Introduction
Machining iron castings can be a challenging but rewarding job for machinists. In order to create the highest quality cast iron parts, there are many things to consider when machining iron castings.
In this blog post, we will discuss the top 10 issues that you should be aware of in order to produce high quality cast iron parts.
By following these tips, you can ensure that your iron castings meet your exact specifications and requirements.
1. Know the material properties
First, the material used must be suitable for machining iron castings.
Iron castings are generally gray cast iron, ductile iron, malleable iron or white cast iron. Different materials require different processing techniques and tools to achieve the desired results.
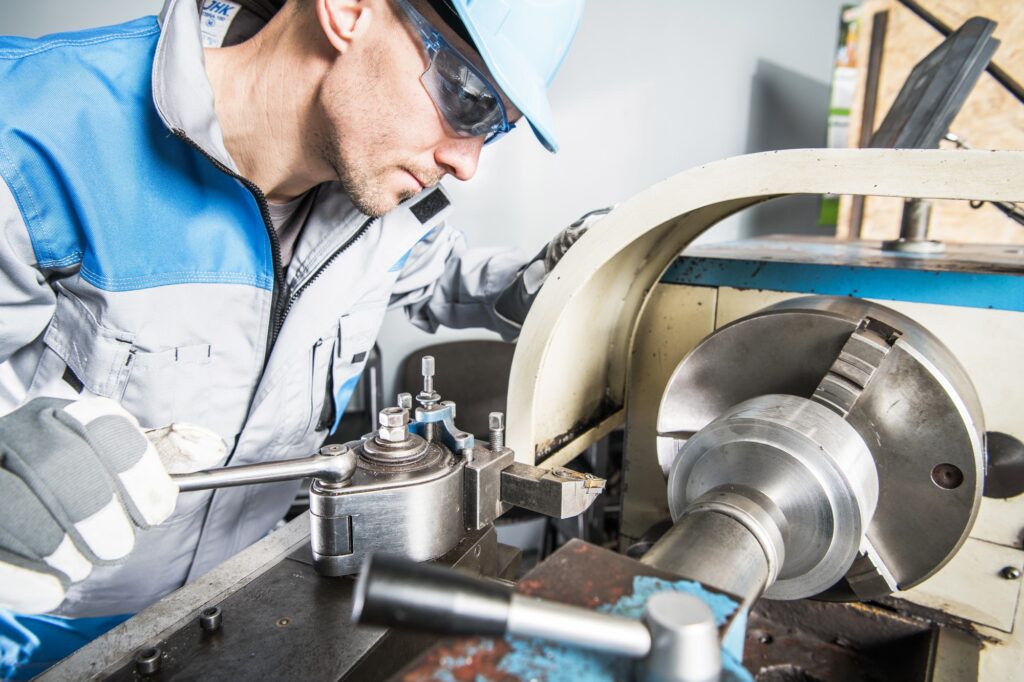
Just like the differences in the elements of gray cast iron and ductile iron, the content of carbon, silicon, manganese, phosphorus and sulfur, and the content of graphite must be noted.
Therefore, in order to achieve the desired results, it is necessary to have a good understanding of the properties of the material.
2. Select the right tool
Next, the right tool selection and setup is critical for machining iron castings.
The choice of cutting tool will depend on the type of material to be machined, for example whether it is a soft or hard casting.
The geometry of the cutting tool should be optimized according to the work piece material and its hardness.
In addition, the appropriate cutting speed and feed rate should be selected according to the application requirements.
