Introduction
Casting is a process for manufacturing metal products. In the casting process, sand is one of the indispensable raw materials.
In this article, we will introduce the 3 most commonly used sands in iron casting, hoping to help you better understand the casting process.
1. Green sand
This is the longest history of the molding material. From the Bronze Age to the present, it has been used for thousands of years.
Today the development of science and technology has fundamentally changed the way humans produce. But in the modern foundry industry, green sand still makes the most widely used molding material.
The main components of green sand are silica sand, clay and water.
It is also known for its green hue, which comes from the moisture content of the clay. What makes it particularly useful is that it provides good flow and excellent cohesiveness.
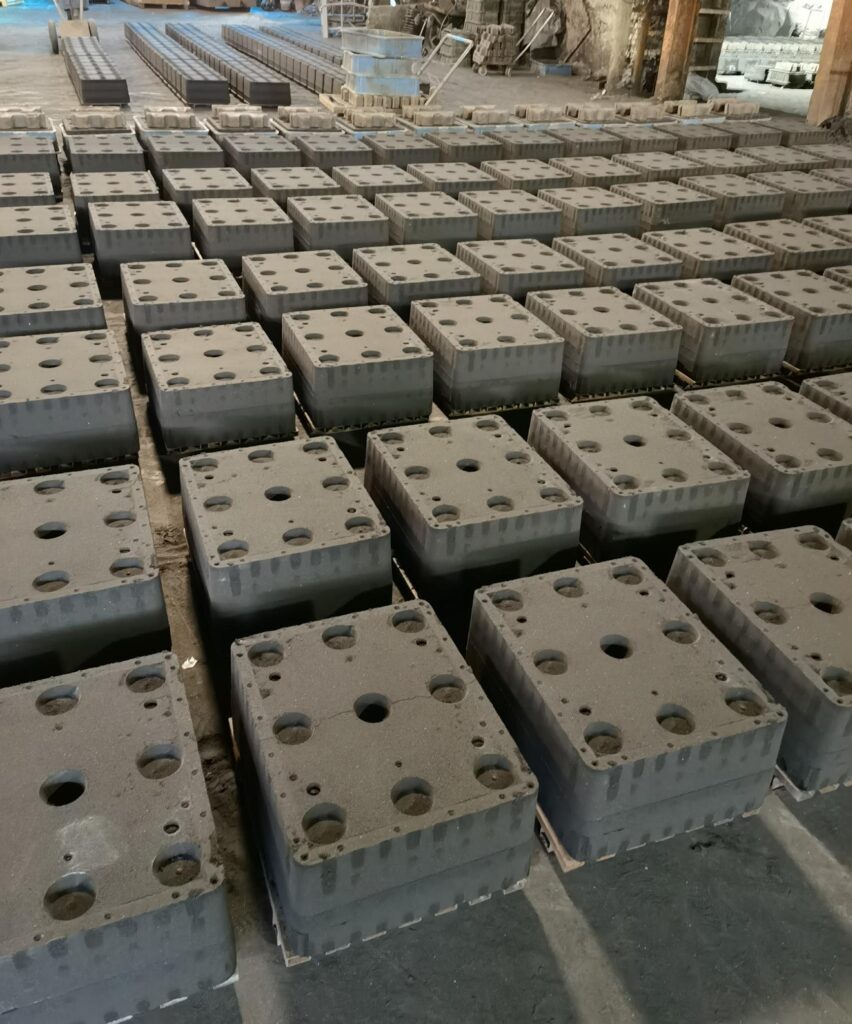
Advantages of green sand
-Adaptability to modelling methods
From the most primitive green sand for hand molding to the present high-pressure, high-speed molding, green sand has undergone many improvements, but no essential changes.
-Available in a variety of raw sands
Various raw sands currently used in foundry production, such as silica sand, zircon sand, chromite sand, etc., are adaptable to clay.
-Low cost
Clay is a natural product with abundant reserves, wide distribution, low price and abundant supply.
Moreover, the reuse of green sand is excellent, except for a small part of the clay in the sand close to the iron casting which is burned into dead clay, most of the sand can be recycled.
-Peculiar strength performance
After the green sand is mixed and compacted, the casting mold has a high strength.
It can keep the shape given by the mold pattern or core box when it is released from the mold, does not deform during the handling and closing process, and can withstand the rinsing of molten iron.
