Introduction
Iron castings are one of the most commonly used components in a wide range of industrial and commercial applications. They are known for their durability, strength and resistance to wear and tear.
However, lead times for iron castings can vary depending on a number of factors.
In this blog post, we will discuss 10 factors that may affect the lead time of iron castings. By understanding these factors, you can smoothly communicate with your suppliers when working on your iron casting project to ensure you get your castings on time.
1. Casting design
The complexity of the casting design can have a significant impact on the lead time required for production.
Complex castings can take longer to design and manufacture due to the intricate details involved, while simple designs are often faster and easier to create.
The simpler and more efficient the design, the less time this can take up front in communicating with suppliers.
If your castings require complex detailing, then allow more time upfront in the design process, with more patience, to ensure the process is accurate and efficient.
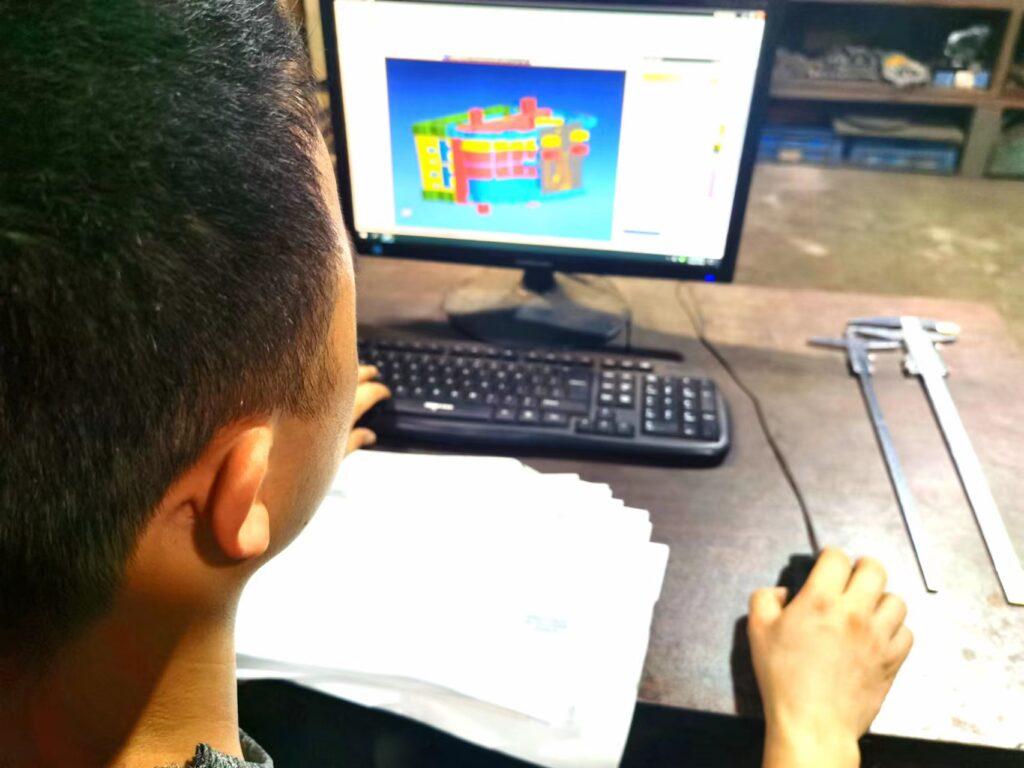
2. Molds and Patterns
After the casting design is determined, custom molds and patterns need to be created for each casting design. These molds and patterns are the primary tools used for iron casting.
They are designed with a specific geometry that matches the desired casting shape, dimensions and tolerances. The design of the mold is critical because it controls how the molten iron flows during the pouring process and how quickly it cools.
The design of the mold also affects the surface finish, dimensions and quality.
Once the molds and patterns are designed, they are usually made of wood, aluminum or foam. The design of the iron casting, the size, and the number of orders are used to determine which material to use for the mold.
The more complex the design of the mold, the longer it will take to make, which may directly affect the lead time of the casting.
Generally speaking, the production time for a pair of molds is about 20 days, if the design is more complex and requires the production of core boxes, it will take another 5-10 days of production time.