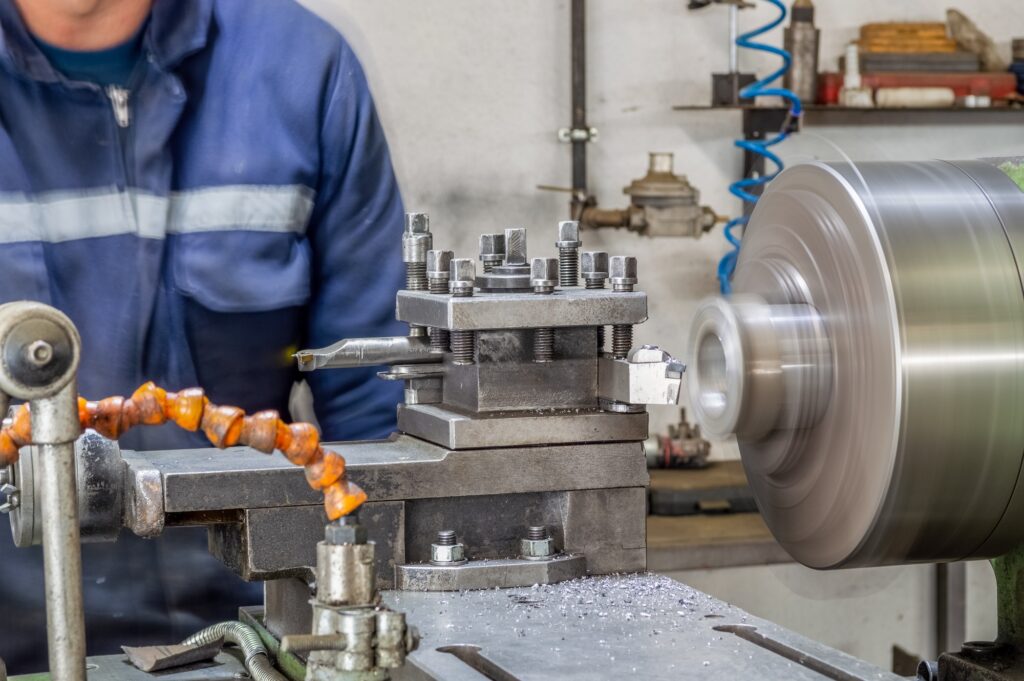
It is important to consider the tool life. This is because tools that are not suitable for the material being machined may wear out quickly and need to be replaced frequently.
Finally, cooling mechanisms should be used to ensure long tool life and improve surface finish.
By selecting the correct tool and setup, operators can increase productivity while minimizing wasted material.
3. Use of fixtures
Third, when machining iron castings, attention must be paid to fixtures. Depending on the complexity and use of the part, different types of fixtures can be selected.
In order for the part to maintain its original shape during machining, it is important to ensure that the correct fixtures and clamps are used. This will prevent warping or distortion of the part as a result of machining.
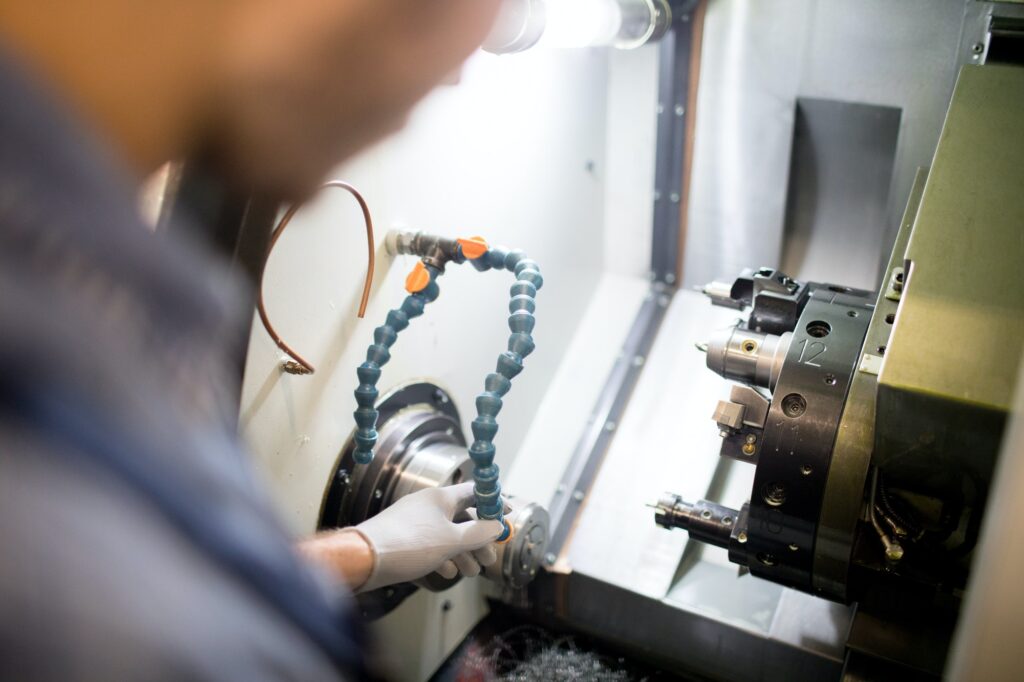
For example, a simple fixture is suitable for machining flat surfaces or right-angled edges, while an extendable fixture can be used when machining highly complex shaped parts and machining multiple areas in one setup.
