Introduction
Iron casting production is a complicated and resource-intensive process that needs careful management to ensure adequate output and waste minimization. Iron casting is used in various sectors, including automotive, aerospace, and construction. It is melting iron into cast iron moulds to create the required form. Yet, this process can only be efficient and helpful if handled appropriately.
This blog will look at strategies to maximize efficiency and reduce waste in iron casting production.
What Exactly Is Iron Casting, And How Is It Used In Industries?
Iron castings is pouring molten iron into a cast iron mould to form a particular shape. The cast iron mould, which can be constructed of sand, ceramic, or metal, comprises two sections that combine to produce a hollow filled with molten iron. The cast iron mould is removed once the iron has cooled and hardened, and the cast iron welding rod item is cleaned and polished to the necessary specifications.
Iron casting production has been used for thousands of years to make various things, from simple implements to complicated machinery pieces. It is a very adaptable method capable of producing pieces ranging in size and shape from microscopic and detailed to massive and unwieldy.
Method of Iron Castings
Pattern design, cast iron mould manufacturing, melting and pouring, cooling and solidification, and finishing are all phases of the Iron casting production process.
- Making patterns
The pattern is a copy of the finished product used to make the cast iron casting. It is often constructed of wood, plastic, or metal and is handcrafted by a competent artisan.
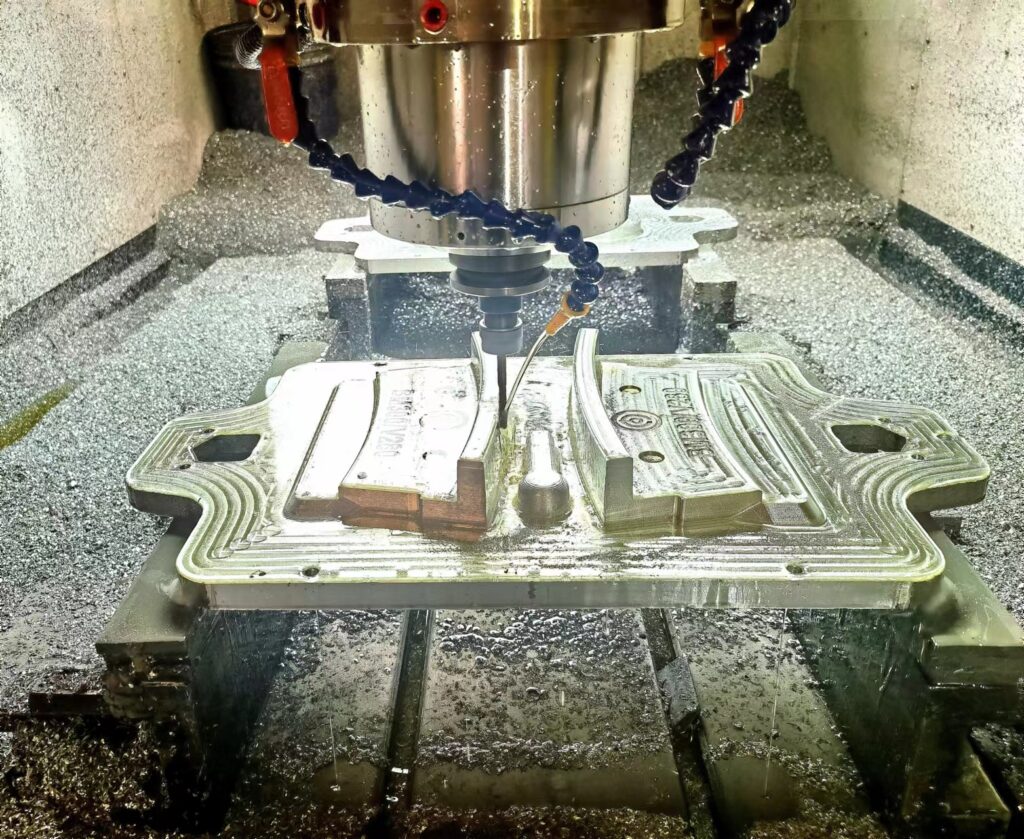
- Making a mould
The mould is created by compressing the design in a container with sand, clay, or metal. The mould is usually made in two halves, separated after packing the sand, and the pattern is removed.
