Introduction
Iron castings are a common part in many different types of machinery. Therefore, it is important to inspect iron castings for any potential defects before importing them.
In this blog post, we will discuss 10 things to look for when checking iron castings. By doing so, you can ensure that they meet your quality standards and expectations and reduce your purchasing risk.
1. Make Samples
Before purchasing iron castings in bulk, be sure to communicate with your supplier about making samples, which is a very important factor in reducing risk.
Ask the supplier to provide samples so that you can check for defects in their workmanship before committing to a bulk order.
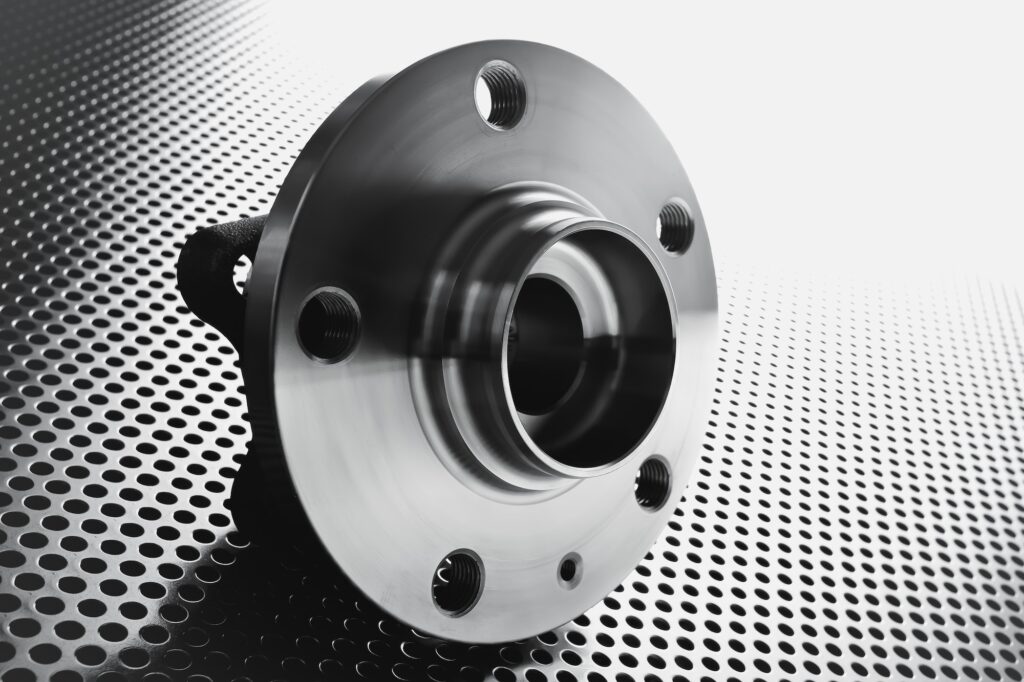
If the supplier is unwilling or unable to provide samples, this may be a sign to be wary. It is also possible that the cost of the sample is an issue that needs to be effectively communicated with the supplier.
Paying attention to these factors will help reduce your risk of importing iron castings. By ensuring that the castings meet your quality standards, you can avoid costly delays and repairs.
2. Appearance
The most significant appearance defects are sand leakage, misalignment and porosity.
Sand Leakage
Sand leakage is when molten iron comes in contact with sand and if the molding process is not controlled properly, sand leakage can occur.
This will result in a rough surface of the iron and may even cause hollowness.
Misalignment
Misalignment occurs when two parts of the casting are not properly aligned with each other. This can cause stress points that can lead to cracking or fracture.
Porosity
Porosity is when air bubbles are trapped in the metal during the solidification process. These air bubbles will make the metal weaker and more susceptible to corrosion.
If you see any of these cosmetic defects, it is important to reject the casting or ask for it to be repaired or replaced. Otherwise, it could lead to a dangerous situation.
