Introduction
Casting is an ancient manufacturing method that has been one of the main methods of manufacturing metal products for thousands of years.
There are many methods of casting production, and different casting methods with different processes, characteristics and product features.
This article will introduce 5 common casting methods and their characteristics.
The process of casting production are mainly divided into two categories: sand casting and special casting. Special casting is also divided into die casting, investment casting, lost foam casting, centrifugal casting, etc.
Sand casting
The most common casting method is sand casting, which is one of the oldest and most versatile methods and is still in common use.
Sand casting uses sand to form a sand mold, and liquid metal is poured into the sand mold to obtain the casting.
The materials used for molding are raw sand, binder and additional materials such as coal dust.
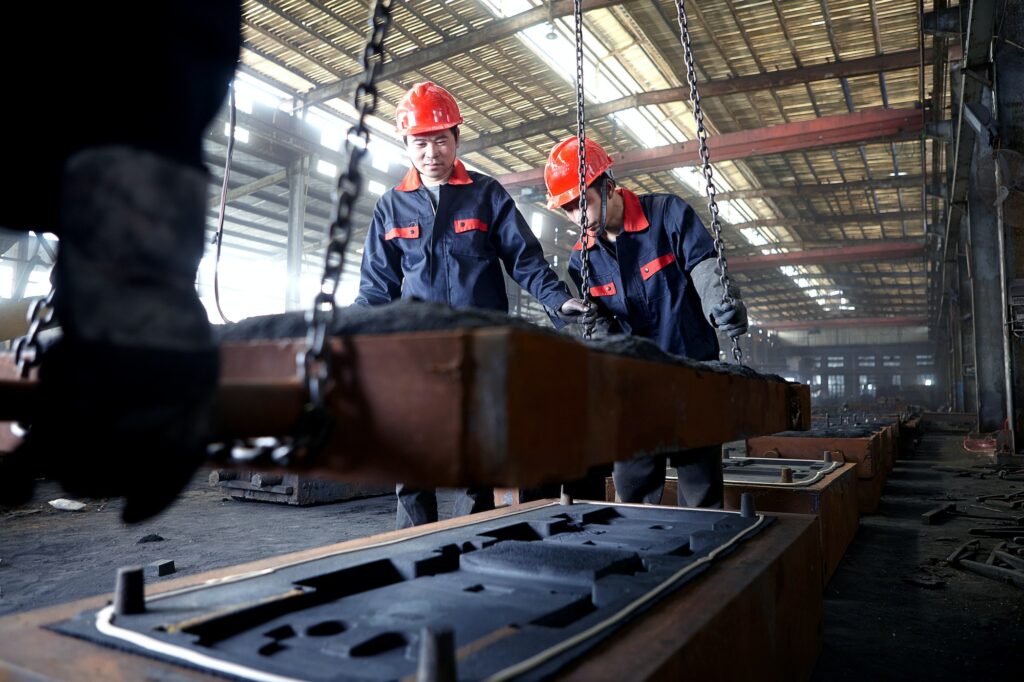
There are two methods of sand casting: hand molding and machine molding. Sand casting is often used for products that require high strength or are large and complex, such as engine blocks and machine frames.
The biggest advantage of this method is that it is cheap and easy to use, making it ideal for small batches or prototypes.
However, the sand casting method also has some disadvantages. For example, the dimensional accuracy of the castings is low and the surface finish can be rough. Although production costs are low, hand molding is not very efficient.
In addition, sand casting is not suitable for mass production due to its long cycle time and complicated process.
Overall, the sand casting method is an economical and proven option for producing cast products in small batches. It is a versatile method that can be used for objects of various sizes and shapes.
Die Casting
Die casting is a metal casting process that uses high pressure to force molten metal into a mold, which is quickly filled and solidified under pressure to form a casting.
Die casting is one of the most accurate and efficient methods for producing high quality castings.