- Pouring and melting
The iron is heated in a furnace and then poured into the mould via a tube known as a sprue. The molten iron fills the mould’s chamber and solidifies as it cools.
- Solidification and cooling
The iron hardens as it cools, taking on the shape of the mould. Cooling is essential for ensuring that the cast iron casting object has the appropriate qualities, such as strength and longevity.
- Finishing
The mould is removed when the iron has been set, and the cast iron welding rod is cleaned and polished to the necessary specifications. Machining, grinding, polishing, and painting are examples of such processes.
Applications of Iron Casting
Iron casting production has several uses in a wide range of industries. Cast iron’s strength, durability, and adaptability make it an excellent material for various items. Following are some examples of Iron casting production applications:
Automotive Industry: Engine blocks, cylinder heads, gearbox cases, suspension components, and brake parts are all produced using iron castings in the automobile industry. To resist the rigors of regular use, these parts must be solid and durable. Cast iron is a common material for engine blocks and other automotive components due to its ability to absorb vibration and minimize noise.
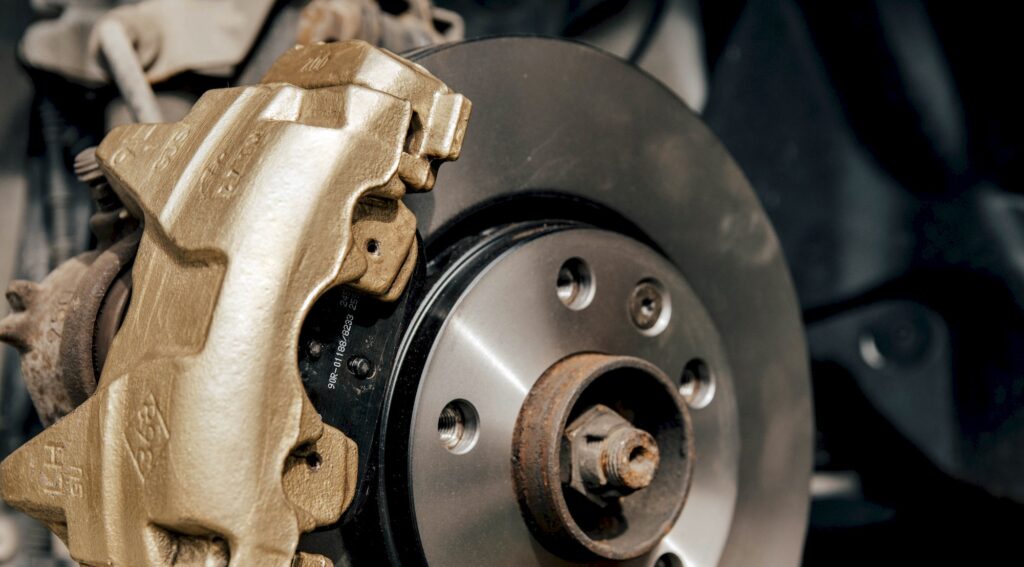
Construction Industry: Cast iron is used to make pipes, fittings, maintenance hole covers, and other components in the construction industry that can handle severe weights and challenging environmental conditions. Cast iron pipes are long-lasting and corrosion-resistant, making them an excellent choice for water and sewage systems. Because of their strength and longevity, cast iron maintenance hole covers are widely used in construction.
Agricultural Industry: Cast iron is widely used in farm machinery such as plows, harrows, and cultivators. Cast iron is an excellent material for agricultural machinery that must survive rugged terrain and abrasive materials due to its capacity to tolerate big weights and harsh weather conditions.
Manufacturing Industry: Cast iron is used in Manufacturing to make machinery components, tools, and equipment that require great precision and accuracy to work effectively. Machine frames, covers, bases, gears, and other precision pieces are cast iron.
Ways to Maximize Efficiency and Reduce Waste in Iron Casting Production
Here are some ways to maximize efficiency and reduce waste in iron casting production.
1. Improve the Casting Design
The casting design is the initial stage in the manufacturing process and considerably influences efficiency and waste savings. Manufacturers can reduce the quantity of material required and waste created by improving the casting design.
Using simulation software to examine the flow of molten iron and detect potential faults is one technique to optimize the casting design. This program can also assist in determining the best location for gating systems and vents to guarantee appropriate filling and solidification.
