Introduction
Designing a casting system for iron castings can be a complex process. There are many factors to consider, such as the type of metal being cast, the size and shape of the casting, and the required production speed.
In this blog post, we will discuss 10 issues that should be considered when designing a casting system for iron castings. By understanding these factors, you can create an efficient system that produces high quality castings.
1. Mold material
The type of mold material you choose will determine the quality and strength of your castings.
Different metals require specific mold materials that can withstand the temperature and pressure of the pouring process.
You should also consider the end application of the casting, as some mold materials are better suited for certain applications than others.
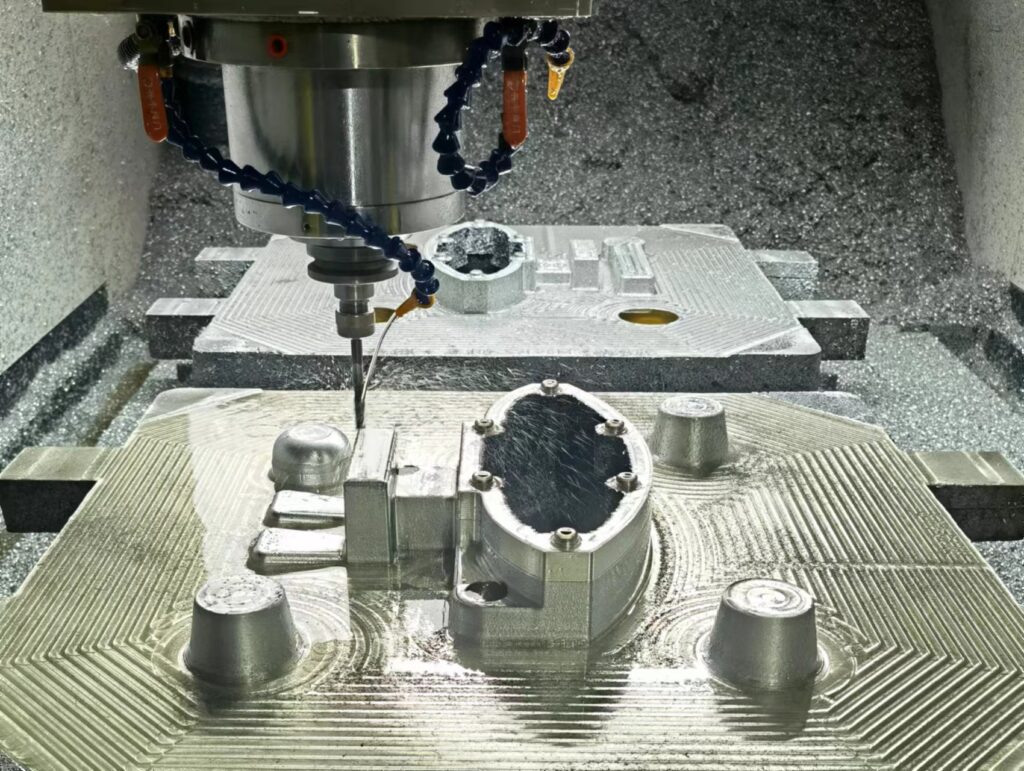
For example, some materials may do better at resisting corrosion, while others can withstand higher temperatures.
Consider carefully the type of metal you are casting, as this will affect which mold material is best for your project.
2. Pouring Temperature
Determine the ideal pouring temperature for your project.
A temperature that is too low will cause the casting to crack or distort, while a temperature that is too high will result in burn marks and bubble formation.
Interestingly, the pouring temperature may vary depending on your geographical location, climate, and environment. So it is best to consult a local expert with experience in this area.
In addition, any changes to the alloy or shape of the part will affect the pouring temperature – so it is important to keep this in mind when making adjustments to your pouring system design. Taking some extra time to get the perfect pouring temperature for your project is worth it – it can save you from a lot of potential headaches.
Before starting the casting process, make sure to test-pour at your desired temperature to ensure the quality of the final part.