When using adjustable fixtures in such cases, it is important to ensure that the fixture is securely and reliably fastened to allow the cutting process to proceed smoothly.
In addition, when selecting any fixture, choose one that can accommodate the size of the casting being machined. With this in mind, it is best to choose a fixture with adjustable.
4. Use of coolant
Fourth, there must be sufficient coolant when machining iron castings.
Coolant helps reduce friction, improve surface finish, and extend tool life. It also helps prevent iron casting material from overheating and reducing its strength.
If coolant is not used properly, it can lead to various problems such as poor tool finish, excessive tool wear, and even metal cracking due to thermal shock.
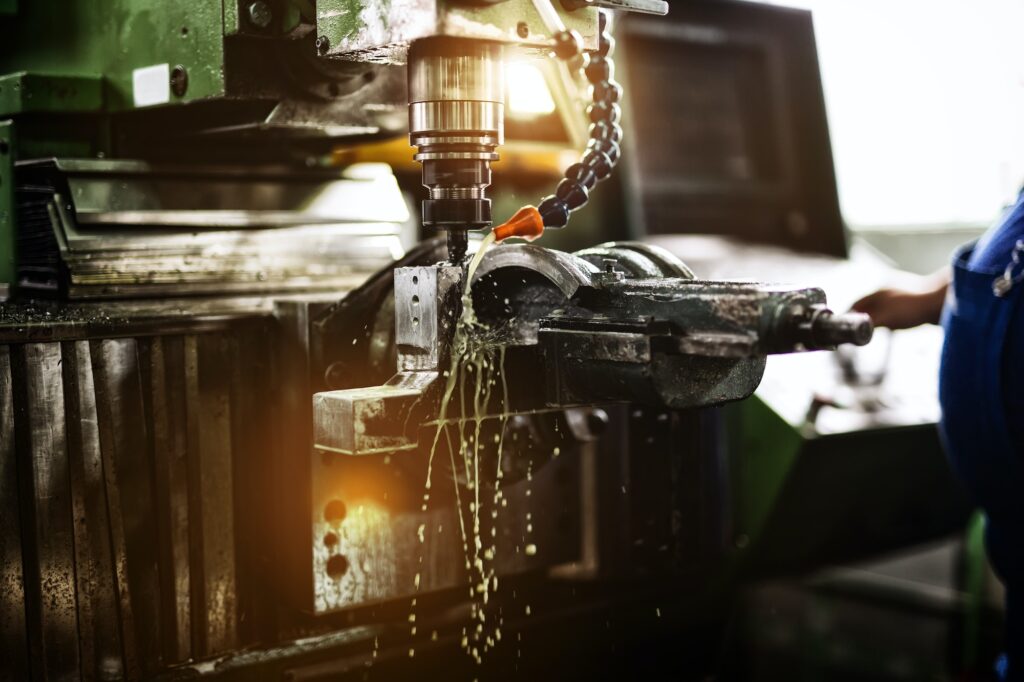
Therefore, manufacturers must ensure that their machines are equipped with sufficient coolant and that the coolant circulates effectively around the work piece during machining.