Another approach would be to adopt lightweight designs that consume less material. Hollow or ribbed portions, for example, can minimize final product weight without sacrificing strength or usefulness. This saves resources and makes the product easier to handle and carry.
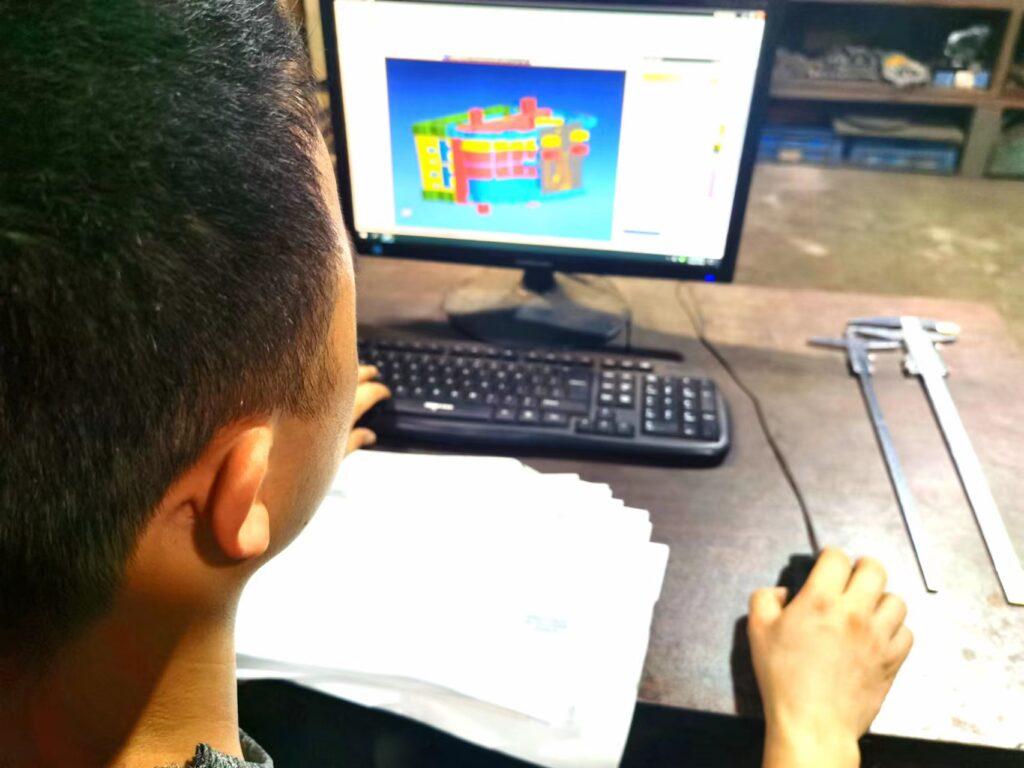
2. Adopt Lean Manufacturing Methodologies
Lean Manufacturing is a manufacturing philosophy focusing on continual improvement and waste reduction. It entails identifying and removing non-value-added tasks and improving material and information flow throughout Manufacturing.
A pull production system, in which items are only created when there is a demand, is one method of implementing lean Manufacturing in iron casting production. This decreases inventory, which may be expensive to keep and manage.
Another approach is to adopt defined work methods to reduce variability and increase efficiency. This involves using visual management tools to track job progress and detect bottlenecks in the manufacturing process.
3. Maximize Energy Efficiency
Iron casting production is an energy-intensive process that can have a substantial environmental impact. Maximizing efficiency decreases greenhouse gas emissions and industrial costs by lowering energy usage.