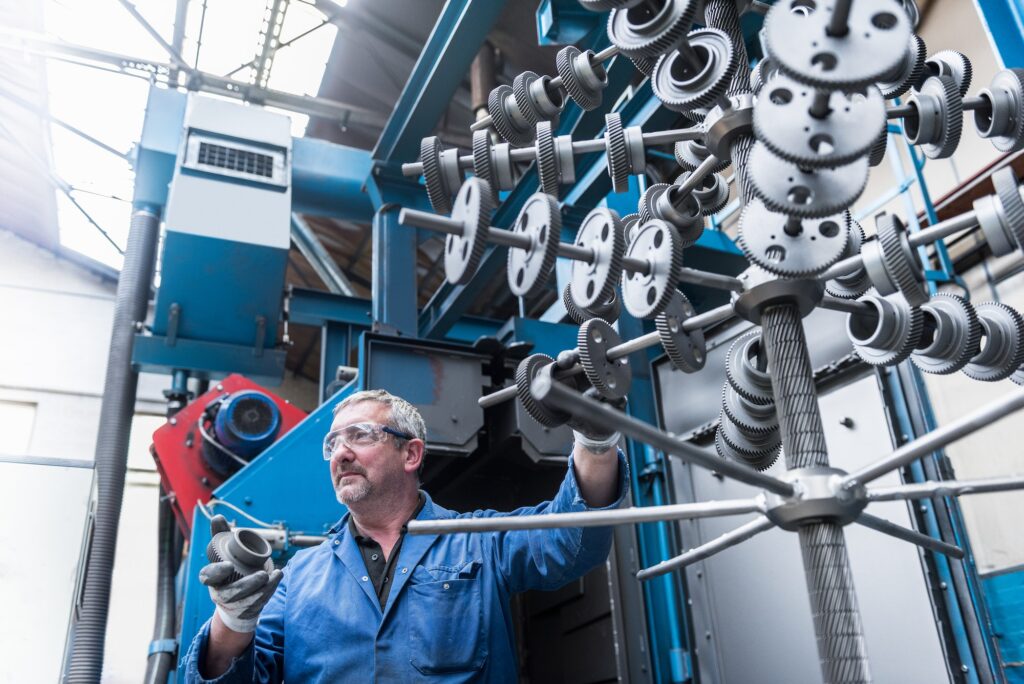
3. Surface Finish
Rust
Check the surface for any signs of rust or corrosion. The surface of the casting is rusting because it was not properly protected during storage.
Uniform
Make sure the surface finish is uniform and consistent. The most predominant method of surface preparation for castings is shot peening.
If there are surface defects, it is most likely due to a reduction in the quality of the blasting media or the blasting parameters should be optimized.
Burrs
Make sure there are no sharp edges or burrs on the casting. If burrs occur frequently, it is most likely due to poor mold design or improper mold maintenance.
All of these surface defects can be easily remedied by the supplier if they are caught early on. By focusing on surface finish, you can avoid potential problems down the road.
4. Dimensional Size and Accuracy
Casting size
Castings should be sized to within the required tolerances with sufficient machining allowance to allow for finishing operations.
If there is not enough machining allowance, the casting will not be machined above and will need to be reworked or scrapped.