In addition, it is important to regularly check the level and condition of the coolant to keep it clean and in optimal operating condition.
By taking these steps, manufacturers can ensure that their iron castings are machined safely and with optimal results.
5. Cutting speed
Fifth, the cutting speed must be appropriate for the application and material being machined.
Higher speeds may result in lower surface finishes, while slower speeds may result in increased tool wear.
The cutting speed should be adjusted according to the hardness of the material and the type of tool used.
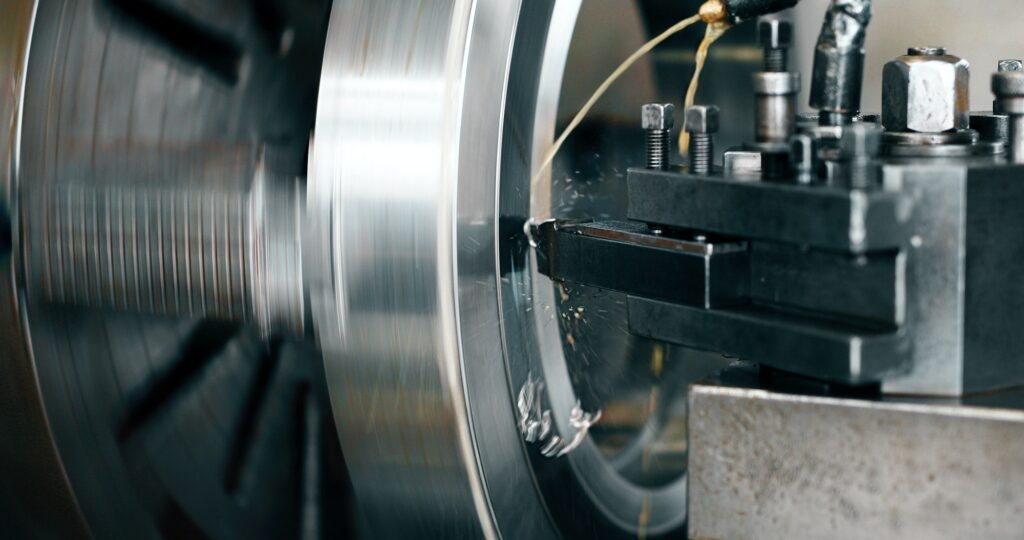
In general, lower speeds are used for harder materials, while higher speeds are used for softer materials.
It is also important to remember that feed rates must also be considered when machining iron castings, as they can have a significant impact on surface finish and tooling.
It is important to find the right balance between feed rate and speed.
6. Cutting pressure
Sixth, the cutting pressure must be appropriate to the material and application. Too much pressure can cause excessive wear on the insert, leading to premature failure.
On the other hand, too little pressure can lead to poor cutting quality and even burn marks due to friction caused by too little cutting force.
