Introduction
There are many things to consider when packing iron castings for shipping. From ensuring worker safety to making sure the finished product meets standards, there are a number of potential problems that can arise if you’re not careful.
In this blog post, we’ll discuss the 10 most important issues to keep in mind when packing iron castings for shipping. By understanding these potential problems, you can avoid them and ensure that your castings are produced safely and efficiently.
1. Pay attention to safety and protection
Wear the correct protective equipment. Safety should always come first when packing iron castings, so make sure everyone in the area is wearing the proper protective clothing and equipment. This includes gloves, goggles, steel-toed boots and any other items necessary to ensure a safe working environment.
It is not enough to wear the correct equipment, but you should also make sure that the air quality in the work area is also safe. It takes a relatively long time when packing iron castings, and dust and other particles from the castings can be dangerous, so use a proper ventilation system to keep the area clean and comfortable.
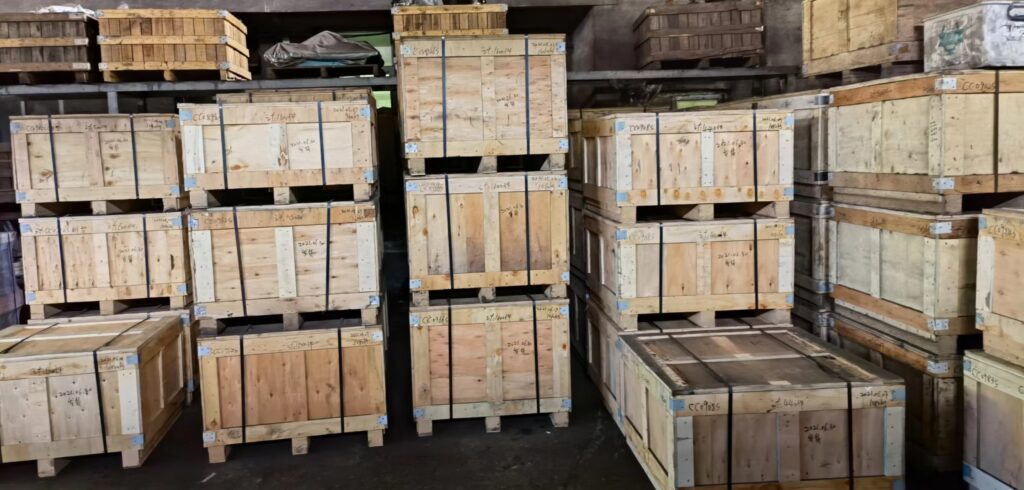
Be aware of your surroundings when packing iron castings. It is important to be aware of any potential hazards in the area. Any working parts should be guarded and properly maintained to ensure safety.
Check for sharp edges. Iron castings often have sharp edges that can cause injury. Use a file or grinder to remove any sharp edges before packing to ensure everyone’s safety.
2. Quality control
I bet you don’t want to be sent back with a batch of poor quality castings.
It goes without saying that it is important to check quality throughout the production process. This can help ensure that all parts produced are manufactured to specification and tolerance levels.
If the iron castings are inspected for quality once again when they are packed in a crate. This is one more quality check, and it is one more guarantee for the iron casting product.
For example, some small burrs on iron casting products are likely to be overlooked. Especially for industries with strict requirements, it will be a huge loss for everyone when these burrs are found after the product is packed and shipped. But then with the management of many quality tests, we will surely be able to find out the problems.
We should never ignore these details, the details make the difference between success and failure. Please make sure to check the quality again before packing to avoid any loss.