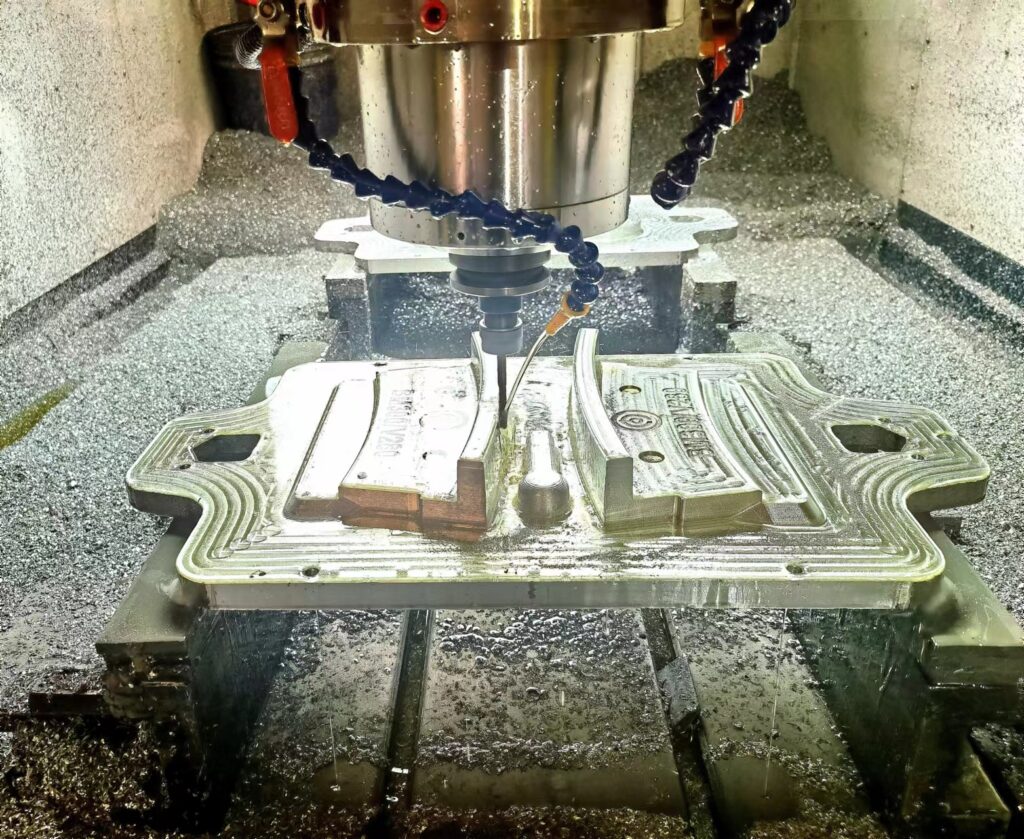
3.Material selection
There are many materials for iron castings, from gray cast iron and ductile iron to malleable cast iron and white cast iron. Each of these materials has different properties that can affect the lead time of iron castings.
Gray cast iron is one of the most common types of iron used to cast objects because of its low cost and ease of casting. It is a relatively brittle material, so it may not be the best choice for objects that require high strength or durability.
Ductile iron is a stronger and more durable option than gray cast iron and is often used for large parts and components.
When choosing a material for your iron castings, it is important to consider the strength and durability needed for the part, but it is especially easy to overlook the lead time needed to produce these parts.
If you’re looking for something with a quick turnaround time, gray cast iron may be your best choice. This is because it requires a smaller variety of elements and is readily available.
However, if you are looking for a more durable material, ductile iron or alloy cast iron is a better choice.
However, because more elements need to be added to create different properties and machinability, these can have a significant impact on the lead time of your iron castings.