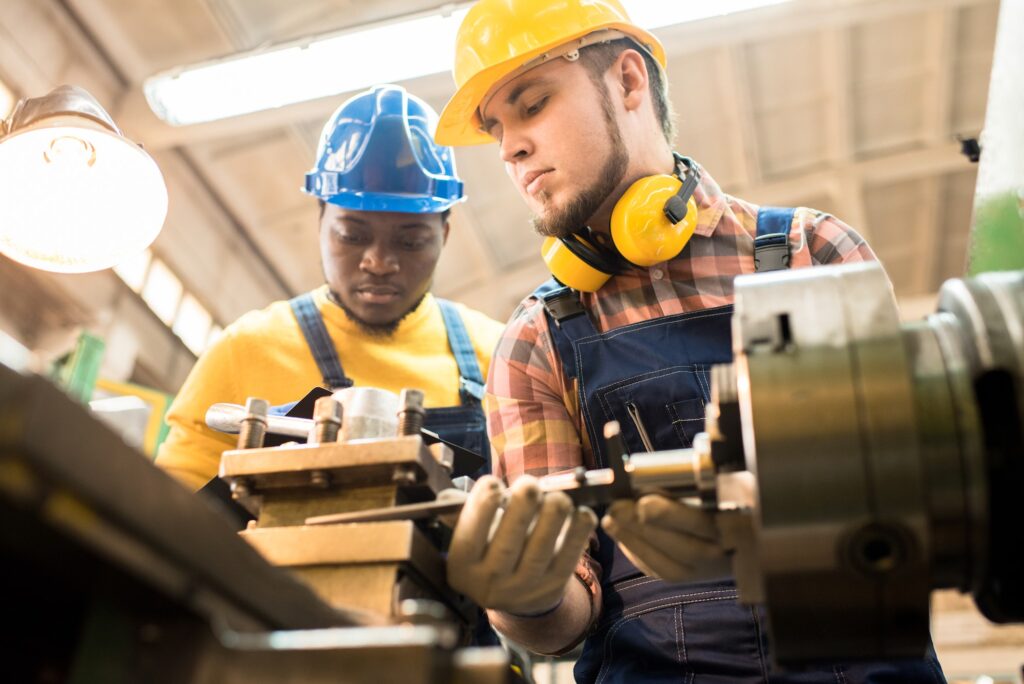
Accuracy of machining dimensions
The accuracy of the machined dimensions of the casting is equally important.
The accuracy of the dimensions should be within the specified tolerances. If the dimensions are not accurate, the casting will not fit or function properly with other parts.
There are three primary methods to check dimensional accuracy on castings.
First, critical features on the casting are measured using a coordinate measuring machine (CMM). This is the most accurate method of checking dimensions, but it is also the most expensive and time consuming.
Second, measurements are taken using micrometers or vernier calipers. This is the most common method of inspection.
Third, use a template or gauge that has been made to match the required tolerances. This method is not as accurate as using CMM, but it is efficient and less expensive.
5. Weight Consistency
When checking the weight of iron castings, use a weight gauge to measure the weight of the casting.
The weight should be in general agreement with the requirements. If not, there may be a problem with the iron casting.
In addition, because each manufacturer has different standards for the material ratio of iron castings, there will be some errors, thus causing the rough weight of iron castings to fluctuate.
Blank weight up and down 0.1kg is normal.
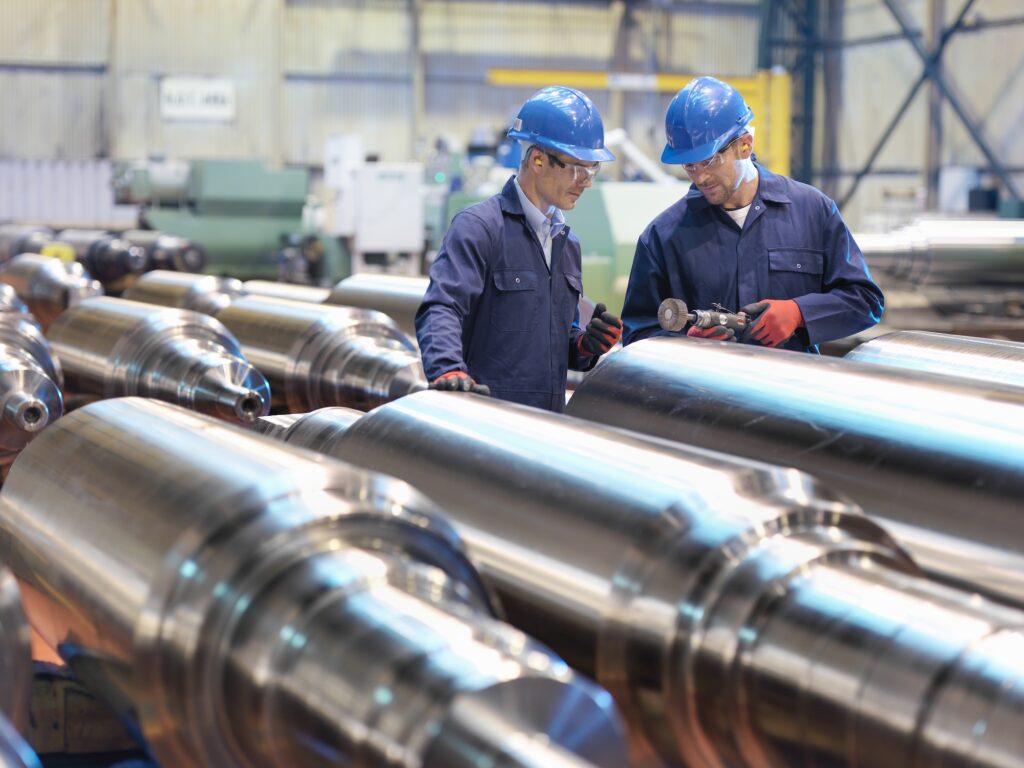
6. Mechanical Properties
Iron castings are a common part in many machines and structures.