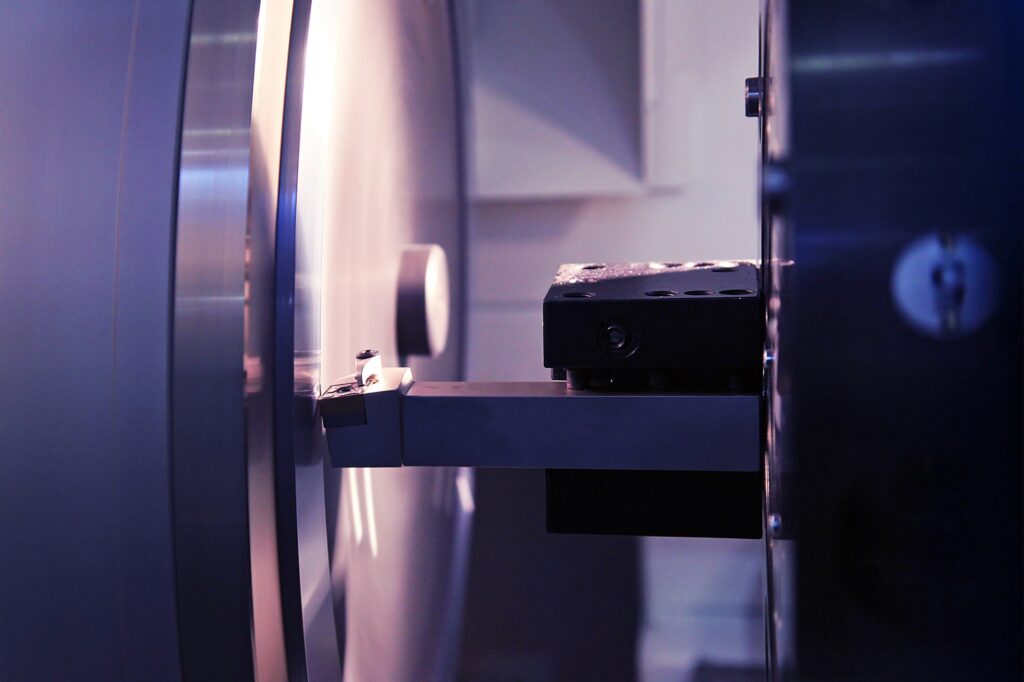
Therefore, it is important to adjust the cutting pressure to the type of material being cut and its application requirements.
In addition, the cutting pressure should be as consistent and uniform as possible to ensure consistent cut quality.
With proper attention to the cutting pressure, it is possible to achieve good results on iron castings.
7. Chip control
Seventh, attention must be paid to chip control during machining. Chips from iron castings may become entangled in the cutting tool and cause damage to the tool or part.
When machining, it is important to use the correct cutting tool and speed so that chips of uniform size can be produced.
If chips are too large, they can clog the machine and cause excessive wear on the cutting tool. Conversely, if the chips are too small, they can lead to a loss of power or accuracy.
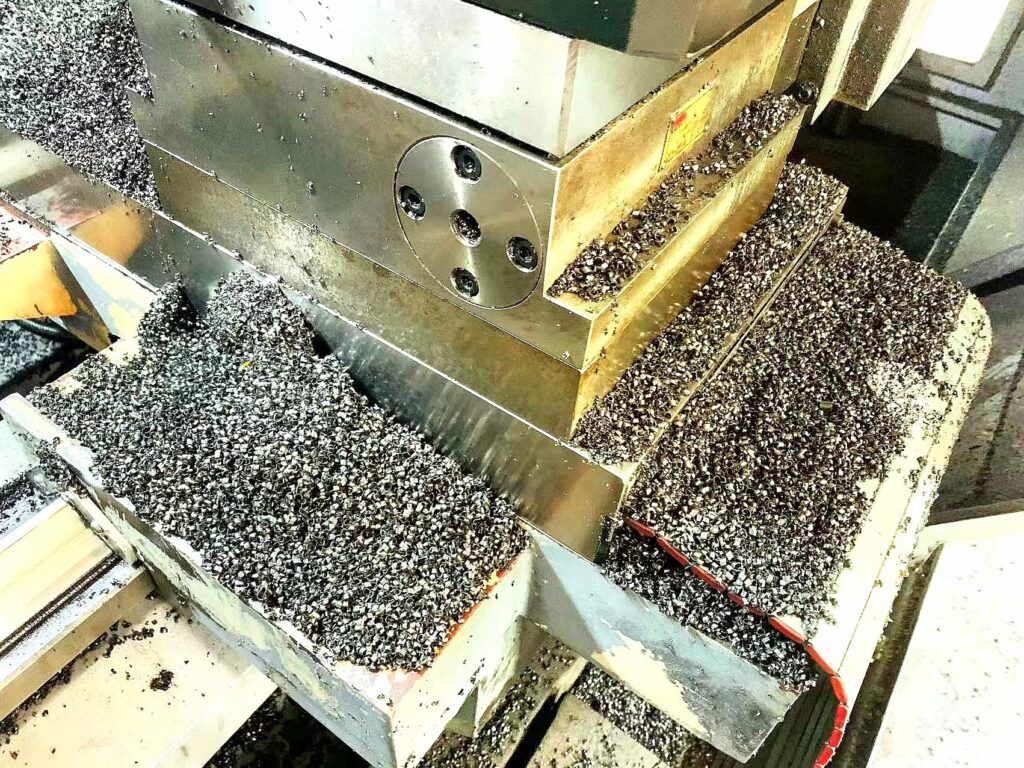
It is critical to use the correct cutting parameters and machine settings to ensure optimal chip control.
