castings are often used in a variety of components associated with the production and transmission of electricity, such as turbines, generators and transformers. They can also be found in electric motors, switchgear and other electrical equipment.
Because of their strength, durability and corrosion resistance, iron castings make them ideal for use in harsh environments or where humidity is high. In addition, iron castings provide the precise dimensions needed for tight tolerances, allowing electrical components to fit together tightly and work properly.
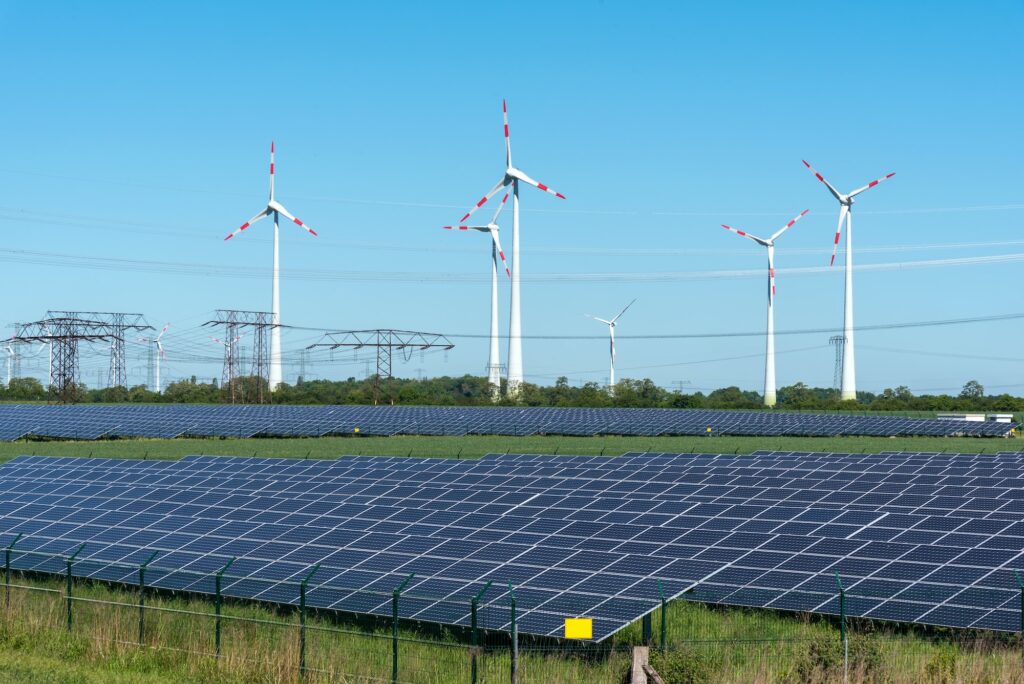
Iron castings are an essential part of the power generation and transmission process, making efficient and reliable power production possible. By making components that can withstand heat, moisture, mechanical stress and corrosion, iron castings help ensure that the electricity we use continues to flow reliably.
Thus, without the strength and reliability of iron castings. The power generation and transmission industry would not be able to operate at its current level of efficiency and reliability. Iron castings allow us to produce and transmit electricity safely, quickly and economically around the world.
Role in the Shipbuilding Industry
Iron castings are also used in the construction of ships, particularly hulls, decks and other structural components. Shipbuilders need these parts to be strong, durable and corrosion resistant to withstand the extreme conditions of the sea.
Iron castings are used as frames and bulkheads to provide strength and stability for large ships. In addition, iron castings are used for deck machinery such as winches, mooring equipment and rudder mounts.
Iron castings also provide the perfect material for propeller shafts, propellers and stern tubes. By using iron castings for these components, shipbuilders are able to ensure that their ships are strong enough to withstand the pressures of the ocean.
Since iron is a relatively inexpensive material compared to other materials, it provides an economical solution. Shipbuilders are able to reduce costs while still providing a high quality product. In addition, iron castings can be customized to meet any specific requirements that shipbuilders may have. This allows them to create parts that meet their exact specifications and needs.