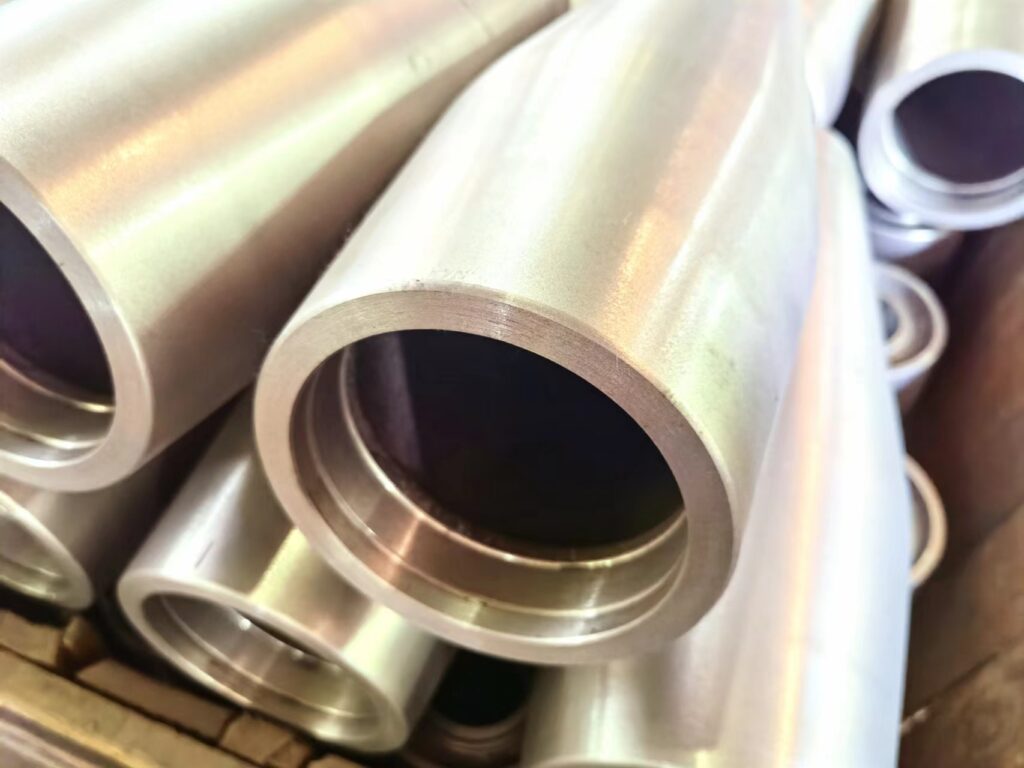
4. Casting process
The casting process you choose will also affect the lead time of your cast iron parts. For example, investment casting has a much longer lead time than sand casting because of the complexity involved in investment casting.
Investment casting is also a more expensive process, but it offers higher accuracy and better quality of cast iron parts. Sand casting is a much simpler process that requires less time, money and energy to complete.
However, since sand castings are usually of lower quality than investment casting, they may require additional machining or other finishing.
Whichever casting process you choose, it is important to ensure that the foundry has sufficient resources and equipment to complete the job in a timely manner.
5. Order quantity
The quantity you need for your order is another factor that may affect the lead time. If you order a large quantity, the foundry may take longer to produce the cast iron parts and fulfill your order.
Likewise, if you order a smaller number of castings, the foundry may be able to complete your order in a shorter period of time.