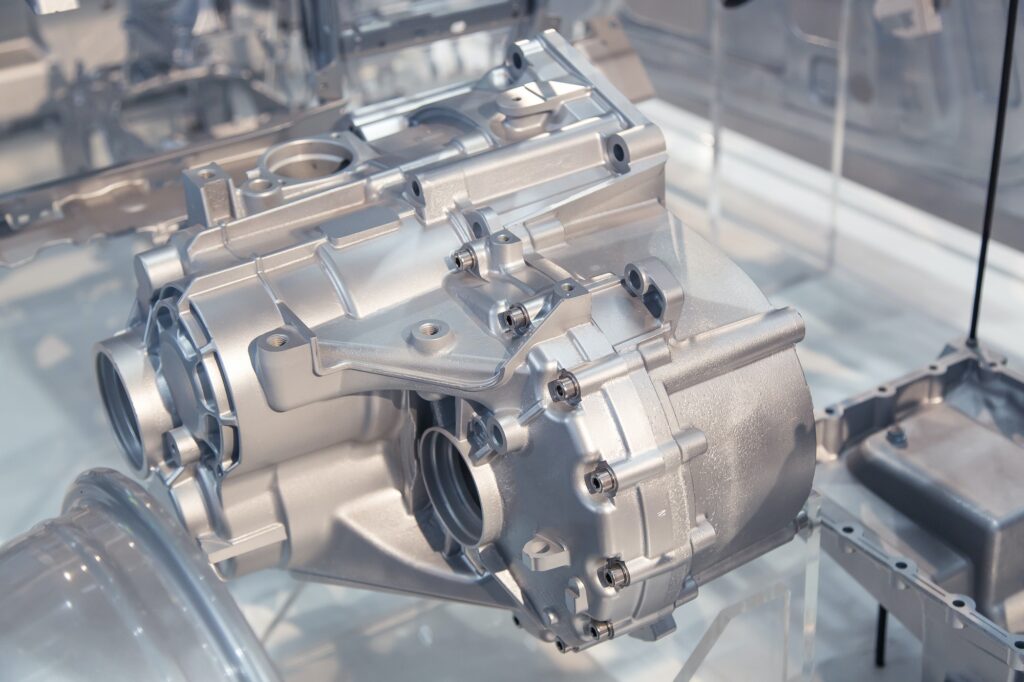
It is most commonly used for aluminum, zinc and magnesium alloys. Die casting produces a product with superior strength and finish compared to the traditional sand casting process.
This method utilizes a gas-tight chamber to hold molten metal at high pressures ranging from 500 psi to over 15,000 psi, depending on the alloy being cast.
The walls of the chamber are heated with an electric current or gas flame, and the metal is injected into a prefabricated mold. The pressure of the liquid metal pushes the walls of the mold apart, creating a well-defined casting shape. Once cooled, the casting can be machined to exact specifications.
The benefits of this process include improved surface finish, superior strength, greater dimensional accuracy and faster production.
Die casting is often used to make automotive parts, electrical components and industrial products. However, it can also be used to create custom shapes for jewelry or other works of art.
The die casting process produces a higher quality product than can be achieved with traditional sand casting methods, making it a popular choice for many applications.