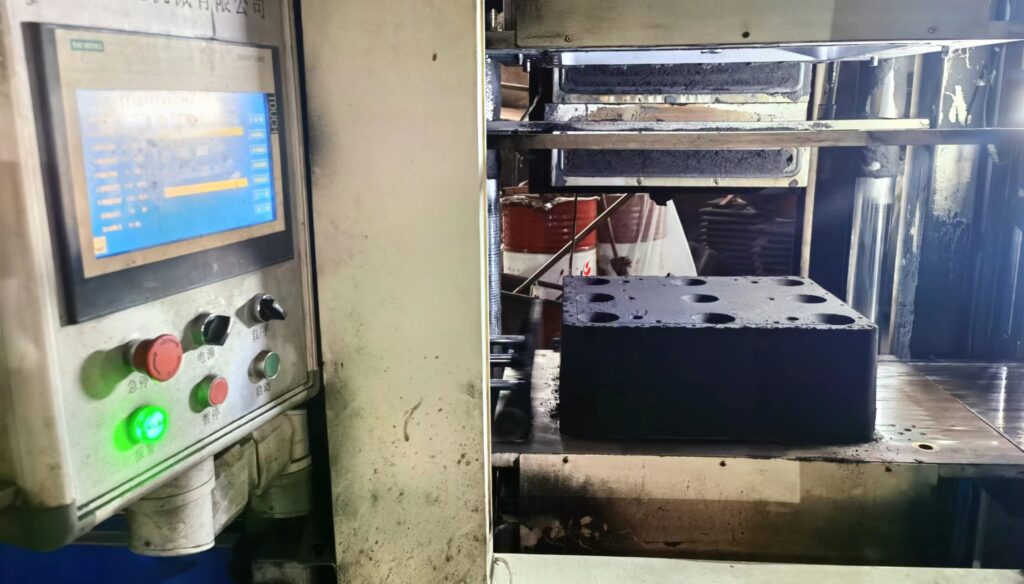
The shortcomings of green sand are
-The energy required for mixing green sand is large, and the time for mixing sand is long.
-The fluidity of green sand is not good, and it is not easy to make castings with high compactness.
Therefore, the molding equipment has to be large and bulky, and energy consumption is also high.
-The dimensional accuracy of the castings produced is low.
-The surface quality of castings is relatively poor.
Generally, foundries control the quality of the sand by four parameters. They are the effective bentonite content, compactability, wet compressive strength and moisture control.
Green sand is generally used in iron castings of about 20kg, once the weight is too much, the sand will not be able to bear it.
Resulting in iron casting easy to swell, swell the balance will become larger, the weight becomes heavier, more serious so that the iron casting inside will produce holes, the formation of voids.
Therefore, the weight is relatively large iron casting products, it is recommended to choose resin sand for casting.
2. Resin sand
Since the mid-1940s synthetic resin began to be used in casting production, as a sand binder resin, the variety continues to increase, and the quality continues to improve.
At present, the process of using resin sand, after continuous development, is also becoming more and more perfect. The resin sand can fully meet the requirements of various casting alloys and different production conditions.