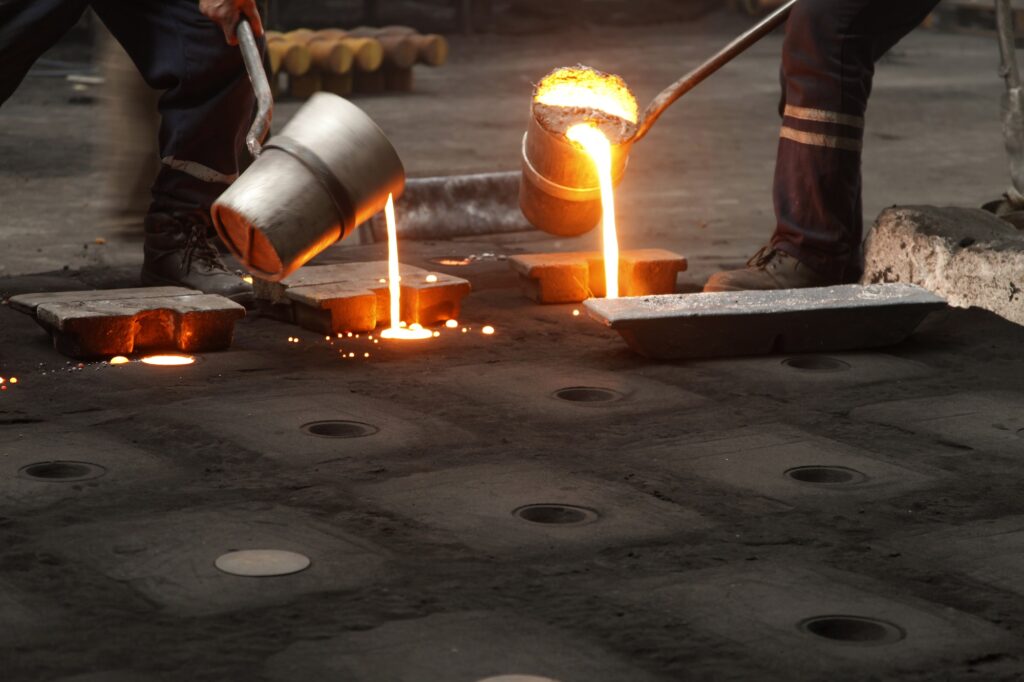
It is important to consider the quantity of your order when developing a lead time plan. When placing an order for iron castings, you must take into account all potential factors that could affect turnaround.
An example is the production scheduling situation. Production scheduling is a key factor in ensuring timely delivery of castings. If the foundry has many production orders, it may take longer to fulfill your order due to the need to prioritize other orders.
Please work friendly with your suppliers, and timely exchange of information is key to ensuring timely delivery. Having a well-thought-out collaboration plan will make your procurement project go smoother.
6. Heat Treatment and Finishing
The heat treatment and finishing operations required by your design will also affect the lead time of your cast iron parts.
Heat treatment is an important step in the production of a part because it imparts strength and hardness properties at a certain temperature. However, the time required for heat treatment must also be taken into account.
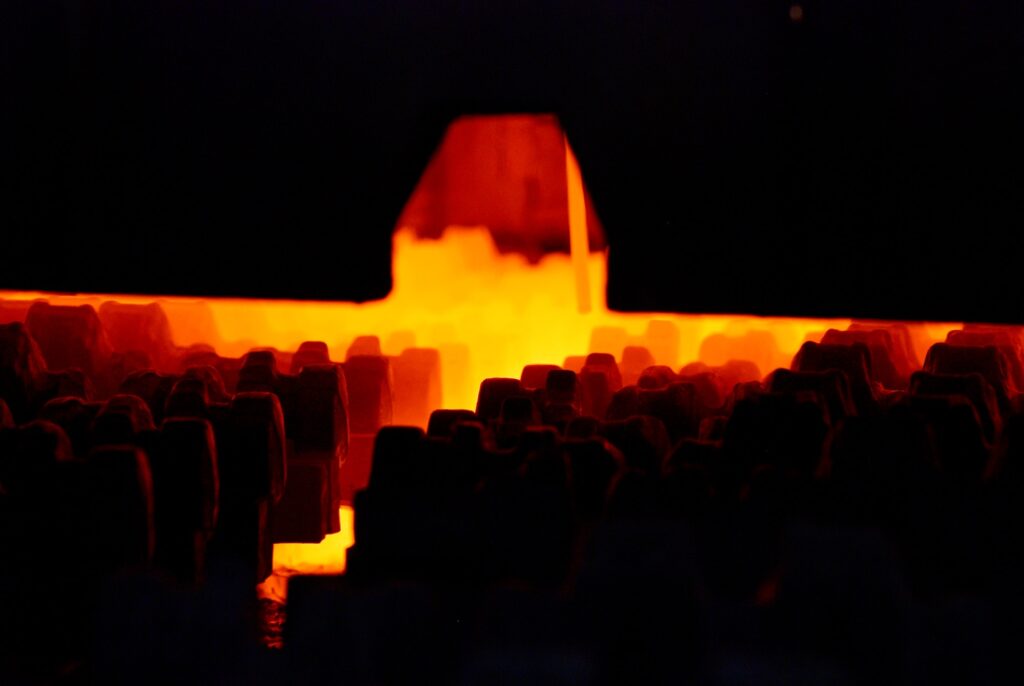
In addition, finishing operations such as machining, grinding, polishing and plating all add to the lead time of the part due to their respective processing times. The increased hardness of heat-treated iron castings makes it necessary to spend more additional time on machining.