It is important to test the mechanical properties of these castings to ensure that they can meet the requirements of the application.
There are several methods that can be used to test the mechanical properties of iron castings.
Hardness testing
One common method is to use a hardness tester. The hardness tester measures the resistance of the material to penetration.
The Brinell test is the most common method for checking the hardness of iron castings.
A Brinell hardness tester measures the indentation hardness of a sample by pressing a hardened steel ball into the surface of the sample.
Things to keep in mind when checking the hardness of iron castings include the type of test used, the size of the indentation and the depth of the indentation. The Brinell hardness of cast iron is approximately 180-220.
Tensile Strength Testing
Another common method is to use a tensile tester. A tensile tester measures the amount of force required to pull something apart. Cast iron has a tensile strength of about 55,000 psi.
Impact Testing
Iron castings can also be tested with an impact test. Impact testing measures how much force is needed to break something. Cast iron has an impact strength of about 2,500 ft/lbs.
Fatigue Testing
Finally, iron castings can be tested with a fatigue test. Fatigue testing measures how much stress a material can withstand before it fails. Cast iron has a fatigue strength of approximately 2,000,000 psi.
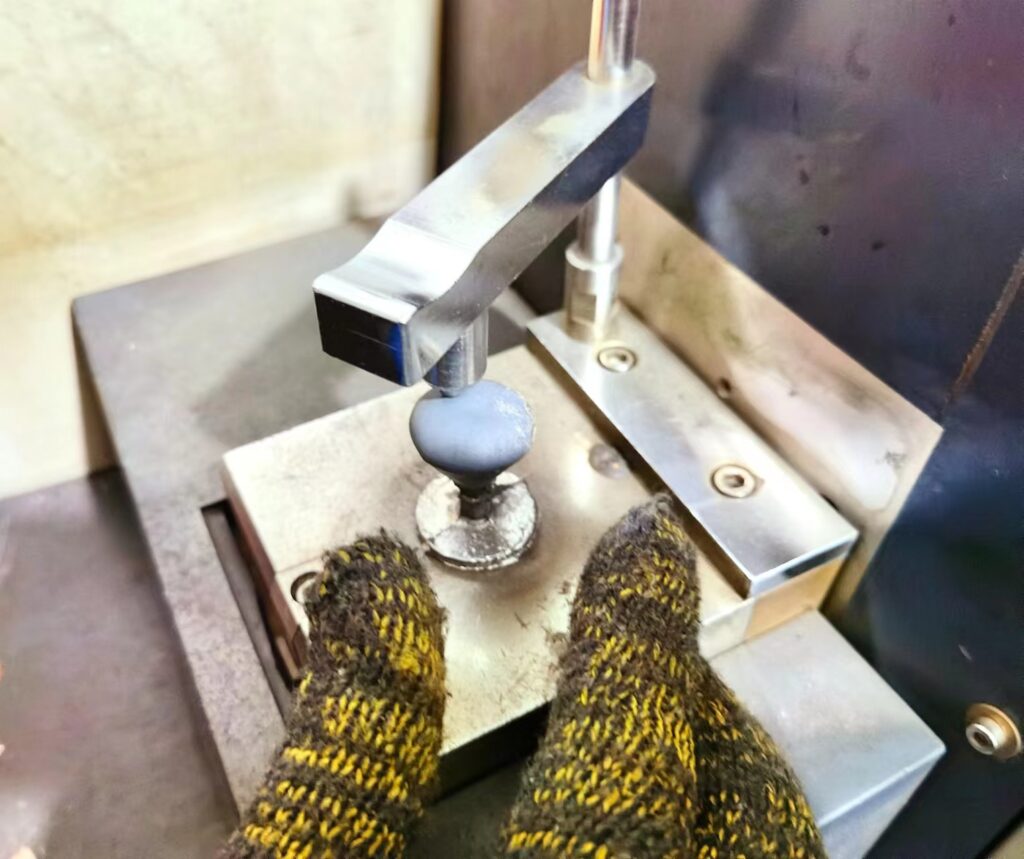
7. Chemical Composition
A spectrometer is used to determine the chemical composition in iron castings. The most important elements are carbon, silicon, manganese, phosphorus and sulfur.