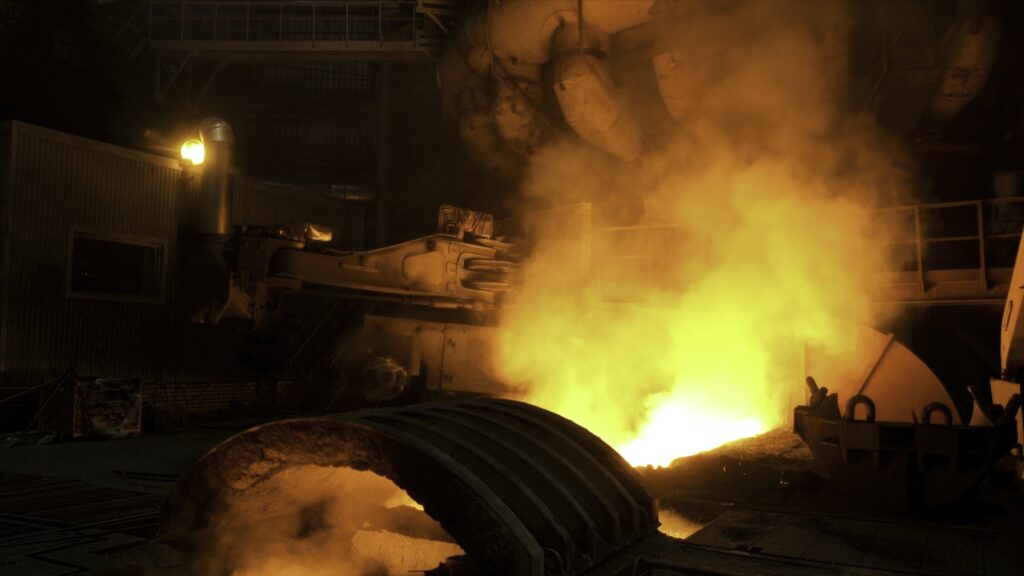
Using electric furnaces instead of gas-fired furnaces is one technique to enhance energy efficiency. Electric furnaces are more energy efficient, need less maintenance, and emit fewer pollutants than gas-fired ones.
Another approach is to install a heat recovery system, which absorbs waste heat from the furnace and utilizes it to pre-heat entering air or water. This minimizes the energy required to heat these materials, potentially resulting in considerable cost savings.
4. Set up Reuse and Recycling Strategies
Waste from iron casting production includes scrap metal, sand, and moulding ingredients. Recycling and reuse initiatives can help minimize waste and save resources.
One method of recycling scrap metal is to melt it down and utilize the molten metal to make new castings. This eliminates waste and conserves resources by minimizing the amount of virgin material required.
Another approach is to repurpose moulding materials such as sand. Manufacturers may minimize the quantity of fresh sand required by treating and reconditioning existing sand, lowering material and disposal costs.
5. Make Use Of Green Sand Moulding
Green sand moulding is a decorative casting technique that employs a sand, clay, and water mixture as the cast iron mould material. It is a low-cost, versatile method extensively utilized in iron casting production.
Green sand moulding has the benefit of being easily recycled and reused. Sand may be reconditioned and reused several times, lowering material and disposal costs.
Another advantage is that green sand cast iron moulds are simple to modify or repair. This decreases the need for new cast iron moulds and the quantity of scrap produced throughout Manufacturing.
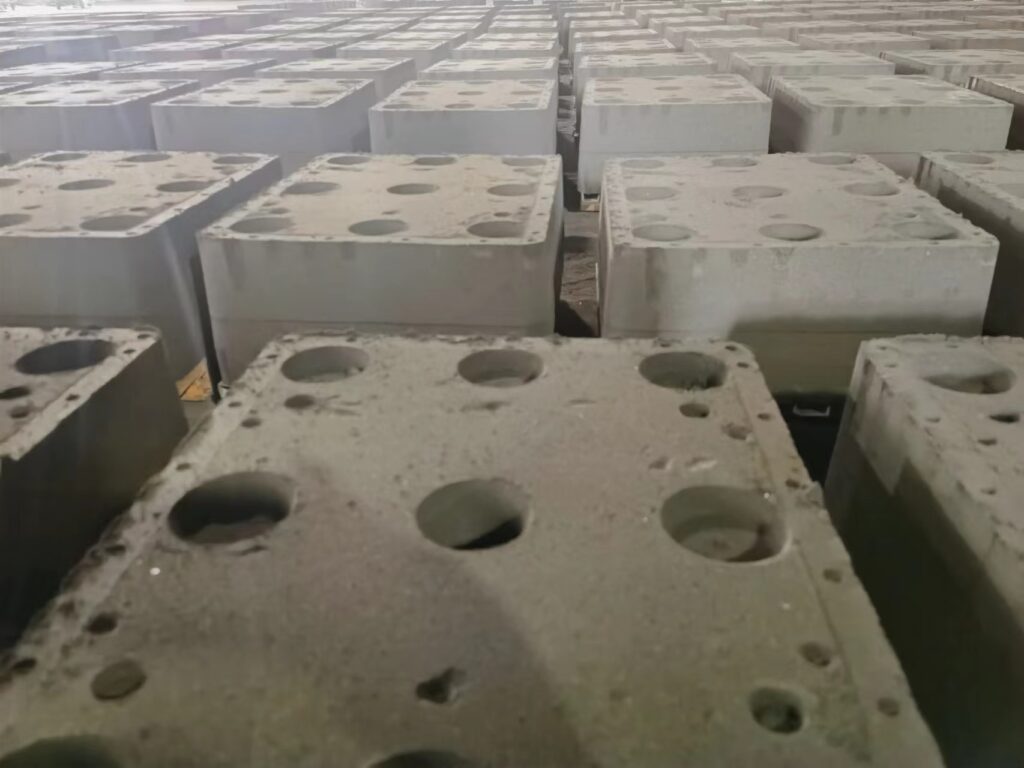