If the foundry is not equipped with the appropriate finishing and heat treatment equipment, it is also necessary to take into account the transportation time for outsourcing, as well as the production operation time. This invariably extends the lead time.
7. Inspection and quality control procedures
Quality control procedures must be followed to ensure that the delivered parts meet customer specifications.
This process starts with incoming inspection. All raw materials are inspected for physical, chemical and mechanical properties to ensure compliance with customer requirements.
Iron castings are examined through a microscope to see the graphite form and a spectrometer to check that the composition is up to standard.
A visual inspection of all parts for surface finish, dimensions and defects is also included. After casting, the castings are subjected to various tests such as X-ray testing and ultrasonic testing, which help identify any internal defects.
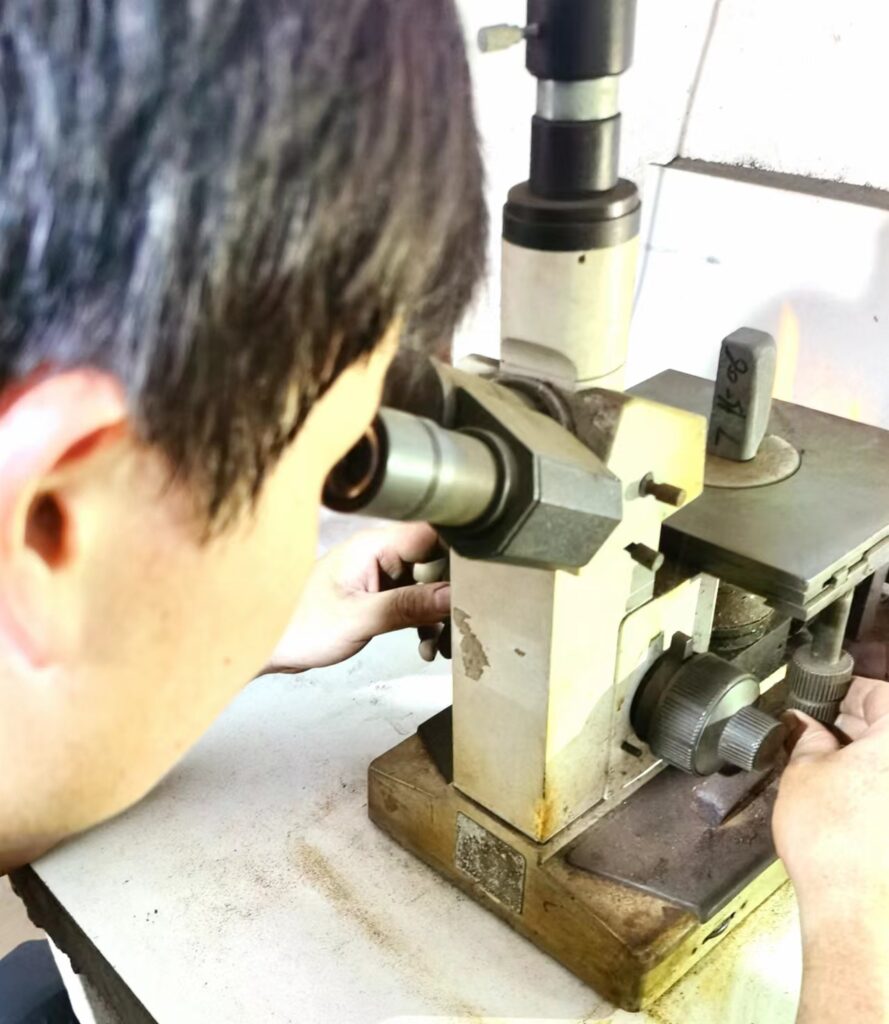
After machining, the castings are checked again for dimensions, surface defects, etc.
Finally, the shipping quantity and packaging specifications are reconfirmed before shipment.