These five elements together account for more than 95% of the weight of the casting. Other trace elements are magnesium, chromium, molybdenum, nickel, copper, vanadium and titanium.
Depending on the needs of the iron casting product, the carbon and silicon content of the casting can be controlled. Manganese content is 0.70- 0.90%. Both phosphorus and sulfur are kept low, usually below 0.05%.
It is important to note that if the carbon content is too high, the casting will be brittle and prone to cracking.
If the silicon content is too high, the casting will be porous and fragile.
If the manganese content is too high, the casting will be hard and difficult to machine.
The other trace elements listed above are also usually kept low because they can negatively affect the performance of iron castings.
For example, magnesium and chromium can act as impurities and make iron castings more brittle. Molybdenum and vanadium can make castings harder and more difficult to machine.
Overall, the chemical composition of iron castings is something to be aware of because it can affect the performance of the final product.
By controlling the content of certain elements, you can ensure that your iron castings meet your specific requirements.
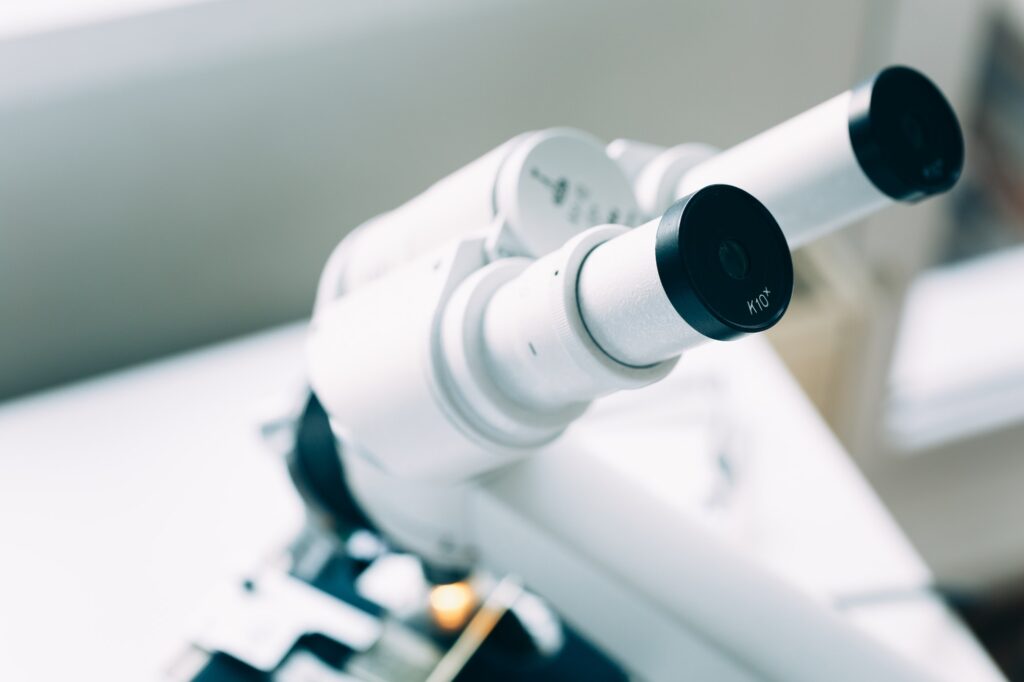
It is also important to note that if your supplier is unable to provide records of composition analysis, or even a spectrometer, it is advisable to switch to a more reliable supplier.