6. Use Quality Control Methods
Quality control procedures are essential in iron casting production to guarantee that the finished product satisfies the needs and specifications of the client. Manufacturers may maximize efficiency and minimize waste by employing efficient quality control systems that reduce scrap and rework.
Using inspection and testing methods throughout the manufacturing process is one technique to adopt quality control measures. Visual inspections, dimensional measurements, and material testing are all performed to confirm that the castings fulfill the specified criteria.
Another approach is implementing a system for tracking faults and determining their fundamental causes. Manufacturers may lower the chance of future errors and enhance overall product quality by identifying and treating the core causes of faults.
7. Introduce Waste Management Strategies
Even with the tremendous efforts to limit waste, some waste is unavoidable in Manufacturing iron castings. Waste management strategies may assist in ensuring that garbage is managed and disposed of in an ecologically friendly way.
Separating and segregating waste streams is one method of implementing waste management strategies. Separating scrap metal, sand, and other materials for recycling or reuse and appropriately disposing of hazardous items fall under this category.
Another approach would be to put a tracking and reporting trash creation and disposal system. This assists manufacturers in identifying areas for improvement and tracking their progress over time.
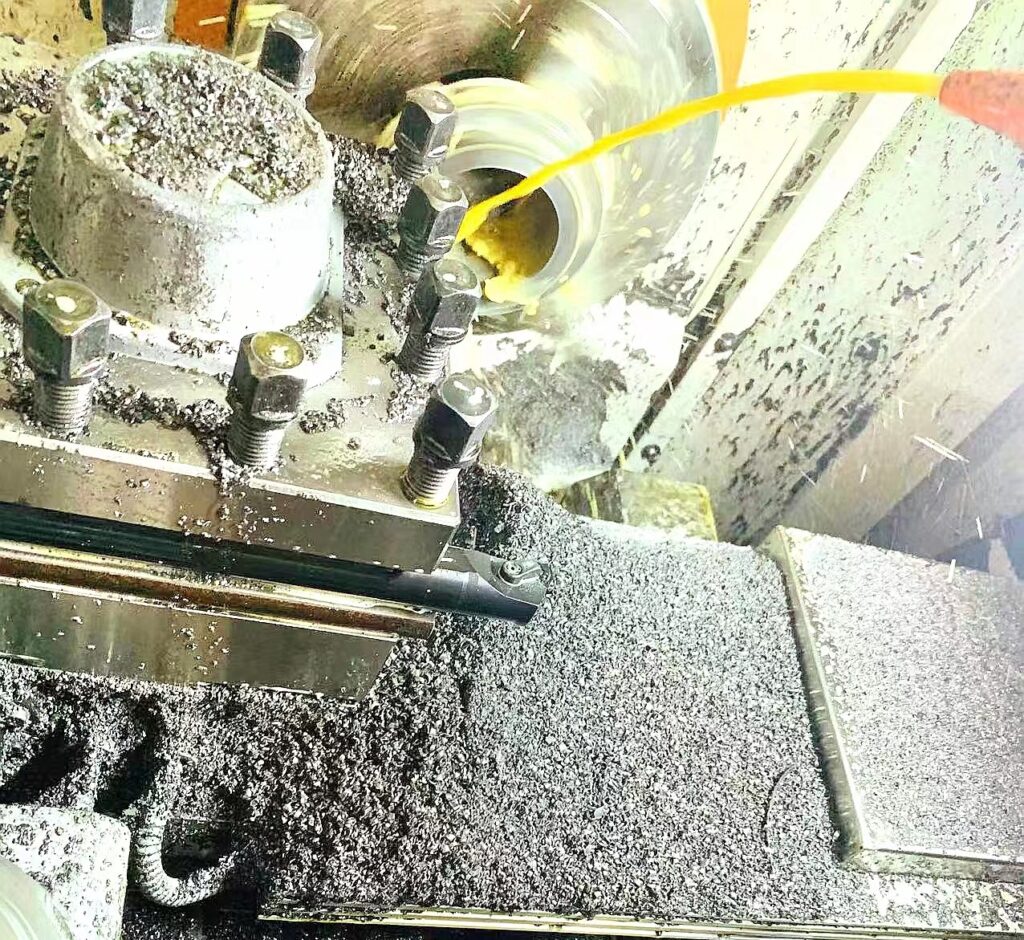
8. Optimization of the Supply Chain
The supply chain can also have an impact on the efficiency of the manufacturing process. Streamlining the supply chain may cut lead times, reduce inventory, and increase production efficiency.