In addition, if there is a requirement for third party inspection, this part is also accounted for.
Through these quality control measures, suppliers ensure that the iron castings delivered to customers meet the requirements in terms of precision and quality in addition to inspection and quality control procedures can avoid errors, rework and shorten the delivery time, please communicate with the supplier to do a good job of quality control system.
8. Logistics and shipping
Depending on your location, the delivery route may vary and also affect the lead time. Local manufacturers are usually better able to deliver iron castings on time, as they may have more efficient delivery routes than international suppliers.
But there are many factors to consider when a project is underway. International suppliers are not as good as local manufacturers in terms of location, but they are still very advantageous when you consider the overall cost.
If you want to import iron castings from China (and of course I highly recommend you do so), you need to take into account the time of transportation by sea.
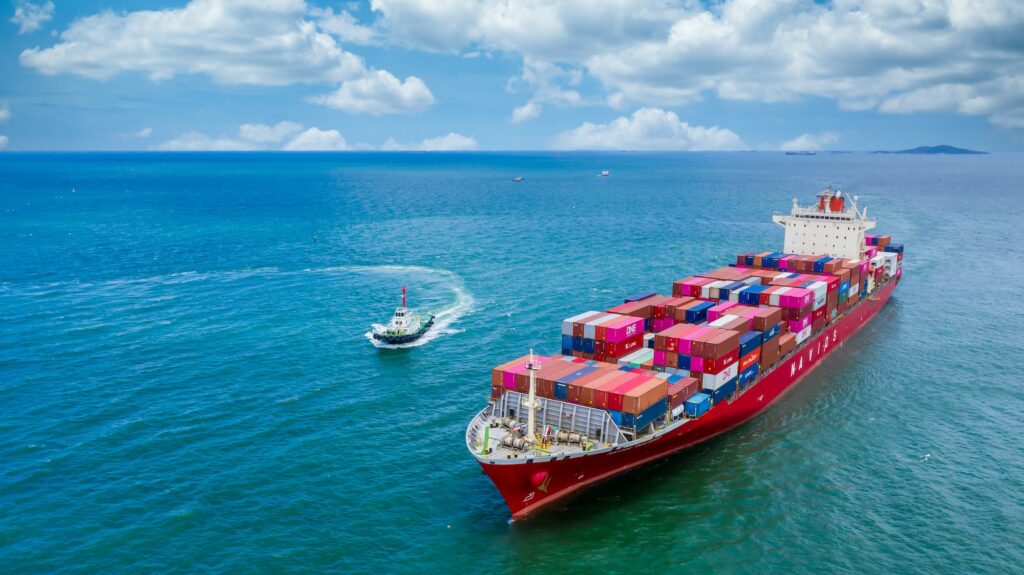
Especially during the epidemic, it was not uncommon to see delays in ship departures due to port blockages. But with the liberalization of China, the sea transport will also return to normal.
Of course, logistics also refers to the mode of transport used. For example, you can also transport cross-country by air.
But this is only suitable for small quantities of lighter samples. In the case of heavier weight and larger volume of iron castings, air transport can shorten the time but is very expensive.
Therefore, it is important to factor logistics into your project’s timeline before choosing who to buy from.
9. Customs clearance
When exporting from China, you may encounter customs checks during customs clearance. If you encounter inspection, everything is normal and you need to wait for 3-5 days more.
When importing iron castings, it is important to know how long it takes to clear customs. The length of this process depends on the country’s regulations and the type of imported product.
As a rule, customs clearance adds about one to two weeks to the delivery time of the goods.
During customs clearance, please prepare all documents in advance to ensure smooth and efficient customs clearance and faster delivery of goods.
10. Finding suppliers
There are a total of 9 factors affecting the lead time of iron castings mentioned above. These 9 factors are the time to be taken into account in the whole process from production to receipt of goods by the manufacturer.