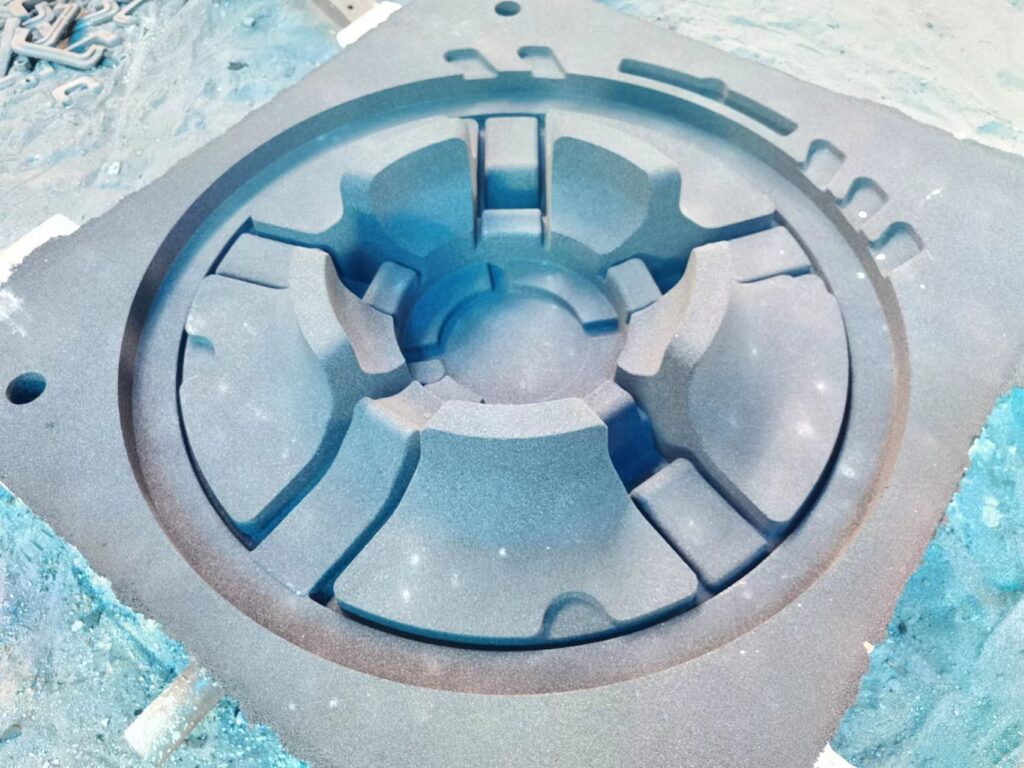
This type of sand is made of silica sand mixed with phenolic resin or furan resin.
It has high thermal stability and low permeability and is usually used for large precision castings with complex shapes. Its advantages include good surface finish, excellent dimensional accuracy and repeatability.
Green sand makes the sand sticky by water and clay, and then molded by extrusion.
And resin sand makes the sand cured and molded by chemical reaction within the sand, such as mixing hardener into the sand. This type of sand is generally suitable for small batches of complex shaped castings.
The disadvantage of resin sand is that it requires a larger cost than green sand. On average, a ton is about $150 more expensive than green sand.
The main process methods for resin sand include the heat hardening process and the self-hardening sand process.
The heating hardening process uses a shallow hardener that does not work or has little effect at room temperature. When heated to a certain temperature, the resin is rapidly cross-linked and hardened.
Self-hardening sand process is the resin and hardener are added at the time of sand mixing, molding, core making, resin in the catalytic effect of the hardener gradually cross-linking reaction and harden on their own, casting or core also gradually get the required strength. This method is more suitable for making castings and larger cores, and is mostly used for small batch production.
Resin sand remains a popular choice for those who want to get the most out of their castings. Therefore, if you are casting something that requires more detail, consider using resin sand for the job.
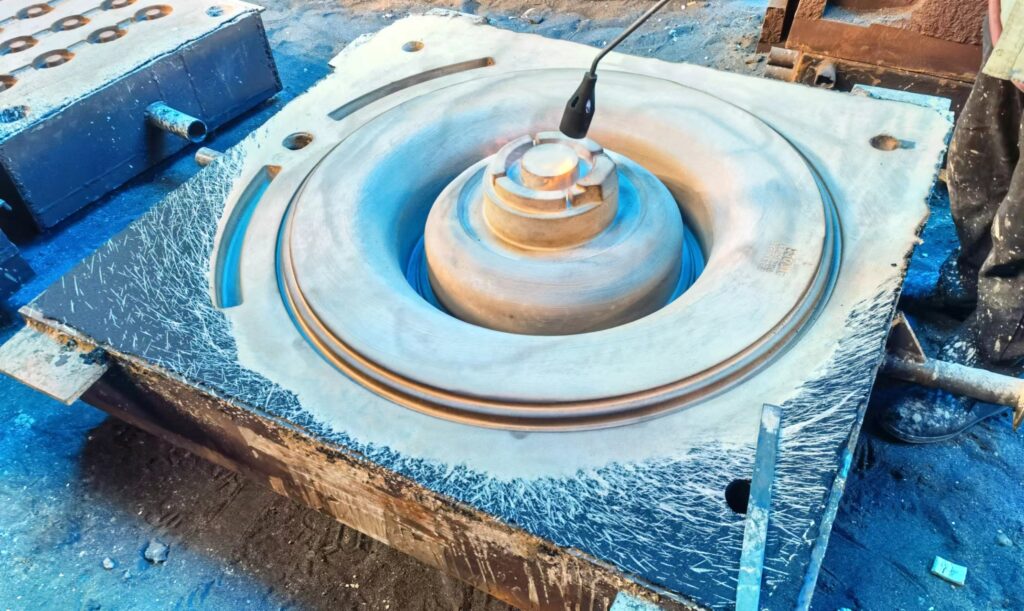
3. Water-glass sand
When it comes to casting, water-glass sand is of interest. This type of sand is a chemically bonded sand made from sodium or potassium silicate mixed with quartz sand and is widely used in foundry production.