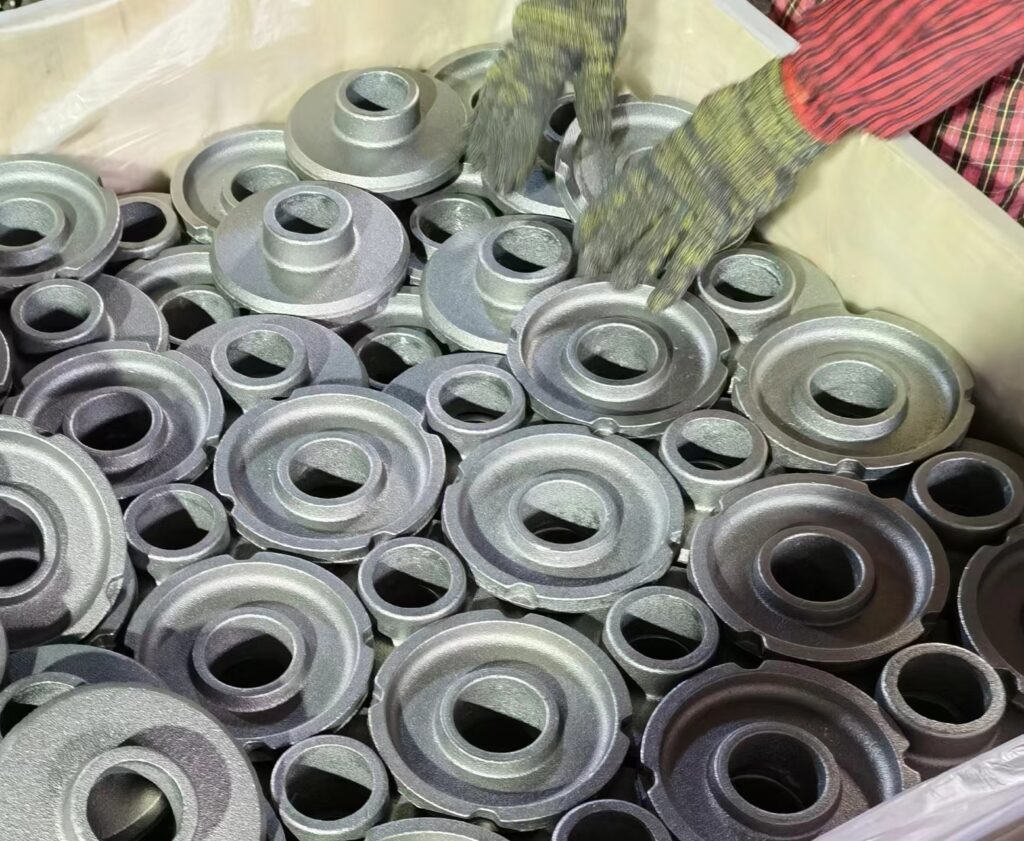
3. Anti-rust treatment
Once the iron casting is exposed to air or contacted with moisture, the rusting speed is very fast. Therefore, before packaging, it is a critical step to prevent rusting of iron casting products.
This usually involves spraying or immersing the product in a rust prevention solution. A rust preventive solution consists of two main components – a protective layer that prevents moisture and air from coming into contact with the casting, and a corrosion inhibitor that protects the metal parts from reacting with oxygen.
Once the rust prevention treatment is applied, it ensures that the product is dry before it is packaged. If this is not the case, then moisture can build up in the package and cause rusting over time.
This can lead to damage to the product and costly repairs to the customer. Therefore, make sure your iron casting products are properly rust-proofed prior to packaging for shipping.
4. Crate material
Generally speaking, when packing iron castings in crates, use wooden boxes. While some other materials, too, can do a good job, wood is the best material when it comes to protecting your iron castings from any potential damage.
For example, if you pack your iron castings in a cardboard box, then you are likely to be left with a damaged or broken item very quickly.