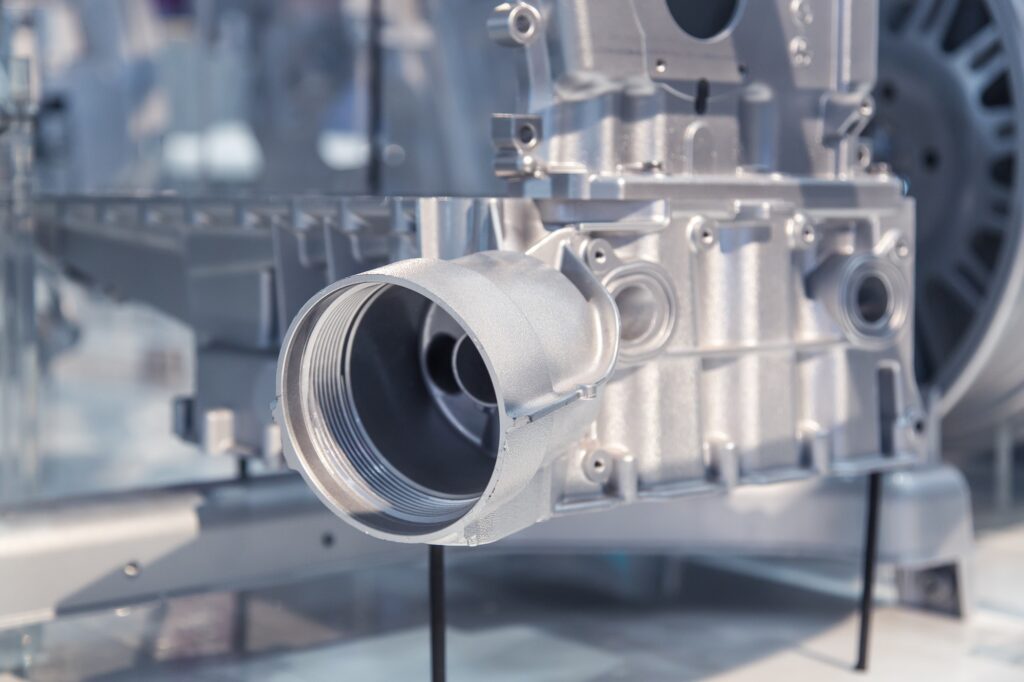
Disadvantages of die casting include
– High level of skill and experience required to produce high quality castings
– High cost of die casting equipment
– High cost of materials required for die casting
– Potential for porosity in castings if the process is not carefully monitored
– Heat treatment is not available for regular die castings
Despite these disadvantages, die casting is still a popular choice for manufacturers and fabricators because of the ease of automation and high productivity of its production.
For complex shapes if you have high strength requirements and superior surface finish requirements, die casting is the ideal choice.
Whether your casting project requires a single casting or thousands of identical parts, die casting can meet your needs.
Because of its ability to produce precision parts of unmatched quality, this method remains one of the most popular metal casting processes.
Investment Casting
Investment casting is a metal casting process.
A mold is made from paraffin wax, a refractory material is applied around the mold to make a shell, the mold is melted off and roasted at high temperatures, and then the casting is made by casting a liquid metal.
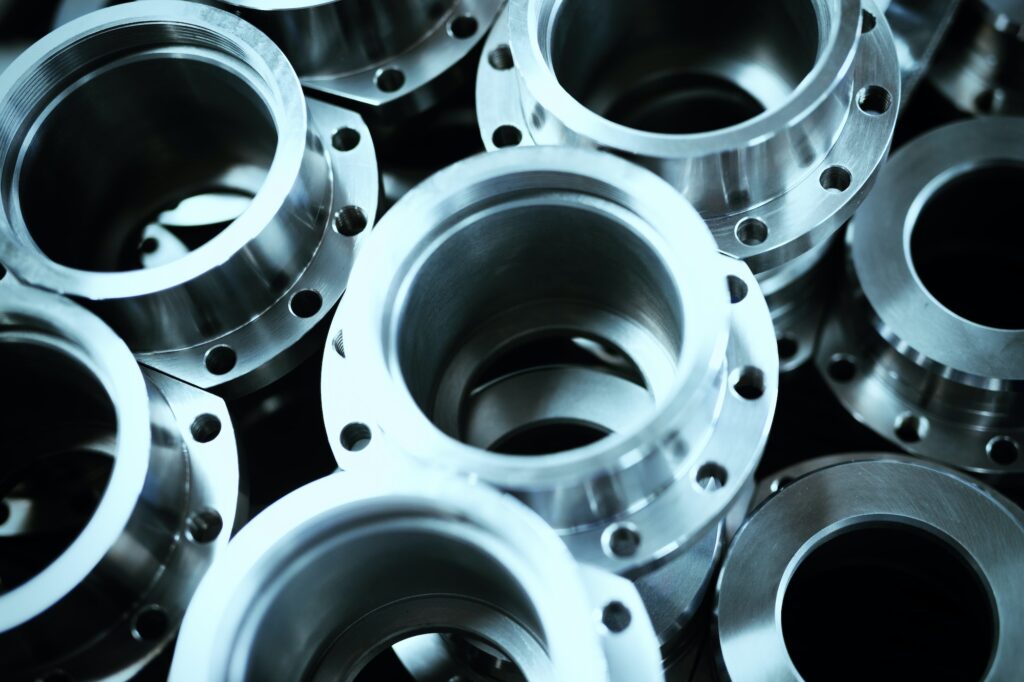
Investment casting produces very precise castings with a very smooth surface. However, there are many production processes and it is mostly used for the production of small size castings.