It is popular for its excellent bonding ability, so much so that molds made with this type of sand are strong enough to withstand very high temperatures.
Advantages of water-glass sand
1) Water glass is inexpensive, and water glass sand is the lowest cost chemically hardened sand.
2) When molding, the castings are basically hardened and demolded, and the dimensional accuracy of the castings is higher than with green sand.
3) Moulding, core making, pouring and sand dropping are odorless. Generally, there is no big irritating effect on the operator’s skin. The labor environment is better.
4) The strength of water glass sand is reduced above 800℃.
Because of the melting of hardened water glass bonding film, so it is very unlikely to produce thermal crack when it is used to produce cast steel parts.
5) It can be used together with green sand.
When using water glass sand as surface sand, clay wet sand can be used as backing sand. The moisture of the backing sand does not obviously affect the hardening of the water glass sand, and the two can be combined very well.
6) No nitrogen. there is no need to worry about the problem of porosity of the casting due to nitrogen.
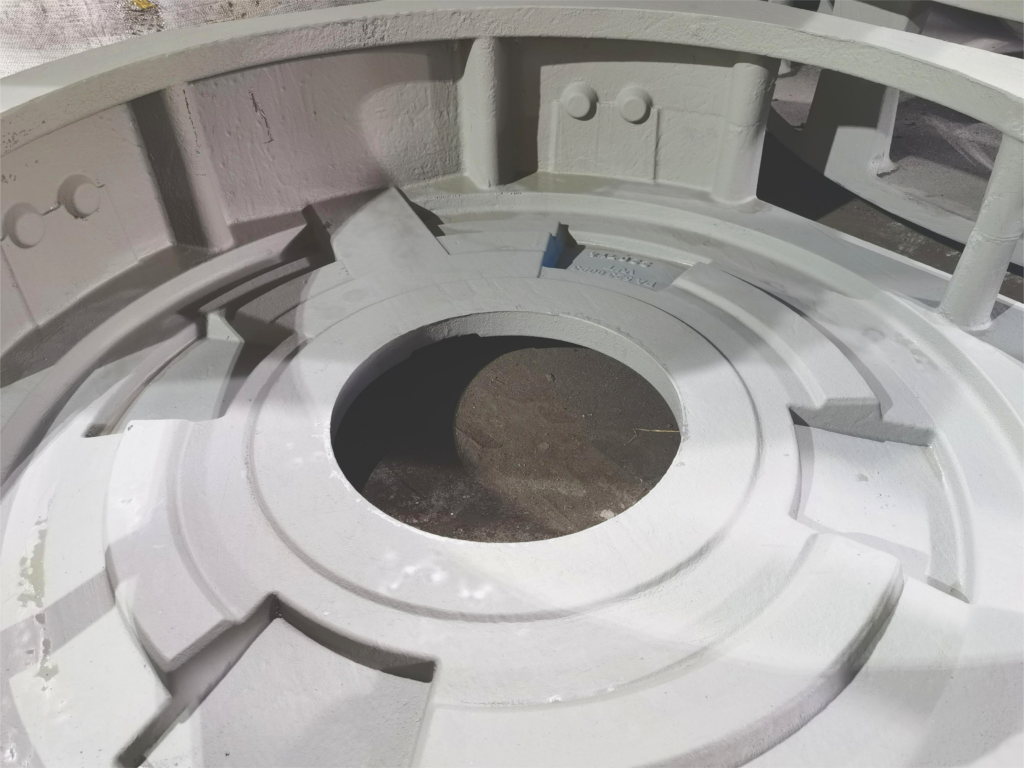
The main problems of water-glass sand are
1) Difficulty in sand falling
After casting, the water glass is heated and dehydrated, and the strength of the sand is greatly increased, which is the main reason for the difficulty of falling sand of water glass sand.