For example, you may collaborate with your suppliers to ensure the timely supply of materials and components required for Manufacturing. You may also use just-in-time (JIT) Manufacturing to decrease inventories and the risk of stockouts or overproduction.
Collaboration with customers and partners to share information and coordinate production schedules is another strategy to optimize the supply chain. This can assist in shortening the lead time, enhance on-time delivery, and boost customer satisfaction.
9. Optimization of Process
Process factors like pouring temperature, pouring rate, and cooling rate can all significantly influence decorative casting quality and production efficiency. Optimizing these characteristics may decrease scrap and rework while increasing overall productivity.
For example, computer simulation tools may forecast solidification behavior and optimize gating and riser design. This can assist in reducing the possibility of flaws such as porosity or shrinkage while also increasing casting yield.
You may also employ automated pouring systems to manage the pouring rate and temperature, which helps increase the casting process’s precision and uniformity. Automatic pouring systems can also help to reduce labor costs and the danger of injuries or accidents.
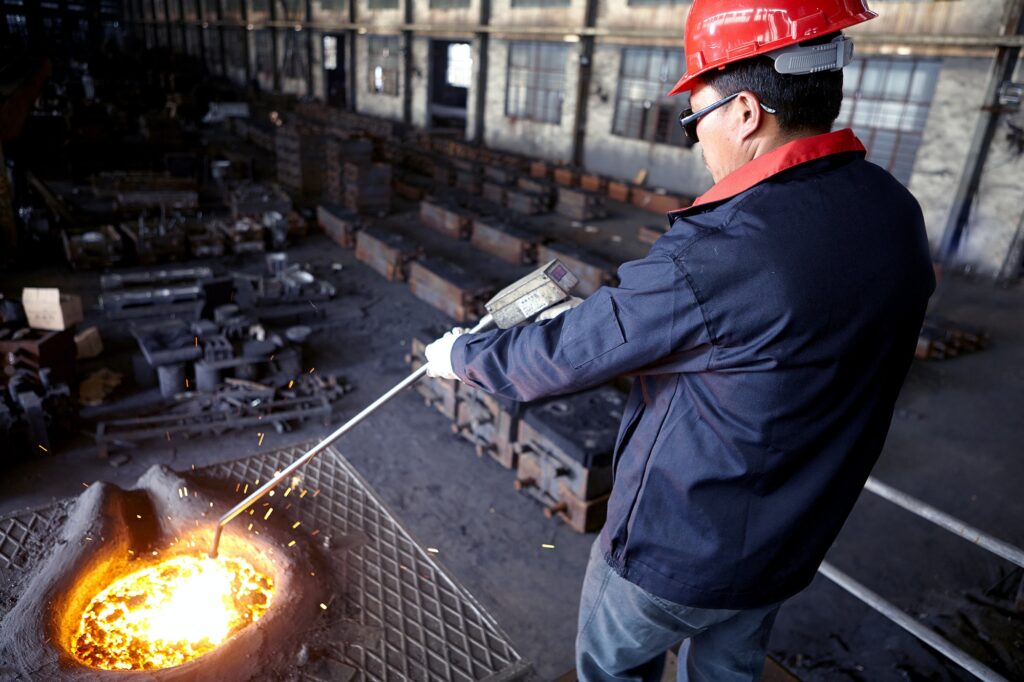
Lean Manufacturing concepts can also be used to optimize the process. Lean Manufacturing is a systematic strategy to reduce waste and increase efficiency. The following are the fundamental principles of Lean Manufacturing:
- Mapping the Value Stream: Find and remove wasteful and value-added operations in the manufacturing process
- Just-in-Time Manufacturing: Make only what is required, when, and in the amount required to reduce inventory and lead times.