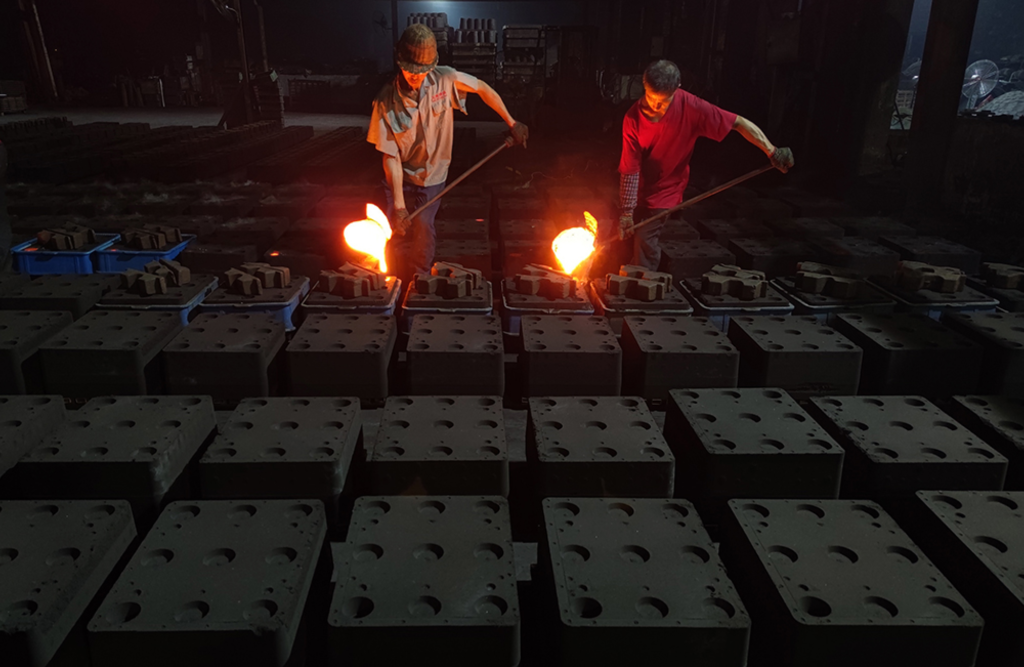
3. Pouring and gating
Establish a proper pouring and gating system that will help ensure the best quality of the casting.
The pouring temperature is one of the most important factors in ensuring the quality of the casting. Iron castings can be poured with hot or cold metal, depending on the type and complexity of the part being poured.
Hot metal will ensure faster pouring and better material flow to smaller parts, while cold metal is usually preferred for larger parts where the extra cooling time helps prevent shrinkage porosity and other defects.
Choosing the right gate size and shape for your casting is important: a gate that is too large can lead to excessive turbulence, while a gate that is too small can lead to metal starvation and incomplete filling of the mold cavity.
The number of runners used will also affect the flow of metal through the mold, and properly sized gates and runners will allow for uniform cooling and solidification of the casting.
So just the right balance is important. Correct gating and pouring can improve the quality of the casting to a great extent.
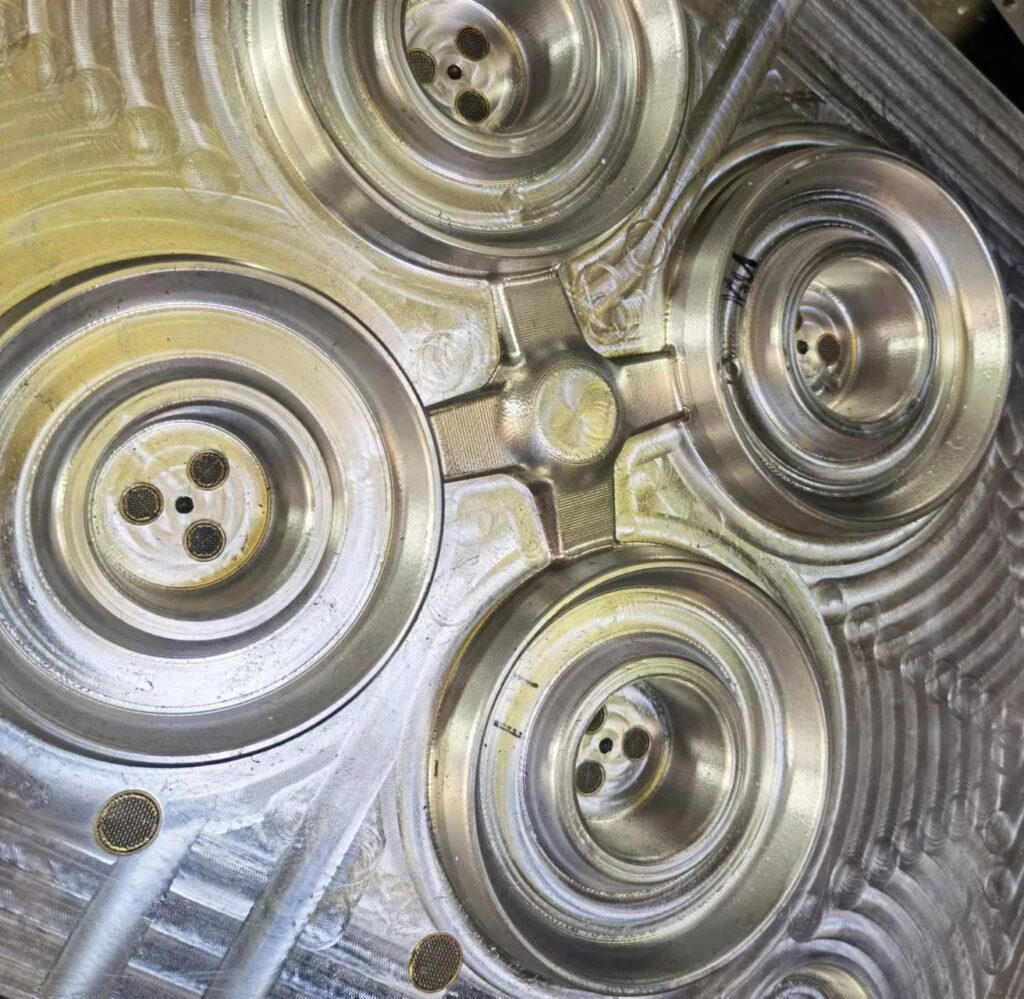