It is mainly used for casting high precision parts, such as aircraft-engine parts and medical devices.
Investment casting is a good method for producing precise, complex parts with excellent surface finish and dimensional accuracy.
It also allows the use of low melting point alloys, enabling complex shapes to be cast in mass production using the same wax pattern.
Despite such advantages, investment casting can be expensive and limited in the following ways: it is a lengthy production process; the cost of the molding process can be high; and the amount of metal that can be used is limited.
Therefore, when considering casting methods, investors must carefully weigh all of these factors before deciding which method to adopt.
Lost Foam Casting
Lost foam casting is a method of casting objects.
The mold is made of foam, the mold is not removed after molding, and when pouring liquid metal, the mold vaporizes and disappears to obtain the casting.
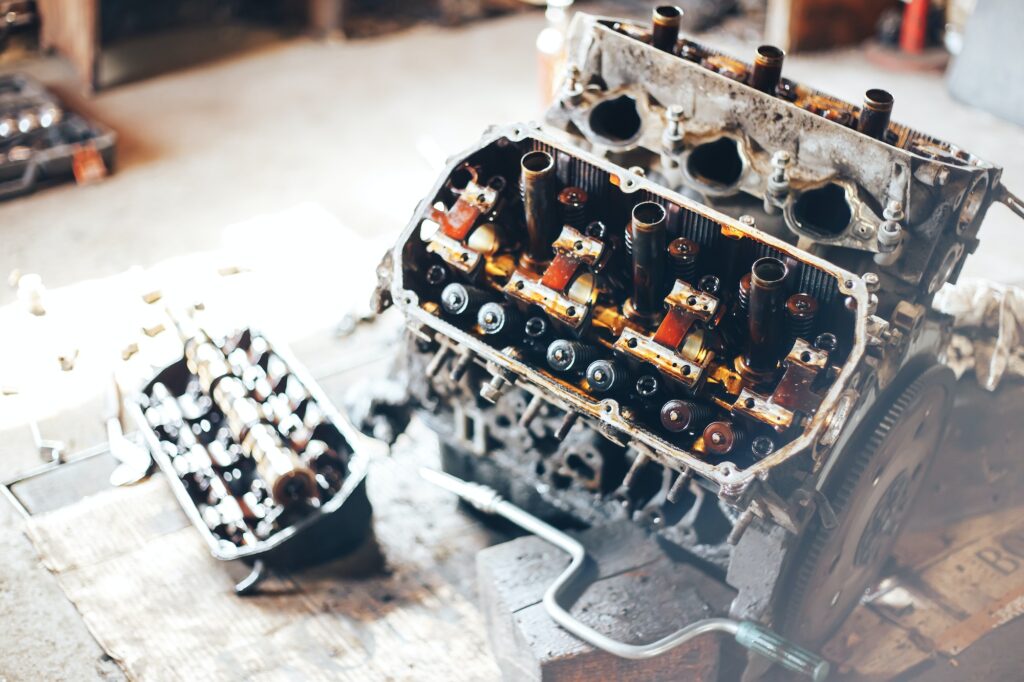
This method is usually used for small objects that require a high degree of precision and allows for rapid molding and casting of complex shapes because the mold is burned off and does not need to be removed.
Lost foam casting can produce parts that are highly accurate and have intricate details.
It is used in a variety of industries, including aerospace and automotive, for parts such as fasteners, hardware and engine parts.
The process is also used in the jewelry industry to produce small objects with a high degree of detail and precision.