In addition, chips should be regularly removed from the work area to prevent clogging.
If chips get stuck, they can cause damage to the machine or part if not removed in a timely manner.
8. Work piece surface
Eighth, attention must be paid to the surface of the work piece before and after machining.
Any burrs, files and rust must be removed from the surface prior to machining. Otherwise, the subsequent machining quality of the work piece will be damaged.
After machining, attention should be paid to the surface for cracks or cold shuts, and if so, these defects should be repaired promptly.
In addition, if the polishing process should be cleaned and the material should be ground to ensure a smooth surface.
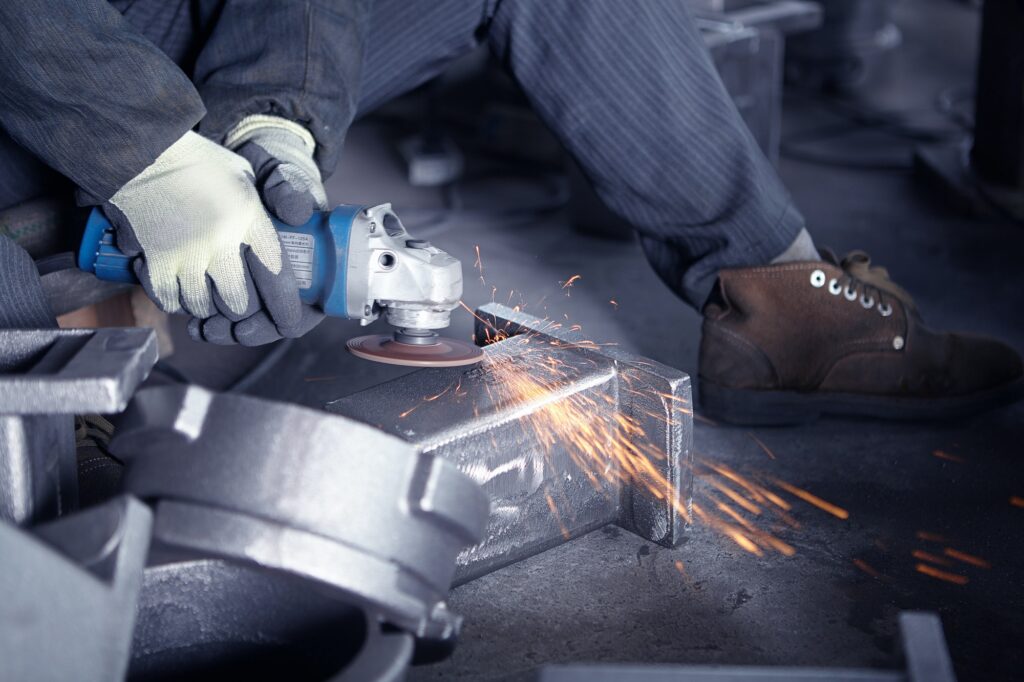
Finally, if necessary, the work piece should be heat treated to improve its durability.