- Improving: Continually improve the manufacturing process by incorporating all personnel and making incremental modifications.
You may reduce cycle time, enhance quality, and maximize overall production efficiency using Lean Manufacturing concepts.
10. Make Use of Advanced Materials
Utilizing modern materials in iron casting production can aid in waste reduction and efficiency. In some situations, lightweight materials such as aluminum and magnesium, for example, can be utilized instead of iron. These materials offer a better strength-to-weight ratio, which can minimize material consumption and increase end-product fuel economy.
Another approach would be to employ materials with lower melting temperatures, such as zinc and tin. Because these materials take less energy to melt, they can help to minimize energy usage and greenhouse gas emissions. Furthermore, these materials have a greater recyclability rate, which might help decrease Manufacturing waste.
11. Use Automation
Automation and robots can maximize efficiency and decrease waste in iron-casting operations. Automated pouring systems, for example, can assist assure uniform cast iron mould filling, lowering the possibility of faults and the requirement for rework.
Similarly, robotic machining and finishing can decrease material waste throughout similar procedures. Robots can decrease material removal and manufacture products with greater precision and consistency by carefully regulating the cutting and finishing processes.
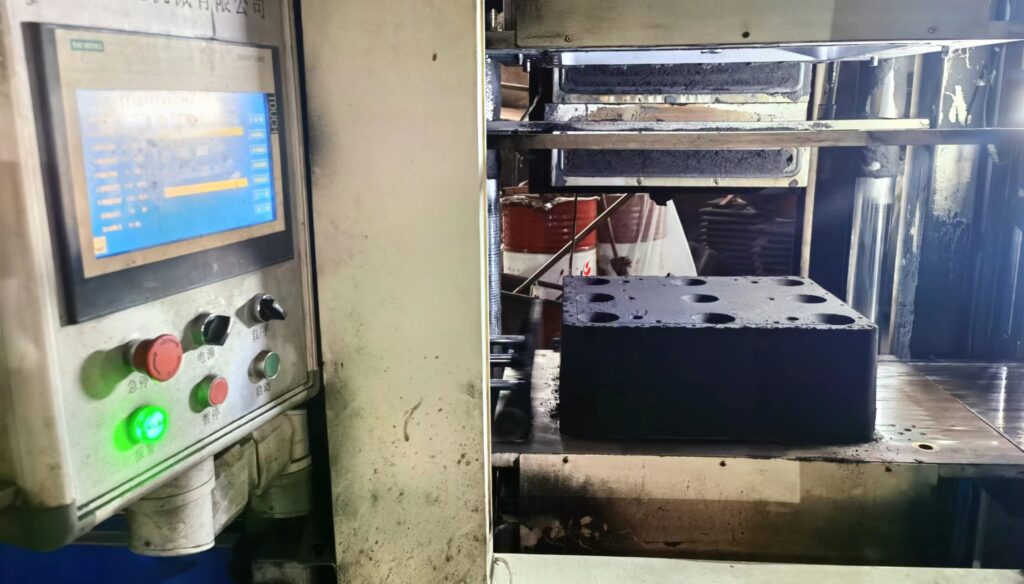
12. Work With Suppliers And Customers
Collaboration with suppliers and consumers may assist manufacturers in reducing waste and increasing efficiency. Working with suppliers, for example, to acquire recycled or sustainable materials can assist in lessening the environmental effect of the manufacturing process.
