Introduction
When it comes to making a mold for iron casting, there are a few key areas that need to be taken into account.
In this blog post, we’ll discuss what those areas are and how to ensure your mold is up to the task. So whether you’re a first-time caster or an experienced pro, read on to find out more!
1. The size of the mold
It should be big enough to accommodate the iron casting.
When selecting a mold for your iron castings, it’s important to make sure the size is adequate.
Too small, and you might need to resort to precision welding or other costly repairs; too large, and you’ll be pouring money into resources you don’t need.
Generally speaking, a larger size mold will be more advantageous than a smaller size mold. A large size one helps create an even pressure distribution in the mold cavity and ensures that the entire shape of the casting is filled out to its fullest potential.
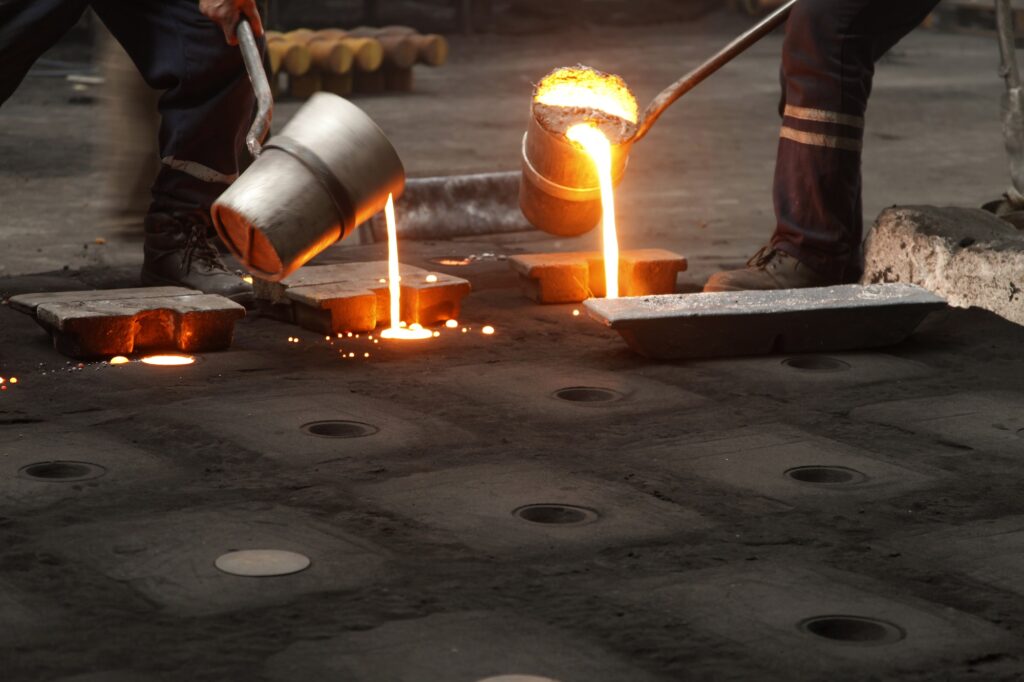
In addition, when using a larger size mold you have more room for cutting edges that are essential for allowing air and gas to escape during the pouring process.
Lastly, with extra space, you have more room to add feeders or risers which helps enhance casting yield and precision.
Larger molds can make all the difference in creating high quality iron castings but only if chosen wisely as there are several factors to consider before picking your perfect size.
2. The shape of the mold
It should be able to withstand the pressure of the iron casting process.
When it comes to making iron castings, the shape of the mould is important.
It must be able to withstand the pressure generated during the pouring process and create a high-quality cast.
This can be accomplished by using high-grade materials and incorporating mold features such as ribs and bosses that help provide additional support.