A reputable iron casting supplier will be able to provide you with the information you need to ensure that their customers receive the best possible product.
8. Microstructure
The microstructure of cast iron can be examined with light microscopes, scanning electron microscopes and transmission electron microscopes.
When examining the metallographic structure of iron castings, the following points must be noted.
-Type of cast iron
-Carbon content
-Form of graphite
-Presence of other elements
-History of heat treatment
Graphite in gray cast iron is in the form of flakes, while in ductile iron it is in the form of nodules.
Castings made from malleable iron have a high carbon content and graphite is present in the form of pearlite.
The microstructure of white cast iron differs from other types of cast iron in that it contains a high percentage of carbon in the form of smectite.
The type of iron casting, its carbon content and the form of graphite will determine the properties of the casting.
The presence of other elements in the casting may also have an effect on its properties.
The heat treatment history must also be taken into account when examining the metallographic structure of iron castings.
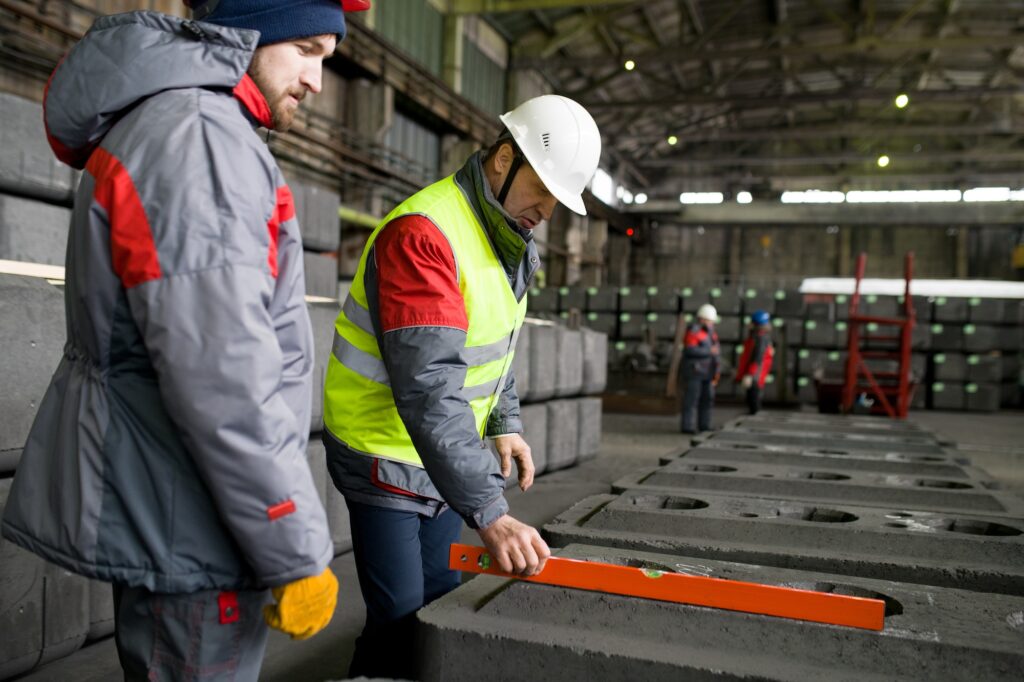
9. Flaw Detection
If you purchase iron castings of high quality requirements, to ensure the quality of these iron castings, it will be important to detect any defects or flaws that may exist within the part.