Similarly, working with consumers to improve the end product’s design may assist in decreasing material usage and waste. Manufacturers may make a product that satisfies client expectations while avoiding waste by understanding the product’s functional requirements and working jointly to optimize the design.
13. Use Sustainable Energy Sources
Iron casting production takes substantial energy to melt the metal and power the machinery. Reducing waste and production costs can be achieved using renewable energy sources like solar, wind, and hydroelectricity.
Iron casting productionfirms may minimize their dependency on fossil fuels and lessen their carbon footprint by adopting renewable energy sources. Moreover, sustainable energy sources can assist in cutting energy prices, resulting in lower production costs and increased profitability.
14. Minimize Packaging Waste
The packing materials needed to transport the castings might generate a lot of trash. Manufacturers can utilize eco-friendly packaging materials such as biodegradable polymers, recycled cardboard, or reusable containers to decrease packaging waste.
Manufacturers can also create a closed-loop packaging system in which packaging materials are collected and reused. This method may considerably minimize waste while also lowering production costs.
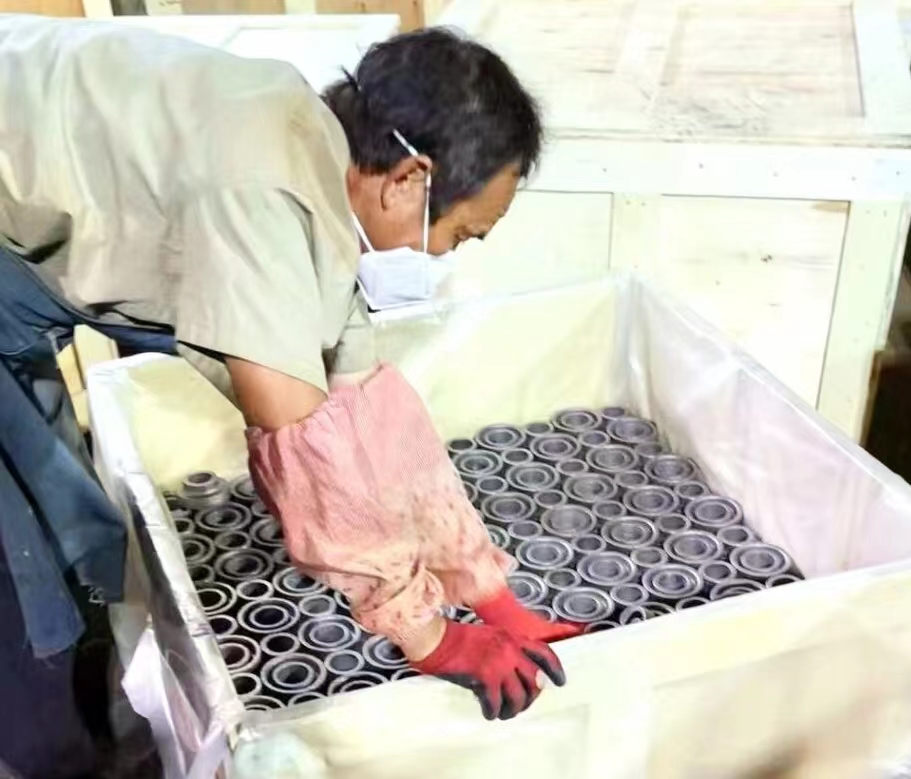
Conclusion
In conclusion, optimizing casting design, implementing lean manufacturing practices, improving energy efficiency, implementing recycling and reuse programs, using green sand moulding, implementing quality control measures, implementing waste management programs, using advanced materials, implementing automation and robotics, and collaborating with suppliers and customers necessitates a holistic approach.
By implementing these tactics, manufacturers may establish a more sustainable and efficient production process that satisfies client expectations while minimizing environmental effects.
Maximizing efficiency and minimizing waste are extremely important to the foundry’s production. In addition, buyers can refer to the ideas listed in this article for comparison and communication during the inspection of iron casting suppliers.
Castimoo is a Chinese supplier with 30 years of experience in iron casting production. It is also the first Chinese supplier to make iron castings by recycling cast iron scrap. We spare no effort in cost reduction and efficiency. The quality of iron casting products is well received by our customers. If you have the need to purchase iron castings, welcome to contact us. We are always here for you.