4. Venting
Venting is an important part of the casting process as it helps to remove trapped gases from the mold cavity and prevents porosity in the casting.
The choice of venting system will depend on the size and complexity of the casting, as well as the type of material used.
Different materials require different amounts of venting, and the size and shape of the casting will affect how much gas needs to be released.
The correct size and location of the vent will also help to ensure that the heat is evenly distributed throughout the mold, which helps to avoid any stress or distortion in the finished part.
5. Heat Treatment
Heat treatment is performed after the casting is completed. Heat treatment will improve the strength and ductility of the casting and should be done according to the desired properties of the metal being cast.
In particular, quenching (rapid cooling) and tempering (controlled cooling) are two common heat treatment techniques used to enhance the toughness of castings.
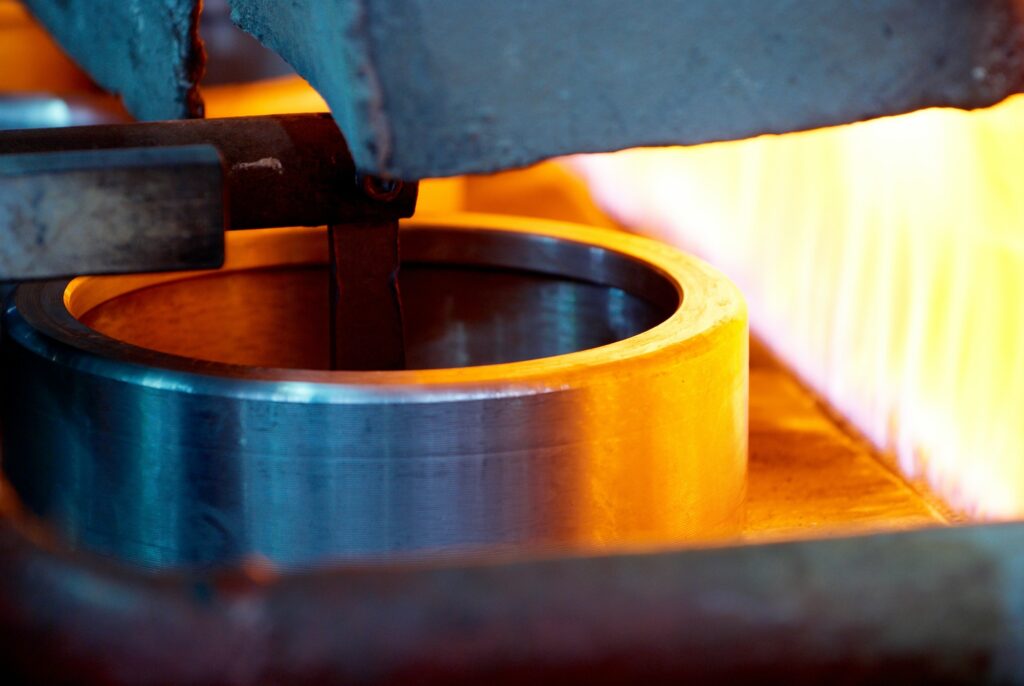
Quenching increases the hardness of the metal, while tempering reduces the brittleness of the metal.