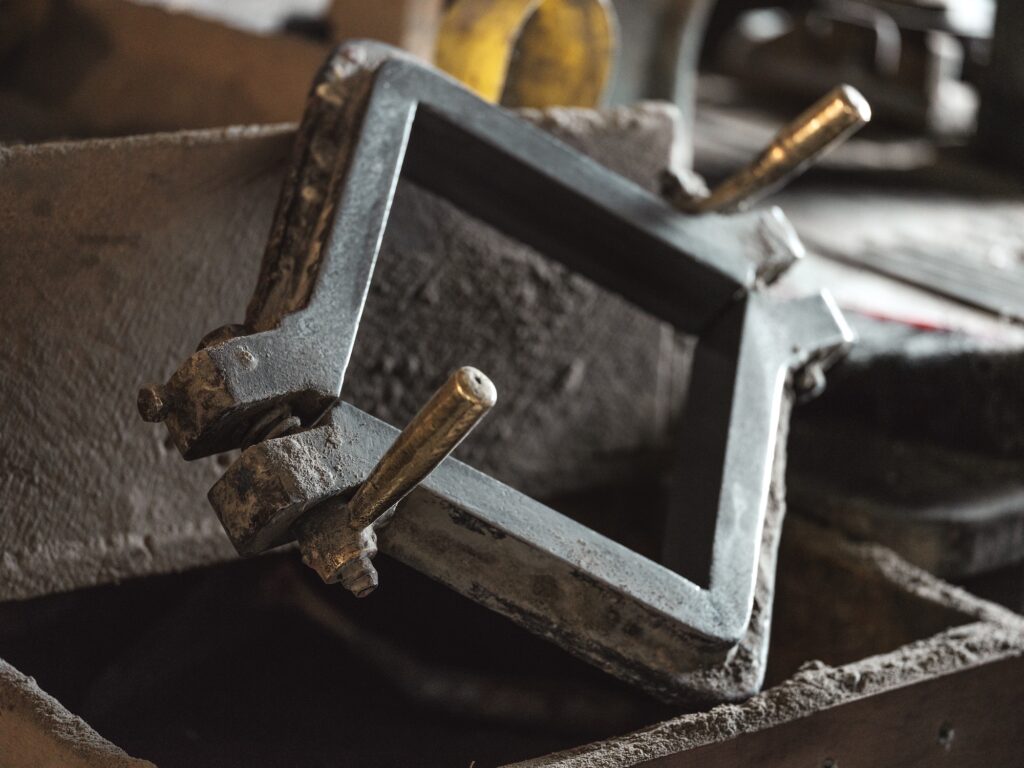
Understanding how different shapes respond to pressure will allow you to choose the right mold for your job, ensuring that you end up with an iron casting of superior strength and integrity.
Additionally, considering how long molds last is important – look for molds made from densely compacted materials like graphite or ceramic in order to get a quality mold that will stand up over multiple cycles of production.
3. The material of the mold
It should be made from a heat-resistant material that can withstand high temperatures.
Using the right kind of material for your mold is essential when working with molten materials at high temperatures.
It’s important to select a heat resistant material that won’t break down or become impaired by the intense temperature levels.
Additionally, it should possess qualities such as durability, flexibility and strength so it can stand up to multiple uses and any external force that might be applied during a casting process.
With the correct heat-resistant material, you can be sure your mold is safe and effective regardless of the high temperatures.
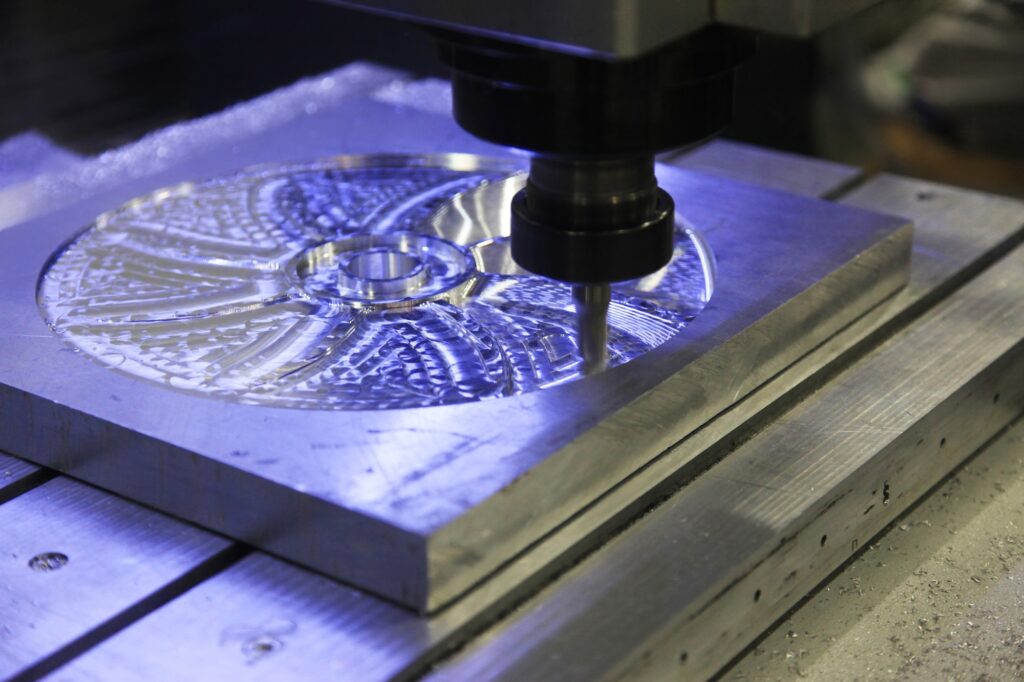
4. The thickness of the mold
It should be thick enough to prevent the iron from breaking through.