By paying attention to the surface of the work piece during and after processing, you can ensure that their iron castings are of high quality.
9. Safety factors
Ninth, safety factors must be considered when machining iron castings.
Ensure that all personnel involved in the operation are properly trained and familiar with safety protocols.
Ensure that protective equipment is worn at all times, including face shields, gloves and hard hats.
In addition, keep a fire extinguisher nearby in case any accidents occur.
Finally, always follow the manufacturer’s requirements for proper use of tools and equipment.
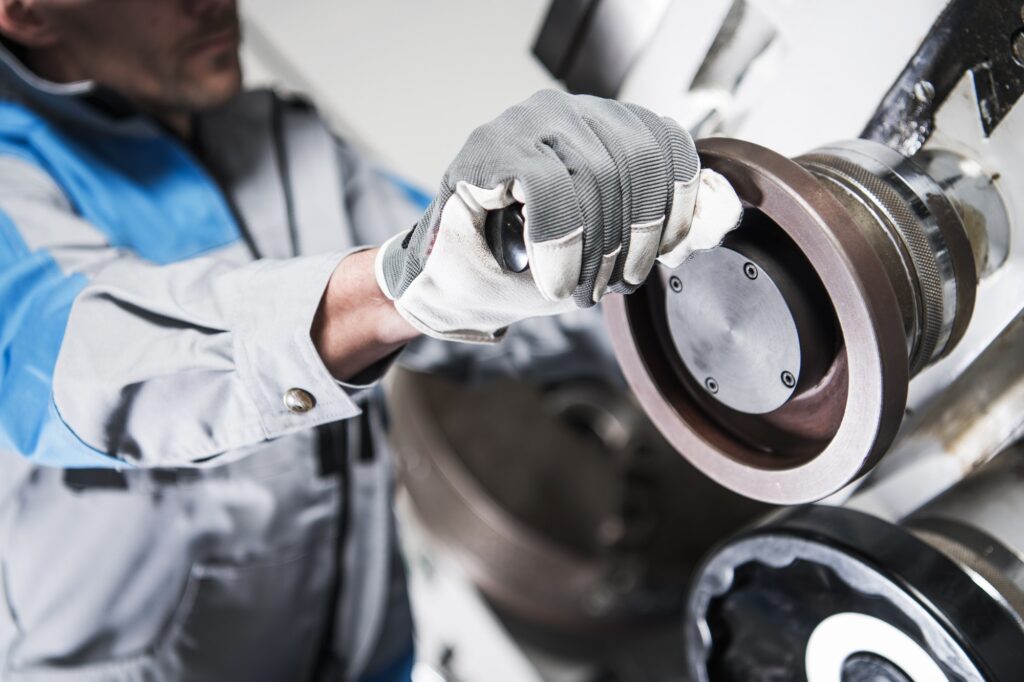
10. Noise control
Finally, noise control should be observed when machining iron castings.
The processing of iron castings can produce loud and unpleasant noise that needs to be suppressed.
Appropriate soundproofing materials should be used around the casting line and any noisy equipment should be placed in an enclosed area.
Careful consideration must also be given to the design of the casting, as certain shapes may produce echoes or increase vibration, which can lead to increased noise.
In addition, proper maintenance and lubrication of the machine is essential to ensure that the equipment produces minimal noise during operation.
Taking these steps will help ensure a quieter and more pleasant work environment for everyone involved in the cast iron process.
Conclusion
In summary, there are ten issues that must be addressed when machining iron castings.
Machining iron castings can be a challenging process.
However, if you are able to follow these recommendations effectively, you can achieve the production of high quality iron castings.
Castimoo is a supplier that produces and sells iron castings. We provide you with one-stop service from mold design to final processing.
Our products are highly recognized by domestic and foreign customers, and we are sure to help you solve your problems and bring you considerable profits.
If you need to purchase iron castings in China, welcome to contact us.