Introduction
Shrinkage is always a problem when you make iron castings. That’s because if shrinkage is not properly controlled, it can easily lead to shrink holes and shrink loosening in iron castings, which will seriously affect the accuracy and strength of iron castings.
If you are a buyer of iron castings, poor shrinkage of the product is a problem that you should never ignore. Imagine being anxious when you purchase iron castings with shrinkage problems that cannot be solved.
In this blog post, we will discuss the 6 main causes of bad shrinkage in iron castings and how to prevent them from happening. After reading this, you’ll be one step closer to being a professional iron casting buyer.
What is shrinkage?
Shrinkage is the phenomenon of volume reduction that occurs in iron castings during the process of pouring and cooling. Therefore, shrinkage is a physical phenomenon that occurs normally in the casting process.
But if not properly controlled, shrinkage is the root cause of shrink holes, loosening, thermal cracking, cold cracking and deformation of iron castings.
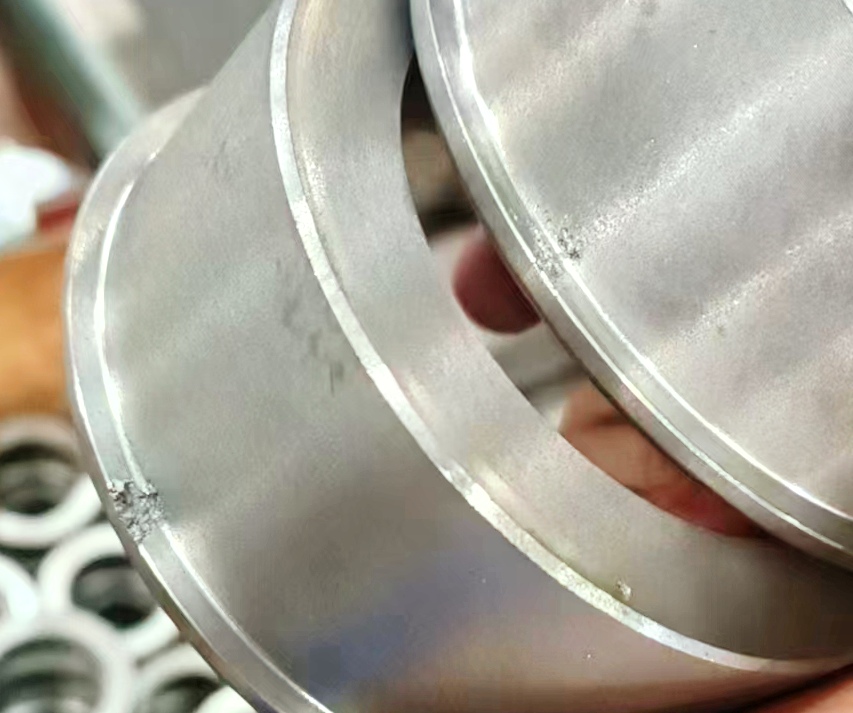
The following are the 6 major causes of poor shrinkage of iron castings.
1. Poor gate design
Unreasonable gate design can lead to excessive turbulence of molten iron, or uneven flow of molten iron, which can cause shrinkage.
In addition, an overly long gate system can also lead to an increase in solidification time, resulting in an increase in the level of shrinkage due to longer cooling time.
The gate width for most castings should not exceed 10% of the casting wall thickness. Also, the gate should be designed in a curved shape to reduce turbulence and reduce the risk of shrinkage.
2. Bad riser design
A badly designed riser can lead to an uneven cooling rate of the casting, resulting in localized shrinkage and even thermal cracks.
This is because the design of the riser has a significant impact on the rate of cooling and solidification of the molten metal.
The lack of a riser can prevent the molten iron from adequately filling the mold cavity, leading to material loss and further shrinkage of the casting.