Both processes should be considered when designing a casting system for iron castings to maximize the strength and ductility of the casting.
In addition, proper heat treatment reduces residual stresses, which can cause the casting to crack or distort after cooling.
Therefore, it is important to select the appropriate heat treatment for each type of iron casting to achieve the best performance.
6. Mold filling
Mold filling is an important step in achieving quality castings.
It involves controlling the rate of molten metal flow into the mold cavity in order to ensure uniform filling. Factors to be considered include the size of the opening, pressure drop, gravity and turbulence.
In addition, the thermal conditions within the mold cavity need to be taken into account, as heat can cause undesirable metal vaporization or solidification in certain areas.
In order to ensure the quality of the casting, the influence of the mold filling must be taken into account when designing the casting system for iron.
With the right design, it is possible to achieve good casting quality, reduce scrap rates and thus improve cost effectiveness.
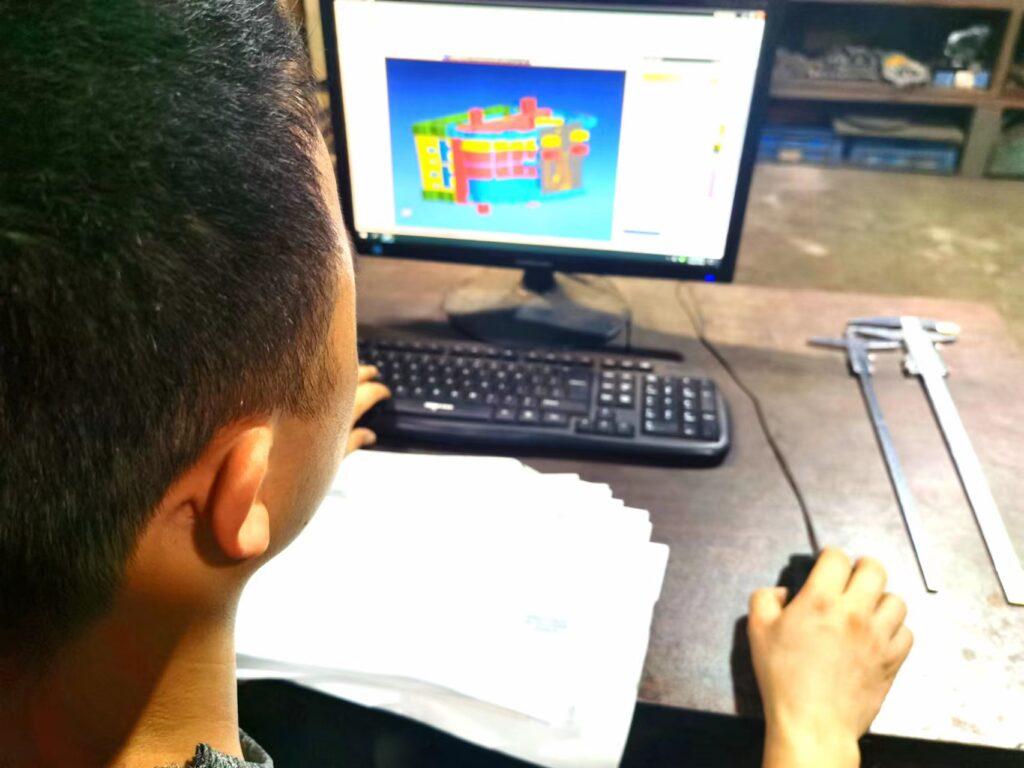
7. Riser design
The design of the risers is an important part of the casting system as they provide additional molten metal to compensate for the shrinkage during cooling.