The main advantages of lost foam casting are that it eliminates the need to create a new mold each time an object needs to be cast, and it produces a high degree of stability.
The advantages of this process include low cost and high speed. The entire manufacturing process can be accomplished in one step because no time is spent making the mold.
Other benefits include improved dimensional accuracy because the foam expands when heated, filling any spaces or voids in the model.
Finally, this method does not use sand in the molding process, which also reduces sand waste.
The main disadvantages of lost foam casting are that it can be difficult to produce large quantities of parts and that investing in the necessary equipment can be expensive.
In addition, the evaporated foam can create a dangerous environment and the process requires a high degree of precision, which can be difficult to achieve.
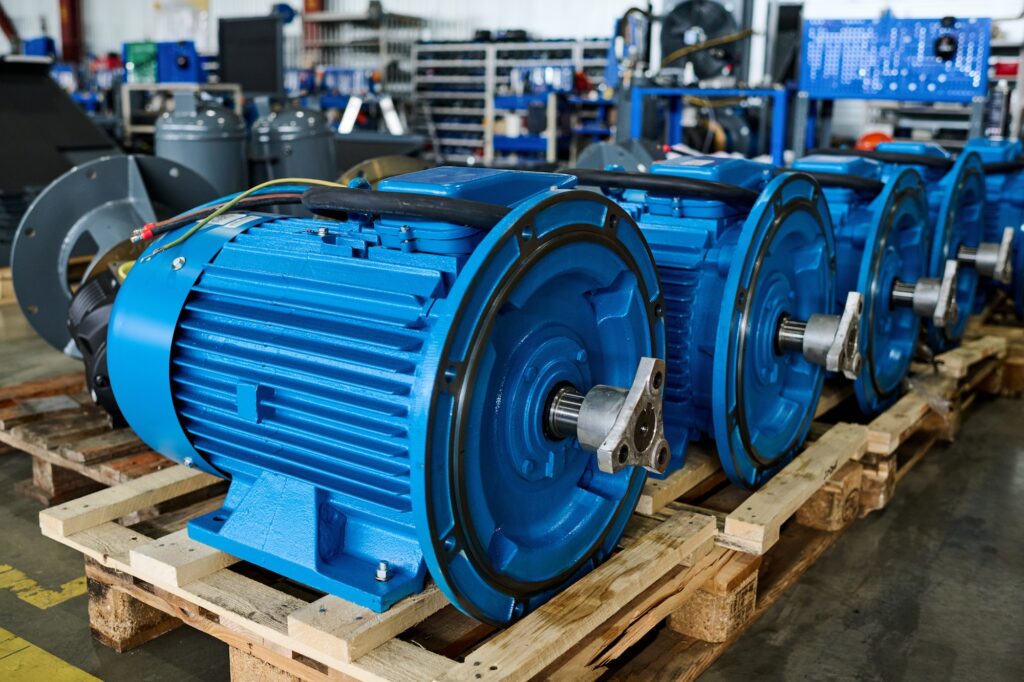
Centrifugal Casting
Centrifugal casting is a casting method that uses centrifugal force to throw molten metal into a mold. The metal is poured into a thin-walled mold that rotates on a high-speed axis. The centrifugal force throws the metal against the walls of the mold and fills the cavity of the mold.
The advantage of centrifugal casting is that it can produce parts with very thin wall thicknesses. The parts produced have good strength and dimensional accuracy. The process is also fast and economical, as it requires minimal finishing.
Centrifugal casting can be used to produce a wide range of metals, including iron, steel, aluminum, copper, bronze and brass. It is most commonly used to produce automotive parts, such as gear blanks.
The main disadvantage of centrifugal casting is that it produces parts with high porosity. This can lead to the formation of trapped air pockets and internal voids.
The process also produces lower yields than more traditional casting methods, so it may not be suitable for mass production.
Centrifugal casting is an important casting method used in manufacturing. It is a fast and economical process that produces parts with good strength and dimensional accuracy.
However, it has its limitations and should be used with caution. For mass production, traditional casting methods may be more suitable.