There are a number of methods available for defect detection, including radiography, ultrasonic inspection and magnetic particle inspection.
Radiography
It involves the use of X-rays to create an image of the casting. This image is then analyzed to determine the presence, size and location of any defects that may be present.
X-rays are able to penetrate most materials and can be used to test castings of all sizes, making them ideal for this type of testing. However, if the casting is large, the cost can be expensive.
Ultrasonic Inspection
Ultrasonic inspection is another common method of defect detection.
In this type of inspection, sound waves pass through the material being inspected, bounce off any defects and produce an echo that is picked up by the receiver. The time it takes for the echo to return can be used to calculate the size of the defect.
Ultrasonic inspection can be used to detect surface and subsurface defects.
The advantage of ultrasonic inspection is that it can be used on a variety of materials, including metals, plastics and composites. It can also inspect larger areas in less time than other methods.
The disadvantages are the high cost of the equipment and the fact that interpretation of the results can be difficult.
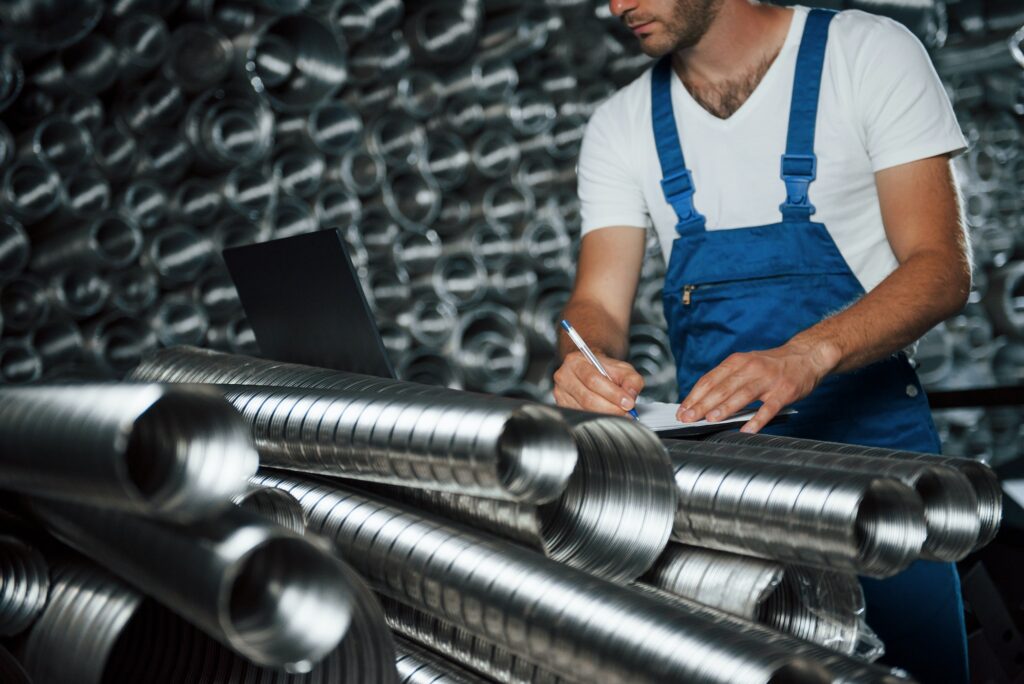
Magnetic particle inspection
Magnetic particle inspection is another method that can be used to detect defects in ferrous castings. This method is based on the principle that the magnetic field is distorted by the presence of defects.
The magnetic particle inspection device consists of a magnet and an indicator. The magnet is used to generate a magnetic field in the area to be inspected.