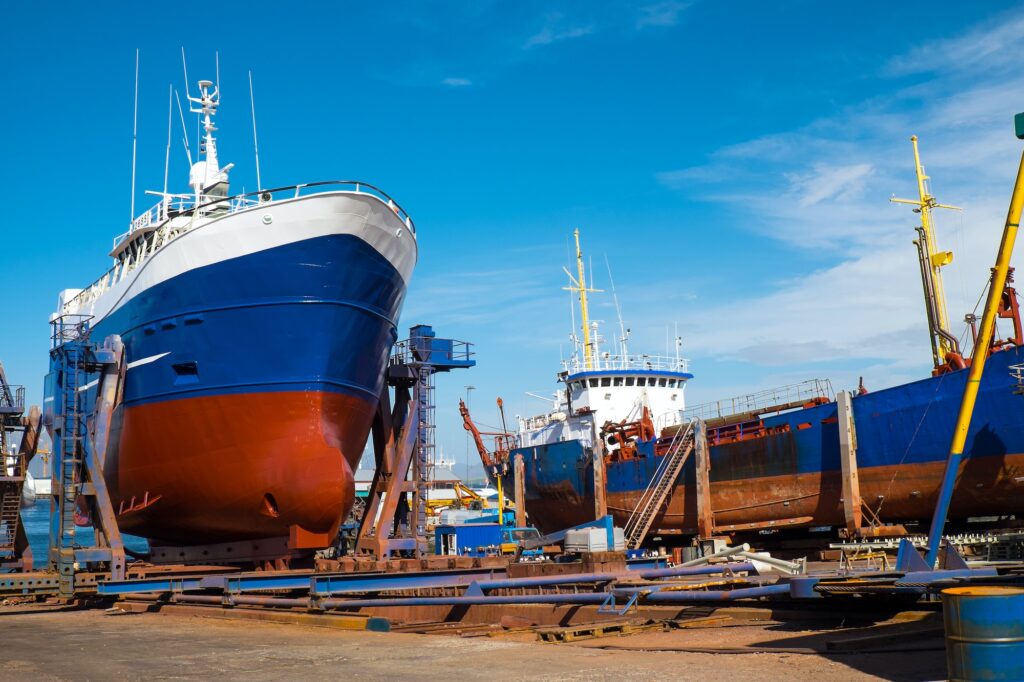
Role in the Aerospace Industry
Iron castings are widely used in the aerospace industry for safety-critical components on aircraft, such as landing gear, brakes and engine components. They help ensure a longer service life and better performance of these components.
The superior strength and durability of iron castings make them ideal for aerospace applications. In addition, the process of metal casting offers a wide range of design possibilities that can be customized to meet specific requirements. This provides engineers with greater flexibility in designing aircraft components, allowing them to produce parts that are optimized in terms of performance, weight, cost and safety.
Iron castings are also known for their high degree of accuracy and repeatability. This makes them ideal for producing complex shapes with tight tolerances, which is critical in the aerospace industry where precision and quality control are essential.
Conclusion
Iron castings are everywhere. They are the foundation of modern industry, helping to produce high-strength, more durable components. They can also be customized into unique shapes and sizes, depending on the application. No matter what kind of machine part you are considering making, iron castings are an integral part.
In short, whether you are making parts for advanced machines or decorating more unique products, iron castings are up to the task. They play an important role in various industries, giving machines a longer life and better performance. We hope this article will help you better understand iron castings and their industrial applications.
Castimoo is a supplier specializing in the production of iron castings and has been deeply engaged in the field of gray cast iron and ductile iron for more than 30 years. Our products are mainly used in industrial equipment and have brought considerable benefits to domestic and foreign customers. We hope our products and services can bring you profits as well. Welcome to contact us at any time.