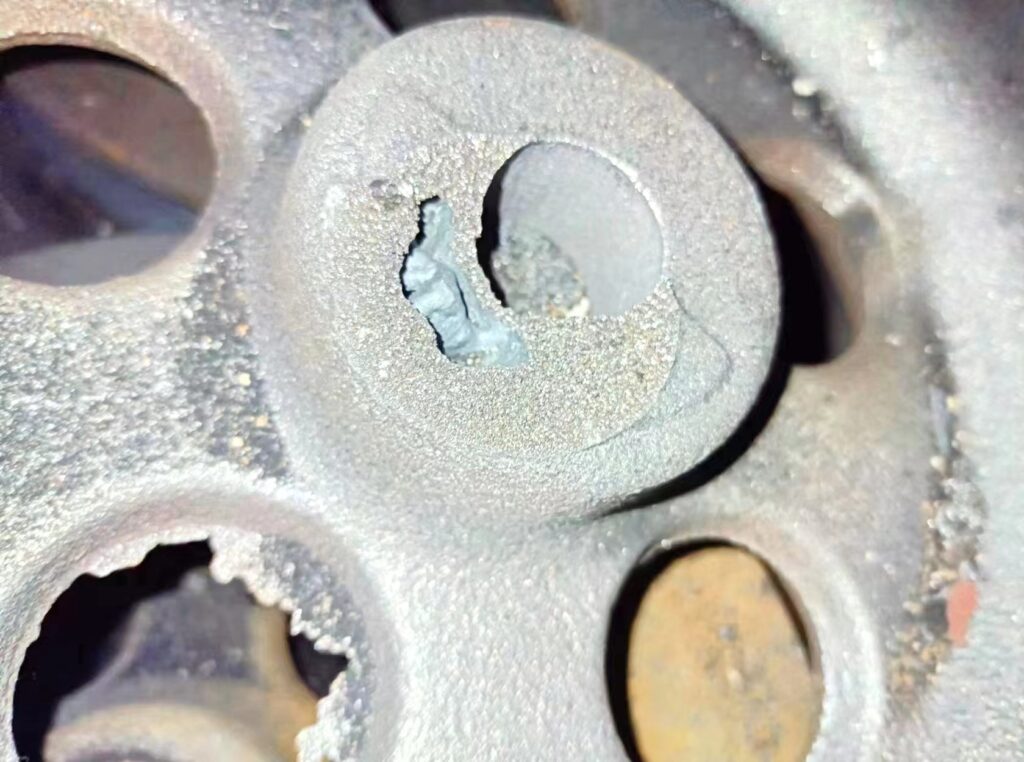
If the number of risers is too large, or the size of the risers is too large, it will result in uneven cooling of the molten metal as it flows from the casting cavity to each riser.
Plus, the location of the risers must be set reasonably. If the risers are too close to each other, the excess heat from the risers will not dissipate and the molten metal in the mold cavity will still be overheated.
All these factors can lead to undesirable shrinkage. Therefore, the designer must pay close attention to the riser design when making iron castings to ensure that shrinkage is minimized.
3. Improper pouring temperature
Temperature is critical when pouring molten iron. If the temperature is too high, it may cause excessive shrinkage in certain areas. Too low a temperature and the iron will not flow properly, resulting in inconsistent thickness throughout the casting.
If the time between pouring and solidification is too long, it may lead to more shrinkage. It is important to always keep the pouring temperature within the optimum range for each type.
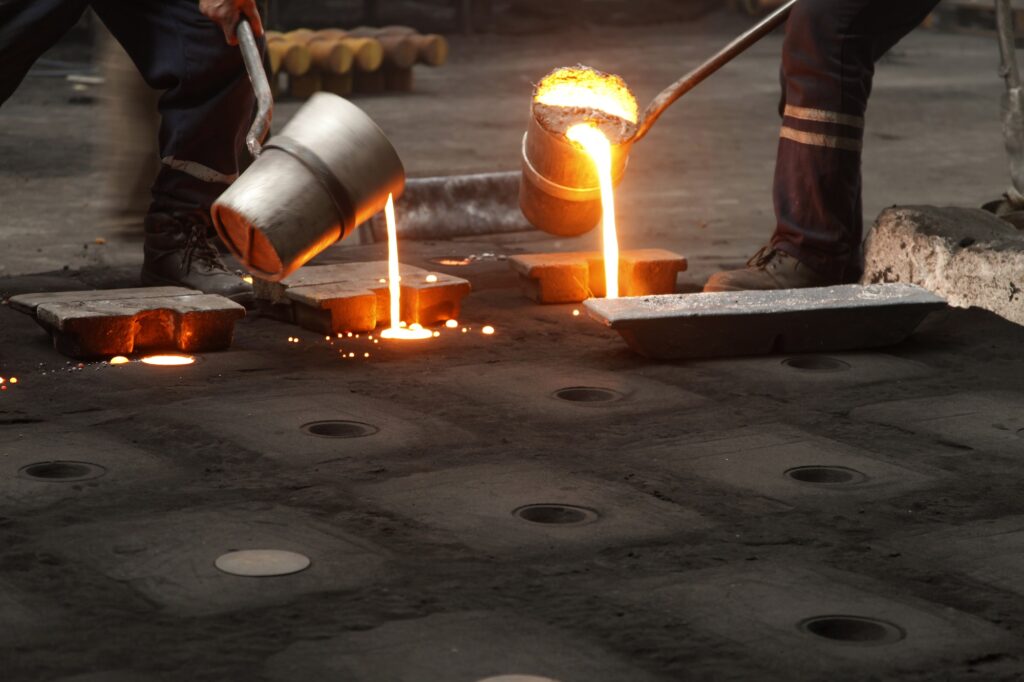
The ideal pouring temperature for iron castings is approximately 1150-1300°C (2102-2372°F), and it is important to maintain this temperature range as accurately as possible.