The indicator is then used to detect any distortions in the magnetic field. This method is most effective when the casting is made of a ferromagnetic material, such as iron.
Magnetic particle inspection can be used to detect a variety of defects, including cracks, voids and inclusions. This method is particularly useful for detecting defects that are not visible to the naked eye.
However, magnetic particle inspection is relatively slow and expensive, but it can detect very small defects in castings.
The choice of the correct flaw detection method depends on the specific application as well as the size and complexity of the casting.
10. Thermal Stress Relief
Thermal Stress Relief (TSR) is a process used to remove residual stresses from castings. This is achieved by heating the casting to a temperature below the melting point and then cooling it slowly.
TSR is important for large or heavy castings because these castings may be prone to cracking if residual stresses are not removed.
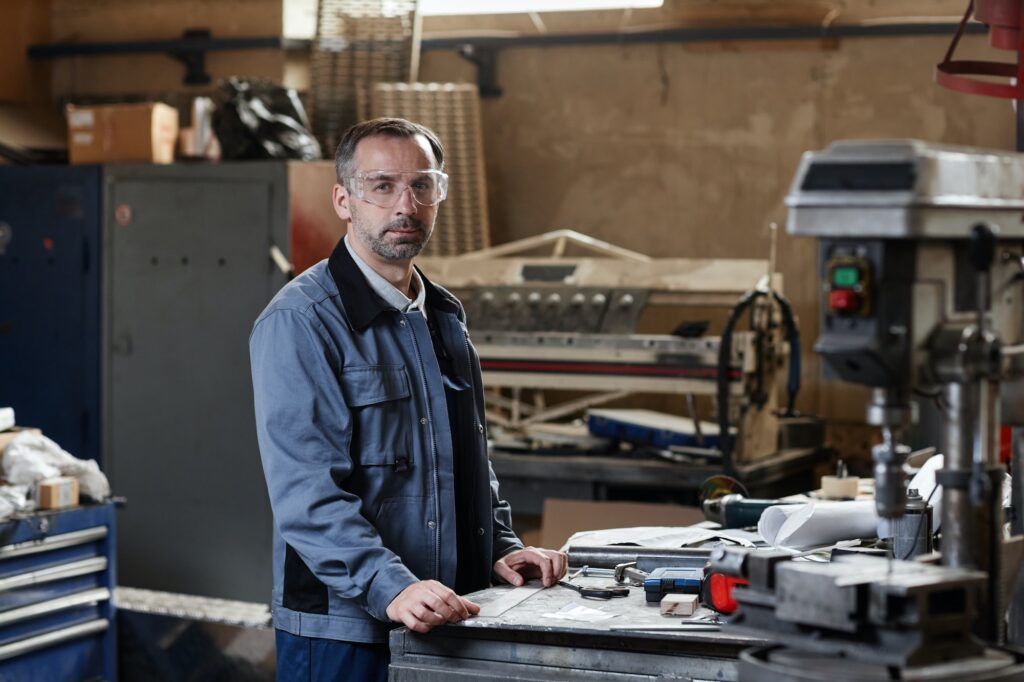
There are several ways to detect TSR in iron castings.
One way is to use a magnifying glass or microscope to look for cracks or other evidence of cracking.
Another method is to use an x-ray machine to look for changes in the microstructure of the casting.
Finally, you can use a hardness tester to measure the hardness of the casting. If the hardness increases after TSR, it indicates that residual stresses have been relieved.
Conclusion
When checking the quality of iron castings, there are 10 factors that should be considered, such as make samples, appearance, surface finish, dimensional size and accuracy, weight consistency, mechanical properties, chemical composition, microstructure, flaw detection and thermal stress relief.
By taking all of these factors into account, you will be able to determine whether or not an iron casting meets your standards for quality.
Castimoo has an independent laboratory, complete with testing instruments, and reasonable testing methods. Strict quality process to ensure product quality.
Our gray iron castings and ductile iron casting products are well received by our customers both at home and abroad. We hope we can help you too.