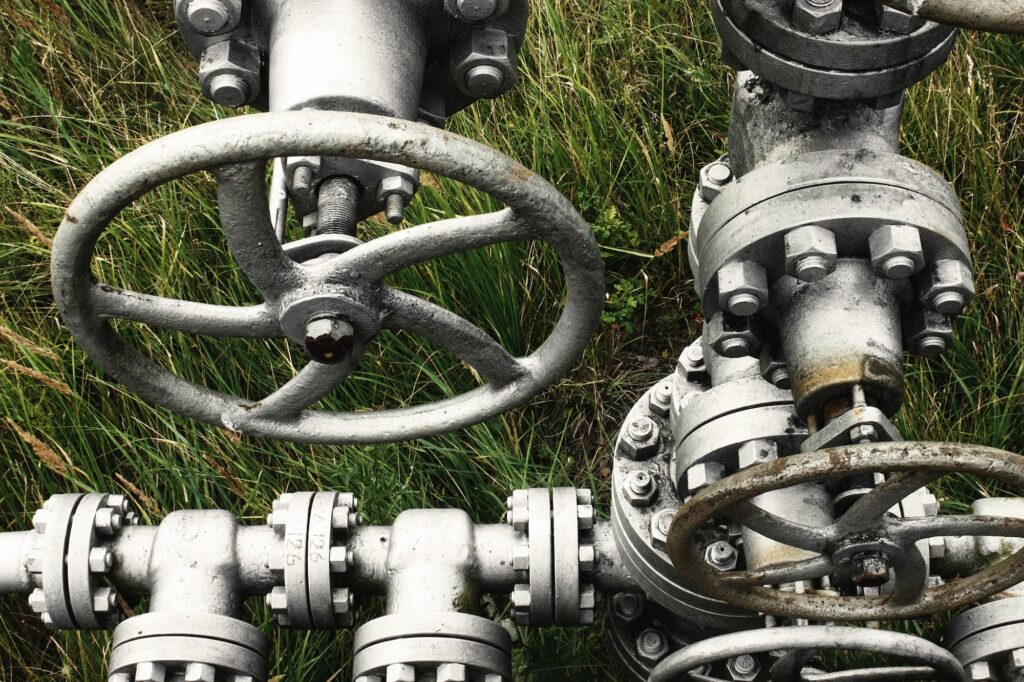
Conclusion
To summarize, five common casting process and their characteristics are presented to you today. They are sand casting, die casting, investment casting, lost foam casting and centrifugal casting.
Sand casting is a common and versatile process that can be used to produce parts in a variety of metals. It is often used for low to medium volume production because it is relatively inexpensive and the molds can be reused. However, sand molds limit the size and complexity of parts that can be produced.
Die casting is similar to sand casting, but the metal is injected into the mold under high pressure, which results in a much finer final product. Die casting also allows the use of finer sand than sand casting, which produces a higher quality surface finish. However, die casting is more expensive than sand casting, and the molds cannot be reused.
Investment casting is a process used to make very precise metal parts with a high degree of detail. Molten metal is poured into a ceramic or metal mold coated with a refractory material. After the metal solidifies, the mold is destroyed, creating a single-use mold. This process is more expensive than sand casting, but it can produce parts with very intricate details.
Lost foam casting is similar to investment casting, but uses disposable or ” lost foam ” rather than reusable molds. This type of mold is made of wax, and after the part is cast, the wax mold is melted, leaving only the metal part. This process is also more expensive than sand casting, but it produces parts with very intricate details.
Centrifugal casting is a process that uses centrifugal force to cast metal parts. Molten metal is poured into a mold that rotates at high speed. This forces the molten metal to flow outward through small openings in the mold, resulting in a highly detailed end product with an excellent surface finish. Centrifugal casting is more expensive than sand casting, but it can produce parts with very intricate details.
Castimoo is a supplier specializing in the design and production of iron castings. If you have casting questions or need to purchase iron castings, welcome to visit our website castimoo.com or contact us by email. We hope we can help you.
One Response