The effective way to solve the difficulty of falling sand is to reduce the amount of water glass in the sand. If the amount of water glass does not exceed 3.5%, the problem of sand falling difficulties can be basically alleviated.
2)Strong moisture absorption
Water glass sand is quite sensitive to the humidity of the environment, made of castings or cores are easy to absorb moisture and lead to a significant decline in strength, which is also a difficult problem to solve.
Generally speaking, the relative humidity of the storage environment of the cast or core exceeds 30%, that is, it has obvious influence on its strength.
When using water glass sand, if the relative humidity of the environment is about 75%, the storage period should not exceed 8 hours; if the relative humidity is above 80%, it should not exceed 2 hours.
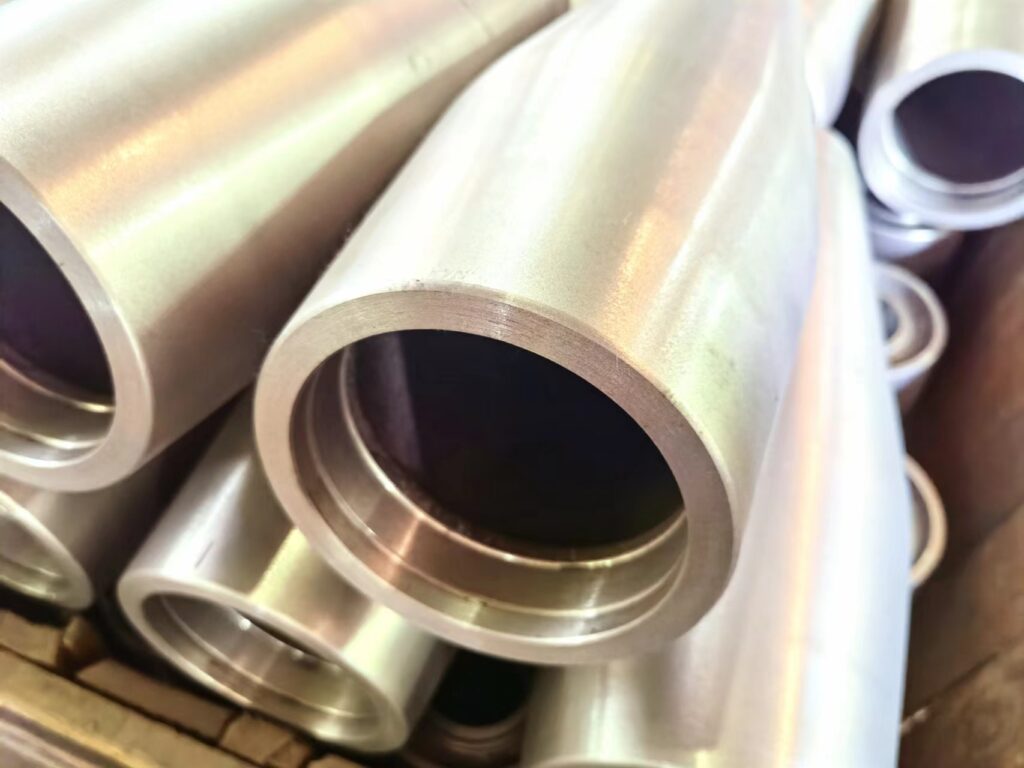
Conclusion
This article has introduced you to the 3 most common types of sand used in casting. They are green sand, resin sand, and water glass sand.
Regardless of which sand you use for casting, it is important to maintain a healthy working environment to ensure product quality and safety. Make sure you follow safe work practices and use the correct tools and protective equipment.
The end result of sand casting may not immediately meet your expectations, but with proper sand preparation, skilled operation and good maintenance, you will be able to produce high quality castings. With the right sand and the right technique, you can achieve the results you want.
Castimoo is a cast iron supplier with 30 years of experience. Equipped with 2 sets of resin sand production lines, 2 sets of green sand automatic molding production lines, and 5 sets of small vibratory compaction molding machines. We are able to provide you with a comprehensive range of high quality iron casting products and solutions.
No matter what type of sand used for casting, it plays an important role in ensuring the quality of the part. The various types of foundry sand have different characteristics and can be selected according to production and quality requirements. We hope that this article has given you a better understanding of foundry sands.
One Response