Designing a riser system with the proper shape and size will prevent sink marks and leaks.
It is important to consider the size and shape of the riser in relation to the size of the casting and how it will be placed in the mold cavity.
In addition, risers can be designed with chokes or vents to better control the direction of molten metal flow and improve yield and quality.
Proper riser design can also help reduce scrap rates and minimize manufacturing costs.
By carefully considering the design of the riser, you can create an efficient and successful casting system for iron castings.
8. Cleaning
After the casting is removed from the mold, it must be cleaned to remove debris from the porous surface.
This is an important step because it affects the appearance, strength and dimensional accuracy of the casting. Depending on the type of casting and the desired surface finish, various methods can be used to clean the part.
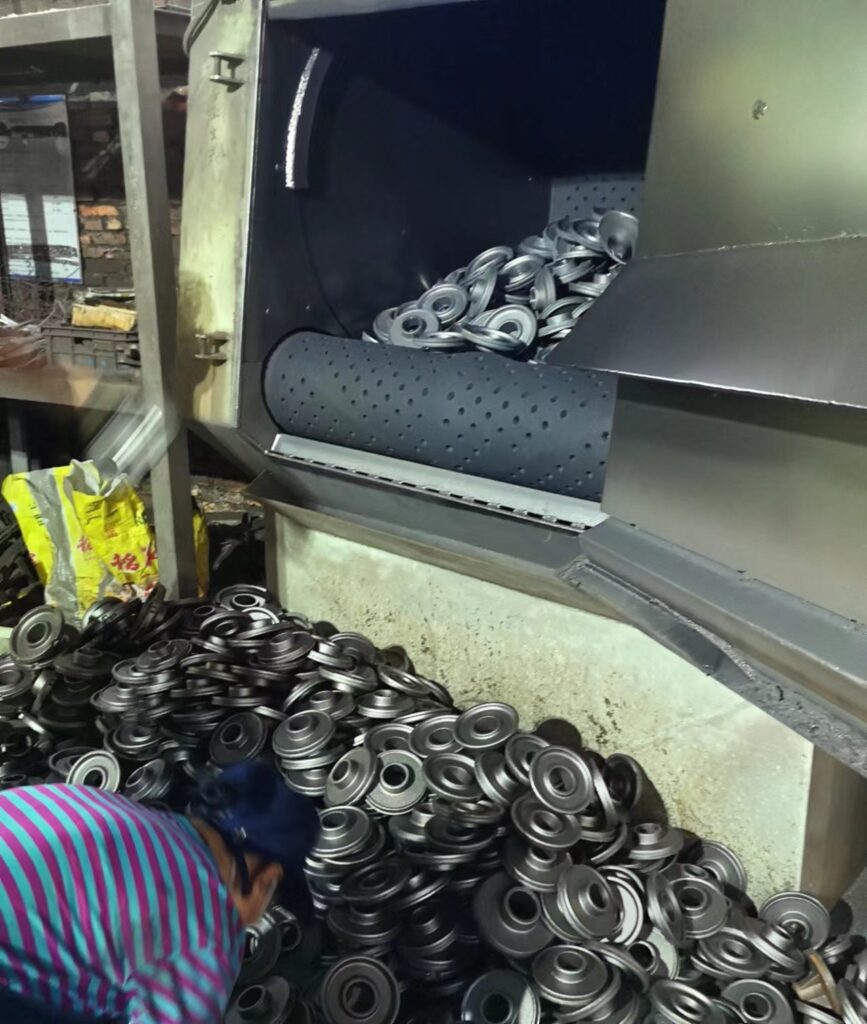
Sandblasting with water or abrasive materials is a common method, as it removes sand and scale from the surface while still providing a textured surface. Chemical cleaning, such as acid washing or alkaline etching, can also be used to remove impurities.
It is important to note that these chemicals can react with metals, so it is important to research which type of cleaning is appropriate for the application.