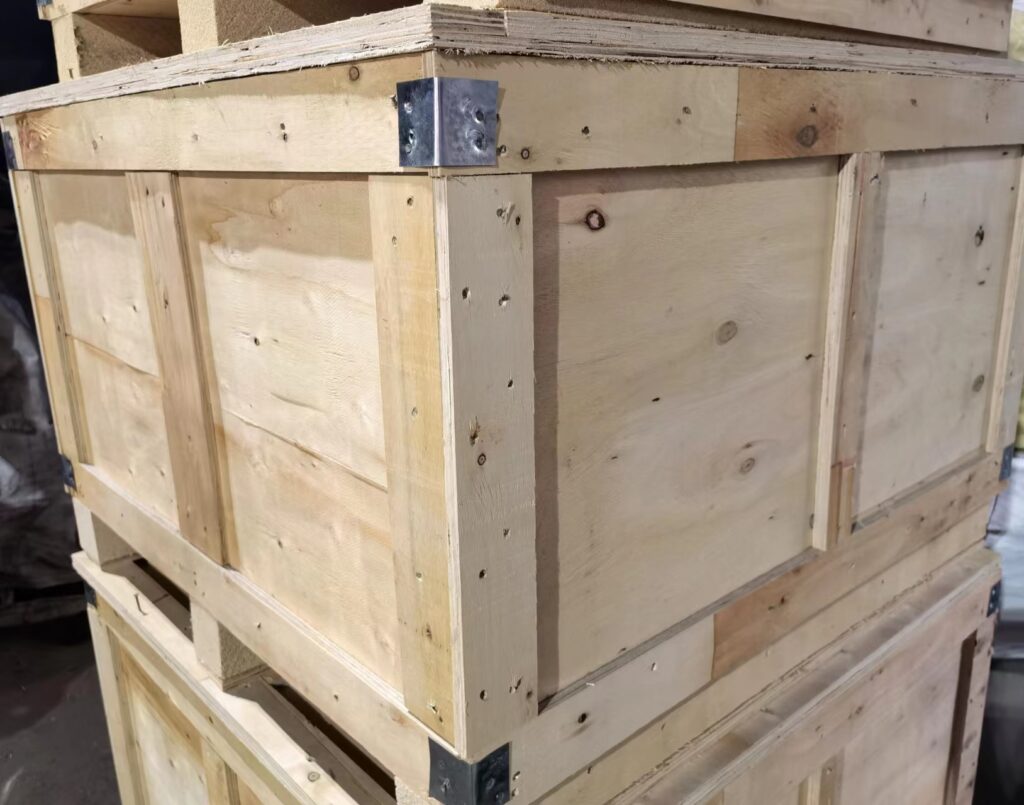
Also, if your supplier is in China and you are importing iron castings from China, you will want to pay special attention to the material used to pack the wooden crates.
If you use solid wood material, you will need to provide proof of fumigation when clearing customs. Generally, we will use export-specific plywood to crate, which can save a lot of unnecessary trouble.
But at the same time, pay attention to the thickness of the plywood. If the thickness is too thin, it is not conducive to protecting the iron casting from any shock that may occur during transportation.
It is wise to make sure you are getting good quality plywood crates to keep your iron castings safe and secure throughout the shipping process.
5. Packaging materials
When packing iron castings, just as important as the crate material is to use the correct padding. You want to make sure you have enough packing material, such as bubble wrap or foam, to protect the iron casting from any bumps or bruises during shipment.
In addition, if the product in the box is any sensitive parts (such as door handles or trim pieces), it is important to make sure there is cushioning material around these parts to prevent them from being damaged.
Not only will this help ensure that your iron castings arrive safely, but it will also ensure that you get a quality product. So don’t skimp on your packaging materials, these are the important details you need to reap the benefits of positive customer feedback.