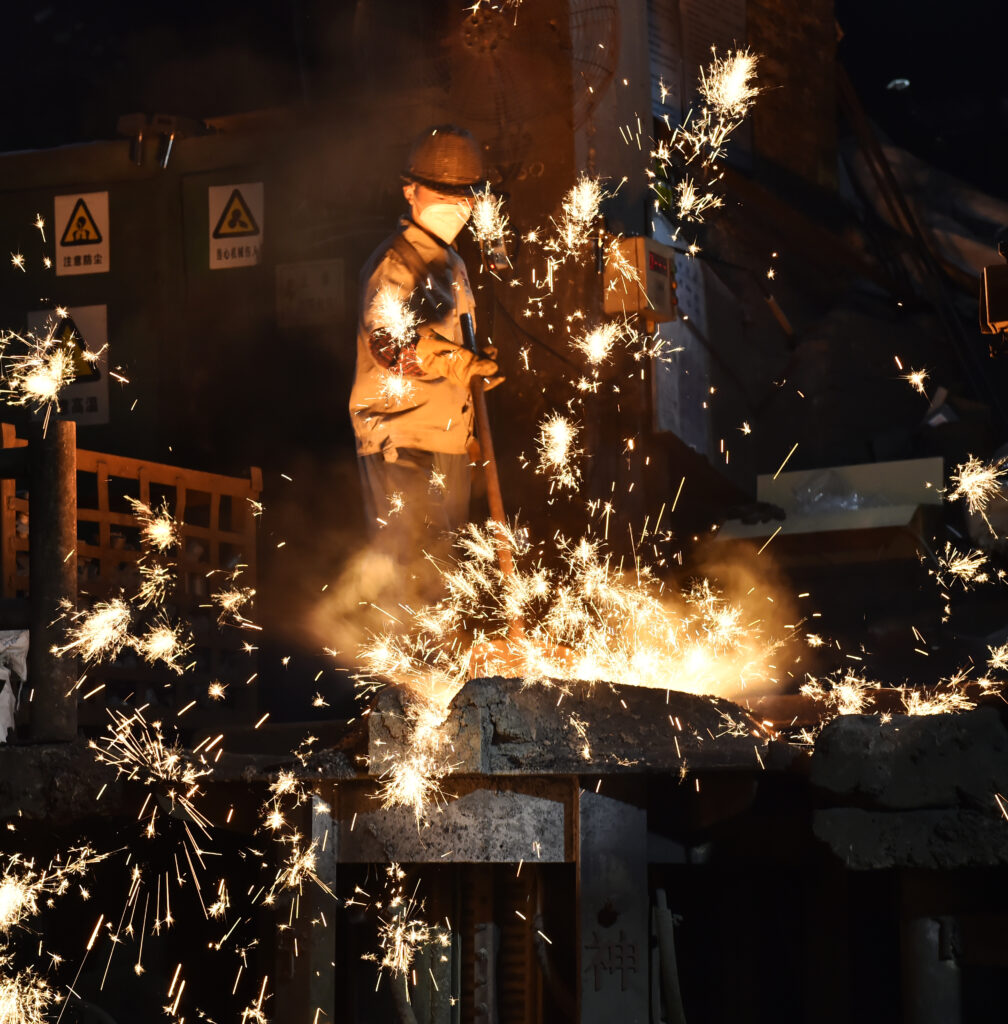
But before that, how to find the right supplier, which is the most important work of the buyer, but also need to spend the most time and effort link.
A quality supplier can provide quality iron castings and meet the delivery time requirements.
Finding a suitable supplier requires the buyer to conduct market research, analyze potential suppliers, compare prices, communicate and negotiate, and check credit ratings.
This series of work can take several months or even longer to carry out, which very much tests a buyer’s patience and ability.
Conclusion
By understanding these 10 factors that affect the lead time of iron casting, you will be able to learn more details when working with suppliers and ensure timely delivery of iron casting products to carry out your projects more efficiently.
Here’s the point, you’re in luck if you’re reading this article.
We are Castimoo, an iron casting supplier from China. We specialize in designing, producing and selling gray cast iron and ductile iron products for you, and have been deeply engaged in this business for 30 years.
Besides being well received by customers in China, our iron casting products are also exported to the United States, Japan, France and other countries, and are also well accepted by overseas customers.
If you need to purchase iron castings for your project, please feel free to contact us. We hope that our products and services can bring you greater profits.
One Response