Ultimately, proper cleaning can ensure the safety and quality of the product.
9. Inspection and Testing
Defects in castings occur during the manufacturing process and can be dangerous and lead to failure.
Therefore, inspecting and testing castings is an important part of the casting process.
Inspectors can use visual techniques or non-destructive tests to check surface quality and look for any potential defects in the casting.
In addition, specialized testing methods, such as x-ray inspection or ultrasound, can help detect undetectable internal defects.
By detecting and correcting these defects, the reliability of iron castings can be improved.
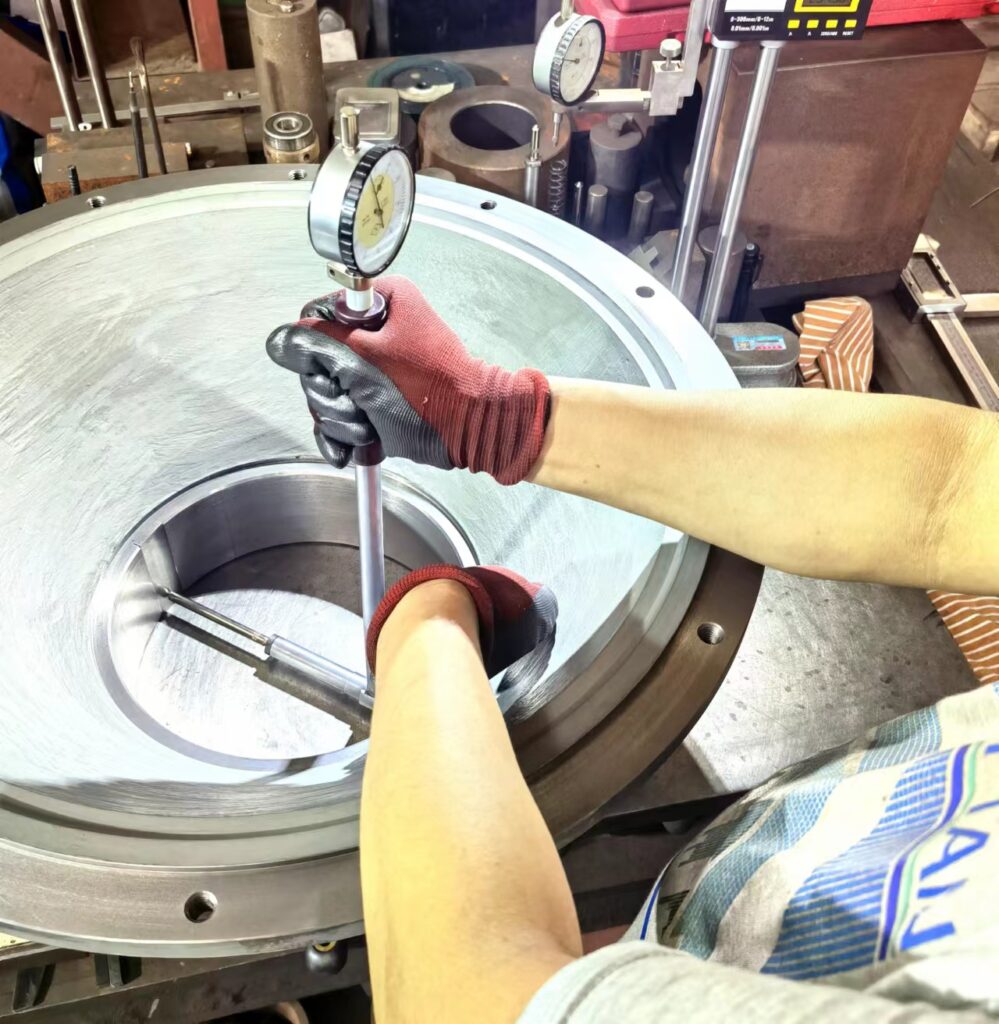
By taking the time to regularly inspect and test castings, manufacturers can help ensure that their products are safe and reliable for buyers.
In addition, early detection of defects can save a company money by avoiding expensive rework or scrap costs.
Therefore, proper inspection and testing is an important part of the iron casting production process.