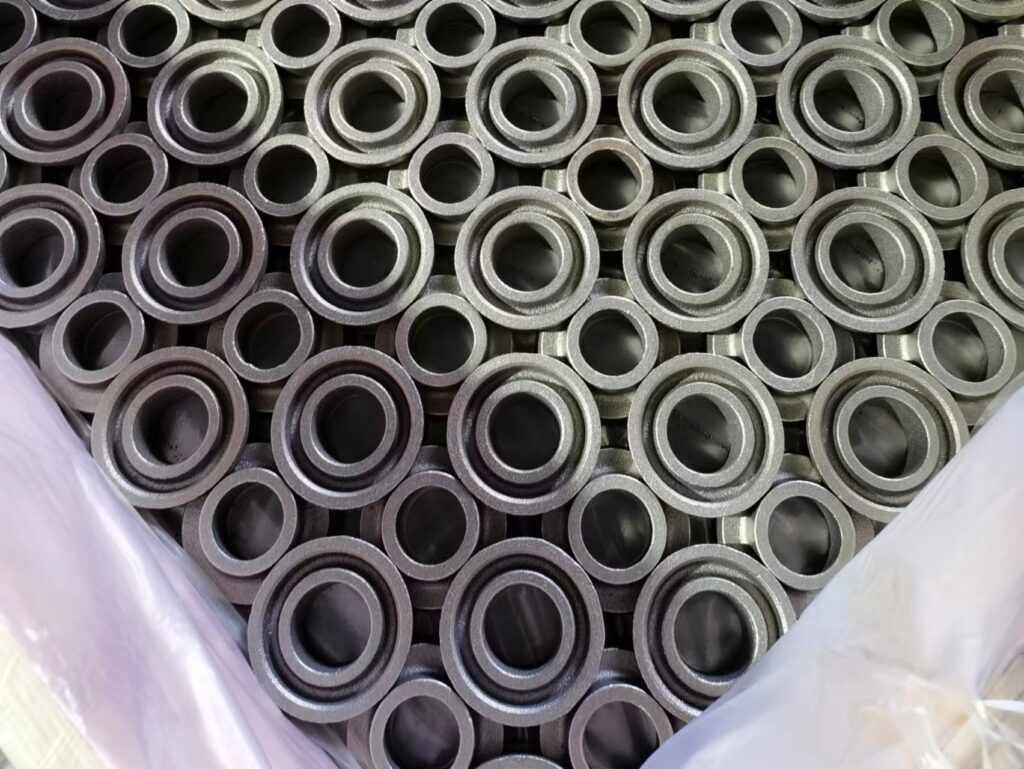
6. Control the weight
When boxing iron castings, remember not to overload the crates. The weight of the package should be kept at a reasonable level, which will allow the operator to be in a safe working environment during the loading and unloading process. If the weight is too heavy, loading and unloading will not be possible and may lead to injuries.
When the weight of the package is kept at a reasonable level, it saves costs associated with transportation and storage. It also helps prevent damage or breakage during shipping, which can lead to costly returns and refunds.
Finally, controlling the weight of the package will ensure that handlers can handle the boxes safely and without putting too much strain on the handling equipment.
7. Loading method
It is also important to consider how each crate is loaded. Packages should be arranged to maximize the protection of the contents without having to leave too much space in the box. Otherwise, vibration and oscillation during transportation may cause damage to the casting.
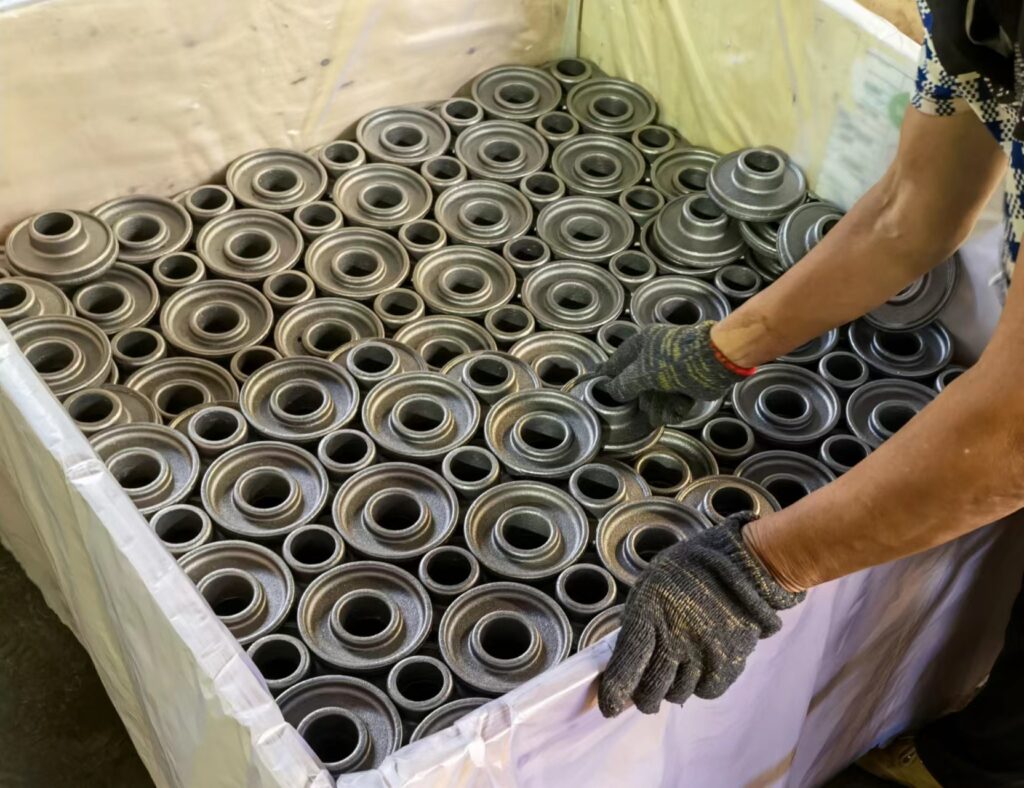
It is important that the loading method is appropriate for the size and weight of the package, as well as its contents. Before loading, calculate the quantity, weight and volume size of the contents to get the most reasonable package.