A difference of a few degrees can make all the difference when producing quality castings. The best way to ensure temperature is to monitor it with a thermocouple.
4. Unsatisfactory pouring speed
A pouring speed that is too slow to allow adequate heat transfer and cooling during solidification can also lead to coarse grain structure.
This results in excessive heat during solidification, which can lead to alloy segregation and increase the chance of cracking or other defects.
Too fast a pouring rate may prevent the molten iron from filling the mold cavity reasonably well, leading to shrinkage voids or other defects.
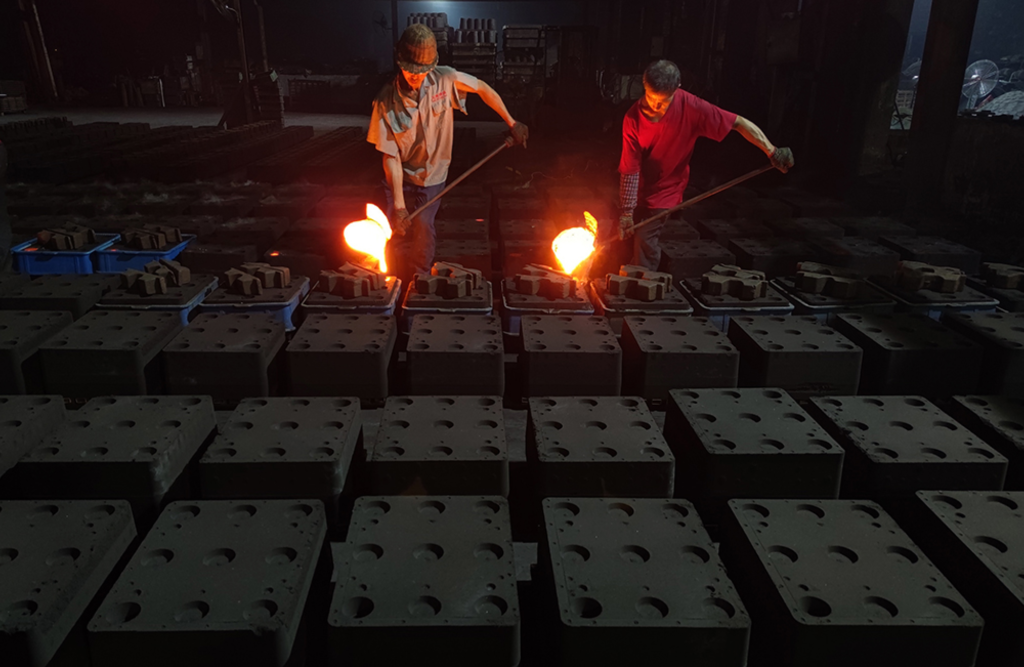
It is important to maintain a steady pouring rate for castings because it allows enough time for the molten metal to properly fill the cavities.
The ideal pouring rate should be adjusted to the size, shape and complexity of the iron casting being produced, using a controlled pouring rate appropriate to the size of the iron casting being poured.
An experienced operator can easily adjust the pouring speed to match the size and complexity of any iron casting.
5. Uneven wall thickness
If the wall thickness of iron castings is too thick or too thin, it can cause uneven cooling and excessive shrinkage in certain areas.
This can lead to uneven strength and integrity of the casting, resulting in undesirable shrinkage. It can also cause surface irregularities and warping problems.
To solve this problem, engineers must measure the wall thickness during the design process and adjust it as needed. This will ensure that the casting has a uniform wall thickness for optimal cooling and performance.
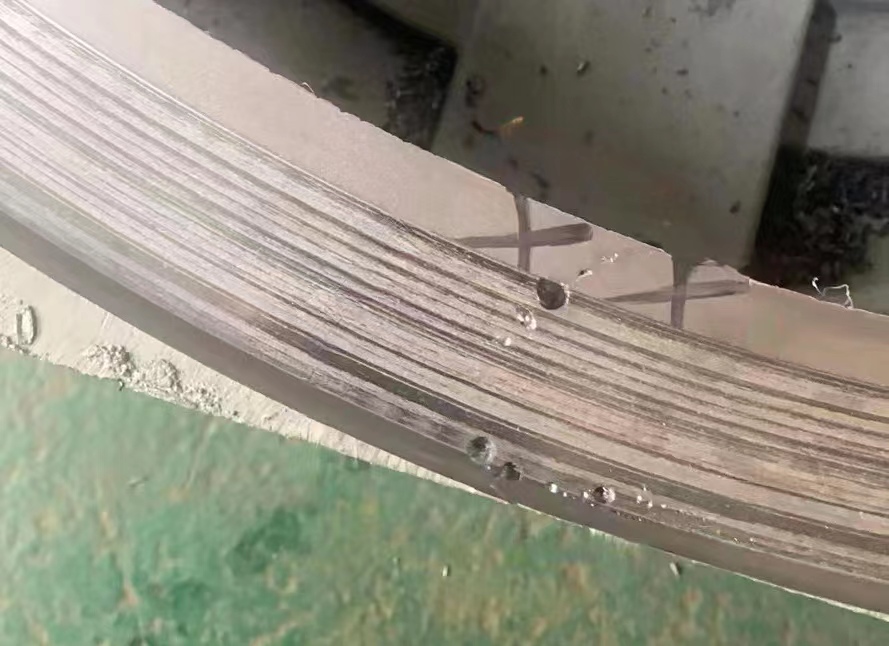
In addition, the use of modern simulation techniques can help engineers predict and prevent non-uniform wall thicknesses in iron castings.