When casting an iron product, the thickness of the mould is incredibly important.
Too thin, and there is risk of it breaking under the pressure from the molten metal, which can be disastrous for both your process and your materials.
On the other hand, if you design a mould that is too thick – though certainly not as risky – it increases cost without improving your results or expanding design options.
The sweet spot in this situation is making sure your mould is thick enough to prevent any issue with breakage, but not so thick that you’re needlessly spending extra resources.
Thoughtful consideration of the mould wall thickness can help ensure successful production and efficiency while casting.
5. The smoothness of the mold
It should be smooth so that the iron casting comes out without any defects.
The process of creating iron castings is complex and involves many variables, but one element that’s paramount to success is the smoothness of the mold.
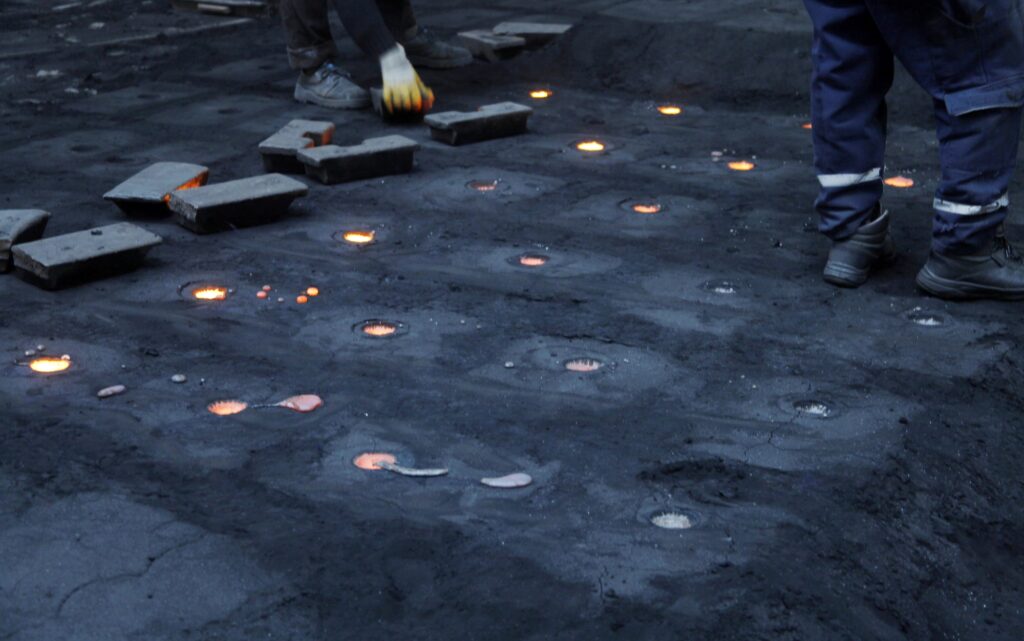
With a smooth surface, you can be sure the resulting cast will have no imperfections like bubbles or striations.
This is why it’s so important when choosing molds for your projects to ensure that each one has a consistently smooth surface.
It may seem like only a small detail, but having a good-quality mold with a perfect finish provides greater accuracy in your castings and creates pieces that people will love for years to come.
Conclusion
These are 5 main points to consider when you are creating a mold for your iron casting.
The size, shape, material, thickness and smoothness of the mold all play an important role in ensuring that your iron casting comes out perfect.
Keep these factors in mind when you are planning your next project and you will be sure to create a success.
Castimoo is a supplier specializing in the design and production of iron castings.
All you need to do is tell us what you need, and our R&D team led by university professors will provide you with a professional OEM&ODM service from mold design to finished cast iron processing.
If you have casting questions or need to purchase iron castings, welcome to visit our website castimoo.com or contact us by email.
We hope we can help you.