The most common method of loading is the stacking method, which consists of arranging the parts on their sides and in layers with a sheet between each layer to avoid wear and tear.
This allows for safe and efficient packaging and also ensures that there is enough space between the parts to prevent them from being scratched or broken during transport.
Another method is to use blocking and bracing methods, which involves using blocks or pads between the parts so that they are held securely in place. This prevents them from rubbing against each other during transport.
Whichever loading method is used, it is important to ensure that all parts are adequately protected during transport. Choose a method that provides maximum protection for your specific packaging needs. The correct loading method is the key to successful and safe transportation of iron castings.
8. Labeling
Label the crates clearly and legibly, including product name, model number, quantity, weight, volume, delivery date, etc. Label the crates with the correct information to ensure safe and accurate delivery of your iron casting products.
The label must be clearly and legibly written so that it can be seen from all angles. Proper labeling helps customers identify the items they have ordered and find them quickly in your inventory.
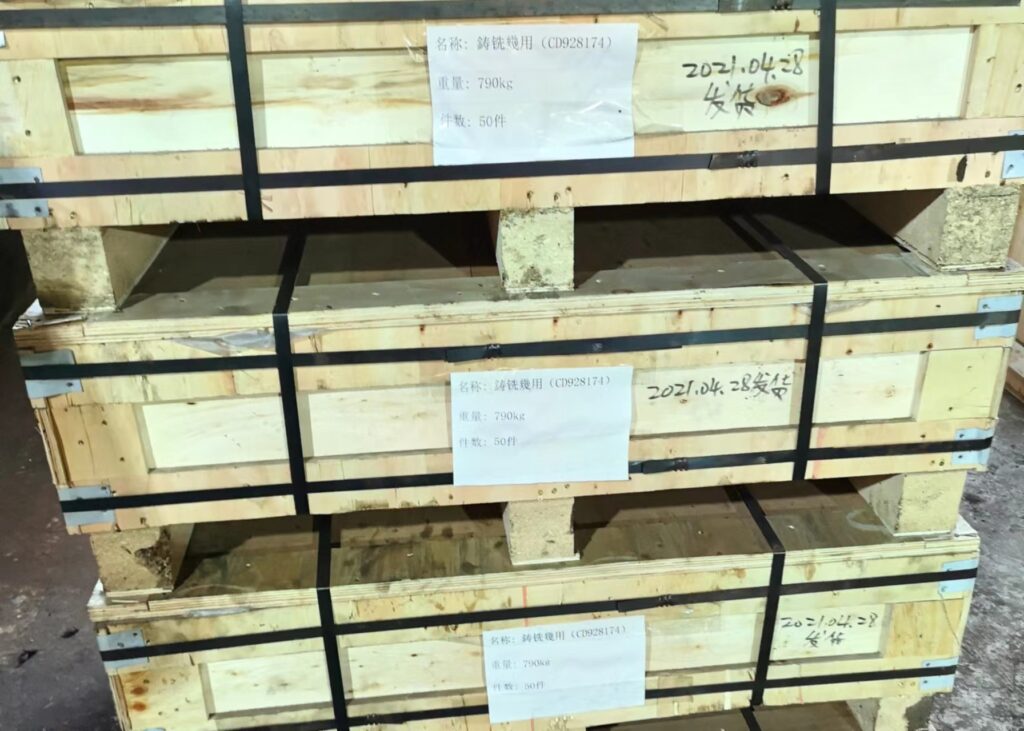
In addition, identifying products with labels makes it easier for your staff to keep track of them and helps reduce the risk of lost or damaged products.
Labels should also include any special instructions related to the castings, such as storage temperature, humidity, and other requirements. This will help ensure that your customers receive the highest quality products while helping you keep them safe during storage and shipping.