An example is the use of a good computer-aided engineering (CAE) program, which can quickly analyze and correct any potential problems in the mold design prior to manufacturing.
6. Improper composition blending
If the composition elements in the iron casting are not able to be properly adjusted, it can lead to shrinkage and other problems in the finished iron casting.
For example, the content of carbon and silicon elements is too low, the content of manganese and chromium elements is too high, or the balance of these elements is not properly adjusted.
Improper blending of components can cause shrinkage in two ways: first, it can lead to an increase in the liquid phase temperature of the alloy; second, it can lead to a reduction in the solidification range.
The result is that the iron casting will shrink more than it should, leading to undesirable dimensions or shapes.
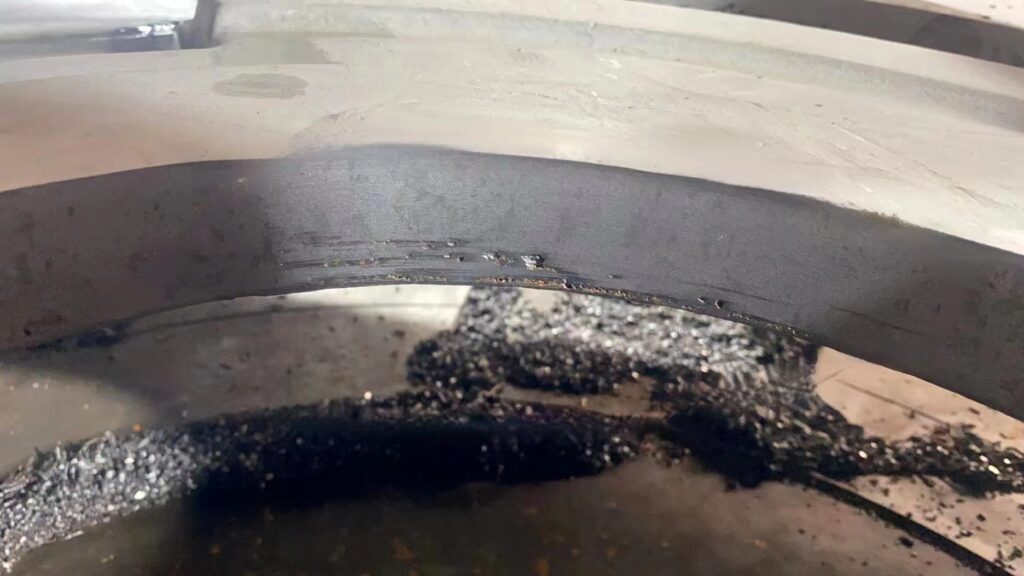
To prevent these problems from occurring, cast iron manufacturers must ensure that all components are properly blended and balanced to create high quality castings with minimal shrinkage.
Operators should periodically take samples of molten metal for laboratory analysis via a spectrometer to confirm that the composition is balanced.
Shrinkage of iron castings can be minimized through proper composition blending and careful process control.
Conclusion
The basic principle of preventing shrink holes and shrinkage loosening in castings is to specify the correct casting process for the shrinkage and solidification characteristics of the casting, so that the casting is solidified in the process of establishing good shrinkage conditions, so that the shrinkage appears in the final solidification of the casting.
In this way, a certain size of riser is placed in the last solidification place of the casting, so that the shrinkage hole is concentrated in the riser, or the gate is opened in the last solidification place to make up the shrinkage directly.
By understanding the above six common causes of shrinkage, the shrinkage problem of iron castings can be effectively prevented.
They are poor gate design, bad riser design, improper pouring temperature, unsatisfactory pouring speed, uneven wall thickness of iron castings, and improper composition blending.
When these causes are optimized, the occurrence of undesirable shrinkage can be minimized.
Castimoo has been specialized in designing, producing and selling iron castings for 30 years.
Our team, led by university professors, combines theory and practice to design the most rational pouring system for your iron castings as well as the most efficient production rate.
Our products are recognized by domestic and foreign customers, and we hope our professionalism can bring you more profit.