10. Surface treatment
After inspection and testing of the casting, a surface treatment, such as paint or powder coating, can be applied. This helps protect the metal from corrosion and wear, and can help enhance the appearance of the product.
However, it is important to consider the type of finish that is appropriate for a particular application. Some types of coatings may be difficult to apply or may not provide adequate protection in certain environments.
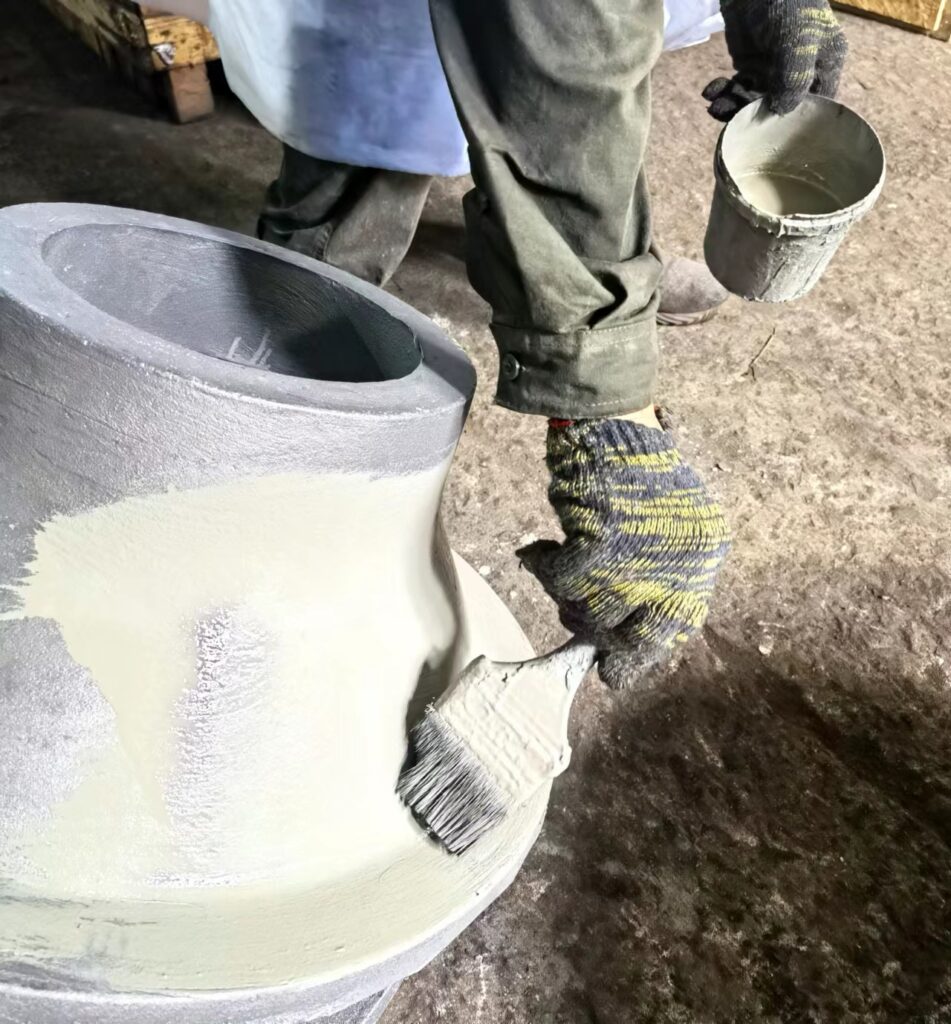
In addition, some treatments may require specialized equipment or chemicals, which can add cost and complexity to the casting process.
It is important to weigh these factors against the performance benefits that can be gained from a particular surface treatment.
Ultimately, the best surface treatment for any given casting will depend on its intended use and the intended operating environment.
Conclusion
By considering the above 10 issues when designing a casting system for iron castings, you can develop a pouring system that is efficient and produces high quality castings.
These are mold material, pouring temperature, pouring and gating, venting, heat treatment, mold filling, riser design, cleaning, inspection and testing, and surface treatment.
Castimoo is a supplier specializing in the design, production and sales of iron castings. With 30 years of experience in this field.
If you have any questions about iron castings, please feel free to communicate with us. Hope to have the opportunity to cooperate with you.