Labeling iron castings is a critical step in ensuring that they arrive safely at their destination and in perfect condition. Not only does it provide important information to your customers and employees, but it also ensures that your products remain organized and identifiable throughout the entire production to delivery process.
Proper labeling helps protect the quality of your castings and can help you minimize losses due to shipping errors.
Labeling iron castings may seem like a small detail but it is an important step in helping you maintain a professional image for your business.
9. Fix the crates
Fix the crates before shipping. Once your iron castings are packed and ready to go, make sure you fix the box with tin tape or other fasteners so it won’t open and fall apart due to bumps during shipping. This will prevent any possible damage to the contents of your package.
In addition, you can label the box “Fragile – Handle with Care” so that handlers know to take extra care when handling your shipment. Properly protecting and labeling your package can help ensure that it arrives safely at its destination.
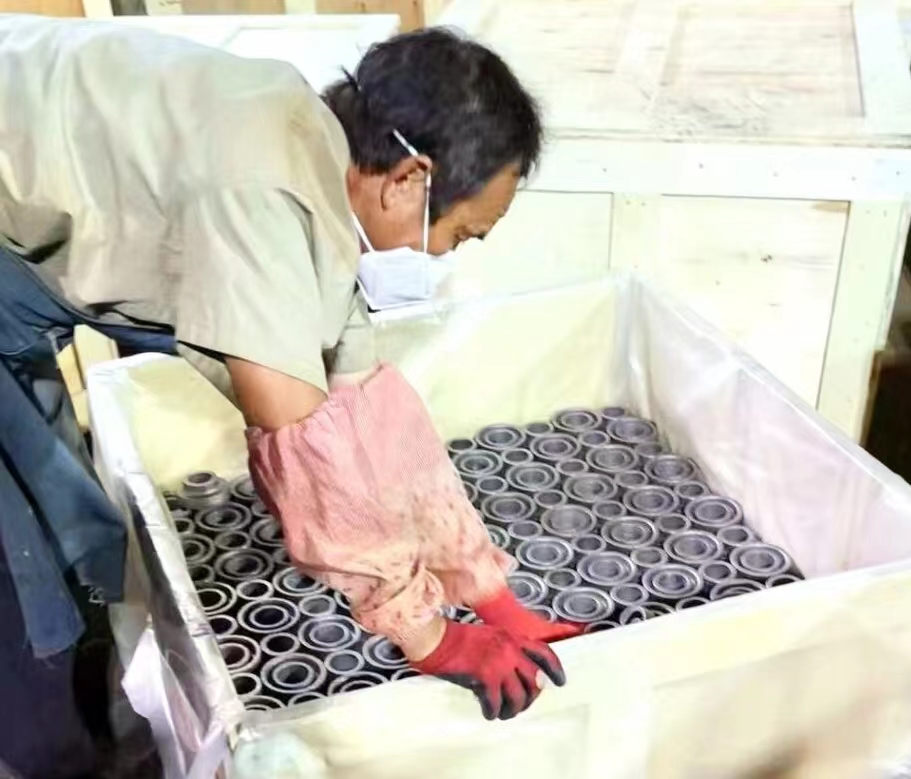
10. Choose a reliable shipping partner
When you pack iron castings for shipment, it is very important to choose a reliable shipping partner. A reliable partner will have experience shipping items of all sizes, shapes and weights. They will be able to provide the right packing materials and techniques to ensure your castings arrive safely at their destination.
A good shipping partner will also have a good customer service team that can address your progress or any questions about your shipment. Choose someone with a proven track record of delivering packages on time and to perfection. If done properly, choosing the right shipping partner can save you a lot of time and money.
Finally, consider adding insurance to your shipment. In the event of a force majeure accident in transit, insurance will give you peace of mind and can compensate you for your losses.
Conclusion
This article summarizes for you 10 issues to keep in mind when packing iron castings. They are attention to safety and security, quality control, anti-rust treatment, crate material, packing materials, weight control, loading method, labeling, fix the crate and choosing a reliable shipping partner.
By following these 10 tips, you can ensure that your iron castings are safely packed in boxes and that they arrive at their destination as scheduled.
We are Castimoo, a supplier specialized in manufacturing iron castings. We have more than 30 years of experience in the field of gray cast iron and ductile iron. We are able to provide you with more professional services and at the same time, we are able to bring more benefits for you.